The 18650 pack builder has become an indispensable tool in modern battery technology, revolutionizing the way we create powerful and reliable battery packs. Whether used in electric vehicles, consumer electronics, or renewable energy systems, these builders ensure that lithium-ion cells are assembled with precision and safety. In this article, we dive deep into the world of 18650 pack builders, exploring their structure, functionality, and applications. We also discuss the importance of safety, maintenance, and future trends that will shape the industry. Whether you’re a manufacturer or a tech enthusiast, understanding the 18650 pack builder is key to unlocking the full potential of modern battery technology.
What is a 18650 Pack Builder?
A 18650 pack builder is a specialized tool or system designed to assemble 18650 lithium-ion battery cells into functional battery packs. These packs are widely used in various applications, from consumer electronics to electric vehicles. The 18650 pack builder ensures that the cells are connected in a specific configuration (series or parallel) to achieve the desired voltage, capacity, and power output. This process involves precise engineering to ensure safety, efficiency, and longevity of the battery pack.
Structure and Components of a 18650 Pack Builder
The structure of a 18650 pack builder typically includes several key components:
- Cell Holder: This holds the 18650 cells in place during the assembly process.
- Welding System: Often uses laser or spot welding to connect the cells.
- Battery Management System (BMS): Ensures the pack operates within safe parameters.
- Cooling System: Manages heat dissipation to prevent overheating.
- Control Unit: A computer or microcontroller that oversees the entire assembly process.
Each component plays a crucial role in ensuring the final battery pack is both efficient and safe.
How Does a 18650 Pack Builder Work?
The operation of a 18650 pack builder can be broken down into several steps:
- Cell Sorting: Cells are sorted based on their capacity and internal resistance to ensure uniformity.
- Cell Placement: Cells are placed into the cell holder in the desired configuration.
- Welding: The welding system connects the cells using nickel strips.
- BMS Integration: The Battery Management System is connected to monitor and control the pack.
- Testing: The assembled pack undergoes rigorous testing to ensure it meets all specifications.
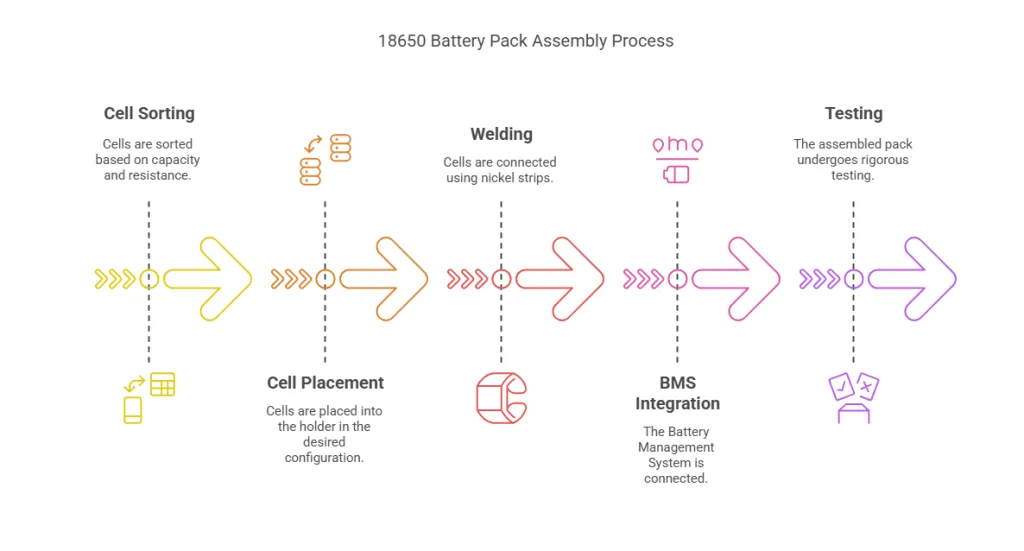
This step-by-step process ensures that each battery pack is built to the highest standards.
Applications of 18650 Pack Builders in the Industry
18650 pack builders are used in a variety of industries, including:
- Electric Vehicles (EVs): For assembling battery packs that power EVs.
- Consumer Electronics: In laptops, power tools, and other portable devices.
- Renewable Energy: For energy storage systems in solar and wind power installations.
- Medical Devices: In portable medical equipment that requires reliable power sources.
The versatility of 18650 pack builders makes them indispensable in modern technology.
Work Environment for 18650 Pack Builders
The work environment for 18650 pack builders is typically a controlled manufacturing setting. Key aspects include:
- Clean Room Conditions: To prevent contamination of the battery cells.
- Temperature Control: To ensure optimal performance of the welding and assembly processes.
- Safety Protocols: Including fire suppression systems and protective gear for workers.
- Automation: Many processes are automated to increase efficiency and reduce human error.
This environment ensures that the battery packs are produced safely and efficiently, meeting the high standards required by various industries.
What is Testing and Quality Assurance for 18650 Pack Builders?
Testing and quality assurance (QA) are critical steps in the production of 18650 battery packs. These processes ensure that each pack meets safety, performance, and reliability standards before it reaches the end user. QA involves a series of rigorous tests to identify defects, verify performance, and confirm compliance with industry regulations. Without proper testing, battery packs could pose safety risks or fail prematurely, leading to costly recalls or accidents.
Key Testing Methods:
- Capacity Testing: Measures the energy storage capability of the pack.
- Voltage Testing: Ensures the pack delivers the correct voltage under load.
- Cycle Life Testing: Evaluates how many charge-discharge cycles the pack can endure.
- Thermal Testing: Assesses the pack’s ability to handle heat and prevent overheating.
- Safety Testing: Includes short-circuit, overcharge, and puncture tests to ensure the pack won’t fail catastrophically.
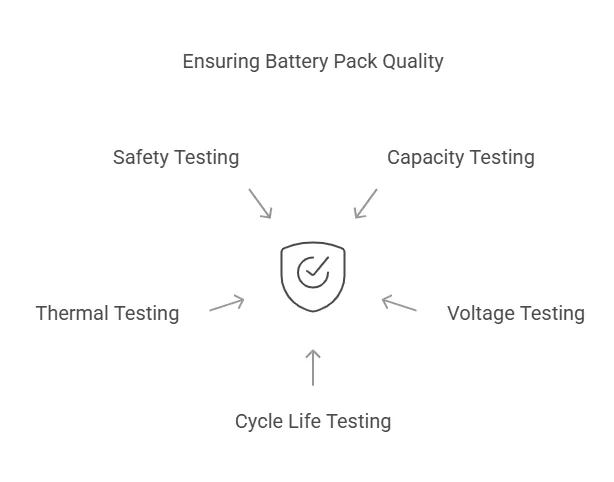
By implementing these tests, manufacturers can guarantee that their 18650 packs are safe, reliable, and high-performing.
Why Safety Precautions and Usage Guidelines are Essential for 18650 Pack Builders
Safety is paramount when working with 18650 pack builders, as improper handling can lead to fires, explosions, or other hazards. These batteries contain highly reactive materials, and their assembly requires strict adherence to safety protocols. Usage guidelines are equally important to ensure the longevity and performance of the battery packs.
Key Safety Precautions:
- Wear Protective Gear: Use gloves, goggles, and fire-resistant clothing.
- Work in a Controlled Environment: Avoid humid or dusty areas to prevent contamination.
- Use Proper Tools: Employ insulated tools and equipment designed for battery assembly.
- Monitor Temperature: Keep the workspace cool to prevent overheating during welding or assembly.
Usage Guidelines:
- Avoid Overcharging: Use a compatible charger to prevent damage.
- Store Properly: Keep packs in a cool, dry place away from flammable materials.
- Inspect Regularly: Check for signs of wear, swelling, or damage.
Following these precautions and guidelines minimizes risks and ensures safe operation.
How to Maintain and Care for 18650 Pack Builders
Proper maintenance and care are essential to keep 18650 pack builders functioning efficiently and extend their lifespan. Regular upkeep prevents malfunctions, reduces downtime, and ensures consistent performance.
Step-by-Step Maintenance Guide:
- Clean the Equipment: Remove dust and debris from the cell holders, welding system, and other components.
- Inspect Connections: Check for loose or corroded connections and tighten or replace them as needed.
- Calibrate Tools: Regularly calibrate the welding system and control unit to ensure precision.
- Lubricate Moving Parts: Apply lubricant to any moving parts to reduce friction and wear.
- Update Software: If the pack builder uses software, ensure it is up to date for optimal performance.
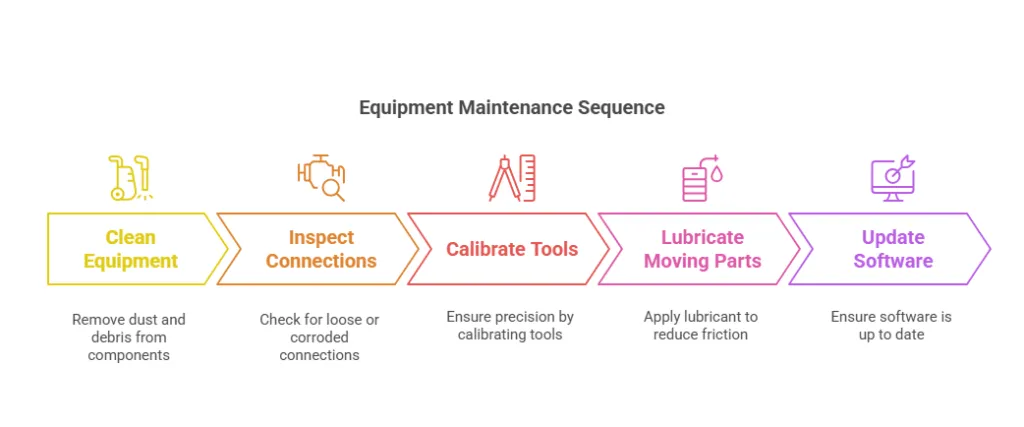
By following these steps, you can keep your 18650 pack builder in top condition and avoid costly repairs.
Troubleshooting Common Issues in 18650 Pack Builders
Even with proper maintenance, 18650 pack builders can encounter issues. Knowing how to troubleshoot these problems can save time and prevent further damage.
Common Issues and Solutions:
-
Poor Welding Connections:
- Cause: Incorrect welding parameters or worn-out electrodes.
- Solution: Adjust the welding settings or replace the electrodes.
-
Cell Misalignment:
- Cause: Improper placement in the cell holder.
- Solution: Re-align the cells and ensure the holder is functioning correctly.
-
Overheating During Assembly:
- Cause: Inadequate cooling or high ambient temperature.
- Solution: Improve ventilation or use a cooling system.
-
BMS Malfunction:
- Cause: Faulty wiring or software glitches.
- Solution: Check connections and update or reset the BMS software.
Addressing these issues promptly ensures smooth operation and high-quality output.
What are the Future Trends in 18650 Pack Builder Technology?
The technology behind 18650 pack builders is constantly evolving to meet the demands of modern industries. Future trends focus on improving efficiency, safety, and sustainability.
Emerging Trends:
- Automation and AI: Increased use of robotics and artificial intelligence to enhance precision and reduce human error.
- Advanced Materials: Development of new materials for cell holders and connectors to improve durability and conductivity.
- Energy-Efficient Designs: Innovations to reduce power consumption during the assembly process.
- Modular Systems: Pack builders that can be easily reconfigured for different battery sizes and configurations.
- Sustainability: Integration of recycling systems to reuse materials and reduce waste.
These advancements will make 18650 pack builders more versatile, efficient, and environmentally friendly, paving the way for next-generation battery solutions.
What are the Types of 18650 Pack Builders: Manual vs. Automated?
When it comes to assembling 18650 battery packs, there are two primary types of pack builders: manual and automated. Each type has its own advantages and is suited for different production needs.
-
Manual 18650 Pack Builders:
- Description: These systems require human operators to perform tasks such as cell placement, welding, and testing.
- Advantages: Lower initial cost, flexibility for small-scale or custom projects.
- Disadvantages: Slower production speed, higher risk of human error, and less consistency.
-
Automated 18650 Pack Builders:
- Description: These systems use robotics, software, and advanced machinery to handle the entire assembly process with minimal human intervention.
- Advantages: High production speed, consistent quality, reduced labor costs, and scalability for large-scale operations.
- Disadvantages: Higher upfront investment and less flexibility for custom configurations.
Choosing between manual and automated pack builders depends on your production volume, budget, and specific requirements.
How to Choose the Right 18650 Pack Builder for Your Production Line
Selecting the right 18650 pack builder is crucial for optimizing your production line. Here’s a step-by-step guide to help you make an informed decision:
-
Assess Your Production Needs:
- Determine your daily or monthly production volume.
- Identify the types of battery packs you need (e.g., series, parallel, or mixed configurations).
-
Evaluate Your Budget:
- Compare the costs of manual vs. automated systems.
- Factor in long-term savings from increased efficiency and reduced labor costs.
-
Consider Scalability:
- Choose a system that can grow with your business.
- Look for modular designs that allow for future upgrades.
-
Check Key Features:
- Ensure the pack builder includes essential features like a reliable welding system, BMS integration, and safety mechanisms.
-
Research Manufacturers:
- Look for reputable manufacturers with a proven track record.
- Read reviews and ask for case studies or references.
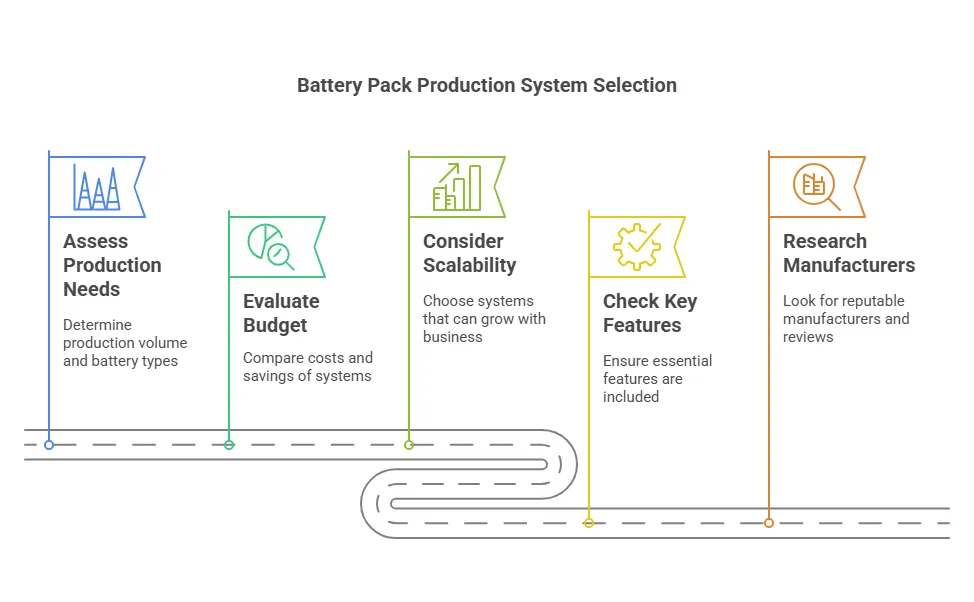
By following these steps, you can select a 18650 pack builder that aligns with your production goals and budget.
Why Energy Efficiency Matters in 18650 Pack Builders
Energy efficiency is a critical factor in 18650 pack builders, as it directly impacts operational costs and environmental sustainability. Efficient systems consume less power, reduce heat generation, and lower the carbon footprint of your production process.
Key Benefits of Energy-Efficient Pack Builders:
- Cost Savings: Reduced energy consumption leads to lower utility bills.
- Improved Performance: Efficient systems often run cooler, enhancing the lifespan of the equipment.
- Environmental Impact: Lower energy use contributes to a greener production process.
How to Improve Energy Efficiency:
- Use advanced welding technologies like laser welding, which requires less energy than traditional methods.
- Implement smart control systems that optimize power usage during idle times.
- Regularly maintain equipment to ensure it operates at peak efficiency.
Investing in energy-efficient 18650 pack builders not only saves money but also supports sustainable manufacturing practices.
What Key Features to Look for in a 18650 Pack Builder
When selecting a 18650 pack builder, certain features are essential to ensure high-quality output and smooth operation. Here are the key features to consider:
- Precision Welding System: Ensures strong and consistent connections between cells.
- Battery Management System (BMS) Integration: Allows for real-time monitoring and control of the battery pack.
- Modular Design: Enables easy reconfiguration for different pack sizes and configurations.
- Safety Mechanisms: Includes features like overheat protection, short-circuit prevention, and emergency stop buttons.
- User-Friendly Interface: Simplifies operation and reduces the learning curve for operators.
- Scalability: Supports future expansion or upgrades to meet growing production demands.
By prioritizing these features, you can choose a pack builder that delivers reliability, efficiency, and versatility.
How Automation in 18650 Pack Building is a Game Changer for the Industry
Automation has revolutionized the 18650 pack building process, offering significant advantages over traditional manual methods. Here’s why automated systems are transforming the industry:
Benefits of Automation:
- Increased Production Speed: Automated systems can assemble packs much faster than manual methods.
- Consistent Quality: Robotics and software ensure uniformity and precision in every pack.
- Reduced Labor Costs: Automation minimizes the need for human operators, lowering labor expenses.
- Enhanced Safety: Automated systems reduce the risk of accidents and injuries in the workplace.
- Scalability: Automated pack builders can easily handle large-scale production demands.
Key Automation Technologies:
- Robotic Arms: For precise cell placement and welding.
- AI and Machine Learning: To optimize the assembly process and detect defects in real time.
- Integrated Software: For seamless control and monitoring of the entire production line.
Automation is not just a trend; it’s a necessity for companies looking to stay competitive in the fast-evolving battery industry. By adopting automated 18650 pack builders, manufacturers can achieve higher efficiency, better quality, and greater profitability.
This comprehensive guide explores the world of 18650 pack builders, specialized systems designed to assemble lithium-ion battery cells into functional packs. We break down the key components, including cell holders, welding systems, and battery management systems, and explain how they work together to ensure safety and efficiency. The article also covers the step-by-step process of building a battery pack, from cell sorting to rigorous testing and quality assurance. We highlight the diverse applications of these builders in industries like electric vehicles, consumer electronics, renewable energy, and medical devices. Additionally, we discuss the importance of safety precautions, maintenance tips, and troubleshooting common issues. Finally, we look ahead to future trends, such as automation, advanced materials, and energy-efficient designs, which promise to make 18650 pack builders even more versatile and sustainable.