In the realm of modern technology, the 18650 battery has emerged as a cornerstone of innovation. From laptops and electric vehicles to power tools and renewable energy storage, these cylindrical lithium-ion batteries are ubiquitous. But what goes into the manufacturing of these powerful energy cells? In this blog, we delve into the intricate process of 18650 battery production, exploring the principles, challenges, and future trends that shape this vital industry. Whether you’re an industry professional or simply curious about the technology behind everyday devices, join us on this journey to uncover the secrets of 18650 battery manufacturing.
What is 18650 Battery Manufacturing?
18650 battery manufacturing refers to the process of producing cylindrical lithium-ion batteries that are 18mm in diameter and 65mm in length. These batteries are widely used due to their high energy density, reliability, and versatility. The manufacturing process involves several critical stages, including electrode preparation, cell assembly, and quality testing. The name “18650” is derived from the battery’s dimensions, making it a standard size in the industry. These batteries are commonly used in laptops, electric vehicles, power tools, and other high-demand applications. The manufacturing process ensures that each battery meets strict safety and performance standards, making them a preferred choice for various industries.
How Does the 18650 Battery Production Process Work?
The production of 18650 batteries involves a detailed and precise workflow to ensure high quality and performance. Here’s a step-by-step breakdown of the process:
-
Electrode Preparation:
- The anode (typically made of graphite) and cathode (often lithium cobalt oxide or other lithium-based compounds) are coated onto metal foils.
- The coated foils are then dried and rolled to achieve the desired thickness.
-
Cell Assembly:
- The anode, cathode, and separator (a thin porous film) are layered together and wound into a cylindrical shape.
- The wound cell is inserted into a metal casing, and electrolytes are injected to facilitate ion movement.
-
Sealing and Formation:
- The cell is sealed to prevent leakage and ensure safety.
- The battery undergoes an initial charge-discharge cycle to stabilize its performance.
-
Testing and Quality Control:
- Each battery is rigorously tested for capacity, voltage, and safety parameters.
- Batteries that pass the tests are labeled and packaged for distribution.
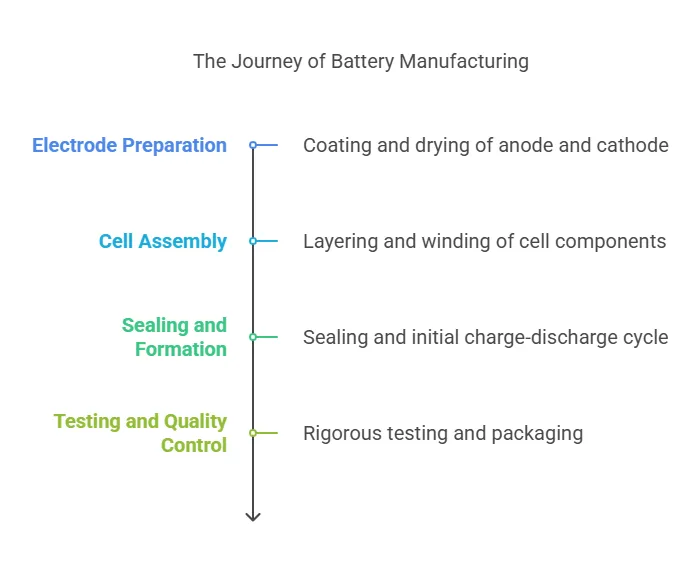
This meticulous process ensures that 18650 batteries deliver consistent performance and meet industry standards.
Why is the Principle of 18650 Battery Manufacturing Important?
The principle of 18650 battery manufacturing revolves around creating a safe, efficient, and high-performance energy storage solution. The design and production process are based on the electrochemical properties of lithium-ion technology, which allows for high energy density and long cycle life. Key principles include:
- Precision Engineering: Ensuring uniform electrode coating and precise cell assembly to avoid defects.
- Safety Measures: Incorporating safety features like pressure relief vents and thermal stability to prevent overheating or explosions.
- Efficiency Optimization: Maximizing energy output while minimizing internal resistance to enhance performance.
Understanding these principles is crucial for manufacturers to produce batteries that meet the demands of modern applications while adhering to safety and environmental regulations.
What Are the Applications of 18650 Batteries in Various Industries?
18650 batteries are highly versatile and are used across a wide range of industries due to their reliability and high energy density. Some key applications include:
- Consumer Electronics: Powering laptops, flashlights, and portable devices.
- Electric Vehicles (EVs): Serving as the building blocks for EV battery packs due to their high capacity and durability.
- Power Tools: Providing the necessary energy for cordless drills, saws, and other tools.
- Renewable Energy Storage: Storing energy in solar and wind power systems for later use.
- Medical Devices: Ensuring reliable power for critical equipment like portable monitors and diagnostic tools.
The adaptability of 18650 batteries makes them a cornerstone of modern technology, enabling innovation across multiple sectors.
How Does 18650 Battery Manufacturing Impact Battery Performance?
The manufacturing process of 18650 batteries directly influences their performance, safety, and longevity. Here’s how:
- Electrode Quality: Uniform coating and precise thickness ensure consistent energy output and reduce internal resistance.
- Cell Assembly: Proper winding and sealing prevent short circuits and enhance durability.
- Electrolyte Composition: High-quality electrolytes improve ion conductivity and thermal stability.
- Testing Protocols: Rigorous testing ensures that only batteries meeting performance standards reach the market.
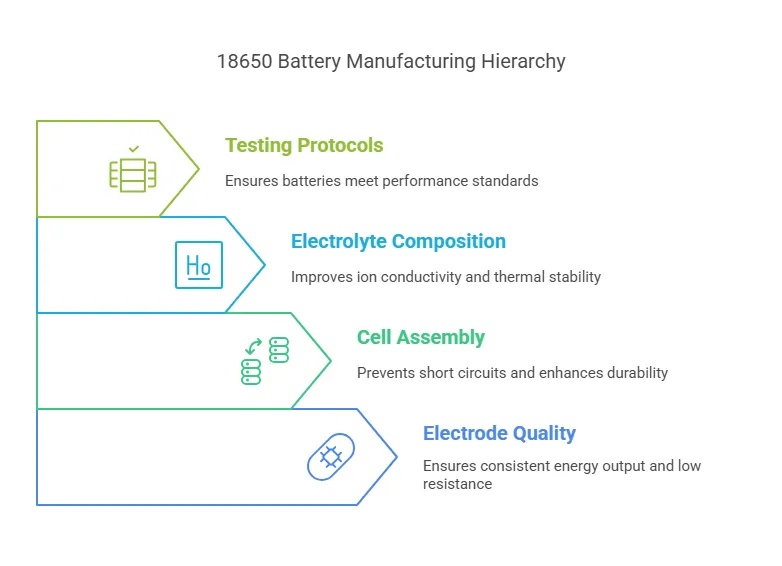
By optimizing each stage of manufacturing, producers can create batteries that deliver superior performance, longer life cycles, and enhanced safety, meeting the needs of demanding applications.
These topics provide a comprehensive overview of 18650 battery manufacturing, addressing key aspects that appeal to both industry professionals and curious readers.
What Testing Methods Are Used in 18650 Battery Manufacturing?
Testing is a critical part of 18650 battery manufacturing to ensure safety, reliability, and performance. Here are some key testing methods employed:
-
Capacity Testing:
- Measures the energy storage capacity of the battery.
- Ensures the battery meets specified performance standards.
-
Voltage Testing:
- Checks the open-circuit voltage and operating voltage range.
- Identifies any inconsistencies in voltage output.
-
Cycle Life Testing:
- Simulates repeated charge-discharge cycles to evaluate longevity.
- Helps determine the battery’s lifespan under real-world conditions.
-
Safety Testing:
- Includes overcharge, short-circuit, and thermal stability tests.
- Ensures the battery can withstand extreme conditions without failure.
-
Impedance Testing:
- Measures internal resistance to assess efficiency and heat generation.
- High impedance can indicate potential performance issues.
These tests are conducted at various stages of production to ensure only high-quality batteries reach the market.
Why is Quality Control Crucial in 18650 Battery Production?
Quality control (QC) is essential in 18650 battery production to maintain consistency, safety, and performance. Here’s how QC is implemented:
-
Raw Material Inspection:
- Ensures materials like lithium, cobalt, and graphite meet purity standards.
- Prevents defects caused by subpar materials.
-
In-Process Monitoring:
- Tracks electrode coating, cell assembly, and electrolyte filling.
- Identifies and corrects deviations in real-time.
-
Final Product Testing:
- Conducts comprehensive tests on finished batteries.
- Verifies capacity, voltage, and safety parameters.
-
Documentation and Traceability:
- Maintains detailed records of each production batch.
- Enables quick identification and resolution of issues.
By implementing rigorous QC measures, manufacturers can deliver reliable and safe 18650 batteries to their customers.
What Are the Common Challenges in 18650 Battery Manufacturing?
Manufacturing 18650 batteries involves overcoming several challenges to ensure quality and efficiency. Some common issues include:
-
Electrode Coating Uniformity:
- Inconsistent coating can lead to performance issues.
- Requires precise machinery and regular calibration.
-
Electrolyte Filling:
- Over- or under-filling can affect battery performance.
- Automated systems are used to ensure accuracy.
-
Thermal Management:
- High temperatures during production can damage components.
- Controlled environments and cooling systems are essential.
-
Safety Risks:
- Lithium-ion batteries are prone to thermal runaway if not handled properly.
- Strict safety protocols and equipment are necessary.
-
Cost Management:
- High-quality materials and advanced machinery increase production costs.
- Balancing cost and quality is a constant challenge.
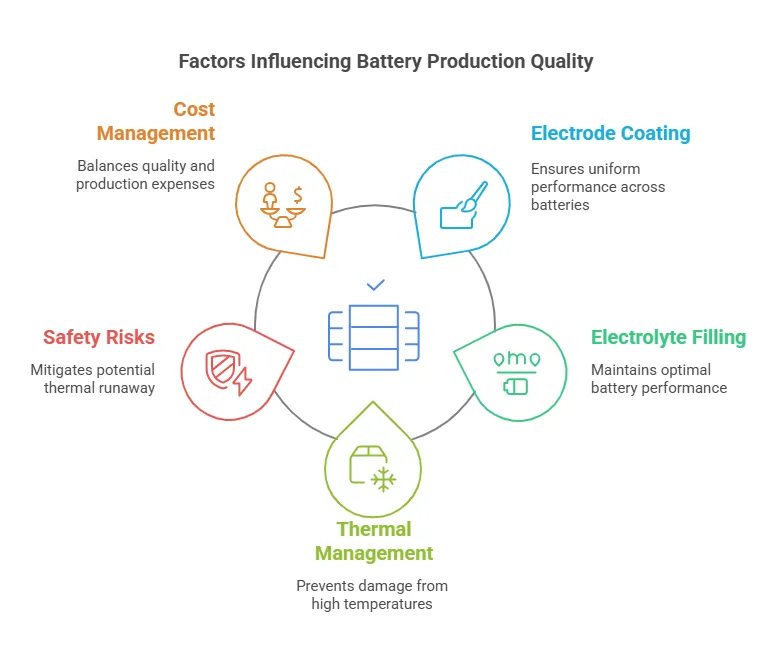
Addressing these challenges requires expertise, advanced technology, and continuous improvement in manufacturing processes.
How Do Environment and Safety Considerations Impact 18650 Battery Factories?
Environment and safety are top priorities in 18650 battery factories due to the hazardous nature of lithium-ion technology. Key considerations include:
-
Air Quality Control:
- Prevents contamination of electrodes and electrolytes.
- Cleanrooms with HEPA filters are commonly used.
-
Waste Management:
- Proper disposal of chemical waste and defective batteries.
- Recycling programs for used batteries to reduce environmental impact.
-
Fire Safety Measures:
- Installation of fire suppression systems and thermal sensors.
- Regular safety drills and training for workers.
-
Worker Protection:
- Use of protective gear to prevent exposure to harmful chemicals.
- Ensuring proper ventilation in production areas.
-
Energy Efficiency:
- Implementing energy-saving technologies to reduce carbon footprint.
- Using renewable energy sources where possible.
These measures not only protect workers and the environment but also enhance the overall efficiency and reputation of the manufacturing facility.
What Are the Best Practices for Maintaining 18650 Batteries During Production?
Maintaining 18650 batteries during production is crucial to ensure their quality and longevity. Here are some best practices:
-
Proper Storage:
- Store batteries in a cool, dry place to prevent degradation.
- Avoid exposure to high temperatures or humidity.
-
Handling Precautions:
- Use anti-static equipment to prevent damage from electrostatic discharge.
- Avoid dropping or mechanically stressing the batteries.
-
Regular Inspections:
- Check for physical defects like dents or leaks.
- Monitor voltage and impedance levels during storage.
-
Controlled Charging:
- Use specialized chargers to avoid overcharging or undercharging.
- Follow manufacturer guidelines for charging parameters.
-
Clean Production Environment:
- Maintain a dust-free and temperature-controlled workspace.
- Prevent contamination of battery components.
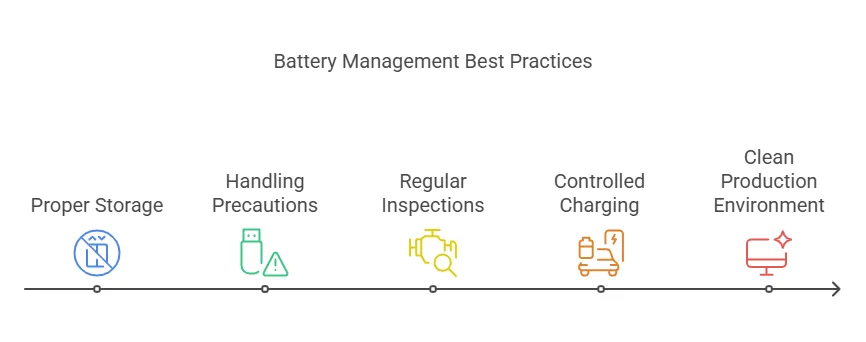
By adhering to these practices, manufacturers can ensure that 18650 batteries remain in optimal condition throughout the production process, reducing waste and improving overall quality.
These topics provide valuable insights into the intricacies of 18650 battery manufacturing, addressing key aspects that appeal to both industry professionals and general readers.
How Can Energy Efficiency Be Improved in 18650 Battery Manufacturing?
Energy efficiency is a critical focus in 18650 battery manufacturing to reduce costs and environmental impact. Here are some strategies to enhance energy efficiency:
-
Advanced Machinery:
- Use high-precision equipment that minimizes energy waste during electrode coating and cell assembly.
- Implement automated systems to reduce manual errors and energy consumption.
-
Process Optimization:
- Streamline production workflows to eliminate redundant steps.
- Optimize drying and curing processes to reduce energy usage.
-
Renewable Energy Integration:
- Install solar panels or wind turbines to power manufacturing facilities.
- Use energy storage systems to balance energy demand and supply.
-
Heat Recovery Systems:
- Capture and reuse heat generated during production for other processes.
- Reduce reliance on external heating sources.
-
Energy Monitoring:
- Install smart meters to track energy consumption in real-time.
- Identify areas for improvement through data analysis.
By adopting these measures, manufacturers can significantly reduce energy consumption while maintaining high production standards.
What Technological Advancements Are Shaping 18650 Battery Manufacturing?
Technological advancements are revolutionizing 18650 battery manufacturing, making it more efficient and sustainable. Key innovations include:
-
Automation and Robotics:
- Automated electrode coating and cell assembly lines improve precision and speed.
- Robots handle hazardous materials, reducing risks to workers.
-
AI and Machine Learning:
- Predictive maintenance systems detect equipment issues before they cause downtime.
- AI algorithms optimize production parameters for better quality and efficiency.
-
Advanced Materials:
- Silicon anodes and solid-state electrolytes enhance energy density and safety.
- New cathode materials like lithium iron phosphate (LFP) reduce costs and environmental impact.
-
3D Printing:
- Enables rapid prototyping of battery components.
- Reduces material waste and accelerates innovation.
-
Smart Manufacturing:
- IoT-enabled devices monitor production in real-time.
- Data-driven insights improve decision-making and process control.
These advancements are driving the industry toward higher performance, lower costs, and greater sustainability.
What Regulatory Standards Govern 18650 Battery Production?
Regulatory standards ensure the safety, quality, and environmental compliance of 18650 battery production. Key standards include:
-
Safety Standards:
- UN 38.3: Ensures batteries can withstand transportation hazards like vibration and temperature extremes.
- IEC 62133: Specifies safety requirements for portable sealed secondary cells.
-
Environmental Regulations:
- RoHS (Restriction of Hazardous Substances): Limits the use of harmful materials like lead and cadmium.
- REACH (Registration, Evaluation, Authorization, and Restriction of Chemicals): Ensures safe handling of chemicals used in production.
-
Quality Standards:
- ISO 9001: Certifies quality management systems in manufacturing.
- ISO 14001: Focuses on environmental management systems.
-
Transportation Regulations:
- IATA Dangerous Goods Regulations: Governs the air transport of lithium-ion batteries.
- ADR (European Agreement Concerning the International Carriage of Dangerous Goods by Road): Applies to road transport.
Compliance with these standards is essential for manufacturers to access global markets and build consumer trust.
How to Optimize 18650 Battery Production for High-Volume Manufacturing?
Optimizing 18650 battery production for high-volume manufacturing requires a combination of advanced technology and efficient processes. Here’s a step-by-step approach:
-
Design for Manufacturability:
- Simplify battery designs to reduce production complexity.
- Use standardized components to streamline assembly.
-
Automate Key Processes:
- Implement robotic systems for electrode coating, winding, and assembly.
- Use automated quality inspection systems to detect defects.
-
Optimize Supply Chain:
- Source high-quality raw materials from reliable suppliers.
- Implement just-in-time inventory to reduce storage costs.
-
Enhance Process Control:
- Use real-time monitoring systems to track production metrics.
- Adjust parameters dynamically to maintain consistency.
-
Scale Up Gradually:
- Start with pilot production to identify and resolve issues.
- Gradually increase output while maintaining quality standards.
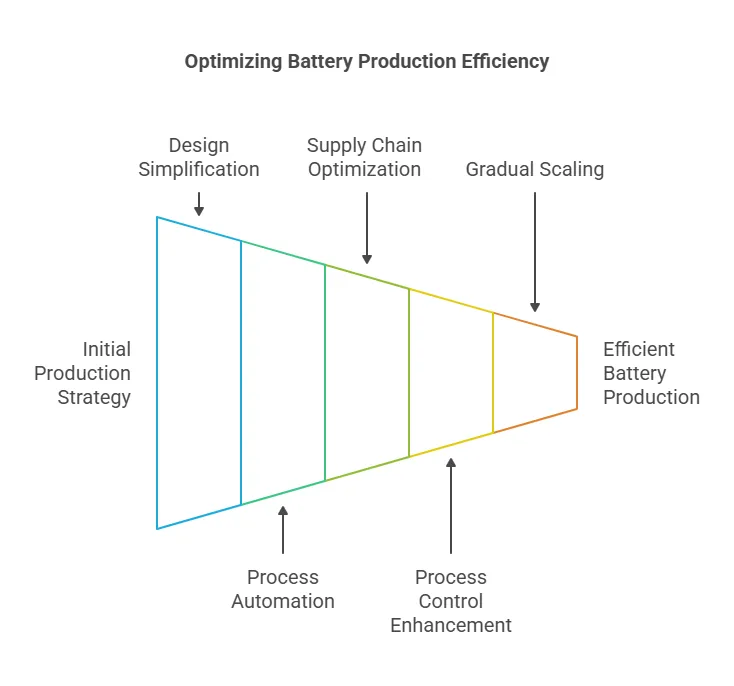
By following these steps, manufacturers can achieve high-volume production without compromising on quality or efficiency.
What Are the Future Trends in 18650 Battery Manufacturing and Innovation?
The future of 18650 battery manufacturing is shaped by emerging trends and innovations that promise to enhance performance, sustainability, and scalability. Key trends include:
-
Solid-State Batteries:
- Replace liquid electrolytes with solid materials for improved safety and energy density.
- Expected to revolutionize the industry by 2030.
-
Recycling and Circular Economy:
- Develop efficient recycling methods to recover valuable materials like lithium and cobalt.
- Reduce reliance on mining and lower environmental impact.
-
AI-Driven Manufacturing:
- Use AI to optimize production processes and predict equipment failures.
- Enhance efficiency and reduce downtime.
-
Customization and Modular Design:
- Produce batteries tailored to specific applications, such as EVs or renewable energy storage.
- Modular designs allow for easy assembly and disassembly.
-
Sustainability Initiatives:
- Adopt green manufacturing practices, such as using renewable energy and reducing waste.
- Develop eco-friendly materials and processes.
These trends highlight the industry’s commitment to innovation and sustainability, paving the way for a brighter future in energy storage.
These topics provide a forward-looking perspective on 18650 battery manufacturing, addressing key trends and innovations that appeal to industry professionals and tech enthusiasts alike.
This comprehensive exploration of 18650 battery manufacturing reveals the meticulous process behind creating these versatile lithium-ion cells. From electrode preparation and cell assembly to rigorous testing and quality control, each stage is crucial in ensuring high performance, safety, and longevity. The article highlights the importance of precision engineering, safety measures, and efficiency optimization in the production process. It also discusses the wide-ranging applications of 18650 batteries across industries, from consumer electronics to medical devices. Additionally, the blog addresses common challenges manufacturers face, such as electrode coating uniformity and thermal management, while emphasizing the importance of environmental and safety considerations in modern factories. Looking ahead, technological advancements like automation, AI, and solid-state batteries are poised to revolutionize the industry, promising enhanced performance and sustainability. This article offers valuable insights for both industry insiders and tech enthusiasts, providing a forward-looking perspective on the future of 18650 battery manufacturing.