In today’s rapidly evolving energy landscape, battery machines have emerged as indispensable tools in the production, assembly, and maintenance of batteries. These specialized devices play a crucial role in ensuring that batteries are manufactured efficiently, safely, and to the highest quality standards. From lithium-ion to solid-state batteries, these machines cater to a wide range of industries, including consumer electronics, automotive, and renewable energy. Understanding their structure, functionality, and applications is key to appreciating their significance in powering our modern world.
What is a Battery Machine?
A battery machine is a specialized piece of equipment designed for the production, assembly, or maintenance of batteries. These machines are integral to the manufacturing process, ensuring that batteries are produced efficiently, safely, and to the highest quality standards. Battery machines can be used for various types of batteries, including lithium-ion, lead-acid, and nickel-metal hydride batteries. They are employed in industries ranging from consumer electronics to automotive and renewable energy sectors.
Battery Machine Product Structure and Design
The structure and design of a battery machine are critical to its functionality and efficiency. Typically, a battery machine consists of several key components:
- Feeding System: This system is responsible for supplying raw materials or components to the machine. It ensures a continuous and precise flow of materials, which is essential for maintaining production speed and accuracy.
- Assembly Unit: This is the core of the battery machine where the actual assembly of battery components takes place. It includes mechanisms for electrode stacking, cell winding, and casing assembly.
- Control System: Modern battery machines are equipped with advanced control systems that monitor and regulate the entire production process. These systems often include programmable logic controllers (PLCs) and human-machine interfaces (HMIs) for easy operation and troubleshooting.
- Quality Inspection Module: To ensure that each battery meets stringent quality standards, battery machines are often equipped with inspection modules that use sensors and cameras to detect defects or inconsistencies in the battery cells.
- Packaging Unit: Once the batteries are assembled and inspected, they are packaged for shipment. This unit ensures that the batteries are securely packed and ready for distribution.
How Does a Battery Machine Work?
Understanding how a battery machine works involves breaking down the process into several key steps:
- Material Feeding: The process begins with the feeding of raw materials, such as electrode sheets, separators, and electrolytes, into the machine. These materials are precisely measured and fed into the assembly unit.
- Electrode Stacking: In this step, the electrode sheets and separators are stacked in a specific sequence to form the battery cell. This is a critical step as it determines the battery’s capacity and performance.
- Cell Winding: The stacked layers are then wound into a cylindrical or prismatic shape, depending on the type of battery being produced. This step requires high precision to ensure that the layers are evenly wound without any gaps or overlaps.
- Casing Assembly: The wound cell is then placed into a casing, which is typically made of metal or plastic. The casing provides structural support and protects the internal components from external damage.
- Electrolyte Filling: Once the cell is encased, the electrolyte is injected into the cell. This step is crucial as the electrolyte facilitates the flow of ions between the electrodes, enabling the battery to store and release energy.
- Sealing: After the electrolyte is filled, the battery is sealed to prevent leakage and contamination. This step often involves heat sealing or ultrasonic welding to ensure a tight seal.
- Quality Inspection: The assembled battery undergoes a series of quality checks, including voltage testing, capacity testing, and visual inspection. Any defective batteries are removed from the production line.
- Packaging: Finally, the batteries are packaged and prepared for shipment. This step includes labeling, boxing, and palletizing the batteries for distribution.
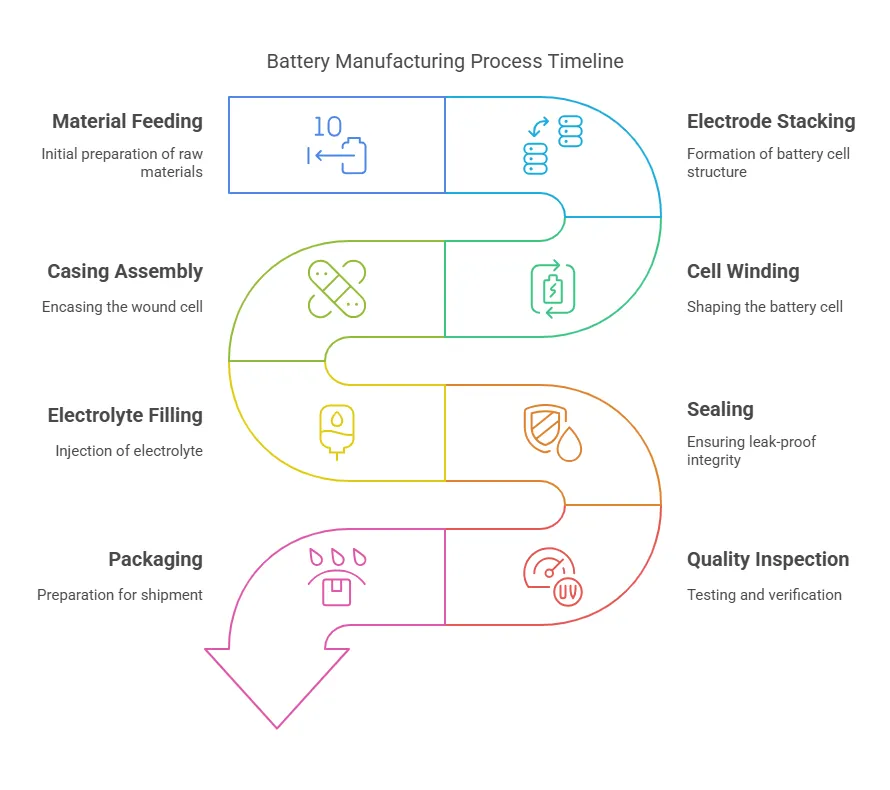
Applications of Battery Machines in the Energy Sector
Battery machines play a pivotal role in the energy sector, particularly in the production of batteries used for energy storage and electric vehicles (EVs). Here are some key applications:
- Grid Energy Storage: Battery machines are used to produce large-scale batteries that store energy generated from renewable sources like solar and wind. These batteries help stabilize the grid by providing backup power during peak demand or when renewable energy generation is low.
- Electric Vehicles (EVs): The automotive industry relies heavily on battery machines to produce high-capacity batteries for electric vehicles. These batteries need to be durable, efficient, and capable of delivering high performance over long distances.
- Portable Electronics: Battery machines are also used in the production of batteries for portable electronics such as smartphones, laptops, and tablets. These batteries need to be lightweight, compact, and capable of holding a charge for extended periods.
- Industrial Equipment: In industries that require heavy machinery, battery machines produce batteries that power equipment such as forklifts, cranes, and other industrial vehicles. These batteries need to be robust and capable of withstanding harsh operating conditions.
Different Types of Battery Machines and Their Uses
There are several types of battery machines, each designed for specific applications and battery types. Here are some of the most common types:
- Lithium-ion Battery Machines: These machines are specifically designed for the production of lithium-ion batteries, which are widely used in consumer electronics, electric vehicles, and renewable energy storage. Lithium-ion battery machines are known for their high precision and efficiency.
- Lead-acid Battery Machines: Lead-acid batteries are commonly used in automotive and industrial applications. The machines used for their production are designed to handle the heavy and bulky components of lead-acid batteries, including lead plates and sulfuric acid electrolytes.
- Nickel-metal Hydride (NiMH) Battery Machines: NiMH batteries are often used in hybrid vehicles and portable electronics. The machines used for their production are designed to handle the specific requirements of NiMH chemistry, including the use of hydrogen-absorbing alloys.
- Solid-state Battery Machines: Solid-state batteries are an emerging technology that offers higher energy density and safety compared to traditional lithium-ion batteries. The machines used for their production are still in the developmental stage but are expected to revolutionize the battery industry.
- Custom Battery Machines: Some manufacturers require custom battery machines tailored to their specific needs. These machines are designed to produce batteries with unique specifications, such as custom shapes, sizes, or chemistries.
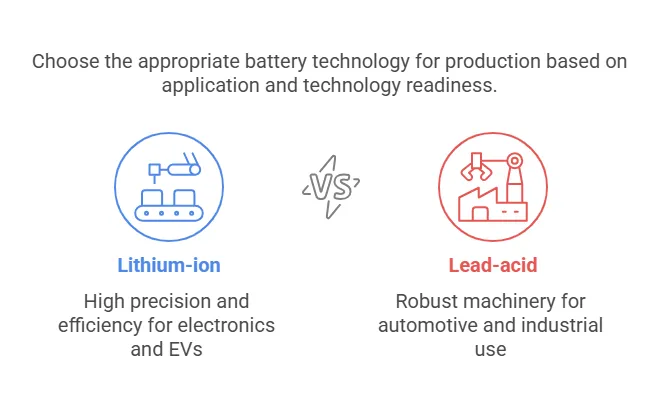
Each type of battery machine is optimized for the specific requirements of the battery it produces, ensuring high quality, efficiency, and reliability.
Battery Machine Workflow: From Raw Material to Finished Product
The workflow of a battery machine is a meticulously designed process that transforms raw materials into fully functional batteries. Here’s a step-by-step breakdown of how this process works:
- Raw Material Preparation: The process begins with the preparation of raw materials, such as electrode powders, separators, and electrolytes. These materials are carefully measured and prepared to meet specific chemical and physical requirements.
- Electrode Coating: The electrode powders are mixed with binders and solvents to form a slurry, which is then coated onto metal foils (usually copper for the anode and aluminum for the cathode). The coated foils are dried and compressed to ensure uniformity.
- Electrode Cutting: The coated foils are cut into precise shapes and sizes, depending on the battery design. This step ensures that each electrode fits perfectly into the battery cell.
- Cell Assembly: The cut electrodes are stacked or wound together with separators to form the battery cell. This step is critical for determining the battery’s capacity and performance.
- Electrolyte Filling: The assembled cell is filled with electrolyte, which facilitates the flow of ions between the electrodes. This step must be done in a controlled environment to prevent contamination.
- Sealing: The cell is sealed to prevent leakage and ensure safety. This often involves heat sealing or ultrasonic welding to create a tight, durable seal.
- Formation and Aging: The sealed battery undergoes a formation process, where it is charged and discharged several times to stabilize its performance. After formation, the battery is aged to ensure it meets quality standards.
- Testing and Inspection: The finished battery is subjected to a series of tests, including voltage, capacity, and safety tests. Any defective batteries are removed from the production line.
- Packaging: Finally, the batteries are packaged and prepared for shipment. This step includes labeling, boxing, and palletizing the batteries for distribution.
Key Features of a High-Performance Battery Machine
High-performance battery machines are designed to deliver efficiency, precision, and reliability. Here are some key features to look for:
- Automation: Advanced automation reduces human error and increases production speed. Automated systems can handle tasks such as material feeding, electrode stacking, and quality inspection.
- Precision Engineering: High-precision components ensure that each battery is produced to exact specifications. This is crucial for maintaining consistency and quality.
- Modular Design: A modular design allows for easy customization and scalability. Manufacturers can add or remove modules to adapt to different production needs.
- Advanced Control Systems: Modern battery machines are equipped with sophisticated control systems that monitor and regulate the entire production process. These systems often include PLCs and HMIs for easy operation and troubleshooting.
- Energy Efficiency: High-performance machines are designed to minimize energy consumption, reducing operational costs and environmental impact.
- Safety Features: Safety is paramount in battery production. High-performance machines include features such as emergency stop buttons, safety guards, and automated shutdown systems in case of malfunctions.

Battery Machine Product Testing: Ensuring Quality and Reliability
Product testing is a critical step in the battery production process. It ensures that each battery meets stringent quality and safety standards. Here’s how battery machine product testing is typically conducted:
- Voltage Testing: This test measures the battery’s voltage to ensure it falls within the specified range. Any deviations can indicate issues with the electrode materials or assembly process.
- Capacity Testing: Capacity testing determines how much energy the battery can store and deliver. This is crucial for ensuring that the battery meets performance expectations.
- Cycle Life Testing: This test involves charging and discharging the battery multiple times to assess its longevity. Batteries that fail to maintain performance over multiple cycles are rejected.
- Safety Testing: Safety tests include overcharge, short-circuit, and thermal stability tests. These tests ensure that the battery can withstand extreme conditions without failing or posing a safety risk.
- Visual Inspection: Automated cameras and sensors are used to inspect the battery for physical defects, such as cracks, leaks, or misaligned components.
- Environmental Testing: Batteries are subjected to various environmental conditions, such as high and low temperatures, humidity, and vibration, to ensure they can operate reliably in different settings.
Battery Machine Maintenance: Tips for Longevity and Performance
Proper maintenance is essential for ensuring the longevity and performance of battery machines. Here are some tips:
- Regular Cleaning: Dust and debris can accumulate on machine components, leading to malfunctions. Regular cleaning helps maintain optimal performance.
- Lubrication: Moving parts should be lubricated regularly to reduce friction and wear. This extends the lifespan of the machine and ensures smooth operation.
- Inspection and Calibration: Regular inspections and calibration of sensors, actuators, and control systems are crucial for maintaining accuracy and efficiency.
- Component Replacement: Wear-and-tear components, such as belts, bearings, and seals, should be replaced periodically to prevent breakdowns.
- Software Updates: Keep the machine’s software up to date to ensure it operates with the latest features and security patches.
- Training: Ensure that operators are well-trained in both operation and maintenance procedures. Proper training can prevent operator errors and extend the machine’s lifespan.
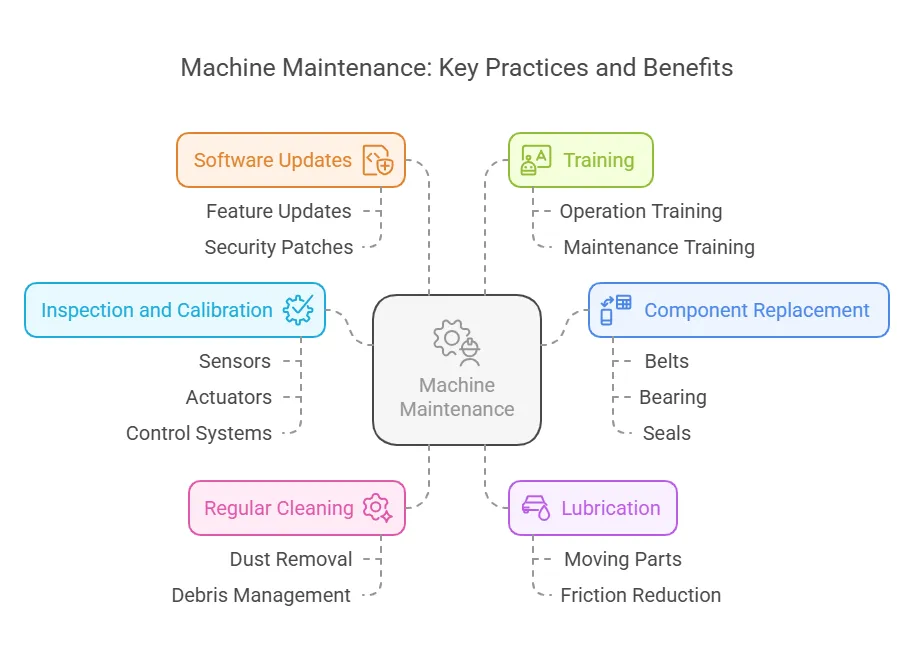
Battery Machine Installation and Setup: Best Practices
The installation and setup of a battery machine are critical for ensuring optimal performance and safety. Here are some best practices:
- Site Preparation: Choose a site that is clean, dry, and free from vibrations. Ensure that the site has adequate space for the machine and any auxiliary equipment.
- Foundation and Leveling: The machine should be installed on a stable, level foundation to prevent vibrations and misalignment. Use leveling feet or shims to achieve perfect alignment.
- Electrical Connections: Ensure that all electrical connections are made according to the manufacturer’s specifications. Use proper grounding techniques to prevent electrical hazards.
- Pneumatic and Hydraulic Systems: If the machine uses pneumatic or hydraulic systems, ensure that all connections are secure and leak-free. Use the recommended fluids and pressures.
- Initial Calibration: After installation, perform an initial calibration of all sensors, actuators, and control systems. This ensures that the machine operates within specified tolerances.
- Test Run: Conduct a test run to verify that the machine operates correctly. Check for any unusual noises, vibrations, or errors in the control system.
- Safety Checks: Before full-scale production, perform a thorough safety check. Ensure that all safety guards, emergency stop buttons, and warning systems are functioning correctly.
By following these best practices, you can ensure that your battery machine is installed and set up for optimal performance, safety, and longevity.
This article delves into the world of battery machines, exploring their essential components, such as the feeding system, assembly unit, control system, quality inspection module, and packaging unit. It outlines the step-by-step workflow, from raw material preparation to the final packaging of batteries. The article also highlights the importance of product testing to ensure quality and reliability, as well as maintenance tips to prolong the lifespan of these machines. Additionally, it discusses the various types of battery machines, including lithium-ion, lead-acid, and solid-state machines, each tailored to specific battery chemistries and applications. Finally, it provides best practices for installation and setup to ensure optimal performance and safety. Battery machines are not just machines—they are the backbone of modern energy storage and mobility solutions.