Prismatic cell assembly is at the forefront of modern energy storage technology, revolutionizing industries with its compact design and high energy density. Unlike traditional battery formats, prismatic cells offer unparalleled space efficiency and reliability, making them ideal for electric vehicles, renewable energy storage, and consumer electronics. From the intricate manufacturing process to the cutting-edge innovations driving their future, prismatic cell assembly is shaping the way we power our world. Join us as we delve into the inner workings, applications, and future trends of this transformative technology.
What is Prismatic Cell Assembly?
Prismatic cell assembly refers to the process of constructing prismatic lithium-ion batteries, which are widely used in various applications due to their high energy density and compact design. Unlike cylindrical or pouch cells, prismatic cells are characterized by their rectangular shape, making them ideal for applications where space efficiency is critical. These cells are commonly used in electric vehicles (EVs), renewable energy storage systems, and portable electronics. The assembly process involves stacking electrode layers, separators, and electrolytes in a precise manner to ensure optimal performance and safety.
How Does the Prismatic Cell Assembly Process and Workflow Work?
The prismatic cell assembly process is a highly controlled and precise workflow that ensures the reliability and efficiency of the final product. Here’s a step-by-step breakdown of the process:
-
Electrode Preparation:
- Electrode sheets (anode and cathode) are coated with active materials, dried, and cut into precise dimensions.
- These sheets are then slit into smaller strips to fit the prismatic cell design.
-
Stacking or Winding:
- The electrode strips are either stacked in layers or wound, depending on the cell design.
- Separators are placed between the anode and cathode layers to prevent short circuits.
-
Tab Welding:
- Tabs (current collectors) are welded to the electrodes to facilitate electrical connections.
-
Encapsulation:
- The stacked or wound layers are placed into a prismatic aluminum or steel casing.
- The casing is then sealed to ensure no leakage of electrolytes.
-
Electrolyte Filling:
- The cell is filled with a liquid electrolyte, which facilitates ion movement between the electrodes.
-
Formation and Testing:
- The assembled cell undergoes a formation process, where it is charged and discharged to stabilize its performance.
- Rigorous testing is conducted to ensure safety, capacity, and longevity.
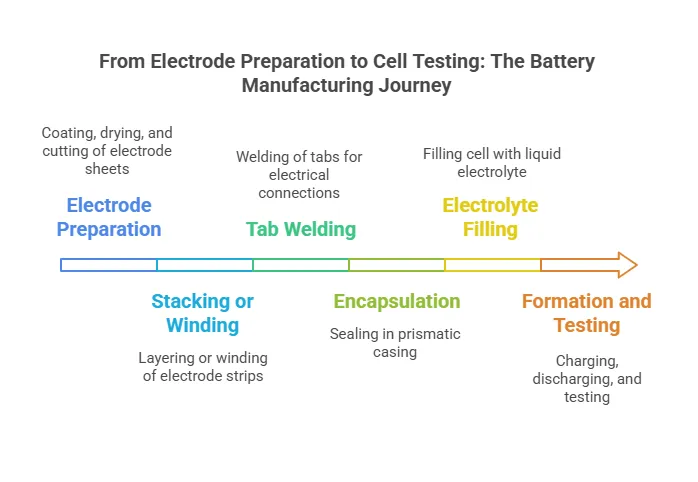
What is the Working Principle of Prismatic Cell Assembly?
The working principle of prismatic cell assembly revolves around the efficient storage and release of electrical energy through electrochemical reactions. Inside the prismatic cell:
- Anode and Cathode: The anode (typically made of graphite) and cathode (often composed of lithium metal oxides) facilitate the movement of lithium ions during charging and discharging.
- Separator: A porous membrane separates the anode and cathode, allowing ion flow while preventing electrical contact.
- Electrolyte: The electrolyte acts as a medium for ion transport between the electrodes.
- Casing: The prismatic casing provides structural integrity and protects the internal components from external damage.
During charging, lithium ions move from the cathode to the anode through the electrolyte. During discharging, the ions return to the cathode, releasing energy in the process.
What are the Applications of Prismatic Cell Assembly?
Prismatic cell assembly is integral to a wide range of industries due to its versatility and efficiency. Key applications include:
- Electric Vehicles (EVs): Prismatic cells are widely used in EV batteries due to their high energy density and space-saving design.
- Renewable Energy Storage: These cells are employed in solar and wind energy storage systems to store excess energy for later use.
- Consumer Electronics: Devices like laptops, smartphones, and power banks often use prismatic cells for their compact size and long-lasting performance.
- Industrial Equipment: Prismatic cells power heavy machinery, drones, and other industrial applications requiring reliable energy sources.
How to Create an Optimal Work Environment for Prismatic Cell Assembly?
Creating an optimal work environment for prismatic cell assembly is crucial to ensuring product quality and worker safety. Here are some key considerations:
-
Cleanroom Facilities:
- Assembly should take place in a cleanroom to prevent contamination from dust and particles, which can affect cell performance.
- Air filtration systems and controlled humidity levels are essential.
-
Temperature and Humidity Control:
- Maintain a stable temperature (typically 20-25°C) and humidity level (below 1% relative humidity) to avoid moisture absorption by the electrolyte.
-
Automated Equipment:
- Use precision machinery for stacking, welding, and sealing to minimize human error and ensure consistency.
-
Safety Measures:
- Implement strict safety protocols, including fire suppression systems and protective gear, to handle flammable electrolytes and high-energy materials.
-
Quality Control:
- Regular inspections and testing should be conducted at every stage of the assembly process to detect and rectify defects early.
By adhering to these guidelines, manufacturers can ensure efficient production and high-quality prismatic cells.
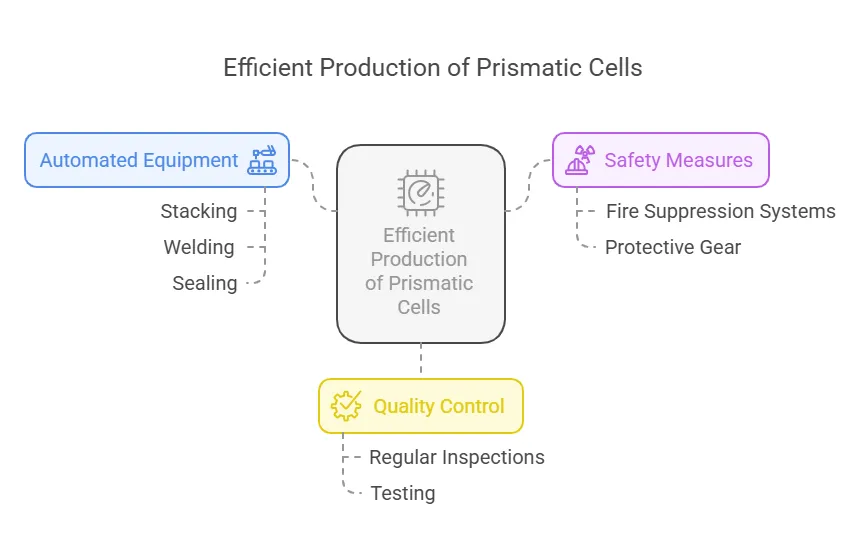
What is Product Testing and Quality Control in Prismatic Cell Assembly?
Product testing and quality control are critical steps in prismatic cell assembly to ensure the reliability, safety, and performance of the final product. These processes involve rigorous checks at every stage of production to identify and address potential defects. Key testing methods include:
-
Electrical Testing:
- Measures voltage, capacity, and internal resistance to ensure the cell meets specifications.
- Detects issues like short circuits or inconsistent performance.
-
Mechanical Testing:
- Evaluates the structural integrity of the cell casing and seals.
- Ensures the cell can withstand physical stress during use.
-
Thermal Testing:
- Assesses the cell’s behavior under high and low temperatures.
- Identifies risks of overheating or thermal runaway.
-
Cycle Life Testing:
- Simulates repeated charging and discharging to determine the cell’s lifespan.
- Helps predict long-term performance and durability.
-
Safety Testing:
- Includes nail penetration, crush, and overcharge tests to evaluate the cell’s response to extreme conditions.
By implementing these testing protocols, manufacturers can deliver high-quality prismatic cells that meet industry standards and customer expectations.
Why are Safety Precautions Crucial in Prismatic Cell Assembly?
Safety precautions in prismatic cell assembly are essential to protect workers, equipment, and the environment. The assembly process involves handling flammable electrolytes, high-energy materials, and sensitive components, making safety a top priority. Key precautions include:
-
Personal Protective Equipment (PPE):
- Workers must wear gloves, goggles, and flame-resistant clothing to minimize exposure to hazardous materials.
-
Fire Safety Measures:
- Install fire suppression systems and keep fire extinguishers readily available.
- Use non-flammable materials in the assembly area.
-
Ventilation Systems:
- Ensure proper ventilation to disperse fumes from electrolytes and prevent the buildup of hazardous gases.
-
Automated Handling:
- Use robotics for tasks like electrolyte filling and welding to reduce human exposure to risks.
-
Emergency Protocols:
- Train workers on emergency response procedures, including evacuation and first aid.
By adhering to these safety measures, manufacturers can create a secure work environment and prevent accidents.
How to Address Common Issues and Troubleshooting in Prismatic Cell Assembly?
Despite careful assembly, prismatic cells can encounter issues that affect performance. Here are some common problems and troubleshooting steps:
-
Low Capacity:
- Cause: Inconsistent electrode coating or improper electrolyte filling.
- Solution: Recheck the coating process and ensure precise electrolyte volume.
-
High Internal Resistance:
- Cause: Poor tab welding or contamination.
- Solution: Inspect and re-weld tabs, and maintain a cleanroom environment.
-
Swelling of the Cell:
- Cause: Gas generation due to overcharging or electrolyte decomposition.
- Solution: Adjust charging parameters and use high-quality electrolytes.
-
Leakage:
- Cause: Improper sealing of the cell casing.
- Solution: Verify sealing equipment and replace faulty casings.
-
Thermal Runaway:
- Cause: Overheating or internal short circuits.
- Solution: Implement thermal management systems and improve separator quality.
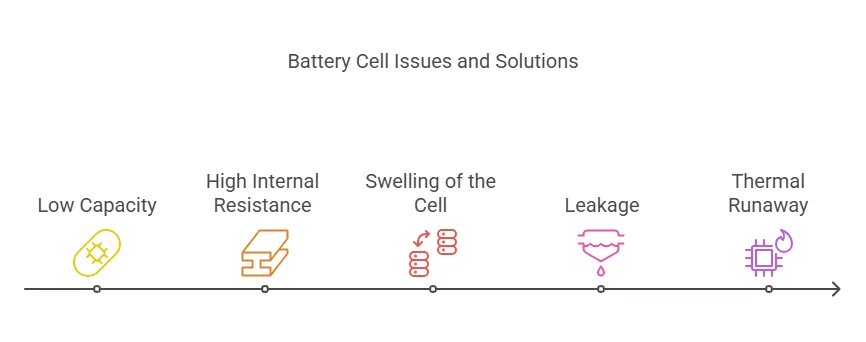
By identifying and resolving these issues early, manufacturers can enhance product reliability and reduce waste.
How to Maintain and Care for Prismatic Cell Assembly Equipment?
Proper maintenance of prismatic cell assembly equipment is essential to ensure consistent production quality and extend the lifespan of machinery. Here’s a step-by-step guide:
-
Regular Cleaning:
- Clean equipment surfaces and components to prevent contamination from dust and debris.
-
Lubrication:
- Apply lubricants to moving parts to reduce friction and wear.
-
Calibration:
- Regularly calibrate machines like welders and coating equipment to maintain precision.
-
Inspection:
- Conduct routine inspections to identify signs of wear, corrosion, or damage.
-
Software Updates:
- Update control software to ensure optimal performance and compatibility with new technologies.
-
Training:
- Train operators on proper equipment usage and maintenance procedures.
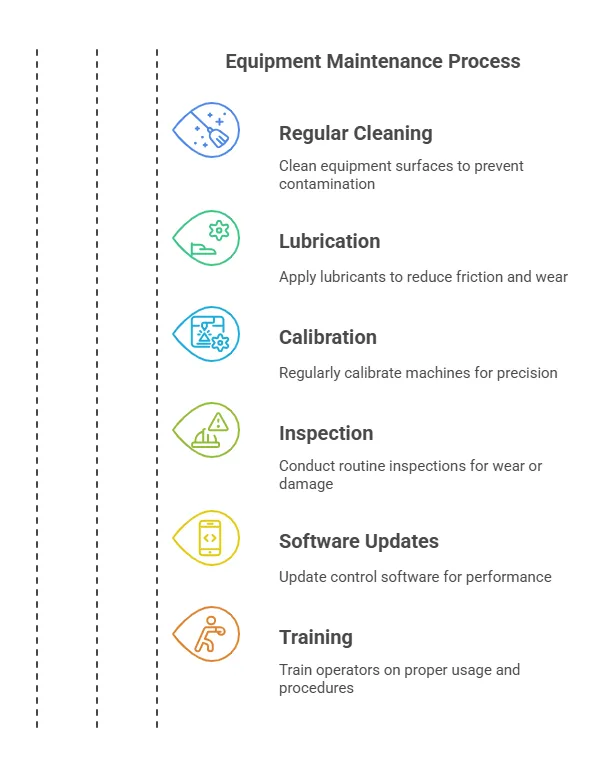
By following these steps, manufacturers can minimize downtime and ensure smooth operations.
What are the Future Trends and Innovations in Prismatic Cell Assembly?
The prismatic cell assembly industry is evolving rapidly, driven by advancements in technology and growing demand for energy storage solutions. Key trends and innovations include:
-
Solid-State Batteries:
- Replacing liquid electrolytes with solid alternatives to improve safety and energy density.
-
Automation and AI:
- Using AI-driven systems to optimize assembly processes and detect defects in real-time.
-
Sustainable Materials:
- Developing eco-friendly materials for electrodes and casings to reduce environmental impact.
-
Modular Designs:
- Creating modular prismatic cells that can be easily replaced or upgraded in battery packs.
-
Fast Charging Technologies:
- Innovating electrode materials and cell designs to enable faster charging without compromising lifespan.
-
Integration with IoT:
- Embedding sensors in prismatic cells to monitor performance and health in real-time.
These innovations are shaping the future of prismatic cell assembly, making batteries safer, more efficient, and environmentally friendly.
What are Solid-State Prismatic Batteries, and Why are They the Next Big Thing?
Solid-state prismatic batteries represent a groundbreaking advancement in energy storage technology. Unlike traditional lithium-ion batteries that use liquid electrolytes, solid-state batteries employ solid electrolytes, offering several advantages:
-
Enhanced Safety:
- Solid electrolytes are non-flammable, reducing the risk of thermal runaway and fires.
- They are more stable under high temperatures and physical stress.
-
Higher Energy Density:
- Solid-state batteries can store more energy in the same volume, making them ideal for applications like electric vehicles (EVs) and portable electronics.
-
Longer Lifespan:
- The absence of liquid electrolytes minimizes degradation, leading to a longer cycle life.
-
Faster Charging:
- Solid-state batteries can support higher charging currents, enabling ultra-fast charging without damaging the cell.
How Do Solid-State Prismatic Batteries Work?
-
Electrode Design:
- The anode and cathode are made from advanced materials like lithium metal or silicon-based compounds.
-
Solid Electrolyte Layer:
- A thin, solid electrolyte layer separates the anode and cathode, allowing ion transport while preventing electrical contact.
-
Stacking Process:
- Electrode and electrolyte layers are stacked in a prismatic configuration to maximize energy density and space efficiency.
-
Encapsulation:
- The stacked layers are enclosed in a prismatic casing, which provides structural support and protection.
While solid-state prismatic batteries are still in the development and commercialization phase, they hold immense potential to revolutionize industries like EVs, renewable energy storage, and consumer electronics.
How to Implement Eco-Friendly and Sustainable Prismatic Cell Manufacturing Practices?
As the demand for prismatic cells grows, so does the need for sustainable manufacturing practices. Eco-friendly production not only reduces environmental impact but also aligns with global regulations and consumer preferences. Here’s how manufacturers can adopt sustainable practices:
Step-by-Step Guide to Sustainable Prismatic Cell Manufacturing:
-
Use Recycled Materials:
- Source recycled aluminum and steel for casings to reduce raw material consumption.
- Recover and reuse materials from end-of-life batteries.
-
Energy-Efficient Production:
- Invest in renewable energy sources like solar or wind to power manufacturing facilities.
- Optimize equipment and processes to minimize energy waste.
-
Non-Toxic Electrolytes:
- Replace traditional liquid electrolytes with non-toxic, biodegradable alternatives.
- Explore solid-state electrolytes for safer and greener options.
-
Waste Management:
- Implement recycling programs for production waste, such as electrode scraps and used electrolytes.
- Treat and dispose of hazardous materials responsibly.
-
Water Conservation:
- Use closed-loop water systems to reduce water consumption during electrode coating and cleaning processes.
-
Sustainable Supply Chain:
- Partner with suppliers who adhere to environmental standards and ethical practices.
- Prioritize local sourcing to reduce transportation emissions.
Benefits of Sustainable Manufacturing:
- Reduced Carbon Footprint: Lower greenhouse gas emissions contribute to climate change mitigation.
- Cost Savings: Energy-efficient processes and waste reduction can lower production costs.
- Brand Reputation: Eco-friendly practices enhance brand image and attract environmentally conscious customers.
By integrating these sustainable practices, manufacturers can produce prismatic cells that are not only high-performing but also environmentally responsible.
Prismatic cell assembly is a highly precise process that constructs rectangular lithium-ion batteries used in electric vehicles, renewable energy storage, and consumer electronics. The assembly involves preparing electrodes, stacking or winding layers, welding tabs, encapsulating in a casing, filling with electrolyte, and rigorous testing. These cells operate through electrochemical reactions, with lithium ions moving between the anode and cathode during charging and discharging. Prismatic cells offer high energy density, compact design, and enhanced safety, making them versatile for various industries. Future innovations include solid-state batteries, AI-driven automation, and sustainable manufacturing practices, which aim to improve safety, efficiency, and environmental impact.