A Lithium Battery Cell Machine is a critical piece of equipment used in the manufacturing and assembly of lithium-ion battery cells. These machines ensure the precision and efficiency required to create batteries for a variety of applications, from smartphones to electric vehicles. The production process involves multiple stages, including electrode preparation, stacking or winding of materials, assembly, and sealing of the battery cells. By automating these processes, the machine significantly reduces the potential for human error, ensuring consistent quality and performance. The primary components, such as the coating unit, slitting machine, and electrolyte filling system, work in harmony to produce high-quality cells. Each step is meticulously controlled to guarantee the final product meets stringent standards. The machine’s role extends beyond just manufacturing, as it also contributes to safety by conducting essential quality testing, such as electrical and cycle testing. This ensures the batteries perform reliably and meet regulatory standards. As lithium battery technology continues to evolve, the role of these machines in industries like consumer electronics, automotive, and energy storage will remain indispensable for creating efficient and sustainable energy solutions.
What is a Lithium Battery Cell Machine?
A lithium battery cell machine is a specialized piece of equipment designed for the manufacturing and assembly of lithium-ion battery cells. These machines are integral to the production process, ensuring precision, efficiency, and consistency in creating battery cells that power a wide range of devices, from smartphones to electric vehicles. The machine typically handles various stages of production, including electrode preparation, cell assembly, and sealing, making it a cornerstone in the battery manufacturing industry.
How Does a Lithium Battery Cell Machine Work?
The operation of a lithium battery cell machine involves several critical steps, each contributing to the creation of a high-quality battery cell. Here’s a step-by-step breakdown:
- Electrode Preparation: The machine starts by preparing the electrodes. This involves coating metal foils (usually aluminum for the cathode and copper for the anode) with active materials, drying them, and then slitting them into precise widths.
- Stacking or Winding: Depending on the type of battery cell (prismatic, cylindrical, or pouch), the machine either stacks the electrodes and separators or winds them into a jelly roll configuration.
- Assembly: The prepared electrodes are then assembled into a cell casing. This step includes inserting the electrodes, adding electrolytes, and sealing the cell to prevent leaks.
- Formation and Testing: After assembly, the cell undergoes a formation process where it is charged and discharged to stabilize its performance. The machine also conducts various tests to ensure the cell meets quality standards.
Key Components of a Lithium Battery Cell Machine
Understanding the key components of a lithium battery cell machine can provide insight into its functionality and importance in the production process. Here are the main components:
- Coating Unit: Applies the active material onto the metal foils.
- Drying Oven: Removes solvents from the coated electrodes.
- Slitting Machine: Cuts the coated electrodes into precise widths.
- Stacking/Winding Unit: Assembles the electrodes and separators into the desired cell configuration.
- Electrolyte Filling System: Injects the electrolyte into the cell.
- Sealing Unit: Ensures the cell is hermetically sealed.
- Formation and Testing Equipment: Charges, discharges, and tests the cell for quality assurance.
Working Principle of a Lithium Battery Cell Machine
The working principle of a lithium battery cell machine revolves around precision and automation. The machine is designed to handle each step of the battery cell manufacturing process with minimal human intervention, ensuring consistency and reducing the risk of errors. Here’s how it works:
- Automation: The machine automates the entire process, from electrode preparation to cell assembly, ensuring each step is carried out with precision.
- Precision Engineering: Each component of the machine is engineered to perform its task with high accuracy, ensuring the final product meets stringent quality standards.
- Quality Control: Integrated sensors and monitoring systems continuously check the quality of the materials and the final product, ensuring any defects are detected and corrected early in the process.
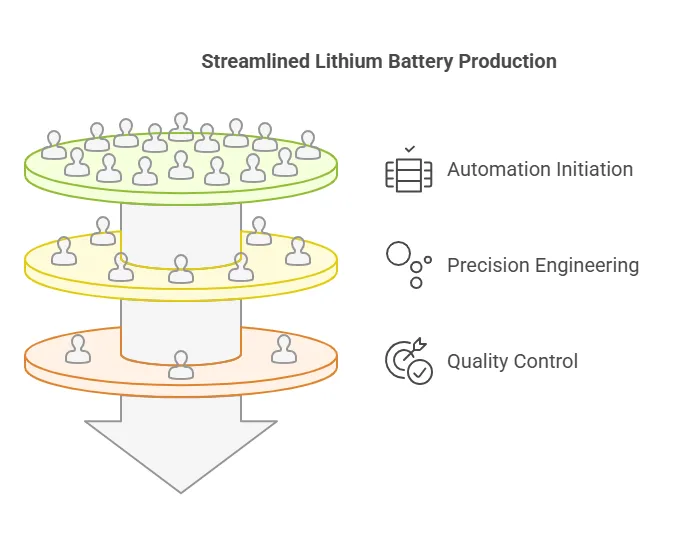
Applications of Lithium Battery Cell Machines in the Industry
Lithium battery cell machines are used across various industries, playing a crucial role in the production of batteries for numerous applications. Here are some key industries where these machines are indispensable:
- Consumer Electronics: Manufacturing batteries for smartphones, laptops, and other portable devices.
- Automotive: Producing batteries for electric vehicles (EVs) and hybrid vehicles.
- Energy Storage: Creating batteries for renewable energy storage systems, such as solar and wind power.
- Industrial Equipment: Powering batteries for industrial machinery and equipment.
In each of these industries, the precision and efficiency of lithium battery cell machines ensure the production of reliable, high-performance batteries that meet the demands of modern technology.
What Are the Environmental Considerations for Lithium Battery Cell Machines?
Lithium battery cell machines play a critical role in the production of energy storage solutions, but their operation and the manufacturing process itself have environmental implications. Here’s what to consider:
- Energy Consumption: These machines often require significant energy to operate, which can contribute to a higher carbon footprint if the energy source is not renewable.
- Material Waste: The production process generates waste materials, such as electrode trimmings and electrolyte residues, which need proper disposal or recycling.
- Chemical Handling: The use of electrolytes and other chemicals in battery production can pose environmental risks if not managed correctly.
- Recycling and Reuse: Manufacturers are increasingly focusing on designing machines that support the recycling of battery components, reducing waste and promoting a circular economy.
To mitigate these impacts, manufacturers are adopting energy-efficient technologies, implementing waste reduction strategies, and ensuring compliance with environmental regulations.
Why is Quality Testing Essential in Lithium Battery Cell Manufacturing?
Quality testing is a non-negotiable aspect of lithium battery cell manufacturing, ensuring the safety, reliability, and performance of the final product. Here’s why it matters:
- Safety Assurance: Defective batteries can pose serious risks, including overheating, fires, or explosions. Rigorous testing helps identify and eliminate such risks.
- Performance Consistency: Quality tests ensure that each battery cell meets specific performance criteria, such as capacity, voltage, and cycle life.
- Regulatory Compliance: Batteries must adhere to international standards and regulations, which require thorough testing and documentation.
How is Quality Testing Conducted? (Step-by-Step)
- Initial Inspection: Visual and dimensional checks to ensure components meet specifications.
- Electrical Testing: Measures voltage, capacity, and internal resistance.
- Cycle Testing: Simulates charge-discharge cycles to evaluate lifespan.
- Environmental Testing: Exposes cells to extreme temperatures, humidity, and vibration to assess durability.
- Safety Testing: Includes overcharge, short-circuit, and crush tests to ensure safe operation.
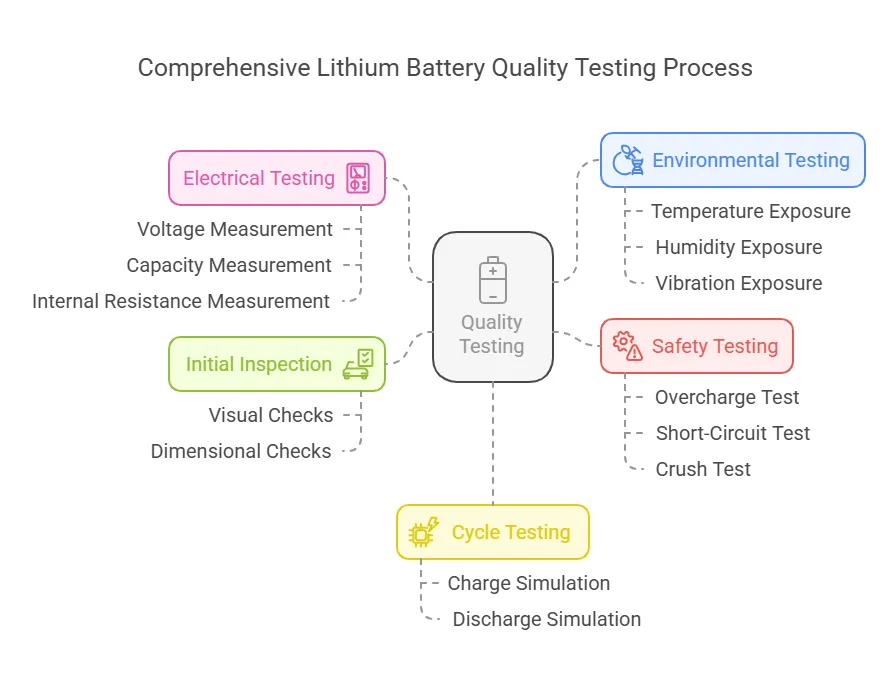
How to Maintain and Care for Lithium Battery Cell Machines?
Proper maintenance and care are crucial to ensure the longevity and efficiency of lithium battery cell machines. Here’s how to keep them in optimal condition:
- Regular Cleaning: Dust and debris can interfere with machine components. Regular cleaning prevents contamination and ensures smooth operation.
- Lubrication: Moving parts require periodic lubrication to reduce wear and tear.
- Calibration: Sensors and precision components should be calibrated regularly to maintain accuracy.
- Inspection and Replacement: Worn-out parts, such as belts or seals, should be inspected and replaced promptly to avoid breakdowns.
Maintenance Checklist (ul li format)
- Clean electrodes and coating units daily.
- Lubricate moving parts weekly.
- Calibration of sensors and testing equipment monthly.
- Inspect and replace worn components quarterly.
What Are the Common Challenges and Solutions in Lithium Battery Cell Manufacturing?
Lithium battery cell manufacturing is a complex process that comes with its own set of challenges. Here are some common issues and how to address them:
-
Electrode Coating Uniformity:
- Challenge: Inconsistent coating can lead to poor battery performance.
- Solution: Use advanced coating machines with real-time monitoring and adjustment capabilities.
-
Electrolyte Filling Accuracy:
- Challenge: Over- or under-filling can affect battery safety and performance.
- Solution: Implement automated filling systems with precise volume control.
-
Cell Sealing Integrity:
- Challenge: Improper sealing can cause leaks or safety hazards.
- Solution: Use high-precision sealing machines and conduct rigorous leak tests.
-
Production Speed vs. Quality:
- Challenge: Balancing high production rates with quality control.
- Solution: Integrate inline quality testing systems to detect defects without slowing down production.
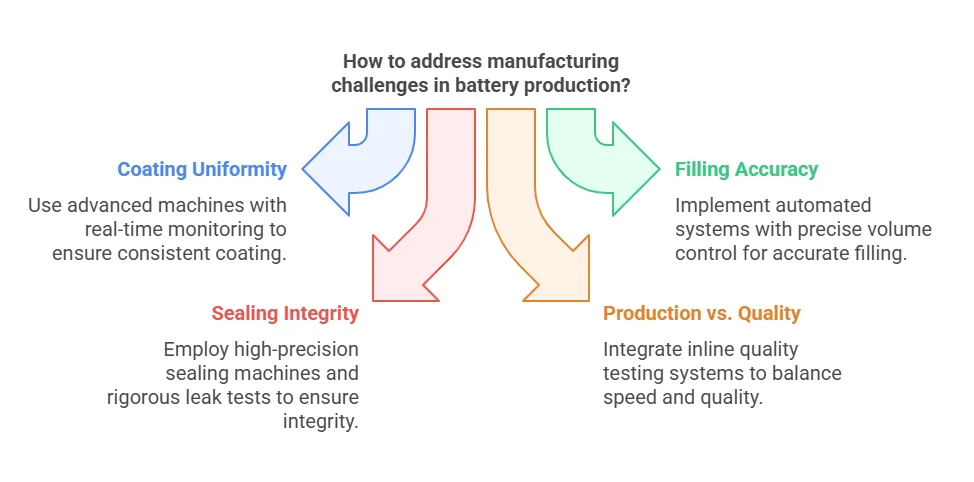
Why Are Safety Precautions Critical When Operating Lithium Battery Cell Machines?
Operating lithium battery cell machines involves handling hazardous materials and high-energy processes, making safety precautions essential. Here’s why:
- Chemical Hazards: Electrolytes and other chemicals used in battery production can be toxic or flammable.
- Electrical Risks: High-voltage equipment poses risks of electric shock or short circuits.
- Mechanical Hazards: Moving parts can cause injuries if not properly guarded.
Key Safety Precautions (ul li format)
- Wear appropriate personal protective equipment (PPE), such as gloves, goggles, and lab coats.
- Ensure proper ventilation to avoid inhaling harmful fumes.
- Regularly inspect electrical systems and grounding to prevent shocks.
- Install safety guards on moving parts to prevent accidents.
- Train operators on emergency procedures, including fire safety and spill response.
By adhering to these precautions, manufacturers can create a safer working environment and reduce the risk of accidents or injuries.
Lithium battery cell machines are pivotal in the production of lithium-ion batteries, which power everything from smartphones to electric vehicles. These machines automate critical steps in the manufacturing process, including electrode preparation, electrode stacking/winding, assembly, and sealing, resulting in high-quality, consistent battery cells. The machines are composed of specialized components such as coating units, drying ovens, and slitting machines that work together to ensure precision in each stage of production. Furthermore, the integration of quality control systems helps identify and eliminate defects early on, ensuring that the final product adheres to rigorous safety and performance standards. As these machines are essential to industries such as consumer electronics, automotive, and energy storage, their efficiency directly impacts the reliability and safety of the batteries produced. Alongside manufacturing, these machines also play a role in minimizing environmental impact by optimizing energy use and supporting recycling processes. With their ability to streamline production while maintaining high safety standards, lithium battery cell machines are crucial to the advancement of energy storage technology, meeting the demands of modern technology and contributing to a sustainable future.