Les équipements de fabrication de batteries sont au cœur de l’innovation énergétique moderne. Ces machines spécialisées sont essentielles pour produire des batteries de haute qualité qui alimentent tout, des véhicules électriques aux systèmes d’énergie renouvelable. Dans ce blog, nous explorerons les composants essentiels et la structure des équipements de fabrication de batteries, leur fonctionnement et leurs principales applications dans divers secteurs. Que vous soyez intéressé par les détails techniques ou par l’impact plus large sur la durabilité, comprendre les équipements de fabrication de batteries est essentiel pour libérer le potentiel des solutions énergétiques de nouvelle génération.
Qu’est-ce qu’un équipement de fabrication de batteries ?
L’équipement de fabrication de batteries fait référence à des machines spécialisées utilisées pour produire divers types de batteries, notamment des batteries lithium-ion, plomb-acide et à l’état solide. Ces systèmes automatisent des processus critiques tels que la préparation des électrodes, l’assemblage des cellules et les tests de qualité pour garantir la précision, l’évolutivité et la sécurité de la production.
Pourquoi est-ce important ?
- Efficacité: Automatise la production à grand volume avec un minimum d’intervention humaine.
- Consistance: Assure une qualité de batterie uniforme pour la performance et la sécurité.
- Innovation: Permet de concevoir des batteries de nouvelle génération (par exemple, une densité d’énergie plus élevée).
Principales industries qui s’appuient sur cet équipement:
- Véhicules électriques (VE)
- Électronique grand public
- Stockage d’énergie renouvelable
Quels sont les composants et la structure des équipements de fabrication de batteries ?
Les lignes de production de batteries modernes intègrent plusieurs sous-systèmes :
-
Unités de fabrication d’électrodes
- Machines d’enduction: Appliquer des matériaux actifs sur des feuilles métalliques.
- Calandres: Comprimer les électrodes à des épaisseurs précises.
-
Modules d’assemblage de cellules
- Machines d’empilage/bobinage: Anodes de couches, séparateurs et cathodes.
- Systèmes de soudage: Sécurisez les languettes et les boîtiers.
-
Systèmes de formation et d’essai
- Unités de charge/décharge: Activer les cellules et mesurer la capacité.
- Inspecteurs par rayons X: Détecter les défauts internes.
Composants auxiliaires critiques:
- Chambres sèches (contrôle de l’humidité)
- Découpeuses laser
- Stations de remplissage d’électrolytes
Comment fonctionne l’équipement de fabrication de batteries ? Un flux étape par étape
Étape 1 : Préparation de l’électrode
- Mélange: Les matières actives, les liants et les solvants sont mélangés dans les boues.
- Revêtement: Les boues sont appliquées uniformément sur des feuilles de cuivre/aluminium.
- Séchage: Les feuilles revêtues passent dans les fours pour évaporer les solvants.
Étape 2 : Assemblage de la cellule
- Refendage: Les électrodes séchées sont coupées en bandes.
- Empilage/Enroulement: Les anodes, les séparateurs et les cathodes sont superposés.
- Emboîtage: Les cellules sont scellées dans des sachets ou des enveloppes métalliques.
Étape 3 : Finition
- Injection d’électrolytes(pour les batteries liquides).
- Cyclisme en formationpour stabiliser les performances.
- Classementbasé sur les mesures de capacité/tension.
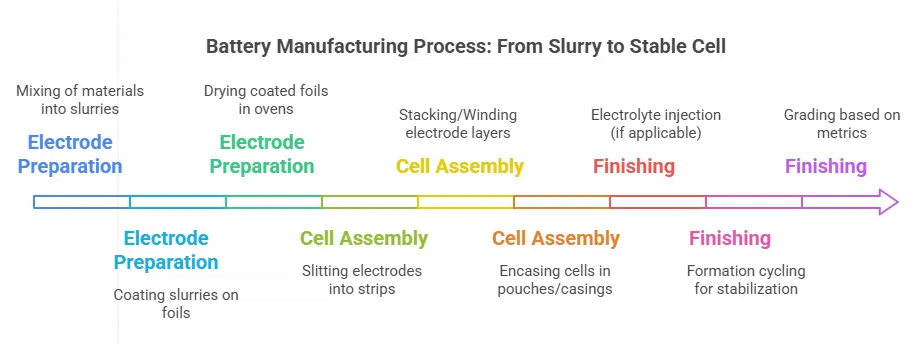
Quels sont les principes de fonctionnement des équipements de fabrication de batteries ?
L’équipement de batterie fonctionne selon trois principes fondamentaux :
1. Ingénierie de précision
- Les capteurs laser et les commandes pilotées par l’IA maintiennent une précision au micron près dans le revêtement et la découpe.
2. Optimisation électrochimique
- Les environnements contrôlés (p. ex., point de rosée < -40 °C) empêchent la dégradation induite par l’humidité.
3. Automatisation et intégration des données
- Les PLC (Programmable Logic Controllers) synchronisent les bandes transporteuses, les robots et les systèmes d’inspection.
- Les capteurs IoT collectent des données en temps réel pour la maintenance prédictive.
Exemple : Fonctionnement de la bobineuse
- Étape 1: Alimentation des couches d’anode/séparateur/cathode à partir de rouleaux.
- Étape 2: Les enroule en un « jellyroll » via le contrôle de la tension.
- Étape 3: Soudures par ultrasons, languettes terminales.
Quelles sont les principales applications des équipements de fabrication de batteries ?
1. Véhicules électriques (VE)
- Produit des cellules prismatiques/de poche de grande capacité pour une plus longue portée.
- L’équipement doit répondre à des normes de durabilité de niveau automobile (par exemple, ISO 16949).
2. Électronique grand public
- Les machines miniaturisées fabriquent des cellules Li-ion compactes pour smartphones/ordinateurs portables.
3. Stockage en réseau
- Les systèmes à usage intensif construisent des batteries de grand format pour les parcs solaires/éoliens.
Applications émergentes:
- Batteries à l’état solide: Nécessite un équipement de dépôt sous vide.
- Recyclage: Machines de démontage/réaffectation des batteries usagées.
Comment l’équipement de fabrication de batteries diffère selon les types de batteries (Li-ion, sodium-ion, etc.)
Qu’est-ce qui rend chaque type de batterie unique ?
L’équipement de fabrication de batteries doit s’adapter à la chimie et à la conception des différents types de batteries. Les principales variantes sont les suivantes :
-
Lithium-ion (Li-ion) Batteries:
- Équipement: Machines de revêtement de précision pour électrodes minces, salles sèches (humidité <1 % pour les électrolytes sensibles à l’humidité).
- Défis: Manipulation d’électrolytes inflammables ; normes de propreté strictes.
-
Sodium-ion (Na-ion) Batteries:
- Équipement: Similaire au Li-ion mais avec des exigences de pureté plus faibles (le sodium est moins réactif).
- Avantage: Peut utiliser une feuille d’aluminium pour les anodes (moins cher que le cuivre pour le Li-ion).
-
Batteries à l’état solide:
- Équipement: Systèmes de pulvérisation cathodique/dépôt sous vide pour électrolytes solides.
- Différence clé: Aucune station de remplissage d’électrolyte liquide n’est nécessaire.
Pourquoi l’équipement varie-t-il ?
- Propriétés des matériaux (par exemple, les ions sodium sont plus gros que le lithium, ce qui nécessite des conceptions d’électrodes différentes).
- Protocoles de sécurité (par exemple, le Li-ion a besoin d’environnements antidéflagrants).
Quelles sont les exigences en matière d’environnement de travail pour les équipements de fabrication de batteries ?
La production de batteries exige des conditions étroitement contrôlées :
1. Normes pour les salles blanches
- Li-ion: Classe ISO 5-7 (minimise la contamination par les particules).
- Humidité: <0,5 % du point de rosée pour les processus sensibles à l’humidité.
2. Contrôle de la température
- Séchage des électrodes : fours à 120–180 °C avec répartition uniforme de la chaleur.
- Salles de formation : Maintenir 25±2°C pour une activation électrochimique stable.
3. Mesures de sécurité
- Ventilation: Systèmes de récupération de solvants (NMP) dans les zones de revêtement.
- Prévention des incendies: Suppression du gaz argon dans les zones de remplissage d’électrolyte.
Configuration étape par étape de l’espace de travail:
- Désignez les zones sèches et humides(revêtement séparé de l’assemblage).
- Installer des moniteurs d’humiditéavec des alertes en temps réel.
- Mise à la terre de tout l’équipementpour éviter les étincelles statiques.
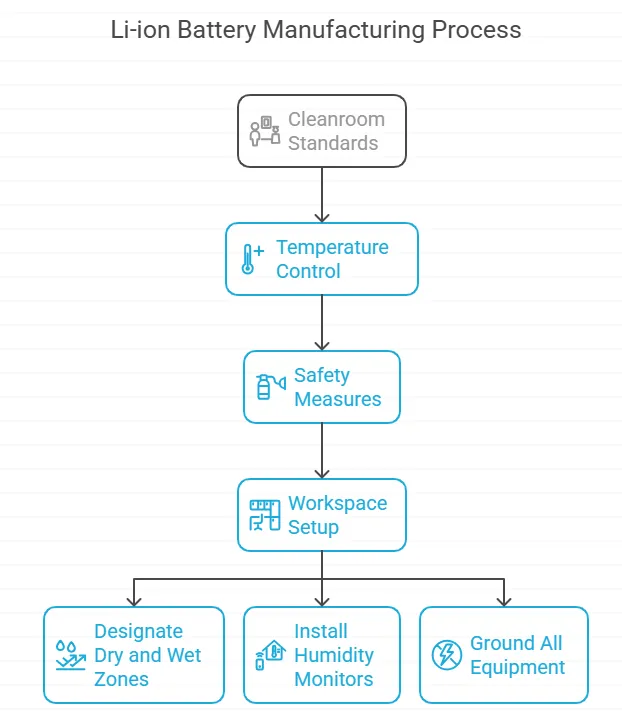
Comment l’équipement de fabrication de batteries est-il testé ? Principales méthodes d’essai des produits
1. Essais en cours de processus
- Épaisseur du revêtement: Les micromètres laser vérifient la précision de ±1μm.
- Défauts d’électrodes: Les systèmes de vision alimentés par l’IA détectent les trous d’épingle/contaminants.
2. Validation au niveau de la cellule
- Essais de cycles: Charge/décharge les cellules 500+ fois pour simuler la durée de vie.
- TDM à rayons X: Vérifie les vides internes ou les désalignements.
3. Tests de conformité à la sécurité
- Pénétration du clou: Garantit l’absence d’emballement thermique dans les cellules Li-ion.
- Protection contre les surcharges: Confirme la réponse du système de gestion de batterie (BMS).
Pourquoi les tests sont importants:
- Détecte 99,9 % des défauts avant l’expédition.
- Réduit les rappels (critiques pour les batteries de VE).
Quelles sont les mesures de contrôle de la qualité utilisées dans les équipements de fabrication de batteries ?
1. Inspection optique automatisée (AOI)
- Compare les dimensions de l’électrode aux modèles CAO avec une tolérance de <5 μm.
2. Contrôle statistique des processus (SPC)
- Suit des mesures telles que la viscosité de la boue (±2 % de variation autorisée).
3. Systèmes de traçabilité
- Le laser marque des codes QR sur chaque cellule pour enregistrer les données de production (temps, ID de la machine, opérateur).
Points de contrôle critiques du contrôle qualité:
- Matières: Les analyseurs XRD confirment la pureté du matériau de la cathode.
- Cordons de soudure: Les testeurs à ultrasons vérifient l’intégrité des articulations.
- Assemblage final: Tests d’étanchéité pour les cellules de poche (détection d’hélium).
Exemple : Flux de travail de contrôle qualité du revêtement d’électrode
- Prélèvement tous les 100mde feuille enduite.
- Mesure poids/largeurvia des balances automatisées.
- Rejeter des lotssi la densité s’écarte de >1,5 %.
Quelles sont les principales précautions d’utilisation des équipements de fabrication de batteries ?
1. Sécurité de l’opérateur
-
Exigences en matière d’EPI:
- Combinaisons antistatiques (pour les pièces sèches).
- Écrans faciaux lors de la manipulation des électrolytes.
2. Maintenance de la machine
- Quotidien: Nettoyez les rouleaux pour éviter l’accumulation de boue.
- Mensuel: Recalibrer les capteurs laser.
3. Risques environnementaux
- Exposition aux solvants: Le NMP doit être capté via des condenseurs (limites OSHA : <10 ppm).
- Risques thermiques: Procédures de cadenassage/étiquetage pour les réparations du four.
Protocole d’arrêt étape par étape:
- Purger les lignes d’électrolyteavec gaz inerte.
- Sauvegarde des données de productionvers les serveurs cloud.
- Vérifiez que tous les modules sont hors tension.pour éviter les courts-circuits.
L’équipement de fabrication de batteries est essentiel pour produire une large gamme de batteries, notamment des batteries lithium-ion, sodium-ion et à l’état solide. Cette machinerie spécialisée automatise les processus critiques tels que la préparation des électrodes, l’assemblage des cellules et les tests de qualité, garantissant une efficacité, une cohérence et une sécurité élevées. Les composants clés comprennent des machines de revêtement, des systèmes d’empilage/d’enroulement et des unités de formation/test. L’équipement fonctionne selon les principes de l’ingénierie de précision, de l’optimisation électrochimique et de l’automatisation, avec différents types de batteries nécessitant des adaptations spécifiques. Des véhicules électriques à l’électronique grand public et au stockage sur le réseau, cet équipement prend en charge diverses applications tout en répondant à des normes de qualité et de sécurité strictes.