Battery manufacturing equipment is at the heart of modern energy innovation. This specialized machinery is crucial for producing high-quality batteries that power everything from electric vehicles to renewable energy systems. In this blog, we will explore the essential components and structure of battery manufacturing equipment, how it works, and its key applications across various industries. Whether you’re interested in the technical details or the broader impact on sustainability, understanding battery manufacturing equipment is key to unlocking the potential of next-generation energy solutions.
What Is Battery Manufacturing Equipment?
Battery manufacturing equipment refers to specialized machinery used to produce various types of batteries, including lithium-ion, lead-acid, and solid-state batteries. These systems automate critical processes like electrode preparation, cell assembly, and quality testing to ensure precision, scalability, and safety in production.
Why Is It Important?
- Efficiency: Automates high-volume production with minimal human intervention.
- Consistency: Ensures uniform battery quality for performance and safety.
- Innovation: Enables next-gen battery designs (e.g., higher energy density).
Key Industries Relying on This Equipment:
- Electric vehicles (EVs)
- Consumer electronics
- Renewable energy storage
What Are the Components and Structure of Battery Manufacturing Equipment?
Modern battery production lines integrate multiple subsystems:
-
Electrode Manufacturing Units
- Coating machines: Apply active materials to metal foils.
- Calenders: Compress electrodes to precise thicknesses.
-
Cell Assembly Modules
- Stacking/Winding machines: Layer anodes, separators, and cathodes.
- Welding systems: Secure tabs and housings.
-
Formation & Testing Systems
- Charging/discharging units: Activate cells and measure capacity.
- X-ray inspectors: Detect internal defects.
Critical Auxiliary Components:
- Dry rooms (humidity control)
- Laser cutters
- Electrolyte filling stations
How Does Battery Manufacturing Equipment Work? A Step-by-Step Flow
Step 1: Electrode Preparation
- Mixing: Active materials, binders, and solvents are blended into slurries.
- Coating: Slurries are uniformly applied to copper/aluminum foils.
- Drying: Coated foils pass through ovens to evaporate solvents.
Step 2: Cell Assembly
- Slitting: Dried electrodes are cut into strips.
- Stacking/Winding: Anodes, separators, and cathodes are layered.
- Encasing: Cells are sealed in pouches or metal casings.
Step 3: Finishing
- Electrolyte injection (for liquid batteries).
- Formation cycling to stabilize performance.
- Grading based on capacity/voltage metrics.
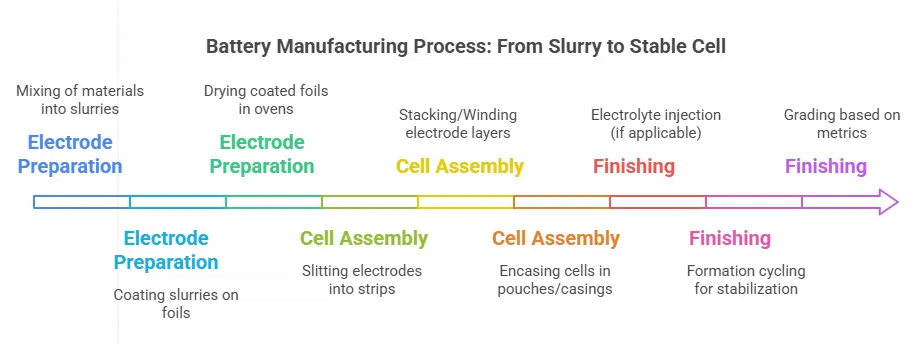
What Are the Working Principles of Battery Manufacturing Equipment?
Battery equipment operates on three core principles:
1. Precision Engineering
- Laser sensors and AI-driven controls maintain micron-level accuracy in coating/cutting.
2. Electrochemical Optimization
- Controlled environments (e.g., dew point < -40°C) prevent moisture-induced degradation.
3. Automation & Data Integration
- PLCs (Programmable Logic Controllers) synchronize conveyor belts, robots, and inspection systems.
- IoT sensors collect real-time data for predictive maintenance.
Example: Winding Machine Operation
- Step 1: Feeds anode/separator/cathode layers from rolls.
- Step 2: Winds them into a “jellyroll” via tension control.
- Step 3: Ultrasonic welds terminal tabs.
What Are the Key Applications of Battery Manufacturing Equipment?
1. Electric Vehicles (EVs)
- Produces high-capacity prismatic/pouch cells for longer range.
- Equipment must meet automotive-grade durability standards (e.g., ISO 16949).
2. Consumer Electronics
- Miniaturized machines manufacture compact Li-ion cells for smartphones/laptops.
3. Grid Storage
- Heavy-duty systems build large-format batteries for solar/wind farms.
Emerging Applications:
- Solid-state batteries: Requires vacuum deposition equipment.
- Recycling: Disassembly/repurposing machines for spent batteries.
How Battery Manufacturing Equipment Differs for Various Battery Types (Li-ion, Sodium-ion, etc.)
What Makes Each Battery Type Unique?
Battery manufacturing equipment must adapt to the chemistry and design of different battery types. Key variations include:
-
Lithium-ion (Li-ion) Batteries:
- Equipment: Precision coating machines for thin electrodes, dry rooms (humidity <1% for moisture-sensitive electrolytes).
- Challenges: Handling flammable electrolytes; strict cleanliness standards.
-
Sodium-ion (Na-ion) Batteries:
- Equipment: Similar to Li-ion but with lower purity requirements (sodium is less reactive).
- Advantage: Can use aluminum foil for anodes (cheaper than copper for Li-ion).
-
Solid-State Batteries:
- Equipment: Sputtering/vacuum deposition systems for solid electrolytes.
- Key Difference: No liquid electrolyte filling stations needed.
Why Does Equipment Vary?
- Material properties (e.g., sodium ions are larger than lithium, requiring different electrode designs).
- Safety protocols (e.g., Li-ion needs explosion-proof environments).
What Are the Work Environment Requirements for Battery Manufacturing Equipment?
Battery production demands tightly controlled conditions:
1. Cleanroom Standards
- Li-ion: ISO Class 5-7 (minimizes particle contamination).
- Humidity: <0.5% dew point for moisture-sensitive processes.
2. Temperature Control
- Electrode drying: 120–180°C ovens with uniform heat distribution.
- Formation rooms: Maintain 25±2°C for stable electrochemical activation.
3. Safety Measures
- Ventilation: NMP (solvent) recovery systems in coating areas.
- Fire Prevention: Argon gas suppression in electrolyte filling zones.
Step-by-Step Workspace Setup:
- Designate dry and wet zones (separate coating from assembly).
- Install humidity monitors with real-time alerts.
- Ground all equipment to prevent static sparks.
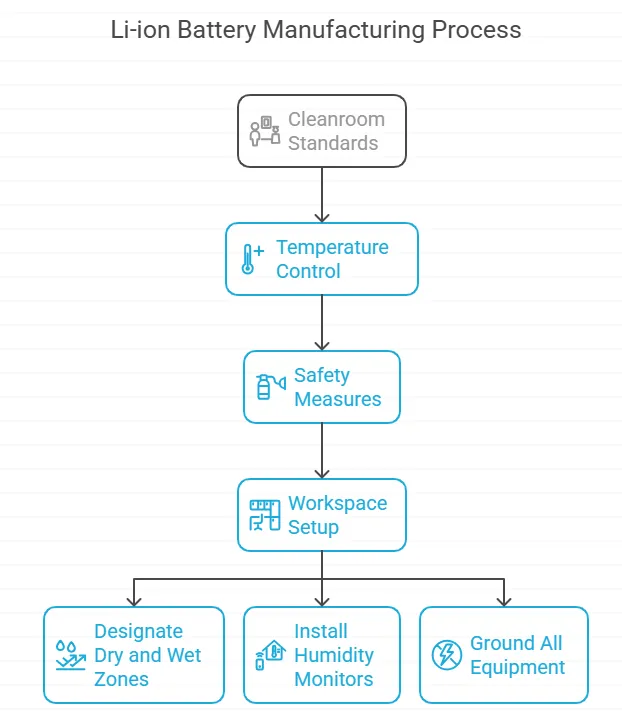
How Is Battery Manufacturing Equipment Tested? Key Product Testing Methods
1. In-Process Testing
- Coating thickness: Laser micrometers verify ±1µm accuracy.
- Electrode defects: AI-powered vision systems detect pinholes/contaminants.
2. Cell-Level Validation
- Cycle testing: Charges/discharges cells 500+ times to simulate lifespan.
- X-ray CT scanning: Checks for internal voids or misalignments.
3. Safety Compliance Tests
- Nail penetration: Ensures no thermal runaway in Li-ion cells.
- Overcharge protection: Confirms battery management system (BMS) response.
Why Testing Matters:
- Catches 99.9% of defects before shipment.
- Reduces recalls (critical for EV batteries).
What Quality Control Measures Are Used in Battery Manufacturing Equipment?
1. Automated Optical Inspection (AOI)
- Compares electrode dimensions to CAD models with <5µm tolerance.
2. Statistical Process Control (SPC)
- Tracks metrics like slurry viscosity (±2% variation allowed).
3. Traceability Systems
- Laser marks QR codes on each cell to log production data (time, machine ID, operator).
Critical QC Checkpoints:
- Raw materials: XRD analyzers confirm cathode material purity.
- Welding seams: Ultrasonic testers verify joint integrity.
- Final assembly: Leak tests for pouch cells (helium detection).
Example: Electrode Coating QC Workflow
- Sample every 100m of coated foil.
- Measure weight/width via automated scales.
- Reject batches if density deviates >1.5%.
What Are the Key Usage Precautions for Battery Manufacturing Equipment?
1. Operator Safety
-
PPE Requirements:
- Anti-static suits (for dry rooms).
- Face shields during electrolyte handling.
2. Machine Maintenance
- Daily: Clean rollers to prevent slurry buildup.
- Monthly: Recalibrate laser sensors.
3. Environmental Risks
- Solvent exposure: NMP must be captured via condensers (OSHA limits: <10 ppm).
- Thermal hazards: Lockout/tagout procedures for oven repairs.
Step-by-Step Shutdown Protocol:
- Purge electrolyte lines with inert gas.
- Backup production data to cloud servers.
- Verify all modules are powered down to prevent short circuits.
Battery manufacturing equipment is vital for producing a wide range of batteries, including lithium-ion, sodium-ion, and solid-state batteries. This specialized machinery automates critical processes such as electrode preparation, cell assembly, and quality testing, ensuring high efficiency, consistency, and safety. Key components include coating machines, stacking/winding systems, and formation/testing units. The equipment operates on principles of precision engineering, electrochemical optimization, and automation, with different types of batteries requiring specific adaptations. From electric vehicles to consumer electronics and grid storage, this equipment supports various applications while meeting stringent quality and safety standards.