Laser welding machines are indispensable tools in the production of lithium-ion batteries, offering unmatched precision, efficiency, and reliability. Their advanced design and working principles enable high-quality welds on materials like aluminum and copper, which are critical for battery performance. These machines are used in various applications, from electrode tab welding to module assembly, ensuring the production of safe and durable batteries. To achieve optimal results, it is essential to maintain a controlled work environment that supports the machine’s performance. By leveraging laser welding technology, manufacturers can meet the growing demands of the energy storage and electric vehicle industries.
What is a Laser Welding Machine for Lithium-ion Batteries?
A laser welding machine for lithium-ion batteries is a specialized device used to join battery components with high precision and efficiency. It utilizes a focused laser beam to create strong, reliable welds on materials such as aluminum, copper, and nickel, which are commonly used in battery manufacturing. This technology is essential for producing high-quality lithium-ion batteries, as it ensures minimal heat distortion, precise control, and consistent weld quality. Laser welding machines are widely adopted in the battery industry due to their ability to meet the stringent requirements of modern energy storage systems.
How Does the Product Structure and Design of Laser Welding Machines Enhance Performance?
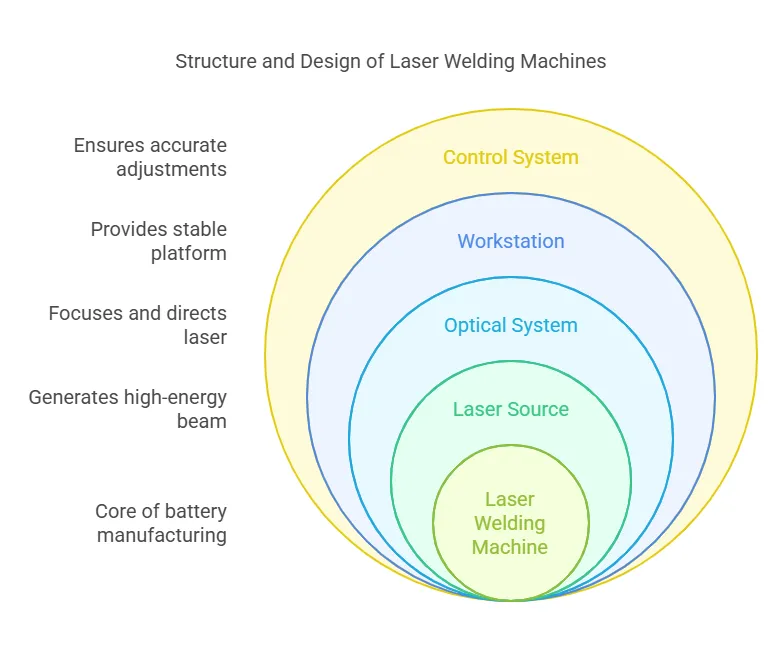
The structure and design of laser welding machines are optimized for lithium-ion battery production. Key components include:
- Laser Source: Generates the high-energy beam for welding.
- Optical System: Focuses and directs the laser beam with precision.
- Workstation: Provides a stable platform for battery components.
- Control System: Ensures accurate parameter adjustments for different materials and thicknesses.
The compact and modular design allows for easy integration into production lines, while advanced cooling systems prevent overheating during continuous operation. These features make laser welding machines highly efficient and reliable for battery manufacturing.
How Does the Working Principle of Laser Welding Machines Ensure Precision?
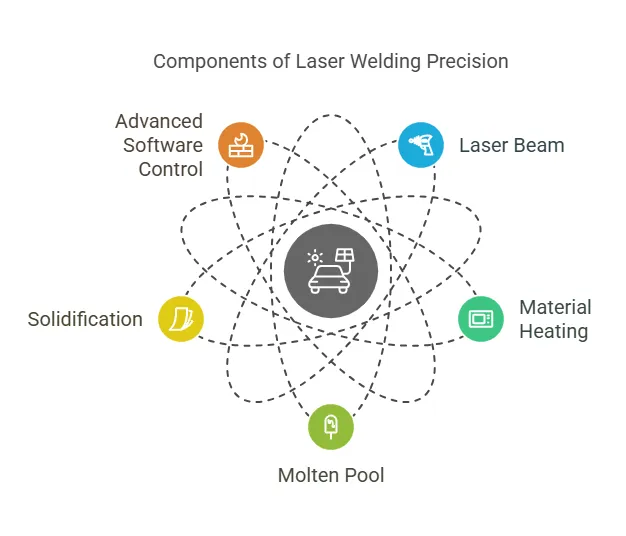
The working principle of laser welding machines revolves around the use of a concentrated laser beam to melt and fuse materials. Here’s how it works:
- The laser beam is directed onto the surface of the battery components.
- The energy from the beam heats the material to its melting point, creating a molten pool.
- As the laser moves, the molten pool solidifies, forming a strong weld.
This process is controlled by advanced software, which adjusts parameters such as power, speed, and focus to achieve optimal results. The non-contact nature of laser welding minimizes contamination and ensures high precision, making it ideal for delicate battery components.
What Are the Key Applications of Laser Welding Machines in Lithium-ion Battery Manufacturing?
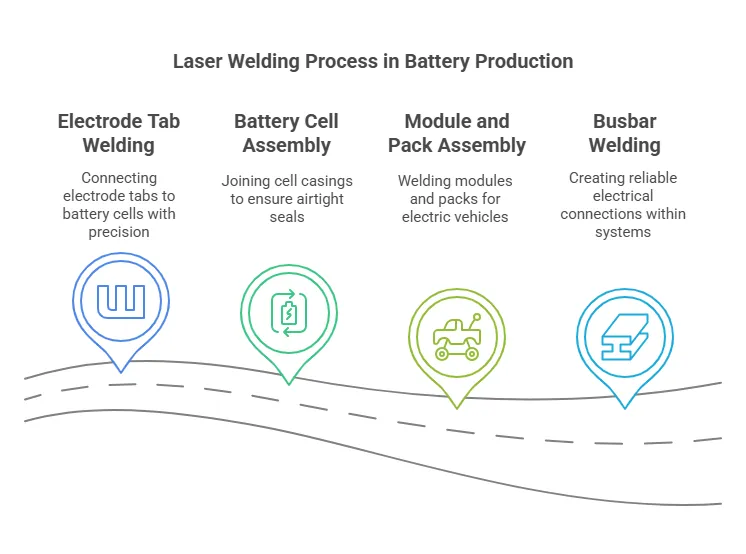
Laser welding machines play a critical role in various stages of lithium-ion battery production, including:
- Electrode Tab Welding: Connecting electrode tabs to battery cells with high precision.
- Battery Cell Assembly: Joining cell casings and ensuring airtight seals.
- Module and Pack Assembly: Welding battery modules and packs for electric vehicles and energy storage systems.
- Busbar Welding: Creating reliable electrical connections within battery systems.
These applications highlight the versatility and importance of laser welding machines in producing safe, durable, and high-performance lithium-ion batteries.
Why is the Optimal Work Environment Crucial for Laser Welding Machines?
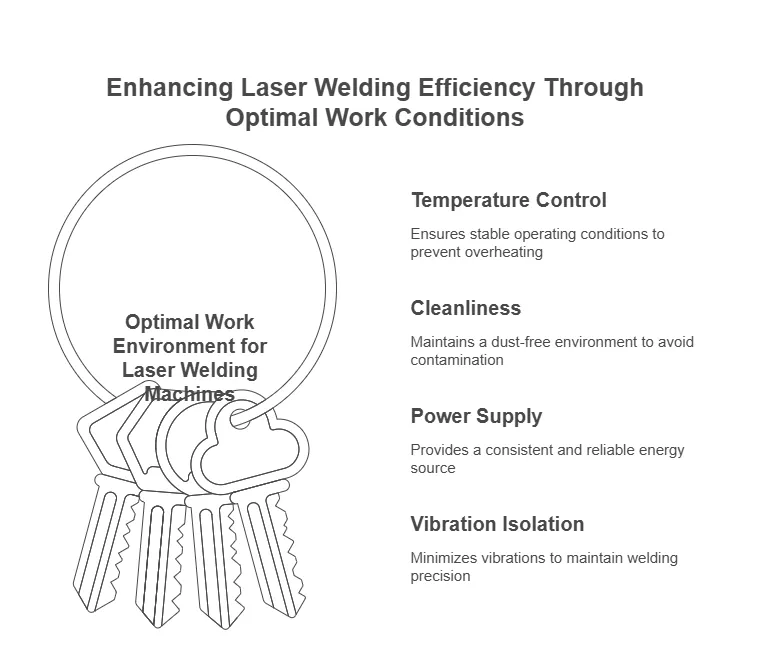
To achieve the best performance and longevity, laser welding machines require an optimal work environment. Key factors include:
- Temperature Control: Maintaining a stable temperature to prevent overheating.
- Cleanliness: Ensuring a dust-free environment to avoid contamination.
- Power Supply: Providing a consistent and reliable power source.
- Vibration Isolation: Minimizing vibrations that could affect welding precision.
By creating an ideal work environment, manufacturers can maximize the efficiency and accuracy of laser welding machines, ensuring consistent quality in lithium-ion battery production.
How is Testing and Quality Control Ensured in Laser Welding Machines for Lithium-ion Batteries?
Testing and quality control are critical to ensuring the reliability and performance of laser welding machines in lithium-ion battery production. Key steps include:
- Weld Strength Testing: Evaluating the durability of welds through tensile and shear tests.
- Visual Inspection: Using microscopes or cameras to check for defects like cracks or porosity.
- Leak Testing: Ensuring airtight seals in battery casings to prevent electrolyte leakage.
- Process Monitoring: Implementing real-time monitoring systems to track welding parameters like power, speed, and focus.
These measures help manufacturers maintain high standards, reduce defects, and ensure the safety and longevity of lithium-ion batteries.
What Are the Safety Precautions and Best Practices for Using Laser Welding Machines?
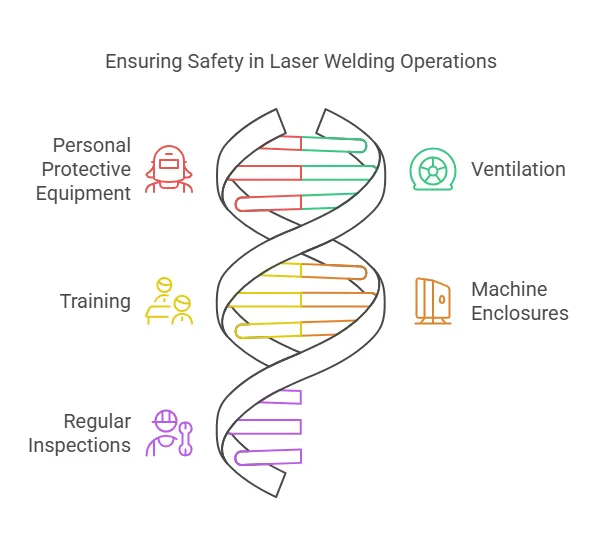
Safety is paramount when operating laser welding machines. Here are essential precautions and best practices:
- Personal Protective Equipment (PPE): Operators should wear laser safety goggles, gloves, and protective clothing.
- Ventilation: Ensure proper ventilation to avoid inhaling fumes generated during welding.
- Training: Provide comprehensive training to operators on machine operation and emergency procedures.
- Machine Enclosures: Use protective enclosures to prevent accidental exposure to laser beams.
- Regular Inspections: Conduct routine checks on the machine’s components to ensure safe operation.
By following these guidelines, manufacturers can minimize risks and create a safer working environment.
How to Maintain and Care for Laser Welding Machines for Lithium-ion Batteries?
Proper maintenance and care are essential to extend the lifespan and performance of laser welding machines. Key practices include:
- Cleaning Optics: Regularly clean lenses and mirrors to maintain beam quality.
- Cooling System Maintenance: Check and refill coolant levels to prevent overheating.
- Calibration: Periodically calibrate the laser source and optical system for accuracy.
- Component Inspection: Replace worn-out parts like nozzles and filters to avoid breakdowns.
- Software Updates: Keep the control system updated with the latest firmware for improved functionality.
A well-maintained machine ensures consistent performance and reduces downtime in production.
What Are the Common Challenges in Laser Welding for Lithium-ion Batteries and How to Overcome Them?
Laser welding for lithium-ion batteries presents several challenges, but they can be addressed with the right strategies:
- Material Sensitivity: Thin materials like aluminum and copper can warp or burn. Solution: Optimize laser parameters (power, pulse duration) to minimize heat input.
- Reflectivity: Highly reflective materials can deflect the laser beam. Solution: Use lasers with shorter wavelengths or surface treatments to reduce reflectivity.
- Precision Requirements: Small components require extreme accuracy. Solution: Implement advanced vision systems for precise alignment.
- Contamination: Dust or oxidation can affect weld quality. Solution: Work in a cleanroom environment and use shielding gases.
By addressing these challenges, manufacturers can achieve high-quality welds and improve production efficiency.
What Technological Advances Are Shaping Laser Welding for Lithium-ion Batteries?
Recent technological advancements are revolutionizing laser welding for lithium-ion batteries:
- Fiber Lasers: Offer higher efficiency and beam quality, enabling faster and more precise welding.
- Automation: Integration with robotics and AI for consistent, high-speed production.
- Real-Time Monitoring: Advanced sensors and software for instant feedback and adjustments.
- Green Lasers: Improved absorption on reflective materials like copper, reducing energy waste.
- Modular Systems: Customizable setups for different battery designs and production needs.
These innovations are driving the industry forward, enabling the production of safer, more efficient, and cost-effective lithium-ion batteries.