Battery manufacturing machines are the unsung heroes behind the rapid advancement of energy storage technologies. These highly specialized machines automate and streamline the production of batteries, ensuring precision, efficiency, and consistency across various industries. From electric vehicles to consumer electronics and renewable energy systems, battery manufacturing machines play a pivotal role in meeting the growing demand for high-performance batteries. This blog delves into the intricacies of these machines, exploring their types, key components, working mechanisms, and applications. Additionally, it highlights the importance of ideal working conditions, quality control measures, safety precautions, and routine maintenance to ensure optimal performance and longevity. Whether you’re an industry professional or a curious enthusiast, this comprehensive guide will provide valuable insights into the world of battery manufacturing.
What is a Battery Manufacturing Machine?
A battery manufacturing machine is a specialized piece of equipment designed to automate and streamline the production of batteries. These machines are essential in the mass production of various types of batteries, including lithium-ion, lead-acid, and nickel-metal hydride batteries. They handle multiple stages of the battery production process, from electrode preparation to final assembly, ensuring high precision, efficiency, and consistency. By integrating advanced technologies such as robotics, AI, and IoT, modern battery manufacturing machines can significantly reduce human error, increase production speed, and improve overall product quality.
Types of Battery Manufacturing Machines
Battery manufacturing machines come in various types, each tailored to specific stages of the battery production process. Here are some common types:
- Electrode Coating Machines: These machines apply active materials onto metal foils to create the battery’s electrodes (anode and cathode).
- Calendering Machines: Used to compress and smooth the coated electrodes to ensure uniform thickness and density.
- Slitting Machines: Cut the coated electrodes into precise widths for further processing.
- Stacking/Winding Machines: Assemble the electrodes and separators into the desired battery cell structure (e.g., prismatic, cylindrical, or pouch).
- Assembly Machines: Handle the final assembly of battery cells, including casing, sealing, and electrolyte filling.
- Formation and Testing Machines: Charge and test the batteries to ensure they meet performance and safety standards.
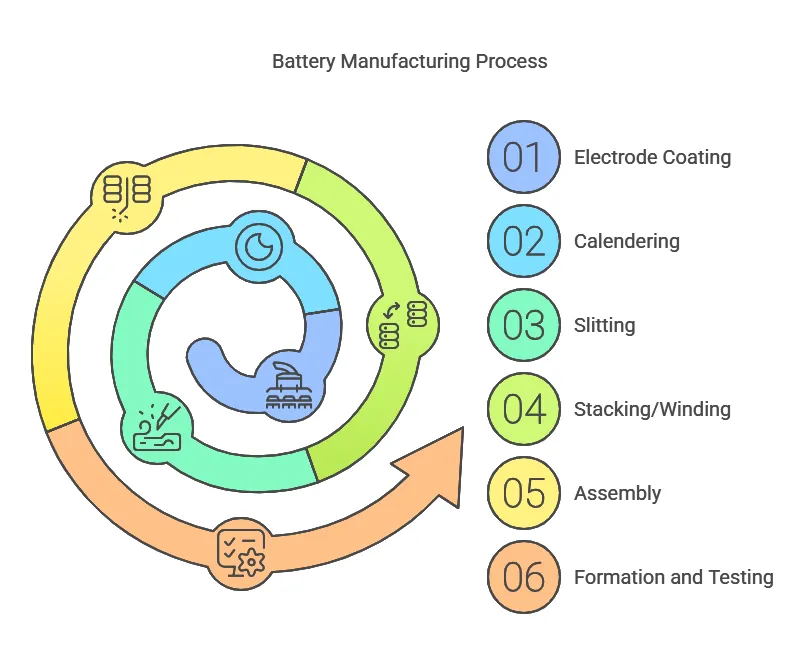
Each type of machine plays a critical role in ensuring the efficiency and reliability of the battery production line.
How Does a Battery Manufacturing Machine Work?
Battery manufacturing machines operate through a series of automated processes that transform raw materials into fully functional batteries. Here’s a step-by-step breakdown of how these machines work:
1. Electrode Preparation:
Raw materials like lithium, cobalt, and graphite are mixed into a slurry.
The slurry is coated onto metal foils using electrode coating machines.
The coated foils are dried and compressed by calendering machines.
2. Electrode Cutting:
Slitting machines cut the coated foils into precise strips.
3. Cell Assembly:
Stacking or winding machines layer the electrodes and separators to form the battery cell.
The cell is then placed into a casing.
4. Electrolyte Filling:
Assembly machines inject the electrolyte solution into the cell.
5. Sealing and Finishing:
The cell is sealed and prepared for the formation process.
6. Formation and Testing:
Formation machines charge the battery for the first time.
Testing machines evaluate the battery’s performance, capacity, and safety.
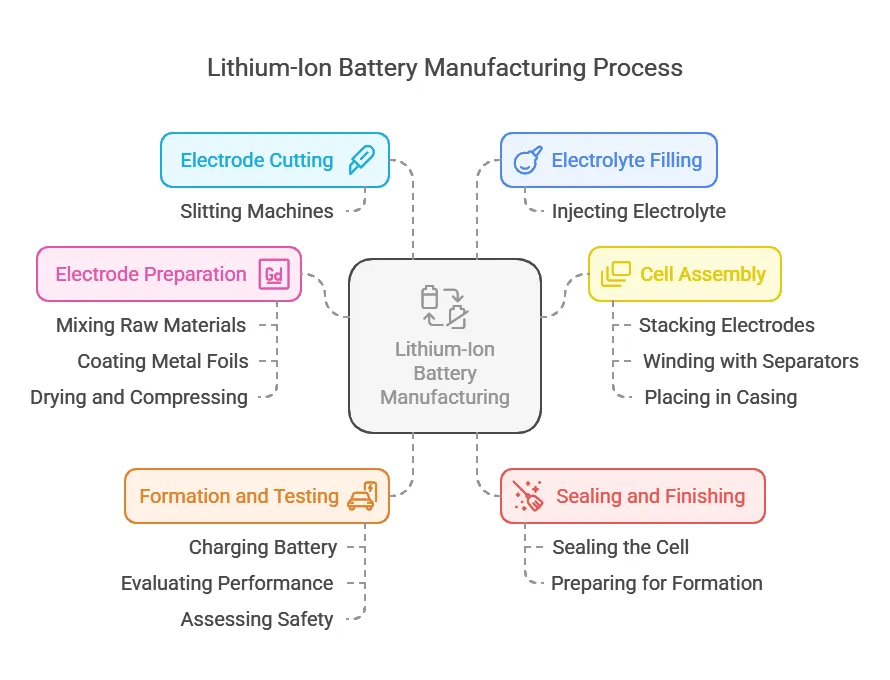
By automating these steps, battery manufacturing machines ensure high precision, consistency, and scalability in production.
Key Components of a Battery Manufacturing Machine
Battery manufacturing machines are complex systems composed of several critical components. These components work together to ensure the efficient and accurate production of batteries. Key components include:
- Coating Head: Applies the electrode slurry onto metal foils with high precision.
- Drying Oven: Removes moisture from the coated electrodes to ensure proper adhesion.
- Calendering Rollers: Compress the electrodes to achieve the desired thickness and density.
- Slitting Blades: Cut the electrodes into precise widths for further processing.
- Robotic Arms: Handle and assemble battery components with high accuracy.
- Electrolyte Filling System: Precisely injects the electrolyte into the battery cell.
- Formation Chambers: Provide controlled environments for the initial charging and discharging of batteries.
- Quality Control Sensors: Monitor and ensure the consistency and safety of the final product.
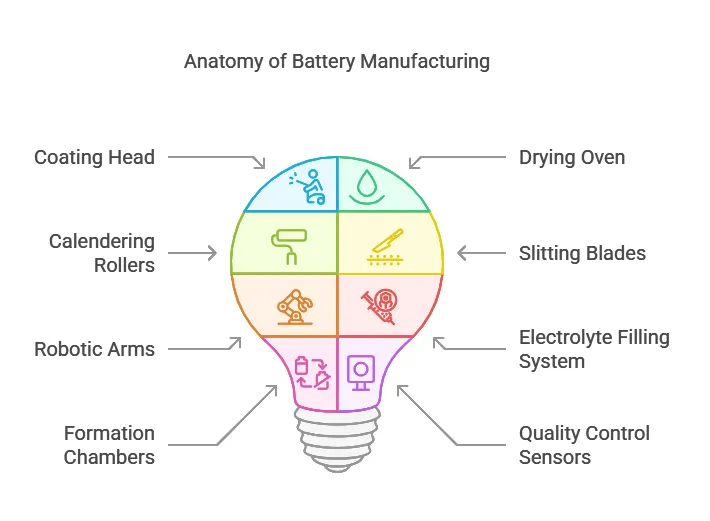
Each component is designed to meet the stringent requirements of battery production, ensuring high performance and reliability.
The battery production process involves several critical steps, each requiring specialized machinery and precise control. Here’s a detailed step-by-step guide:
1. Raw Material Preparation:
Mix active materials, binders, and solvents to create electrode slurries.
2. Electrode Coating:
Use coating machines to apply the slurry onto metal foils (anode and cathode).
3. Drying:
Pass the coated foils through drying ovens to remove solvents and moisture.
4. Calendering:
Compress the dried electrodes using calendering machines to achieve uniform thickness.
5. Slitting:
Cut the electrodes into precise strips using slitting machines.
6. Cell Assembly:
Stack or wind the electrodes and separators to form the battery cell.
Place the cell into a casing.
7. Electrolyte Filling:
Inject the electrolyte solution into the cell using automated filling systems.
8. Sealing:
Seal the cell to prevent leakage and ensure safety.
9. Formation:
Charge and discharge the battery for the first time to activate its electrochemical properties.
10. Testing and Quality Control:
Test the battery for capacity, voltage, and safety.
Sort and package the batteries for distribution.
By following these steps, battery manufacturing machines ensure the production of high-quality batteries that meet industry standards.
Applications of Battery Manufacturing Machines in Different Industries
Battery manufacturing machines are versatile tools that play a crucial role in various industries. Their ability to produce high-quality, efficient, and reliable batteries makes them indispensable in sectors such as:
1. Automotive Industry:
Used to manufacture batteries for electric vehicles (EVs), hybrid vehicles, and start-stop systems.
Ensures the production of high-capacity lithium-ion batteries with long lifespans.
2. Consumer Electronics:
Produces batteries for smartphones, laptops, tablets, and wearable devices.
Focuses on compact, lightweight, and high-energy-density batteries.
3. Renewable Energy Storage:
Manufactures batteries for solar and wind energy storage systems.
Enables efficient energy storage and grid stabilization.
4. Industrial Equipment:
Supplies batteries for forklifts, automated guided vehicles (AGVs), and other industrial machinery.
Emphasizes durability and high performance in demanding environments.
5. Medical Devices:
Produces batteries for portable medical equipment, such as insulin pumps and hearing aids.
Ensures high safety standards and reliability for critical applications.
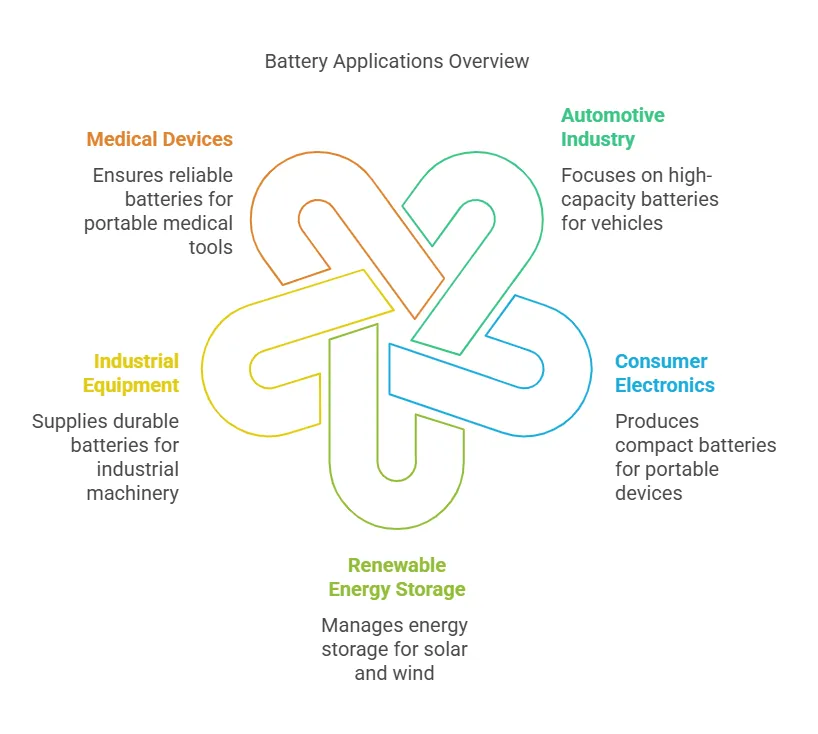
By catering to these diverse industries, battery manufacturing machines drive innovation and support the growing demand for advanced energy storage solutions.
Ideal Working Conditions for Battery Manufacturing Machines
To ensure optimal performance and longevity, battery manufacturing machines require specific working conditions. These conditions include:
1. Controlled Environment:
Temperature and humidity must be regulated to prevent material degradation and ensure consistent production quality.
Ideal temperature range: 20–25°C (68–77°F).
Ideal humidity level: Below 30%.
2. Cleanroom Facilities:
Dust and particulate matter can contaminate battery components, leading to defects.
Cleanrooms with ISO Class 5–7 standards are recommended.
3. Stable Power Supply:
Fluctuations in power can disrupt machine operations and affect product quality.
Uninterruptible power supply (UPS) systems are often used to maintain stability.
4. Proper Ventilation:
Adequate ventilation is necessary to dissipate heat and remove fumes generated during production.
5. Regular Calibration:
Machines must be calibrated frequently to maintain precision and accuracy.
By maintaining these ideal working conditions, manufacturers can maximize the efficiency and reliability of their battery production lines.
Common Quality Control Measures in Battery Manufacturing
Quality control is a critical aspect of battery manufacturing, ensuring that the final products meet safety, performance, and reliability standards. Here are some common measures:
1. Material Inspection:
Raw materials are tested for purity, consistency, and compliance with specifications.
2. In-Process Monitoring:
Sensors and cameras are used to monitor coating thickness, electrode alignment, and other parameters during production.
3. Dimensional Checks:
Electrodes and separators are measured to ensure they meet precise dimensional tolerances.
4. Electrolyte Filling Accuracy:
Automated systems ensure the correct amount of electrolyte is injected into each cell.
5. Formation and Testing:
Batteries undergo initial charging and discharging cycles to activate their electrochemical properties.
Performance metrics such as capacity, voltage, and internal resistance are measured.
6. Safety Testing:
Batteries are subjected to stress tests, including overcharging, short-circuiting, and thermal shock, to ensure safety.
7. Final Inspection:
Visual and automated inspections are conducted to identify defects before packaging.
These measures help manufacturers deliver high-quality batteries that meet industry standards and customer expectations.
Safety Precautions When Operating a Battery Manufacturing Machine
Operating battery manufacturing machines involves handling hazardous materials and high-energy processes, making safety a top priority. Key precautions include:
1. Personal Protective Equipment (PPE):
Operators must wear gloves, goggles, and protective clothing to prevent exposure to chemicals and sharp objects.
2. Proper Training:
Operators should receive comprehensive training on machine operation, emergency procedures, and hazard identification.
3. Ventilation Systems:
Ensure proper ventilation to remove toxic fumes and prevent the buildup of flammable gases.
4. Fire Safety Measures:
Install fire extinguishers, smoke detectors, and sprinkler systems in the production area.
Use non-flammable materials wherever possible.
5. Machine Guarding:
Equip machines with safety guards to prevent accidental contact with moving parts.
6. Emergency Shutdown:
Ensure all machines have easily accessible emergency stop buttons.
7. Regular Inspections:
Conduct routine inspections to identify and address potential safety hazards.
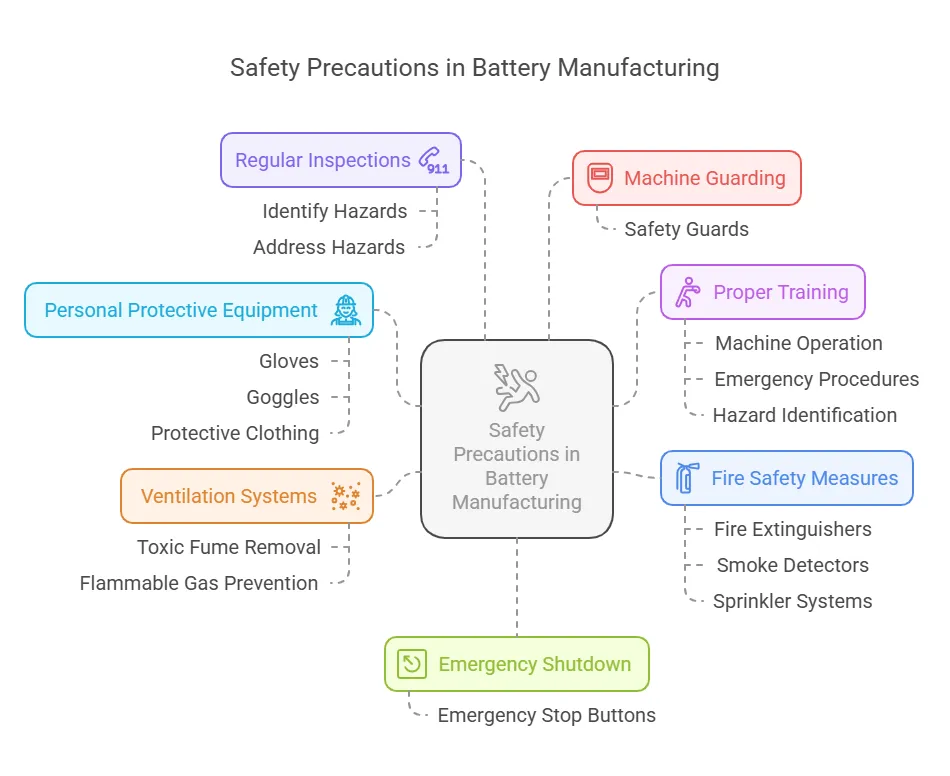
By following these precautions, manufacturers can create a safer working environment and reduce the risk of accidents.
Routine Maintenance and Troubleshooting for Battery Manufacturing Machines
Regular maintenance and timely troubleshooting are essential to keep battery manufacturing machines running smoothly. Here’s a step-by-step guide:
Routine Maintenance:
1. Daily Checks:
Inspect machines for visible damage or wear.
Clean surfaces to remove dust and debris.
2. Weekly Maintenance:
Lubricate moving parts to reduce friction and prevent wear.
Check and tighten loose bolts and connections.
3. Monthly Maintenance:
Calibrate sensors and measuring devices to ensure accuracy.
Replace worn-out components, such as slitting blades or coating heads.
4. Quarterly Maintenance:
Perform a thorough inspection of electrical systems and wiring.
Test safety features, including emergency stop buttons and alarms.
Troubleshooting Common Issues:
1. Uneven Coating:
Check the slurry viscosity and coating head alignment.
Inspect the drying oven for temperature consistency.
2. Machine Jams:
Clear any obstructions in the material feed path.
Ensure the slitting blades are sharp and properly aligned.
3. Electrical Faults:
Inspect wiring and connections for damage.
Test the power supply for stability.
4. Reduced Output Quality:
Verify the calibration of sensors and measuring devices.
Check for wear and tear on critical components.
By following these maintenance and troubleshooting steps, manufacturers can minimize downtime, extend machine lifespan, and maintain consistent production quality.
In conclusion, battery manufacturing machines are indispensable tools in the production of high-quality batteries that power our modern world. From electrode preparation to final assembly, these machines automate complex processes with precision and efficiency, ensuring consistency and scalability. Their applications span across industries such as automotive, consumer electronics, renewable energy, and medical devices, driving innovation and meeting the ever-growing demand for energy storage solutions. To maintain their performance, it is crucial to operate these machines under ideal conditions, implement rigorous quality control measures, and adhere to strict safety protocols. Regular maintenance and timely troubleshooting further enhance their reliability and lifespan. As the world continues to transition toward sustainable energy, battery manufacturing machines will remain at the forefront, enabling the production of advanced batteries that shape the future of technology and energy storage.