In the rapidly evolving landscape of technology and energy solutions, the battery packing machine has become an indispensable tool for industries worldwide. From consumer electronics to electric vehicles and renewable energy storage, these machines are at the forefront of ensuring that battery packs are assembled with precision, efficiency, and safety. This blog explores the critical role of battery packing machines, their intricate components, and the latest innovations that are transforming the industry. Join us as we uncover how these machines are shaping the future of battery production and why they are essential for meeting the demands of a sustainable and high-performance world.
What is a Battery Packing Machine?
A battery packing machine is a specialized piece of equipment designed to automate the process of assembling and packaging battery cells into complete battery packs. These machines are essential in industries where batteries are used extensively, such as consumer electronics, electric vehicles, and renewable energy storage systems. The primary function of a battery packing machine is to ensure that battery cells are securely connected, properly insulated, and efficiently packaged to meet safety and performance standards. By automating this process, manufacturers can significantly increase production speed, reduce labor costs, and minimize the risk of human error, which is critical in maintaining the quality and reliability of battery packs.
Battery Packing Machine Structure and Components
A battery packing machine is composed of several key components that work together to ensure the efficient and accurate assembly of battery packs. These components include:
- Feeding System: This system is responsible for supplying battery cells to the machine. It ensures that cells are fed into the machine at the correct orientation and speed.
- Cell Sorting and Orientation Unit: This unit sorts the battery cells and ensures they are correctly oriented before they are assembled into packs.
- Welding Unit: The welding unit connects the battery cells using techniques such as laser welding or ultrasonic welding. This step is crucial for establishing electrical connections between cells.
- Insulation and Sealing Unit: This unit applies insulating materials and seals the battery pack to protect it from external factors like moisture and dust.
- Testing and Quality Control Unit: After assembly, the battery pack undergoes rigorous testing to ensure it meets safety and performance standards. This unit checks for parameters such as voltage, current, and temperature.
- Packaging Unit: The final unit packages the battery pack, readying it for shipment or further processing.
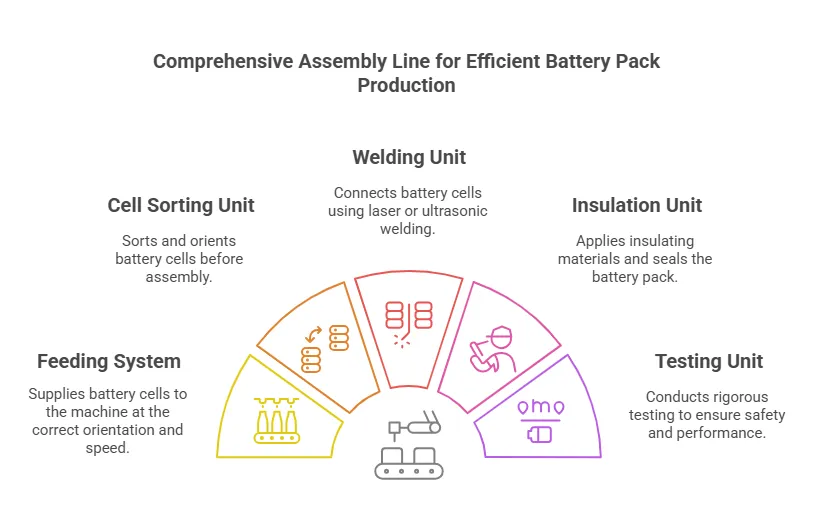
Each component plays a vital role in ensuring the battery packing machine operates efficiently and produces high-quality battery packs.
Battery Packing Machine Workflow: From Cells to Finished Packs
The workflow of a battery packing machine is a meticulously designed process that transforms individual battery cells into fully functional battery packs. Here’s a step-by-step breakdown of the workflow:
- Cell Feeding: Battery cells are fed into the machine through an automated feeding system. This system ensures that cells are delivered at a consistent rate and in the correct orientation.
- Sorting and Orientation: The cells are sorted and oriented to ensure they are correctly positioned for the next stages of assembly.
- Cell Welding: The cells are welded together using advanced welding techniques. This step is critical for establishing the electrical connections that allow the battery pack to function.
- Insulation and Sealing: Insulating materials are applied to the battery pack to protect it from environmental factors. The pack is then sealed to ensure it is secure and safe for use.
- Testing and Quality Control: The assembled battery pack undergoes a series of tests to ensure it meets all safety and performance standards. Any defects or issues are identified and addressed at this stage.
- Packaging: The final step involves packaging the battery pack, making it ready for shipment or further processing.
This workflow ensures that each battery pack is assembled with precision and meets the highest quality standards.
How Does a Battery Packing Machine Work?
A battery packing machine operates through a series of automated processes that ensure the efficient and accurate assembly of battery packs. Here’s how it works:
- Automated Feeding: The machine begins by automatically feeding battery cells into the system. This is done using a conveyor belt or robotic arm that ensures cells are delivered at a consistent rate.
- Precision Welding: Once the cells are in place, the machine uses precision welding techniques to connect them. This step is crucial for establishing the electrical connections that allow the battery pack to function.
- Insulation Application: After welding, the machine applies insulating materials to the battery pack. This protects the pack from environmental factors and ensures its safety.
- Quality Testing: The assembled battery pack is then subjected to a series of tests to ensure it meets all safety and performance standards. This includes checking for proper voltage, current, and temperature levels.
- Final Packaging: Once the battery pack passes all tests, it is packaged and prepared for shipment or further processing.
The entire process is automated, ensuring high efficiency and consistency in the production of battery packs.
Application Scope of Battery Packing Machines
Battery packing machines are used in a wide range of industries where batteries are a critical component. Some of the key applications include:
- Consumer Electronics: Battery packing machines are used to assemble battery packs for devices such as smartphones, laptops, and tablets. These machines ensure that the battery packs are compact, efficient, and safe for use in consumer electronics.
- Electric Vehicles (EVs): In the EV industry, battery packing machines are essential for assembling the large battery packs that power electric cars, buses, and bikes. These machines ensure that the battery packs are robust, reliable, and capable of withstanding the demands of electric vehicles.
- Renewable Energy Storage: Battery packing machines are also used in the renewable energy sector to assemble battery packs for energy storage systems. These systems store energy generated from renewable sources like solar and wind, and the battery packs must be highly efficient and durable.
- Industrial Equipment: In industries that rely on heavy machinery, battery packing machines are used to assemble battery packs for industrial equipment. These packs must be powerful and reliable to ensure the smooth operation of industrial machinery.
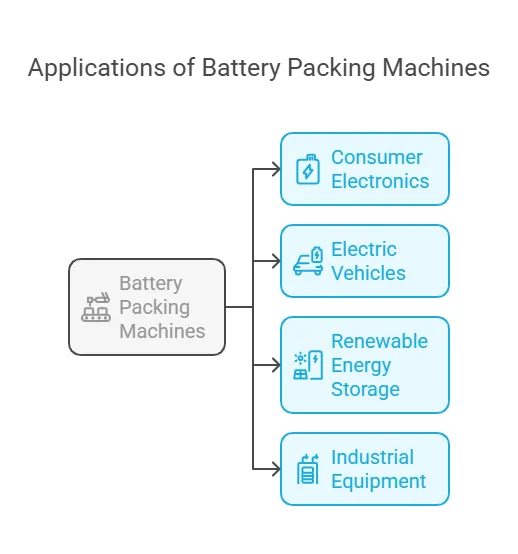
The versatility and efficiency of battery packing machines make them indispensable in these and many other industries.
What is the Optimal Work Environment for Battery Packing Machines?
The optimal work environment for battery packing machines is crucial to ensure their efficient operation and longevity. Here are the key factors to consider:
- Temperature Control: Battery packing machines should operate in a controlled temperature environment, typically between 15°C to 25°C. Extreme temperatures can affect the performance of the machine and the quality of the battery packs.
- Humidity Levels: Maintaining a humidity level between 40% to 60% is essential. Excessive humidity can lead to condensation, which may damage the machine and the battery cells.
- Cleanliness: The workspace should be free from dust and contaminants. A clean environment prevents debris from interfering with the machine’s components and ensures the production of high-quality battery packs.
- Ventilation: Proper ventilation is necessary to dissipate any heat generated by the machine and to maintain air quality. Good airflow helps in preventing overheating and ensures a safe working environment.
- Stable Power Supply: A stable and uninterrupted power supply is critical. Voltage fluctuations can damage the machine and affect the consistency of the battery packs produced.
Creating and maintaining an optimal work environment not only enhances the performance of battery packing machines but also extends their operational life.
How is Battery Pack Testing and Quality Assurance Conducted?
Battery pack testing and quality assurance are vital steps to ensure the safety and reliability of the final product. Here’s a step-by-step guide to the process:
-
Initial Inspection:
- Visual Check: Inspect the battery pack for any visible defects such as cracks, leaks, or misalignments.
- Dimensional Check: Ensure the battery pack meets the specified dimensions and tolerances.
-
Electrical Testing:
- Voltage Test: Measure the voltage of each cell and the overall pack to ensure it meets the required specifications.
- Current Test: Check the current output to verify it aligns with the design parameters.
- Internal Resistance Test: Measure the internal resistance to ensure efficient energy transfer and minimal power loss.
-
Performance Testing:
- Charge/Discharge Cycles: Conduct multiple charge and discharge cycles to evaluate the battery pack’s performance and longevity.
- Capacity Test: Measure the energy capacity to ensure it meets the required standards.
-
Safety Testing:
- Overcharge/Overdischarge Test: Simulate overcharging and overdischarging scenarios to ensure the battery pack can handle extreme conditions without failure.
- Temperature Test: Expose the battery pack to varying temperatures to assess its thermal stability and safety.
-
Final Inspection:
- Labeling and Documentation: Ensure all labels and documentation are accurate and comply with regulatory standards.
- Packaging Check: Verify that the battery pack is securely packaged to prevent damage during transportation.
By following these steps, manufacturers can ensure that each battery pack meets the highest standards of quality and safety.
Why are Safety Precautions Important for Using a Battery Packing Machine?
Safety precautions are essential when using a battery packing machine to prevent accidents and ensure the well-being of operators. Here are some critical safety measures:
- Personal Protective Equipment (PPE): Operators should wear appropriate PPE, including gloves, safety glasses, and protective clothing, to protect against potential hazards.
- Machine Guarding: Ensure all moving parts of the machine are properly guarded to prevent accidental contact.
- Emergency Stop Button: Install and regularly test emergency stop buttons to allow for immediate shutdown in case of an emergency.
- Regular Training: Provide regular training for operators on safe machine operation and emergency procedures.
- Ventilation: Ensure the workspace is well-ventilated to prevent the accumulation of harmful fumes or gases.
- Fire Safety: Equip the workspace with fire extinguishers and ensure all staff are trained in fire safety protocols.
Implementing these safety precautions helps in minimizing risks and creating a safer working environment.
How to Perform Routine Maintenance and Care for Battery Packing Machines?
Routine maintenance and care are essential to keep battery packing machines in optimal condition. Here’s a step-by-step guide:
-
Daily Maintenance:
- Cleaning: Clean the machine daily to remove dust and debris that could affect its performance.
- Inspection: Inspect the machine for any visible signs of wear or damage.
-
Weekly Maintenance:
- Lubrication: Lubricate moving parts to reduce friction and prevent wear.
- Tightening: Check and tighten any loose bolts or screws.
-
Monthly Maintenance:
- Component Check: Inspect critical components such as the welding unit, feeding system, and insulation unit for any signs of wear or damage.
- Calibration: Calibrate the machine to ensure it operates within the specified parameters.
-
Quarterly Maintenance:
- Deep Cleaning: Perform a thorough cleaning of the machine, including hard-to-reach areas.
- Software Update: Update the machine’s software to the latest version to ensure optimal performance.
-
Annual Maintenance:
- Comprehensive Inspection: Conduct a comprehensive inspection of the entire machine, including electrical and mechanical systems.
- Replacement of Worn Parts: Replace any worn or damaged parts to prevent future breakdowns.
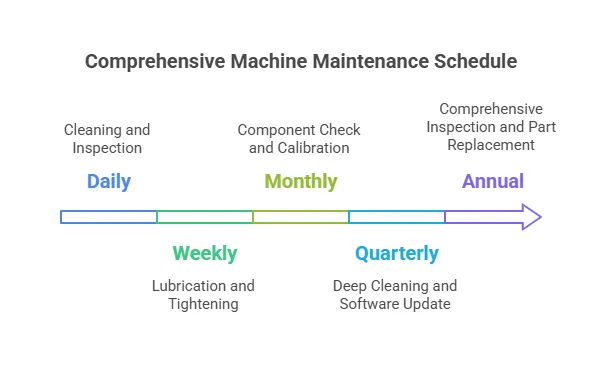
By following this maintenance schedule, you can ensure the longevity and efficiency of your battery packing machine.
What are the Latest Innovations in Battery Packing Machines?
The battery packing machine industry is continuously evolving, with several recent innovations enhancing efficiency and performance:
- Automation and Robotics: Advanced robotics are being integrated into battery packing machines to increase precision and speed. Automated systems can handle complex tasks with minimal human intervention.
- AI and Machine Learning: AI and machine learning algorithms are being used to optimize the packing process. These technologies can predict maintenance needs, improve quality control, and enhance overall efficiency.
- Modular Design: Modern battery packing machines are designed with modular components, allowing for easy upgrades and customization. This flexibility helps manufacturers adapt to changing production needs.
- Energy Efficiency: Newer models are designed to consume less energy, reducing operational costs and environmental impact.
- Enhanced Safety Features: Innovations in safety features, such as advanced sensors and real-time monitoring systems, are making battery packing machines safer to operate.
- Smart Manufacturing: Integration with IoT (Internet of Things) enables real-time data collection and analysis, facilitating smarter decision-making and improving production outcomes.
These innovations are driving the industry forward, making battery packing machines more efficient, reliable, and adaptable to various manufacturing needs.
The battery packing machine is a specialized device that automates the assembly and packaging of battery cells into complete packs. It is a vital component in industries such as consumer electronics, electric vehicles, renewable energy storage, and industrial equipment. These machines consist of key components like feeding systems, cell sorting units, welding units, insulation and sealing units, testing and quality control units, and packaging units. The workflow involves cell feeding, sorting, welding, insulation, testing, and final packaging, ensuring each battery pack meets high safety and performance standards. Optimal operation requires a controlled environment with stable temperature, humidity, cleanliness, ventilation, and power supply. Safety precautions and routine maintenance are essential for efficient operation and longevity. Recent innovations, including advanced automation, AI integration, modular design, energy efficiency, enhanced safety features, and smart manufacturing capabilities, are driving the industry forward. These advancements make battery packing machines more efficient, reliable, and adaptable to modern manufacturing needs.