In the rapidly evolving world of energy storage, the battery pilot line stands as a crucial bridge between laboratory research and large-scale manufacturing. This small-scale production facility is where cutting-edge battery technologies are tested, refined, and validated. From electric vehicles to renewable energy storage, battery pilot lines ensure that innovations in battery design and chemistry are not only feasible but also safe and efficient. In this blog, we will explore the importance of battery pilot lines, their key features, and how they drive the future of sustainable energy solutions.
What is a Battery Pilot Line?
A battery pilot line is a small-scale production facility designed to test and refine the manufacturing processes of batteries before full-scale production begins. It serves as a bridge between research and development (R&D) and mass production, allowing engineers and scientists to experiment with new materials, designs, and manufacturing techniques in a controlled environment. The primary goal of a battery pilot line is to identify potential issues, optimize processes, and ensure that the final product meets quality and performance standards. This step is crucial for industries like electric vehicles (EVs), renewable energy storage, and consumer electronics, where battery performance and safety are critical.
Key Features of Battery Pilot Line Systems
Battery pilot line systems are equipped with advanced technologies and features to support the development and testing of battery prototypes. Here are some of the key features:
- Modular Design: Allows for flexibility in testing different battery chemistries, such as lithium-ion, solid-state, or sodium-ion batteries.
- Precision Equipment: High-accuracy machinery for electrode coating, cell assembly, and electrolyte filling ensures consistent results.
- Data Collection and Analysis: Integrated sensors and software monitor every stage of the production process, providing real-time data for analysis.
- Scalability: Designed to simulate large-scale production, enabling a smooth transition to full manufacturing.
- Safety Mechanisms: Advanced safety protocols to handle volatile materials and prevent accidents during testing.
These features make battery pilot lines indispensable for innovation in battery technology.
How a Battery Pilot Line Works: Workflow and Process
The workflow of a battery pilot line involves several critical steps to ensure the successful development of battery prototypes. Here’s a step-by-step breakdown:
- Material Preparation: Raw materials, such as cathode and anode materials, are prepared and tested for quality.
- Electrode Coating: The materials are coated onto metal foils using precise machinery to create uniform layers.
- Cell Assembly: The coated electrodes are assembled into battery cells, along with separators and electrolytes.
- Formation and Testing: The assembled cells undergo initial charging (formation) and rigorous testing to evaluate performance.
- Data Analysis: Data from the testing phase is analyzed to identify areas for improvement.
- Process Optimization: Based on the analysis, adjustments are made to the materials, equipment, or processes to enhance performance and efficiency.
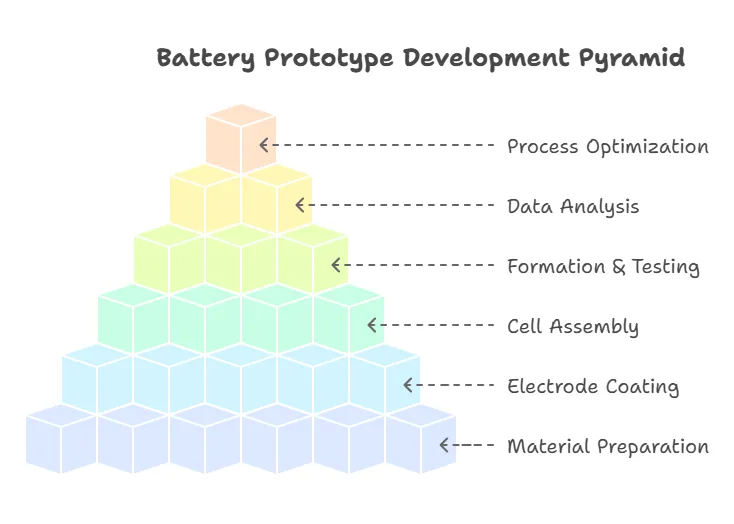
This iterative process ensures that the final product is ready for mass production.
Why Battery Pilot Lines are Important in Manufacturing
Battery pilot lines play a critical role in the manufacturing ecosystem for several reasons:
- Risk Mitigation: They allow manufacturers to identify and address potential issues before scaling up, reducing the risk of costly failures.
- Innovation Acceleration: By providing a platform for testing new technologies, pilot lines accelerate the development of next-generation batteries.
- Cost Efficiency: Optimizing processes at the pilot stage minimizes waste and reduces production costs in the long run.
- Quality Assurance: Ensures that batteries meet stringent quality and safety standards before reaching the market.
- Regulatory Compliance: Helps manufacturers comply with industry regulations and certifications.
Without battery pilot lines, the transition from lab-scale innovations to commercial products would be far more challenging and risky.
How Battery Pilot Lines Ensure Product Quality and Consistency
Battery pilot lines are essential for maintaining high standards of product quality and consistency. Here’s how they achieve this:
- Standardized Processes: Every step, from material preparation to cell assembly, follows strict protocols to ensure uniformity.
- Real-Time Monitoring: Sensors and software track key parameters, such as temperature, pressure, and voltage, during production.
- Iterative Testing: Multiple rounds of testing and refinement help eliminate defects and improve performance.
- Trained Personnel: Skilled technicians and engineers oversee the process, ensuring that best practices are followed.
- Traceability: Detailed records of each batch allow for traceability and accountability in case of issues.
By focusing on these aspects, battery pilot lines ensure that every battery produced meets the highest standards of quality and reliability.
The Role of Battery Pilot Lines in R&D and Scale-Up
Battery pilot lines are a critical component in the transition from research and development (R&D) to full-scale production. They serve as a testing ground where new battery technologies, such as advanced lithium-ion or solid-state batteries, can be evaluated under conditions that mimic real-world manufacturing. Here’s why they are indispensable:
- Bridging the Gap: Pilot lines connect the theoretical work done in labs with the practical demands of mass production.
- Process Validation: They validate whether a new battery design or chemistry can be produced consistently and at scale.
- Cost-Effective Experimentation: By testing on a small scale, companies can avoid the high costs and risks associated with scaling up unproven technologies.
- Data-Driven Decisions: Pilot lines generate valuable data that informs decisions about material selection, equipment, and process optimization.

Without battery pilot lines, scaling up innovative battery technologies would be far more challenging and prone to failure.
Applications of Battery Pilot Lines in the Battery Industry
Battery pilot lines are used across various sectors of the battery industry to drive innovation and improve production processes. Here are some key applications:
- Electric Vehicles (EVs): Developing high-performance, long-lasting batteries for EVs.
- Consumer Electronics: Testing compact and efficient batteries for smartphones, laptops, and wearables.
- Renewable Energy Storage: Creating large-scale batteries for solar and wind energy storage systems.
- Aerospace: Designing lightweight, high-energy-density batteries for satellites and aircraft.
- Medical Devices: Ensuring reliable and safe batteries for life-saving medical equipment.
These applications highlight the versatility and importance of battery pilot lines in advancing battery technology across industries.
Challenges in Setting Up a Battery Pilot Line
Setting up a battery pilot line is a complex endeavor that comes with several challenges:
- High Initial Investment: The cost of specialized equipment, materials, and skilled personnel can be prohibitive.
- Technical Complexity: Integrating advanced technologies, such as precision coating machines and automated assembly systems, requires expertise.
- Regulatory Compliance: Meeting safety and environmental regulations adds another layer of complexity.
- Scalability Issues: Ensuring that processes tested on a small scale can be replicated in mass production.
- Material Sourcing: Securing high-quality raw materials consistently can be difficult.
Addressing these challenges requires careful planning, collaboration with experts, and a commitment to continuous improvement.
How to Optimize Battery Pilot Line Efficiency: Best Practices
Optimizing the efficiency of a battery pilot line is essential for reducing costs and improving output quality. Here are some best practices:
- Streamline Workflow: Design the production process to minimize bottlenecks and downtime.
- Invest in Automation: Use automated systems for repetitive tasks to increase precision and speed.
- Regular Maintenance: Schedule routine maintenance to prevent equipment failures and ensure consistent performance.
- Employee Training: Train staff on the latest technologies and best practices to enhance productivity.
- Data Utilization: Leverage data analytics to identify inefficiencies and optimize processes.
- Material Management: Implement strict quality control measures for raw materials to avoid defects.
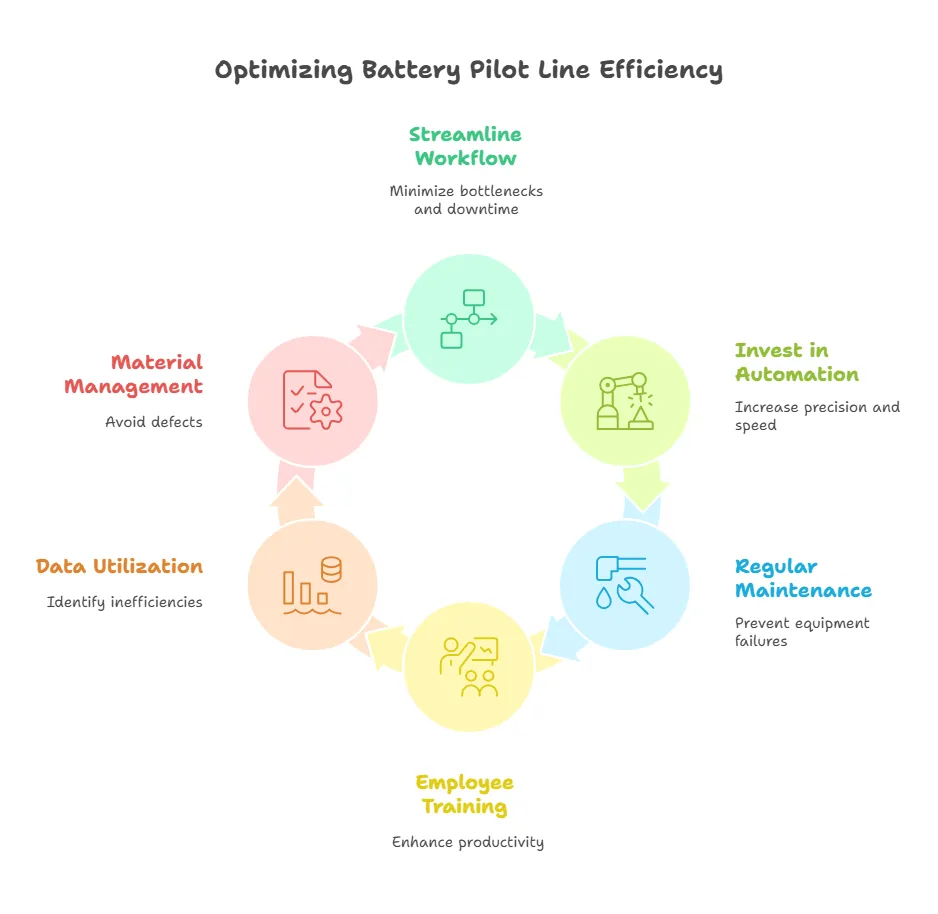
By following these practices, companies can maximize the efficiency and effectiveness of their battery pilot lines.
Testing and Validation in Battery Pilot Lines: Methods and Standards
Testing and validation are critical steps in ensuring that batteries produced in pilot lines meet quality and performance standards. Here’s how it’s done:
-
Step-by-Step Testing Process:
- Initial Inspection: Check raw materials and components for defects.
- In-Process Testing: Monitor key parameters, such as thickness and uniformity, during electrode coating and cell assembly.
- Formation Testing: Conduct initial charge-discharge cycles to activate the battery.
- Performance Testing: Evaluate capacity, cycle life, and energy density under various conditions.
- Safety Testing: Test for thermal stability, overcharge protection, and short-circuit resistance.
-
Standards and Protocols:
- ISO Standards: Compliance with ISO 9001 for quality management and ISO 14001 for environmental management.
- Industry Standards: Adherence to standards set by organizations like IEC (International Electrotechnical Commission) and UL (Underwriters Laboratories).
- Custom Protocols: Develop internal testing protocols tailored to specific battery chemistries and applications.
These methods and standards ensure that batteries are safe, reliable, and ready for commercialization.
Key Considerations for Battery Pilot Line Operation and Maintenance
Operating and maintaining a battery pilot line requires careful planning and execution to ensure efficiency, safety, and longevity. Here are the key considerations:
- Equipment Calibration: Regularly calibrate machinery to maintain precision in processes like electrode coating and cell assembly.
- Safety Protocols: Implement strict safety measures to handle hazardous materials and prevent accidents.
- Staff Training: Ensure that operators and technicians are well-trained in using advanced equipment and following protocols.
- Preventive Maintenance: Schedule routine inspections and maintenance to avoid unexpected downtime.
- Data Management: Use advanced software to monitor performance metrics and identify areas for improvement.
- Material Quality Control: Establish rigorous standards for raw material inspection to prevent defects in the final product.
By addressing these factors, companies can ensure smooth operations and extend the lifespan of their battery pilot lines.
Innovations in Battery Pilot Lines: Future Trends and Developments
The battery pilot line industry is evolving rapidly, driven by technological advancements and growing demand for better batteries. Here are some future trends and developments:
- Automation and AI: Increased use of artificial intelligence (AI) and machine learning to optimize processes and predict outcomes.
- Solid-State Batteries: Pilot lines are being adapted to test and produce solid-state batteries, which offer higher energy density and safety.
- Sustainable Practices: Integration of eco-friendly materials and processes to reduce environmental impact.
- Modular Systems: Development of modular pilot lines that can be easily reconfigured for different battery chemistries and formats.
- Digital Twins: Use of digital twin technology to simulate and optimize production processes before physical implementation.
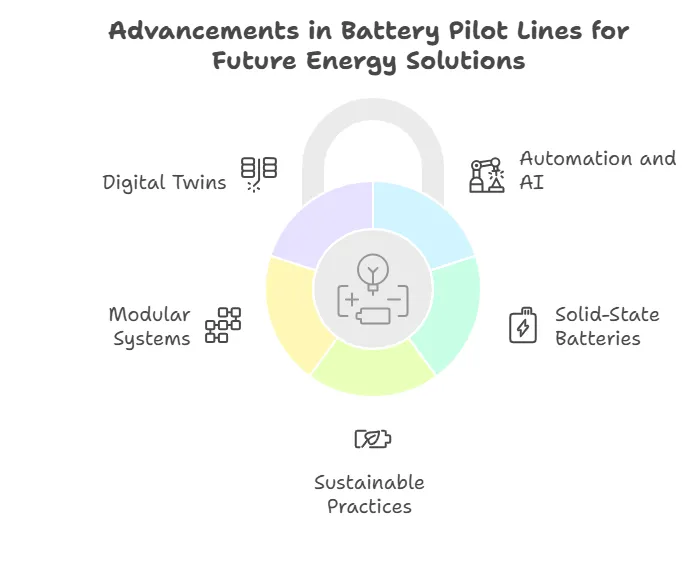
These innovations are shaping the future of battery pilot lines, making them more efficient, flexible, and sustainable.
How Battery Pilot Lines Impact Sustainability in the Battery Industry
Battery pilot lines play a significant role in promoting sustainability within the battery industry. Here’s how:
- Material Efficiency: By optimizing processes, pilot lines reduce material waste during production.
- Energy Savings: Advanced technologies and streamlined workflows lower energy consumption.
- Recycling Integration: Pilot lines can test and implement recycling processes for used batteries, reducing environmental impact.
- Eco-Friendly Innovations: They enable the development of greener battery chemistries, such as lithium-sulfur or sodium-ion batteries.
- Regulatory Compliance: Pilot lines help manufacturers meet stringent environmental regulations and standards.
Through these contributions, battery pilot lines are helping to create a more sustainable battery industry.
Cost Analysis: Setting Up and Running a Battery Pilot Line
Setting up and running a battery pilot line involves significant financial investment. Here’s a breakdown of the costs:
-
Initial Setup Costs:
- Equipment: High-precision machinery for coating, assembly, and testing.
- Facility: Building or retrofitting a space to meet safety and operational requirements.
- Materials: Initial inventory of raw materials for testing and production.
- Labor: Hiring skilled technicians, engineers, and operators.
-
Ongoing Operational Costs:
- Maintenance: Regular upkeep of equipment and facilities.
- Utilities: Energy and water consumption for production processes.
- Training: Continuous education for staff on new technologies and protocols.
- R&D: Investment in research and development to innovate and improve processes.
While the costs can be high, the long-term benefits of reduced risk, improved product quality, and faster time-to-market often justify the investment.
Comparing Battery Pilot Line Solutions: What to Consider When Choosing a System
Choosing the right battery pilot line system is crucial for achieving your production goals. Here are the key factors to consider:
- Flexibility: Can the system handle multiple battery chemistries and formats?
- Scalability: Is it designed to transition smoothly from pilot-scale to mass production?
- Automation Level: Does it offer advanced automation features to improve efficiency and precision?
- Data Integration: Are there robust data collection and analysis capabilities?
- Safety Features: Does the system include comprehensive safety mechanisms for handling hazardous materials?
- Vendor Support: What level of technical support and training does the vendor provide?
- Cost: Does the system offer a good balance between upfront costs and long-term value?
By carefully evaluating these factors, you can select a battery pilot line solution that meets your specific needs and goals.
The battery pilot line is a vital component in modern energy technology, serving as a testing ground for new battery designs and manufacturing processes. Equipped with modular designs, precision machinery, and real-time data analysis, these facilities optimize production efficiency and ensure product consistency. They play a crucial role in risk mitigation, cost reduction, and regulatory compliance, making them indispensable for industries that rely on high-performance batteries. Despite challenges in setup and operation, battery pilot lines drive innovation and sustainability by enabling the development of advanced battery chemistries and eco-friendly practices. As the demand for better energy storage solutions grows, the role of battery pilot lines in bridging the gap between lab-scale research and commercial production becomes more important than ever.