Los equipos de fabricación de baterías están en el corazón de la innovación energética moderna. Esta maquinaria especializada es crucial para producir baterías de alta calidad que alimentan todo, desde vehículos eléctricos hasta sistemas de energía renovable. En este blog, exploraremos los componentes esenciales y la estructura de los equipos de fabricación de baterías, cómo funcionan y sus aplicaciones clave en diversas industrias. Ya sea que esté interesado en los detalles técnicos o en el impacto más amplio en la sostenibilidad, comprender los equipos de fabricación de baterías es clave para desbloquear el potencial de las soluciones energéticas de próxima generación.
¿Qué es el equipo de fabricación de baterías?
El equipo de fabricación de baterías se refiere a la maquinaria especializada que se utiliza para producir varios tipos de baterías, incluidas las baterías de iones de litio, de plomo-ácido y de estado sólido. Estos sistemas automatizan procesos críticos como la preparación de electrodos, el ensamblaje de celdas y las pruebas de calidad para garantizar la precisión, la escalabilidad y la seguridad en la producción.
¿Por qué es importante?
- Eficacia: Automatiza la producción de grandes volúmenes con una mínima intervención humana.
- Consistencia: Garantiza una calidad uniforme de la batería para el rendimiento y la seguridad.
- Innovación: Permite diseños de baterías de próxima generación (por ejemplo, mayor densidad de energía).
Industrias clave que confían en estos equipos:
- Vehículos eléctricos (VE)
- Electrónica de consumo
- Almacenamiento de energía renovable
¿Cuáles son los componentes y la estructura de los equipos de fabricación de baterías?
Las líneas de producción de baterías modernas integran múltiples subsistemas:
-
Unidades de fabricación de electrodos
- Máquinas de recubrimiento: Aplicar materiales activos a láminas metálicas.
- Calandrias: Comprima los electrodos a espesores precisos.
-
Módulos de ensamblaje de celdas
- Máquinas apiladoras/bobinadoras: Ánodos de capa, separadores y cátodos.
- Sistemas de soldadura: Lengüetas y carcasas seguras.
-
Sistemas de formación y ensayo
- Unidades de carga/descarga: Activar celdas y medir la capacidad.
- Inspectores de rayos X: Detectar defectos internos.
Componentes auxiliares críticos:
- Habitaciones secas (control de humedad)
- Cortadoras láser
- Estaciones de llenado de electrolitos
¿Cómo funcionan los equipos de fabricación de baterías? Un flujo paso a paso
Paso 1: Preparación del electrodo
- Mezcla: Los materiales activos, aglutinantes y disolventes se mezclan en lodos.
- Capa: Los lodos se aplican uniformemente a las láminas de cobre/aluminio.
- Secado: Las láminas recubiertas pasan a través de los hornos para evaporar los disolventes.
Paso 2: Ensamblaje de la célula
- Corte: Los electrodos secos se cortan en tiras.
- Apilamiento/bobinado: Los ánodos, separadores y cátodos están estratificados.
- Incorporados: Las células se sellan en bolsas o carcasas metálicas.
Paso 3: Acabado
- Inyección de electrolitos (para pilas líquidas).
- Ciclismo en formación para estabilizar el rendimiento.
- Clasificación Basado en métricas de capacidad/voltaje.
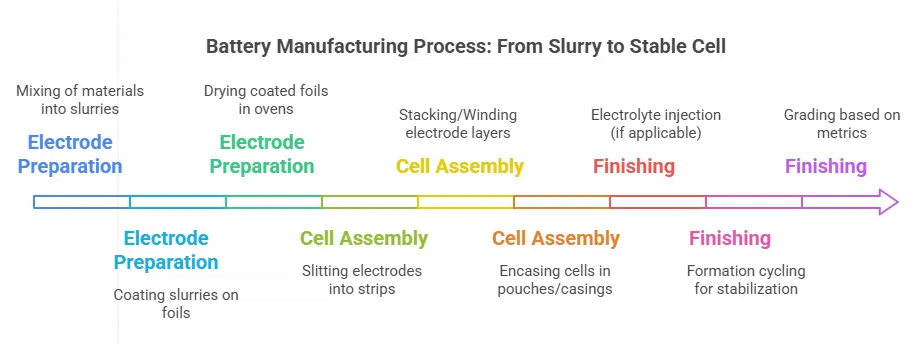
¿Cuáles son los principios de funcionamiento de los equipos de fabricación de baterías?
Los equipos de baterías funcionan según tres principios básicos:
1. Ingeniería de precisión
- Los sensores láser y los controles impulsados por IA mantienen una precisión de nivel micrométrico en el recubrimiento/corte.
2. Optimización electroquímica
- Los entornos controlados (por ejemplo, punto de rocío < -40 °C) evitan la degradación inducida por la humedad.
3. Automatización e integración de datos
- Los PLC (controladores lógicos programables) sincronizan las cintas transportadoras, los robots y los sistemas de inspección.
- Los sensores IoT recopilan datos en tiempo real para el mantenimiento predictivo.
Ejemplo: Operación de la máquina bobinadora
- Paso 1: Alimenta las capas de ánodo/separador/cátodo de los rodillos.
- Paso 2: Los enrolla en un "rollo de gelatina" a través del control de tensión.
- Paso 3: Lengüetas terminales de soldaduras ultrasónicas.
¿Cuáles son las aplicaciones clave de los equipos de fabricación de baterías?
1. Vehículos eléctricos (VE)
- Produce celdas prismáticas/de bolsa de alta capacidad para un alcance más largo.
- El equipo debe cumplir con los estándares de durabilidad de grado automotriz (por ejemplo, ISO 16949).
2. Electrónica de consumo
- Las máquinas miniaturizadas fabrican celdas compactas de iones de litio para teléfonos inteligentes / computadoras portátiles.
3. Almacenamiento en red
- Los sistemas de servicio pesado construyen baterías de gran formato para parques solares/eólicos.
Aplicaciones emergentes:
- Baterías de estado sólido: Requiere equipo de deposición al vacío.
- Reciclaje: Desmontaje/reutilización de máquinas para baterías gastadas.
En qué se diferencian los equipos de fabricación de baterías para varios tipos de baterías (iones de litio, iones de sodio, etc.)
¿Qué hace que cada tipo de batería sea único?
Los equipos de fabricación de baterías deben adaptarse a la química y al diseño de los diferentes tipos de baterías. Las variaciones clave incluyen:
-
Baterías de iones de litio (Li-ion):
- Equipo: Máquinas de recubrimiento de precisión para electrodos finos, salas secas (humedad <1% para electrolitos sensibles a la humedad).
- Desafíos: Manipulación de electrolitos inflamables; Estrictos estándares de limpieza.
-
Baterías de iones de sodio (Na-ion):
- Equipo: Similar a los iones de litio pero con menores requisitos de pureza (el sodio es menos reactivo).
- Ventaja: Puede usar papel de aluminio para ánodos (más barato que el cobre para iones de litio).
-
Baterías de estado sólido:
- Equipo: Sistemas de pulverización catódica/deposición al vacío para electrolitos sólidos.
- Diferencia clave: No se necesitan estaciones de llenado de electrolitos líquidos.
¿Por qué varía el equipo?
- Propiedades del material (por ejemplo, los iones de sodio son más grandes que los de litio, lo que requiere diferentes diseños de electrodos).
- Protocolos de seguridad (por ejemplo, los iones de litio necesitan entornos a prueba de explosiones).
¿Cuáles son los requisitos del entorno de trabajo para los equipos de fabricación de baterías?
La producción de baterías exige condiciones estrictamente controladas:
1. Estándares de sala limpia
- Iones de litio: ISO Clase 5-7 (minimiza la contaminación por partículas).
- Humedad: Punto de rocío del <0,5% para procesos sensibles a la humedad.
2. Control de temperatura
- Secado de electrodos: hornos de 120-180 °C con distribución uniforme del calor.
- Salas de formación: Mantener 25±2 °C para una activación electroquímica estable.
3. Medidas de seguridad
- Ventilación: Sistemas de recuperación de NMP (solventes) en áreas de recubrimiento.
- Prevención de incendios: Supresión de gas argón en zonas de llenado de electrolitos.
Configuración paso a paso del espacio de trabajo:
- Designar zonas secas y húmedas (recubrimiento separado del ensamblaje).
- Instalar monitores de humedad con alertas en tiempo real.
- Conexión a tierra de todo el equipo para evitar chispas estáticas.
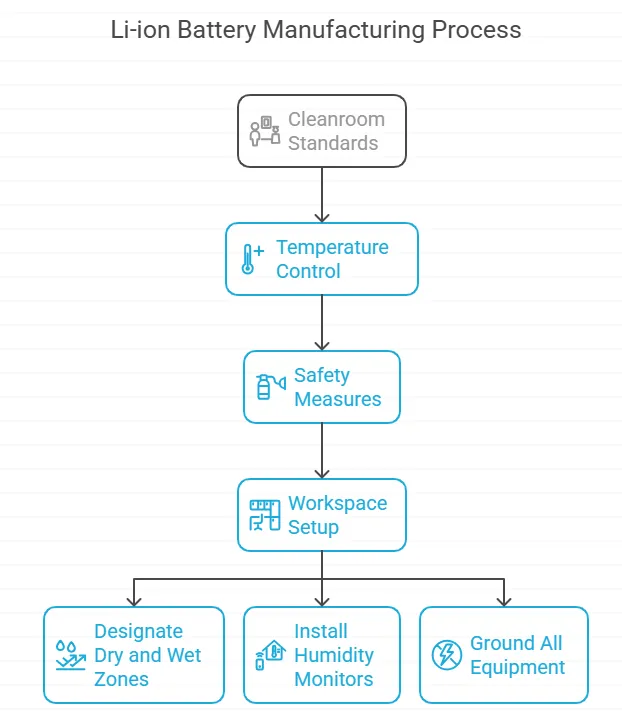
¿Cómo se prueban los equipos de fabricación de baterías? Métodos clave de prueba de productos
1. Pruebas en proceso
- Espesor del recubrimiento: Los micrómetros láser verifican una precisión de ±1 μm.
- Defectos de los electrodos: Los sistemas de visión impulsados por IA detectan agujeros/contaminantes.
2. Validación a nivel de celda
- Pruebas de ciclo: Carga/descarga celdas 500+ veces para simular la vida útil.
- Tomografía computarizada de rayos X: Verifica si hay vacíos internos o desalineaciones.
3. Pruebas de cumplimiento de seguridad
- Penetración de clavos: Garantiza que no haya fugas térmicas en las celdas de iones de litio.
- Protección contra sobrecarga: Confirma la respuesta del sistema de gestión de batería (BMS).
¿Por qué son importantes las pruebas?:
- Detecta el 99,9% de los defectos antes del envío.
- Reduce los retiros del mercado (críticos para las baterías de vehículos eléctricos).
¿Qué medidas de control de calidad se utilizan en los equipos de fabricación de baterías?
1. Inspección óptica automatizada (AOI)
- Compara las dimensiones de los electrodos con los modelos CAD con una tolerancia de <5 μm.
2. Control Estadístico de Procesos (SPC)
- Realiza un seguimiento de métricas como la viscosidad de la suspensión (±se permite una variación del 2 %).
3. Sistemas de trazabilidad
- El láser marca códigos QR en cada celda para registrar los datos de producción (tiempo, ID de la máquina, operador).
Puntos de control de control de calidad críticos:
- Materias primas: Los analizadores XRD confirman la pureza del material catódico.
- Cordones de soldadura: Los probadores ultrasónicos verifican la integridad de las articulaciones.
- Montaje final: Pruebas de estanqueidad para pilas de bolsa (detección de helio).
Ejemplo: Flujo de trabajo de control de calidad de recubrimiento de electrodos
- Muestra cada 100 m de lámina recubierta.
- Medir peso/ancho a través de básculas automatizadas.
- Rechazar lotes si la densidad se desvía >1,5%.
¿Cuáles son las precauciones de uso clave para los equipos de fabricación de baterías?
1. Seguridad del operador
-
Requisitos de EPP:
- Trajes antiestáticos (para salas secas).
- Protectores faciales durante la manipulación de electrolitos.
2. Mantenimiento de la máquina
- Diario: Limpie los rodillos para evitar la acumulación de lodo.
- Mensual: Recalibrar los sensores láser.
3. Riesgos medioambientales
- Exposición a disolventes: El NMP debe capturarse a través de condensadores (límites de OSHA: <10 ppm).
- Riesgos térmicos: Procedimientos de bloqueo/etiquetado para reparaciones de hornos.
Protocolo de apagado paso a paso:
- Líneas de electrolitos de purga con gas inerte.
- Copia de seguridad de los datos de producción a los servidores en la nube.
- Verifique que todos los módulos estén apagados para evitar cortocircuitos.
Los equipos de fabricación de baterías son vitales para producir una amplia gama de baterías, incluidas las baterías de iones de litio, de iones de sodio y de estado sólido. Esta maquinaria especializada automatiza procesos críticos como la preparación de electrodos, el ensamblaje de celdas y las pruebas de calidad, lo que garantiza una alta eficiencia, consistencia y seguridad. Los componentes clave incluyen máquinas de recubrimiento, sistemas de apilamiento/bobinado y unidades de formación/prueba. El equipo funciona según los principios de ingeniería de precisión, optimización electroquímica y automatización, con diferentes tipos de baterías que requieren adaptaciones específicas. Desde vehículos eléctricos hasta productos electrónicos de consumo y almacenamiento en red, estos equipos admiten diversas aplicaciones al tiempo que cumplen con estrictos estándares de calidad y seguridad.