過去10年間で、リチウムイオン電池業界は半自動からスタンドアロンの自動化に移行し、その後徐々に完全な自動化とインテリジェンスに移行しました。このプロセスを通じて、バッテリー製造プロセスの大きな変更は最小限に抑えられています。ただし、バッテリー需要が年間100%を超える継続的かつ急速な成長と、バッテリー材料システムの継続的なアップグレードにより、製造規模とバッテリーシステムの変化に対応するために、バッテリー製造プロセスのアップグレードは必然的に必要になります。これに対応して、リチウムイオン電池業界の「母鶏」であるバッテリー機器も、ブレークスルーの新たな機会に直面しています。
製造技術・設備開発動向
将来的には、エネルギー貯蔵電池の開発傾向は、個々のスモールセルからより大きな容量へとシフトします。リチウムイオン機器は、これらの大型セルの製造精度、高い製造効率を確保し、互換性とスケーラビリティを向上させる必要があります。そのためには、部品の加工精度とモジュールの組立精度も向上させる必要があります。
リチウムイオン電池の大規模製造における課題解決のためには、装置の高効率化が求められています。リチウムイオン装置の生産効率は、主に2つの側面から向上します。まず、より高速で安定した構造と制御方法を使用して、機器の製造速度を上げることによって。次に、補助時間と呼ばれる機器の動きに消費される時間を減らすことです。
一例として、Geesun Intelligentによって開発されたセパレーター用の連続巻線機は典型的な装置です。以前は、各セルは加速して最高巻線速度まで供給され、その後減速し、停止し、セパレーターを切断し、針を通し、次のセル巻線に移っていました。改良後、セパレーターは減速せず、フライング切断機構を使用してセパレーターを切断しますが、これは電極の減速プロセス中に事前に行われます。これにより、電極とセパレーターの切断プロセスに要する時間が短縮され、補助時間がほぼゼロに効果的に最小限に抑えられ、全体的な生産サイクルタイムが30〜60%改善されます(電極の長さによって異なります)。別の例は、レーザー切断速度を以前の80〜120m / minから200m / minに増加させた電極タブ切断機です。
この観点から、リチウムイオン製造装置の進歩と反復は、大規模、高精度、高信頼性、および完全に統合されたインテリジェントソリューションに向かっています。
リチウムイオン製造プロセスの最適化の観点から、統合された完全にインテリジェントな機器は、より高い生産安定性、自動化の増加、および製造プロセスへの適応性の向上を提供します。また、製造会社が人件費とスペースコストを削減し、プロセスリンケージを短縮し、材料の無駄を最小限に抑えるのに役立ち、全体的な効率を向上させる上で重要な役割を果たします。
材料技術と製造技術の深い融合
バッテリー製造プロセス全体を通じて、ナノスケールの材料処理操作からメートルスケールのデバイスの製造と処理への移行が含まれます。これまで、リチウムイオン製造は、主にニュートン力学に基づいて機器の製造効率、品質、およびコストを制御することに重点を置いていました。制御された主なパラメータは、材料の物理的位置、速度、加速度、慣性、摩擦、および抵抗でした。これらの制御は比較的巨視的であり、プロセスの可視性と可観測性は比較的管理が容易でした。
電池は内部電場の影響下でイオンが移動し、外部的には電子の移動に反映されるという事実に基づいて、量子力学を用いて微視的な観点から電池の製造と使用を制御する必要があります。これには、製造および組み立て中の電池の構造と組成の進化、電子とイオンの輸送挙動、界面の問題、および性能スケールが電池に与える影響を考慮する必要があります。充放電プロセス中の界面の変化、性能とスケールの変動、内部分子とイオン間の結合効果、温度の影響、形状と体積の変化を考慮に入れると、バッテリーの安全性、自己放電、サイクル寿命、エネルギー密度、および電力密度を制御する必要があります。
そのためには、熱力学、動力学(イオン輸送速度論、電荷移動速度論、反応速度論、相転移速度論など)、および製造プロセスの安定性を微視的な観点からより深く考慮する必要があります。
しかし、これらの複雑なプロセスの制御には、現在、製造分野での完全な理論モデルが不足しています。これは、マルチフィジックスフィールドカップリング、マルチエレメントおよびヘテロジニアスデータ、マルチスケール形状制御、固有特性の制御、および大量データの管理に固有の課題によるものです。採用できる方法には、定性的トレンド分析とビッグデータモデリングに基づく機械学習と最適化モデリングが含まれます。量子力学理論を使用してバッテリー内の本質的な科学原理を理解することにより、プロセスの最適化、意思決定、および制御を実現できます。分析方法と評価手法を確立して、リコンフィギャラブルで大規模でカスタマイズされたバッテリー製造を実現できます。最終的に、このアプローチは、イオン移動、発熱と移動、内圧制御、プロセス変形、SEI膜形成、リチウムデンドライト制御などの問題に対処できます。
製造の統合と製造原理の変更
前回の議論では、量子の観点からバッテリー製造で考慮すべき微視的な側面に焦点を当てました。リチウムイオン電池における結合電気化学反応の文脈では、複数の物理場が関与するため、無次元数、粒子密度、格子欠陥密度、粒子速度などの一般化された状態変数を使用して、電池の電気化学プロセスの定量化を達成できます。
多方向の平滑粒子動力学数値シミュレーション技術を用いることで、電極のメソスケールの微細構造を考慮した数値モデルを開発することができます。これらのモデルは、放電プロセス中のバッテリー内のイオン濃度フィールド、固液電位フィールド、変換電流密度、およびその他の微視的な詳細をシミュレートできます。さらに、電池の充放電過程の基本的な物理化学的メカニズムや、出力電圧や電極を構成する固体活物質の粒子径など、電池の巨視的な性能との相関関係を解析し、明らかにすることができます。
乾式電極製造は、メソスケール粒子力学の原理に導かれ、電極製造、混合、攪拌、コーティング、乾燥、圧延などのプロセスの統合を伴います。レーザー切断と巻き取り、およびレーザー切断とスタッキングを1つの装置に統合することは重要なトレンドです。将来的には、電池セルの生産に必要な設備は、電極製造装置、組立装置、試験装置の3種類で済むようになると想定しています。ただし、これは理想的なシナリオであり、材料、プロセス、および機器の共同作業と進歩が必要です。それは一夜にして達成できるものではなく、バッテリー製造の専門家の献身的な努力と勤勉さが必要になります。
乾式電極(「ドライコーティング」とも呼ばれます)を調製する主なプロセスには、非繊維化バインダーの選択、造粒用のボールミリング非繊維化バインダー、およびカレンダー作成前の非繊維化バインダー、繊維化バインダー、および電極活物質(カソード/アノード)の混合が含まれます。材料の可塑性を確保するために、成形プロセス中に混合物を100°Cを超える温度に加熱することがよくあります。
マクスウェルが使用する非繊維化バインダーには、ポリフッ化ビニリデンとカルボキシメチルセルロースが含まれますが、主に使用される繊維化バインダーはポリテトラフルオロエチレンです。並列処理は、製造プロセスで一般的に採用されています。テスラの乾式電極製造プロセスの図については、下の図を参照してください。
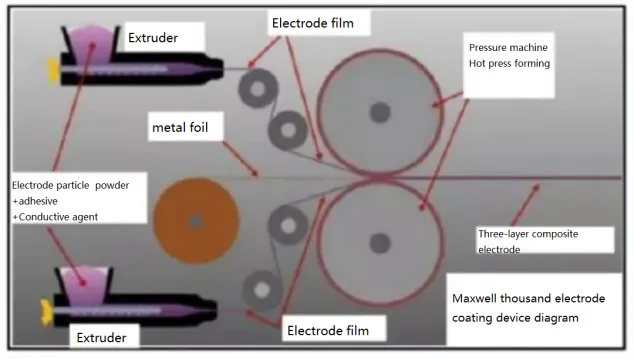
従来の湿式電極プロセスと比較して、テスラ(マクスウェル)が使用している乾式電極プロセスにはいくつかの利点があります。攪拌をボールミリングに、コーティングをカレンダーに置き換え、ウェットコーティング後の乾燥プロセスを排除します。この方法により、溶剤を節約し、処理時間を短縮し、溶剤の残留物を回避し、機器の複雑さを軽減することができます。しかし、ドライプロセスには限界があり、特に活物質の均一な分散を実現するには限界があり、これはスーパーキャパシタの電極材料と比較してリチウムイオン電池の電極にとって特に困難です。
テスラの乾式電極プロセスはさらに簡単で、溶剤を使用する必要はありません。このプロセスは、少量(約5〜8%)の微細なポリテトラフルオロエチレン(PTFE)バインダーがカソードパウダーと混合される電極粉末から始まります。次に、カソード粉末とバインダーの混合物を押し出して、薄い電極材料ストリップを形成します。この押し出された電極材料ストリップは、金属箔集電体にラミネートされて、最終的な電極を生成します。ドライプロセスは、電極製造の効率を向上させ、処理ステップを短縮し、エネルギー貯蔵バッテリーの大規模生産の新たな可能性を開きます。
簡素化された製造プロセスとバッテリー構造
リチウム電池製造の各プロセスで使用される機器は、電池の性能に大きく影響します。バッテリーのプロセスフローの長さも、セル調製の一貫性と制御性に影響を与えます。電極製造とセル形成プロセスの簡素化は成功例です。統合カレンダーおよびスリッター、レーザー切断および巻線機、レーザー切断およびスタッキングマシンなどの機器の開発により、プロセスが合理化され、閉ループ制御の能力が向上しました。この簡素化により、複雑なルートによる材料輸送のコストが削減されるだけでなく、労力も節約されます。
バッテリー業界の将来の発展では、バッテリーの性能と製造構造の最適化に革命的な変化が起こるでしょう。これには、性能、製造、および接続要件に基づくバッテリーケーシングの形状、サイズ、および電極接続の変更が含まれます。内部の集電体と電極接続も、バッテリーのリサイクル要件を満たすために変更される場合があります。
CATLとBYDはどちらも、プロセスを合理化するために異なるアプローチを採用しています。これらは、プロセスフローを短縮するために、さまざまな形式のCTP(Cell to Pack)を利用しています。CTPとは、モジュールステージをスキップし、バッテリーセルをパックに直接統合して、ボリューム使用率を高めることを指します。CATLのCTPバッテリーパックには、複数のバッテリーモジュールがあり、それぞれに複数のセルとこれらのセルを収容するためのフレームが含まれています。彼らは小さなモジュールを大きなモジュールに置き換えました。BYDのCTPは、GCTP(Blade Battery)とも呼ばれ、ブレードバッテリーパックが1つの大きなモジュールのみを使用するという、さらに高いレベルのモジュール排除を実現します。CATL-CTP プロセスと BYD-CTP プロセスの比較については、次の表を参照してください。
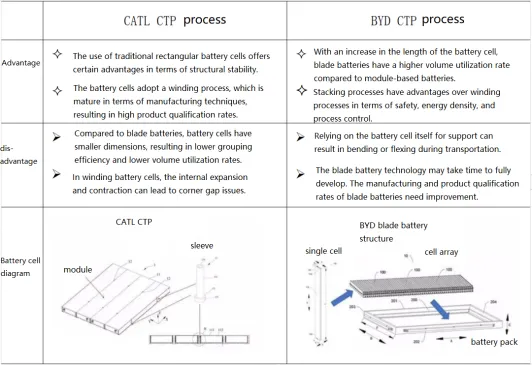
新エネルギー用途の分野におけるリチウムイオン電池の需要は拡大し続けています。主要なリチウムイオン電池企業は、継続的な容量拡大を通じて規模の経済とコスト削減を達成することを目指しています。彼らは、生産ラインのプロセス、パフォーマンス、および生産効率に対するより高い要件を持っています。リチウムイオン機器は、リチウムイオン製造におけるプロセス効率、歩留まり、および生産効率を向上させる上で重要な役割を果たします。イノベーション能力は、バッテリー製造プロセスのコアコンピテンシーです。リチウムイオン機器の継続的な改善と反復、およびリチウムイオン製造技術のさらなるブレークスルーには、緊密な協力が必要です。