Battery laser welding machines play a pivotal role in the evolution of battery manufacturing, offering precision, efficiency, and reliability for the production of high-quality batteries. By utilizing high-energy laser beams, these machines create strong, durable welds with minimal heat-affected zones, ensuring the integrity of delicate battery components. The process involves a highly controlled series of steps, from the generation of the laser beam to the precise fusion of materials, making it ideal for applications ranging from cell assembly to electrode welding. Battery laser welding machines are particularly favored in industries requiring consistent, high-quality results, such as consumer electronics and electric vehicles. As technology advances, these machines continue to improve production efficiency, reduce material waste, and ensure the safety and durability of the final product.
What is a Battery Laser Welding Machine?
A battery laser welding machine is a specialized piece of equipment designed to join battery components using laser technology. This machine is particularly crucial in the battery manufacturing industry, where precision and reliability are paramount. The laser welding process involves the use of a high-energy laser beam to melt and fuse materials together, creating a strong and durable bond. This method is highly favored for its ability to produce clean, precise welds with minimal heat-affected zones, which is essential for maintaining the integrity of battery cells.
Battery Laser Welding Machine Structure and Design
The structure and design of a battery laser welding machine are tailored to meet the specific needs of battery production. Typically, the machine consists of several key components:
- Laser Source: The heart of the machine, generating the laser beam used for welding.
- Optical System: Includes lenses and mirrors that focus and direct the laser beam onto the workpiece.
- Workstation: The area where the battery components are placed and welded. It often includes fixtures to hold the parts in place.
- Control System: A computer-based interface that allows operators to set and adjust welding parameters such as power, speed, and pulse duration.
- Cooling System: Essential for maintaining the temperature of the laser source and optical components, ensuring consistent performance.
The design of these machines often incorporates modularity, allowing for easy maintenance and upgrades. Additionally, safety features such as enclosures and sensors are integrated to protect operators from laser radiation.
Working Principle of Battery Laser Welding Machines
The working principle of a battery laser welding machine revolves around the precise application of laser energy to create welds. Here’s a step-by-step breakdown of how it operates:
- Preparation: Battery components are positioned and secured in the workstation.
- Laser Beam Generation: The laser source emits a high-energy beam, which is then directed through the optical system.
- Focusing: The laser beam is focused onto the specific area where the weld is required.
- Melting and Fusion: The intense heat from the laser melts the material at the weld point, causing it to fuse together.
- Cooling: The molten material cools and solidifies, forming a strong bond.
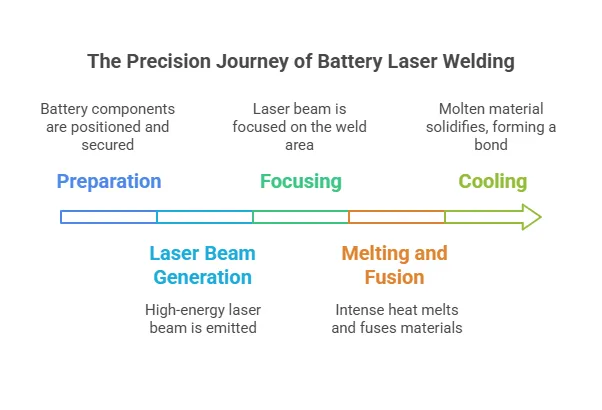
This process is highly controlled, with parameters such as laser power, pulse duration, and beam focus being meticulously adjusted to achieve the desired weld quality.
Applications of Battery Laser Welding Machines in the Battery Industry
Battery laser welding machines are indispensable in the battery industry, where they are used in various applications:
- Cell Assembly: Welding battery cells together to form modules and packs.
- Tab Welding: Connecting battery tabs to terminals with high precision.
- Case Sealing: Sealing battery cases to ensure they are airtight and leak-proof.
- Electrode Welding: Joining electrodes within the battery to ensure proper electrical connectivity.
These applications highlight the versatility and importance of laser welding in producing high-quality, reliable batteries for a range of uses, from consumer electronics to electric vehicles.
How Battery Laser Welding Machines Improve Battery Manufacturing Efficiency
Battery laser welding machines significantly enhance manufacturing efficiency through several key features:
- High Speed: Laser welding is much faster than traditional welding methods, allowing for quicker production cycles.
- Precision: The ability to focus the laser beam precisely reduces material waste and improves weld quality.
- Automation: Many laser welding machines are fully automated, reducing the need for manual labor and minimizing human error.
- Consistency: Laser welding provides consistent results, ensuring that each weld meets the required standards.
- Flexibility: These machines can be easily reprogrammed to handle different battery designs and materials, making them adaptable to various production needs.
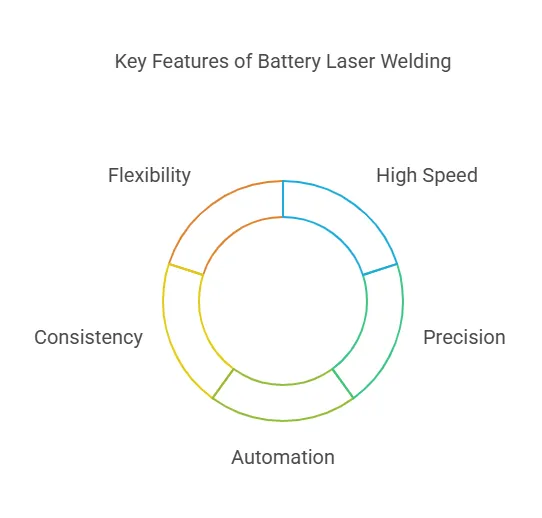
By incorporating these features, battery laser welding machines streamline the manufacturing process, leading to increased productivity and reduced costs.
What is the Ideal Work Environment for Operating a Battery Laser Welding Machine?
The work environment for operating a battery laser welding machine plays a critical role in ensuring both safety and optimal performance. Here’s what an ideal setup looks like:
- Clean and Dust-Free Area: Dust and debris can interfere with the laser beam and damage sensitive components. A clean environment ensures consistent welding quality.
- Controlled Temperature and Humidity: Extreme temperatures or high humidity can affect the machine’s performance. Maintaining a stable environment helps prevent malfunctions.
- Proper Ventilation: Laser welding can produce fumes or particles, so adequate ventilation is necessary to protect operators and maintain air quality.
- Safety Barriers and Signage: The workspace should include safety enclosures, warning signs, and laser safety curtains to prevent accidental exposure to the laser beam.
- Organized Layout: A well-organized workstation with easy access to tools, materials, and controls improves efficiency and reduces downtime.
By creating a controlled and safe work environment, operators can maximize the machine’s performance while minimizing risks.
How is Product Testing and Quality Assurance Conducted in Battery Laser Welding?
Product testing and quality assurance are essential steps in battery laser welding to ensure the reliability and safety of the final product. Here’s how these processes are typically carried out:
- Visual Inspection: Operators examine the welds for surface defects such as cracks, porosity, or uneven seams.
- Dimensional Checks: Measurements are taken to ensure the weld meets specified tolerances and aligns with design requirements.
- Mechanical Testing: Weld strength is tested using methods like tensile testing or shear testing to verify durability.
- Electrical Testing: For battery applications, electrical conductivity tests are performed to ensure proper connections.
- Non-Destructive Testing (NDT): Techniques like X-ray or ultrasonic testing are used to detect internal defects without damaging the product.
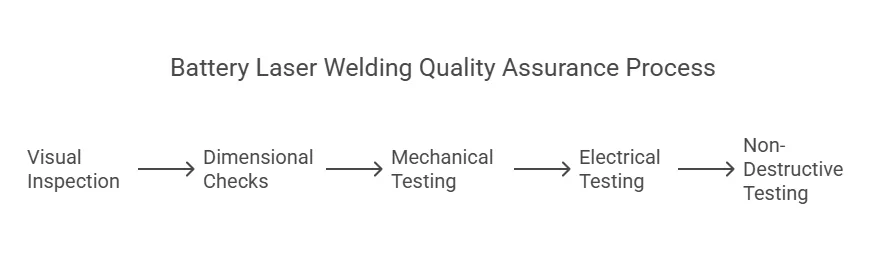
These steps ensure that every weld meets industry standards and performs reliably in real-world applications.
How to Maintain and Care for a Battery Laser Welding Machine
Proper maintenance and care are crucial for extending the lifespan and ensuring the consistent performance of a battery laser welding machine. Follow these steps:
-
Daily Maintenance:
- Clean the optical components (lenses, mirrors) to remove dust or debris.
- Inspect the cooling system for leaks or blockages.
- Check the laser source for any signs of wear or damage.
-
Weekly Maintenance:
- Calibrate the laser beam alignment to ensure precision.
- Lubricate moving parts to reduce friction and wear.
- Test safety features, such as emergency stop buttons and sensors.
-
Monthly Maintenance:
- Replace worn-out components, such as filters or seals.
- Perform a thorough inspection of the electrical system.
- Update the machine’s software to the latest version.
By following a regular maintenance schedule, operators can prevent unexpected breakdowns and maintain high welding quality.
What are Common Issues in Battery Laser Welding and How to Address Them?
Even with advanced technology, battery laser welding can encounter issues. Here are some common problems and their solutions:
-
Inconsistent Weld Quality:
- Cause: Misaligned laser beam or incorrect parameters.
- Solution: Recalibrate the laser alignment and adjust power, speed, or pulse settings.
-
Porosity in Welds:
- Cause: Contamination on the material surface or insufficient shielding gas.
- Solution: Clean the material thoroughly and ensure proper gas flow.
-
Cracking:
- Cause: Excessive heat input or incompatible materials.
- Solution: Optimize welding parameters and use materials with similar thermal properties.
-
Machine Overheating:
- Cause: Cooling system failure or prolonged operation.
- Solution: Check the cooling system for issues and allow the machine to cool down periodically.
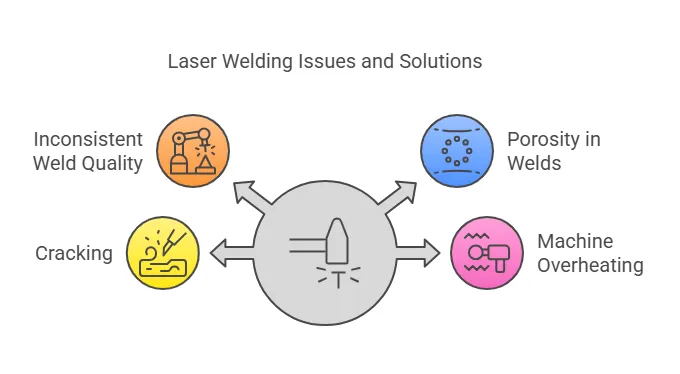
Addressing these issues promptly ensures smooth operation and high-quality welds.
Why are Safety Precautions Critical When Using a Battery Laser Welding Machine?
Safety precautions are paramount when operating a battery laser welding machine due to the high-energy laser beam and potential hazards. Here’s how to ensure safety:
-
Personal Protective Equipment (PPE):
- Wear laser safety goggles to protect your eyes from harmful radiation.
- Use heat-resistant gloves and clothing to shield against burns.
-
Machine Safety Features:
- Ensure the machine has an emergency stop button and safety interlocks.
- Use enclosures or barriers to contain the laser beam.
-
Training and Awareness:
- Provide comprehensive training for operators on safe machine operation.
- Display safety guidelines and warning signs prominently in the workspace.
-
Regular Safety Audits:
- Conduct periodic inspections to identify and address potential hazards.
- Test safety systems, such as sensors and alarms, to ensure they function correctly.
By prioritizing safety, operators can prevent accidents and create a secure working environment.
Battery laser welding machines are revolutionizing the battery manufacturing industry by enabling precise and efficient welds. These machines use high-energy laser beams to join battery components, ensuring strong, reliable connections with minimal risk of material damage. Key components of these machines include the laser source, optical system, and cooling mechanisms, all designed for optimal performance in a controlled environment. From improving production speeds to reducing human error through automation, these machines enhance efficiency and ensure high-quality output. Regular maintenance, proper safety precautions, and thorough testing are essential to maintaining consistent performance. As the demand for more durable, efficient batteries grows, the importance of battery laser welding technology will only continue to rise, driving innovation in the industry.