Les machines de fabrication de batteries sont les héros méconnus de l’avancement rapide des technologies de stockage d’énergie. Ces machines hautement spécialisées automatisent et rationalisent la production de batteries, garantissant précision, efficacité et cohérence dans diverses industries. Des véhicules électriques à l’électronique grand public et aux systèmes d’énergie renouvelable, les machines de fabrication de batteries jouent un rôle central pour répondre à la demande croissante de batteries haute performance. Ce blog se penche sur les subtilités de ces machines, en explorant leurs types, leurs composants clés, leurs mécanismes de fonctionnement et leurs applications. De plus, il souligne l’importance de conditions de travail idéales, de mesures de contrôle de la qualité, de précautions de sécurité et d’un entretien de routine pour garantir des performances et une longévité optimales. Que vous soyez un professionnel de l’industrie ou un passionné curieux, ce guide complet vous fournira des informations précieuses sur le monde de la fabrication de batteries.
Qu’est-ce qu’une machine de fabrication de batteries ?
Une machine de fabrication de batteries est un équipement spécialisé conçu pour automatiser et rationaliser la production de batteries. Ces machines sont essentielles à la production de masse de divers types de batteries, notamment les batteries lithium-ion, plomb-acide et nickel-hydrure métallique. Ils gèrent plusieurs étapes du processus de production de batteries, de la préparation des électrodes à l’assemblage final, garantissant une précision, une efficacité et une cohérence élevées. En intégrant des technologies avancées telles que la robotique, l’IA et l’IoT, les machines modernes de fabrication de batteries peuvent réduire considérablement l’erreur humaine, augmenter la vitesse de production et améliorer la qualité globale du produit.
Types de machines de fabrication de batteries
Les machines de fabrication de batteries sont de différents types, chacune adaptée à des étapes spécifiques du processus de production de batteries. Voici quelques types courants :
- Machines de revêtement d’électrodes :Ces machines appliquent des matériaux actifs sur des feuilles métalliques pour créer les électrodes de la batterie (anode et cathode).
- Machines de calandrage :Utilisé pour comprimer et lisser les électrodes enrobées afin d’assurer une épaisseur et une densité uniformes.
- Machines à refendre :Coupez les électrodes revêtues en largeurs précises pour un traitement ultérieur.
- Machines d’empilage/bobinage :Assemblez les électrodes et les séparateurs dans la structure de cellule de batterie souhaitée (par exemple, prismatique, cylindrique ou en poche).
- Machines d’assemblage :Gérez l’assemblage final des cellules de batterie, y compris le boîtier, l’étanchéité et le remplissage d’électrolyte.
- Formation et machines d’essai :Chargez et testez les batteries pour vous assurer qu’elles répondent aux normes de performance et de sécurité.
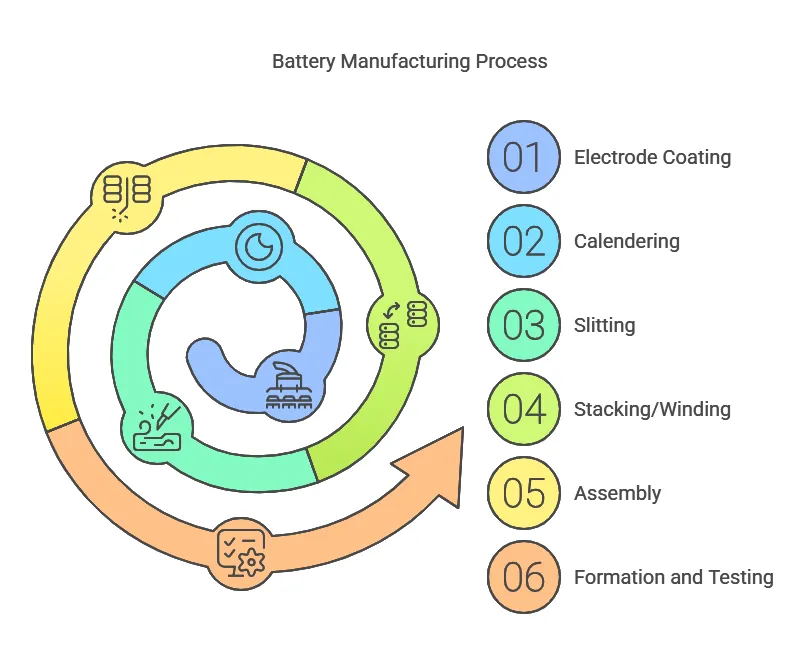
Chaque type de machine joue un rôle essentiel pour assurer l’efficacité et la fiabilité de la chaîne de production de batteries.
Comment fonctionne une machine de fabrication de batteries ?
Les machines de fabrication de batteries fonctionnent grâce à une série de processus automatisés qui transforment les matières premières en batteries entièrement fonctionnelles. Voici une ventilation étape par étape du fonctionnement de ces machines :
1. Préparation de l’électrode :
Des matières premières comme le lithium, le cobalt et le graphite sont mélangées dans une boue.
La boue est recouverte sur des feuilles métalliques à l’aide de machines de revêtement d’électrodes.
Les feuilles revêtues sont séchées et compressées par des machines de calandrage.
2. Découpe à l’électrode :
Les machines à refendre découpent les feuilles revêtues en bandes précises.
3. Assemblage de cellules :
Les machines d’empilage ou d’enroulement superposent les électrodes et les séparateurs pour former la cellule de batterie.
La cellule est ensuite placée dans un boîtier.
4. Remplissage d’électrolytes :
Les machines d’assemblage injectent la solution d’électrolyte dans la cellule.
5. Scellement et finition :
La cellule est scellée et préparée pour le processus de formation.
6. Formation et tests :
Les machines de formation chargent la batterie pour la première fois.
Les machines d’essai évaluent les performances, la capacité et la sécurité de la batterie.
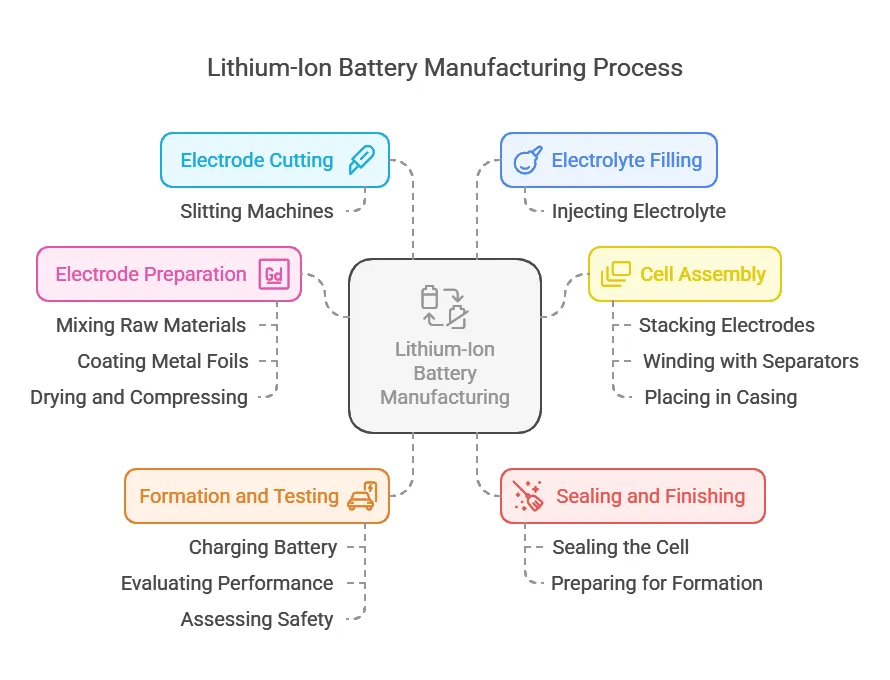
En automatisant ces étapes, les machines de fabrication de batteries garantissent une précision, une cohérence et une évolutivité élevées dans la production.
Composants clés d’une machine de fabrication de batteries
Les machines de fabrication de batteries sont des systèmes complexes composés de plusieurs composants critiques. Ces composants travaillent ensemble pour assurer une production efficace et précise des batteries. Les composants clés sont les suivants :
- Tête de revêtement :Applique la boue d’électrode sur des feuilles métalliques avec une grande précision.
- Étuve:Élimine l’humidité des électrodes enrobées pour assurer une bonne adhérence.
- Rouleaux de calandrage :Comprimez les électrodes pour obtenir l’épaisseur et la densité souhaitées.
- Lames de refendage :Coupez les électrodes en largeurs précises pour un traitement ultérieur.
- Bras robotiques :Manipulez et assemblez les composants de la batterie avec une grande précision.
- Système de remplissage d’électrolyte :Injecte avec précision l’électrolyte dans la cellule de la batterie.
- Chambres de formation :Fournir des environnements contrôlés pour la charge et la décharge initiales des batteries.
- Capteurs de contrôle de la qualité :Surveiller et assurer l’uniformité et la sécurité du produit final.
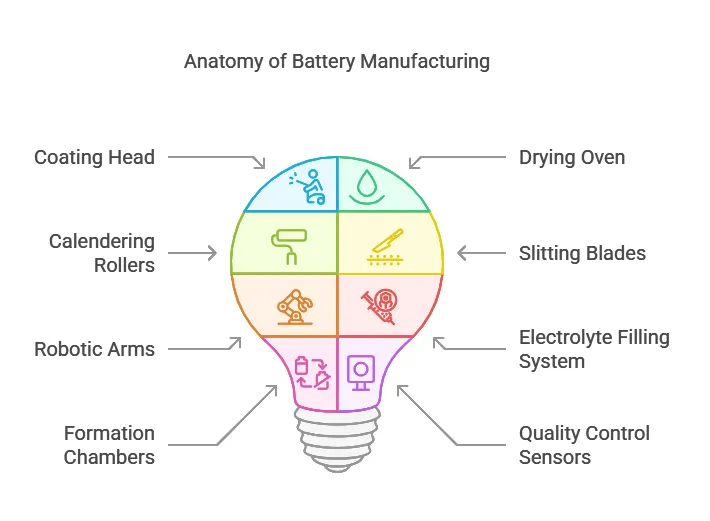
Chaque composant est conçu pour répondre aux exigences strictes de la production de batteries, garantissant des performances et une fiabilité élevées.
Le processus de production d’une batterie comporte plusieurs étapes critiques, chacune nécessitant des machines spécialisées et un contrôle précis. Voici un guide détaillé étape par étape :
1. Préparation des matières premières :
Mélangez des matériaux actifs, des liants et des solvants pour créer des boues d’électrodes.
2. Revêtement de l’électrode :
À l’aide de machines de revêtement, appliquer la boue sur des feuilles métalliques (anode et cathode).
3. Séchage :
Passez les feuilles revêtues dans des fours de séchage pour éliminer les solvants et l’humidité.
4. Calandre :
Comprimez les électrodes séchées à l’aide de machines à calandrer pour obtenir une épaisseur uniforme.
5. Fendage :
Coupez les électrodes en bandes précises à l’aide de machines à refendre.
6. Assemblage de la cellule :
Empilez ou enroulez les électrodes et les séparateurs pour former la cellule de la batterie.
Placez la cellule dans un boîtier.
7. Remplissage d’électrolytes :
Injectez la solution d’électrolyte dans la cellule à l’aide de systèmes de remplissage automatisés.
8. Etanchéité :
Scellez la cellule pour éviter les fuites et assurer la sécurité.
9. Formation :
Chargez et déchargez la batterie pour la première fois pour activer ses propriétés électrochimiques.
10. Tests et contrôle de la qualité :
Testez la capacité, la tension et la sécurité de la batterie.
Triez et emballez les batteries pour la distribution.
En suivant ces étapes, les machines de fabrication de batteries assurent la production de batteries de haute qualité qui répondent aux normes de l’industrie.
Applications des machines de fabrication de batteries dans différentes industries
Les machines de fabrication de batteries sont des outils polyvalents qui jouent un rôle crucial dans diverses industries. Leur capacité à produire des batteries de haute qualité, efficaces et fiables les rend indispensables dans des secteurs tels que :
1. Industrie automobile :
Utilisé pour fabriquer des batteries pour les véhicules électriques (VE), les véhicules hybrides et les systèmes start-stop.
Assure la production de batteries lithium-ion de grande capacité à longue durée de vie.
2. Électronique grand public :
Produit des batteries pour smartphones, ordinateurs portables, tablettes et appareils portables.
Se concentre sur les batteries compactes, légères et à haute densité d’énergie.
3. Stockage de l’énergie renouvelable :
Fabrique des batteries pour les systèmes de stockage d’énergie solaire et éolienne.
Permet un stockage efficace de l’énergie et une stabilisation du réseau.
4. Équipement industriel :
Fournit des batteries pour les chariots élévateurs, les véhicules à guidage automatique (AGV) et d’autres machines industrielles.
Met l’accent sur la durabilité et les hautes performances dans les environnements exigeants.
5. Dispositifs médicaux :
Produit des piles pour les équipements médicaux portables, tels que les pompes à insuline et les appareils auditifs.
Garantit des normes de sécurité élevées et une fiabilité pour les applications critiques.
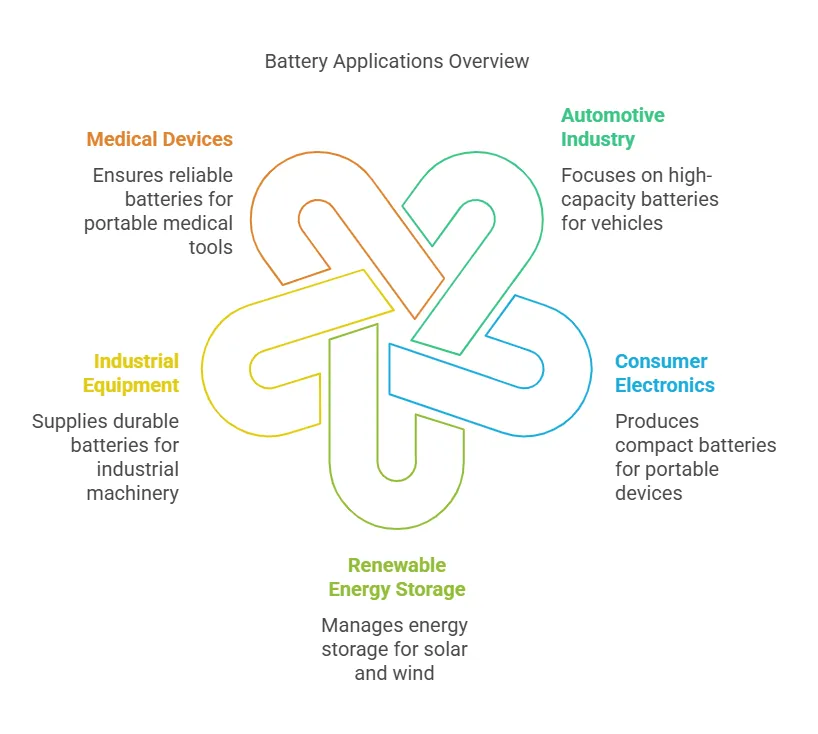
En s’adressant à ces diverses industries, les machines de fabrication de batteries stimulent l’innovation et répondent à la demande croissante de solutions de stockage d’énergie avancées.
Des conditions de travail idéales pour les machines de fabrication de batteries
Pour garantir des performances et une longévité optimales, les machines de fabrication de batteries nécessitent des conditions de travail spécifiques. Ces conditions comprennent :
1. Environnement contrôlé :
La température et l’humidité doivent être régulées pour éviter la dégradation des matériaux et assurer une qualité de production constante.
Plage de température idéale : 20 à 25 °C (68 à 77 °F).
Taux d’humidité idéal : inférieur à 30 %.
2. Installations de la salle blanche :
La poussière et les particules peuvent contaminer les composants de la batterie, entraînant des défauts.
Les salles blanches conformes aux normes ISO 5 à 7 sont recommandées.
3. Alimentation stable :
Les fluctuations de puissance peuvent perturber le fonctionnement des machines et affecter la qualité des produits.
Les systèmes d’alimentation sans coupure (UPS) sont souvent utilisés pour maintenir la stabilité.
4. Une bonne ventilation :
Une ventilation adéquate est nécessaire pour dissiper la chaleur et éliminer les fumées générées pendant la production.
5. Calibrage régulier :
Les machines doivent être calibrées fréquemment pour maintenir la précision et l’exactitude.
En maintenant ces conditions de travail idéales, les fabricants peuvent maximiser l’efficacité et la fiabilité de leurs lignes de production de batteries.
Mesures courantes de contrôle de la qualité dans la fabrication de batteries
Le contrôle de la qualité est un aspect essentiel de la fabrication des batteries, car il permet de s’assurer que les produits finaux répondent aux normes de sécurité, de performance et de fiabilité. Voici quelques mesures courantes :
1. Inspection des matériaux :
Les matières premières sont testées pour leur pureté, leur cohérence et leur conformité aux spécifications.
2. Surveillance en cours de processus :
Des capteurs et des caméras sont utilisés pour surveiller l’épaisseur du revêtement, l’alignement des électrodes et d’autres paramètres pendant la production.
3. Contrôles dimensionnels :
Les électrodes et les séparateurs sont mesurés pour s’assurer qu’ils répondent à des tolérances dimensionnelles précises.
4. Précision de remplissage de l’électrolyte :
Les systèmes automatisés garantissent que la bonne quantité d’électrolyte est injectée dans chaque cellule.
5. Formation et tests :
Les batteries subissent des cycles de charge et de décharge initiaux pour activer leurs propriétés électrochimiques.
Les mesures de performance telles que la capacité, la tension et la résistance interne sont mesurées.
6. Tests de sécurité :
Les batteries sont soumises à des tests de résistance, notamment de surcharge, de court-circuit et de choc thermique, pour garantir la sécurité.
7. Inspection finale :
Des inspections visuelles et automatisées sont effectuées pour identifier les défauts avant l’emballage.
Ces mesures aident les fabricants à fournir des batteries de haute qualité qui répondent aux normes de l’industrie et aux attentes des clients.
Précautions de sécurité lors de l’utilisation d’une machine de fabrication de batteries
L’utilisation de machines de fabrication de batteries implique la manipulation de matières dangereuses et de processus à haute énergie, ce qui fait de la sécurité une priorité absolue. Les principales précautions sont les suivantes :
1. Équipement de protection individuelle (EPI) :
Les opérateurs doivent porter des gants, des lunettes et des vêtements de protection pour éviter l’exposition à des produits chimiques et à des objets pointus.
2. Une formation appropriée :
Les opérateurs doivent recevoir une formation complète sur le fonctionnement de la machine, les procédures d’urgence et l’identification des dangers.
3. Systèmes de ventilation :
Assurez une ventilation adéquate pour éliminer les fumées toxiques et prévenir l’accumulation de gaz inflammables.
4. Mesures de sécurité incendie :
Installer des extincteurs, des détecteurs de fumée et des systèmes de gicleurs dans la zone de production.
Utilisez des matériaux ininflammables dans la mesure du possible.
5. Protection de la machine :
Équipez les machines de dispositifs de sécurité pour éviter tout contact accidentel avec les pièces mobiles.
6. Arrêt d’urgence :
Assurez-vous que toutes les machines sont équipées de boutons d’arrêt d’urgence facilement accessibles.
7. Inspections régulières :
Effectuer des inspections régulières pour identifier et traiter les dangers potentiels pour la sécurité.
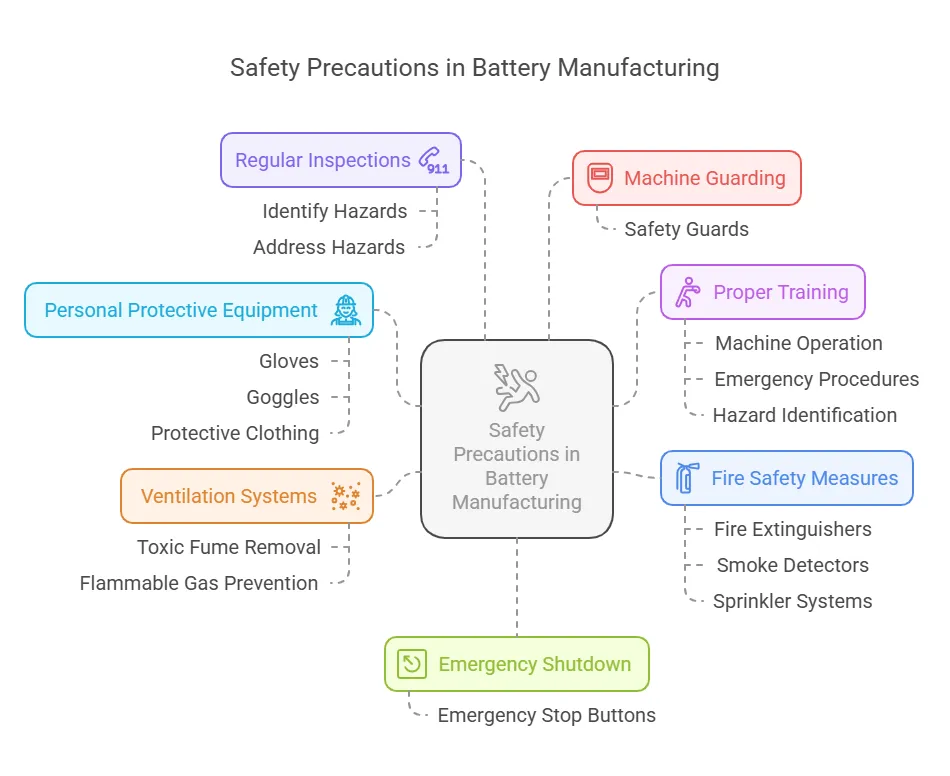
En suivant ces précautions, les fabricants peuvent créer un environnement de travail plus sûr et réduire le risque d’accident.
Maintenance et dépannage de routine pour les machines de fabrication de batteries
Un entretien régulier et un dépannage rapide sont essentiels pour assurer le bon fonctionnement des machines de fabrication de batteries. Voici un guide étape par étape :
Entretien de routine :
1. Contrôles quotidiens :
Inspectez les machines pour détecter les dommages ou l’usure visibles.
Nettoyez les surfaces pour enlever la poussière et les débris.
2. Entretien hebdomadaire :
Lubrifiez les pièces mobiles pour réduire les frottements et prévenir l’usure.
Vérifiez et serrez les boulons et les connexions desserrés.
3. Maintenance mensuelle :
Étalonner les capteurs et les appareils de mesure pour assurer la précision.
Remplacez les composants usés, tels que les lames de refendage ou les têtes de revêtement.
4. Maintenance trimestrielle :
Effectuez une inspection approfondie des systèmes électriques et du câblage.
Testez les caractéristiques de sécurité, y compris les boutons d’arrêt d’urgence et les alarmes.
Dépannage des problèmes courants :
1. Revêtement inégal :
Vérifiez la viscosité de la boue et l’alignement de la tête de revêtement.
Inspectez l’étuve de séchage pour vérifier la constance de la température.
2. Bourrages de machine :
Dégagez toute obstruction dans le chemin d’alimentation du matériau.
Assurez-vous que les lames de refendage sont tranchantes et correctement alignées.
3. Défauts électriques :
Vérifiez que le câblage et les connexions ne sont pas endommagés.
Testez la stabilité de l’alimentation.
4. Qualité de sortie réduite :
Vérifier l’étalonnage des capteurs et des appareils de mesure.
Vérifiez l’usure des composants critiques.
En suivant ces étapes de maintenance et de dépannage, les fabricants peuvent minimiser les temps d’arrêt, prolonger la durée de vie des machines et maintenir une qualité de production constante.
En conclusion, les machines de fabrication de batteries sont des outils indispensables dans la production de batteries de haute qualité qui alimentent notre monde moderne. De la préparation des électrodes à l’assemblage final, ces machines automatisent des processus complexes avec précision et efficacité, garantissant cohérence et évolutivité. Leurs applications s’étendent à des secteurs tels que l’automobile, l’électronique grand public, les énergies renouvelables et les dispositifs médicaux, favorisant l’innovation et répondant à la demande toujours croissante de solutions de stockage d’énergie. Pour maintenir leurs performances, il est crucial de faire fonctionner ces machines dans des conditions idéales, de mettre en œuvre des mesures de contrôle qualité rigoureuses et de respecter des protocoles de sécurité stricts. Une maintenance régulière et un dépannage rapide améliorent encore leur fiabilité et leur durée de vie. Alors que le monde continue de passer à l’énergie durable, les machines de fabrication de batteries resteront à l’avant-garde, permettant la production de batteries avancées qui façonneront l’avenir de la technologie et du stockage d’énergie.