In an era of rapid technological advancement, the demand for efficient and sustainable solutions has never been higher. One such solution lies in the realm of battery recycling. With the exponential growth of electric vehicles, consumer electronics, and renewable energy storage, the importance of battery recycling lines cannot be overstated. This article delves into the inner workings, challenges, and future innovations of battery recycling lines, highlighting their crucial role in building a circular economy and reducing environmental impact.
What is a Battery Recycling Line?
A battery recycling line is a specialized system designed to process used or end-of-life batteries, extracting valuable materials such as lithium, cobalt, nickel, and other metals for reuse in new battery production or other industries. This process not only helps reduce environmental pollution caused by improper disposal of batteries but also conserves natural resources by minimizing the need for raw material extraction. Battery recycling lines are essential in supporting the circular economy, ensuring that materials are reused efficiently and sustainably.
Battery Recycling Line: Product Structure and Workflow
A battery recycling line typically consists of several key components that work together to ensure efficient and safe processing. These include:
- Shredding Unit: Breaks down batteries into smaller pieces for easier handling.
- Sorting System: Separates different types of batteries and materials using advanced technologies like magnetic separation or air classification.
- Crushing and Grinding Unit: Further reduces the size of battery components to extract valuable metals.
- Chemical Leaching Unit: Uses chemical solutions to dissolve and separate metals from other materials.
- Purification System: Refines extracted metals to meet industry standards for reuse.
- Waste Management System: Safely disposes of non-recyclable materials and by-products.
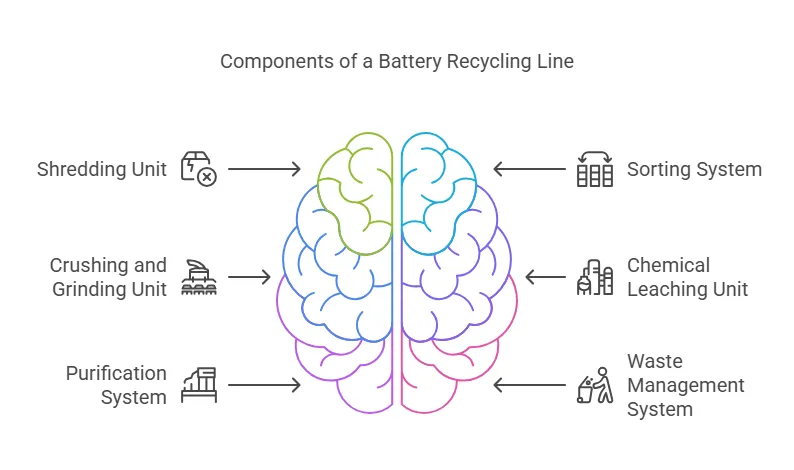
The workflow begins with the collection and transportation of used batteries to the recycling facility. Once processed, the extracted materials are sent to manufacturers for reuse, while the remaining waste is managed responsibly.
How Does a Battery Recycling Line Work?
A battery recycling line operates through a series of well-defined steps to ensure maximum efficiency and safety. Here’s a step-by-step breakdown:
- Collection and Transportation: Used batteries are collected from various sources and transported to the recycling facility.
- Initial Sorting: Batteries are sorted by type (e.g., lithium-ion, lead-acid) and chemistry to ensure proper processing.
- Shredding: Batteries are shredded into smaller pieces to facilitate further processing.
- Separation: Materials like metals, plastics, and electrolytes are separated using mechanical and chemical methods.
- Chemical Treatment: Valuable metals are extracted through leaching and purification processes.
- Refining: Extracted metals are refined to meet industry standards for reuse.
- Waste Disposal: Non-recyclable materials are safely disposed of or treated to minimize environmental impact.
This systematic approach ensures that the recycling process is both efficient and environmentally friendly.
Battery Recycling Line: Key Applications in the Industry
Battery recycling lines play a crucial role in various industries, including:
- Electric Vehicle (EV) Industry: With the rise of EVs, the demand for lithium-ion batteries has surged. Recycling lines help recover valuable materials like lithium and cobalt, reducing the need for new mining.
- Consumer Electronics: Used batteries from smartphones, laptops, and other devices are processed to recover metals for reuse in new products.
- Energy Storage Systems: Large-scale battery systems used in renewable energy storage can be recycled to extract materials for new systems.
- Industrial Applications: Batteries used in industrial equipment and machinery are recycled to recover metals and reduce waste.
By supporting these industries, battery recycling lines contribute to a more sustainable and resource-efficient economy.
The Ideal Work Environment for Battery Recycling Lines
To operate efficiently and safely, battery recycling lines require a carefully controlled work environment. Key considerations include:
- Safety Measures: Due to the hazardous nature of battery materials, facilities must have robust safety protocols, including fire suppression systems and protective equipment for workers.
- Ventilation and Air Quality: Proper ventilation is essential to prevent the buildup of toxic fumes during the recycling process.
- Temperature Control: Some processes, like chemical leaching, require specific temperature conditions to ensure optimal performance.
- Automation and Monitoring: Advanced automation and real-time monitoring systems help maintain efficiency and reduce the risk of accidents.
- Compliance with Regulations: Facilities must adhere to local and international environmental and safety regulations to ensure responsible operations.
By maintaining an ideal work environment, battery recycling lines can operate at peak efficiency while minimizing risks to workers and the environment.
What is Product Testing and Quality Assurance in a Battery Recycling Line?
Product testing and quality assurance are critical components of a battery recycling line to ensure the system operates efficiently, safely, and reliably. These processes involve rigorous checks at every stage of the recycling process, from initial material intake to final output. Testing ensures that the extracted materials meet industry standards for purity and usability, while quality assurance guarantees that the equipment functions as intended without breakdowns or safety hazards.
Key steps in product testing and quality assurance include:
- Material Analysis: Testing incoming batteries to determine their composition and suitability for recycling.
- Process Monitoring: Using sensors and software to track the efficiency of shredding, sorting, and chemical extraction processes.
- Output Verification: Analyzing recovered materials to ensure they meet required specifications for reuse.
- Equipment Calibration: Regularly calibrating machinery to maintain optimal performance.
- Safety Audits: Conducting routine inspections to ensure compliance with safety standards.
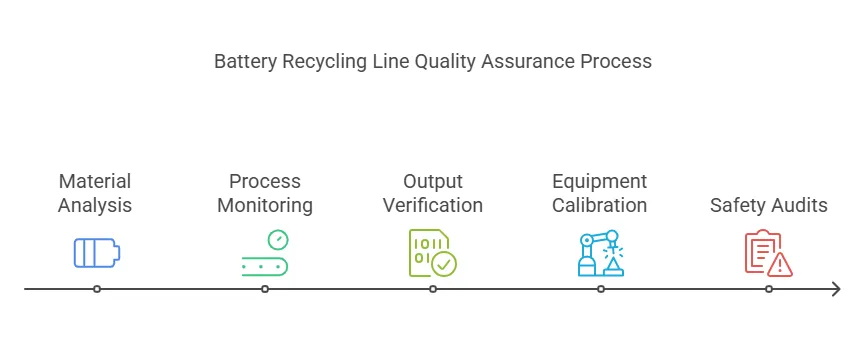
By implementing these measures, battery recycling lines can deliver consistent, high-quality results while minimizing risks.
Why are Usage Precautions Important for Battery Recycling Lines? Best Practices for Safety
Battery recycling lines handle hazardous materials, including toxic chemicals and flammable components, making safety precautions essential. Proper usage practices not only protect workers but also ensure the longevity of the equipment and the efficiency of the recycling process.
Here are some best practices for safety:
- Personal Protective Equipment (PPE): Workers should wear gloves, goggles, masks, and flame-resistant clothing to protect against chemical exposure and physical hazards.
- Fire Prevention: Install fire suppression systems and avoid exposing batteries to high temperatures or sparks during processing.
- Ventilation: Ensure proper ventilation to prevent the buildup of toxic gases released during battery breakdown.
- Training: Provide comprehensive training to operators on handling hazardous materials and emergency procedures.
- Regular Inspections: Conduct routine checks on equipment to identify and address potential issues before they escalate.
By following these precautions, facilities can maintain a safe and productive work environment.
How to Maintain and Care for Your Battery Recycling Line
Proper maintenance is crucial for ensuring the longevity and efficiency of a battery recycling line. Regular care minimizes downtime, reduces repair costs, and ensures consistent performance. Here’s a step-by-step guide to maintaining your recycling line:
- Daily Inspections: Check for wear and tear on shredders, conveyors, and sorting systems.
- Lubrication: Regularly lubricate moving parts to prevent friction and overheating.
- Cleaning: Remove debris and residue from equipment to avoid blockages and corrosion.
- Component Replacement: Replace worn-out parts, such as blades or filters, as needed.
- Software Updates: Ensure control systems and monitoring software are up to date for optimal performance.
- Training: Continuously train staff on proper maintenance procedures and troubleshooting.
By adhering to these practices, you can extend the lifespan of your battery recycling line and maintain its efficiency.
What are the Common Challenges in Battery Recycling Lines and How to Overcome Them?
Battery recycling lines face several challenges that can impact their efficiency and profitability. Understanding these challenges and implementing solutions is key to successful operations.
-
Challenge 1: Diverse Battery Chemistries
Different types of batteries (e.g., lithium-ion, lead-acid, nickel-metal hydride) require unique processing methods.
Solution: Implement advanced sorting technologies to separate batteries by chemistry before processing. -
Challenge 2: Hazardous Materials
Batteries contain toxic and flammable substances, posing safety risks.
Solution: Use automated systems and robust safety protocols to minimize human exposure. -
Challenge 3: High Energy Consumption
Recycling processes can be energy-intensive, increasing operational costs.
Solution: Invest in energy-efficient equipment and explore renewable energy sources. -
Challenge 4: Contamination of Recovered Materials
Impurities in recovered metals can reduce their market value.
Solution: Enhance purification processes to ensure high-quality output.
By addressing these challenges proactively, battery recycling lines can operate more efficiently and sustainably.
What is the Future of Battery Recycling? Innovations in Recycling Lines
The future of battery recycling is being shaped by technological advancements and growing environmental concerns. Innovations in recycling lines are making the process more efficient, cost-effective, and environmentally friendly.
Key innovations include:
- AI and Machine Learning: Using AI to optimize sorting and processing, reducing errors and improving efficiency.
- Direct Recycling Methods: Developing techniques to recover and reuse battery materials without breaking them down completely, saving energy and resources.
- Modular Systems: Designing modular recycling lines that can be easily upgraded or expanded to handle new battery chemistries.
- Green Chemistry: Using environmentally friendly chemicals and processes to minimize waste and pollution.
- Closed-Loop Systems: Creating fully integrated systems where recycled materials are directly fed back into battery production.
These innovations are paving the way for a more sustainable and efficient battery recycling industry, supporting the global transition to clean energy and circular economies.
Why is Cost-Efficiency Important for Battery Recycling Lines in the Long Run?
Cost-efficiency is a critical factor for battery recycling lines, as it directly impacts the profitability and sustainability of recycling operations. While the initial investment in a recycling line can be significant, the long-term savings and revenue potential make it a worthwhile endeavor. By recovering valuable materials like lithium, cobalt, and nickel, recycling lines can offset operational costs and generate income from the sale of these materials.
Key factors contributing to cost-efficiency include:
- Material Recovery Rates: Higher recovery rates of valuable metals increase revenue.
- Energy Consumption: Energy-efficient systems reduce operational costs.
- Automation: Automated processes lower labor costs and improve precision.
- Maintenance: Regular maintenance minimizes downtime and repair expenses.
- Scalability: Modular systems allow for expansion as demand grows, spreading costs over time.
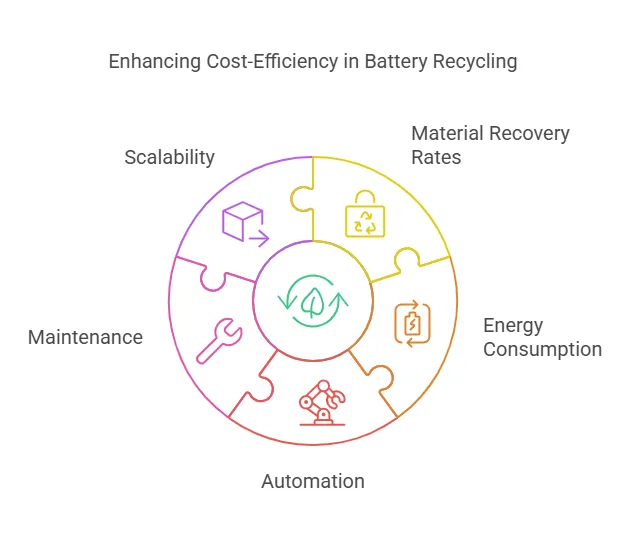
By focusing on these factors, businesses can maximize the cost-efficiency of their battery recycling lines and ensure long-term success.
What are the Regulations and Standards for Battery Recycling Lines?
Battery recycling lines must comply with a range of regulations and standards to ensure safety, environmental protection, and operational efficiency. These regulations vary by region but generally focus on minimizing environmental impact, protecting worker safety, and ensuring the quality of recovered materials.
Key regulations and standards include:
- Environmental Regulations: Laws governing the disposal of hazardous waste and emissions, such as the EU’s Battery Directive or the U.S. Resource Conservation and Recovery Act (RCRA).
- Safety Standards: Guidelines for handling hazardous materials, including OSHA standards in the U.S. or ISO 45001 for occupational health and safety.
- Material Quality Standards: Specifications for recovered materials, such as ASTM International standards for metal purity.
- Data Reporting: Requirements for tracking and reporting recycling rates and material recovery.
Compliance with these regulations not only ensures legal operation but also enhances the credibility and reputation of recycling facilities.
How to Choose the Right Battery Recycling Line for Your Needs
Selecting the right battery recycling line is crucial for meeting your operational goals and ensuring long-term success. Here’s a step-by-step guide to help you make an informed decision:
- Assess Your Needs: Determine the types and volumes of batteries you will be processing (e.g., lithium-ion, lead-acid, etc.).
- Evaluate Recovery Rates: Choose a system that maximizes the recovery of valuable materials like lithium, cobalt, and nickel.
- Consider Automation: Opt for automated systems to reduce labor costs and improve efficiency.
- Check Energy Efficiency: Select equipment with low energy consumption to minimize operational costs.
- Review Safety Features: Ensure the system includes robust safety measures for handling hazardous materials.
- Verify Compliance: Confirm that the recycling line meets all relevant regulations and standards.
- Plan for Scalability: Choose a modular system that can be expanded as your needs grow.
- Compare Costs: Balance upfront costs with long-term savings and revenue potential.
By following these steps, you can select a battery recycling line that aligns with your specific requirements and goals.
What is the Energy Efficiency and Environmental Impact of Battery Recycling Lines?
Energy efficiency and environmental impact are key considerations for battery recycling lines, as they directly affect sustainability and operational costs. Modern recycling lines are designed to minimize energy consumption and reduce environmental harm, making them a greener alternative to traditional mining and disposal methods.
Key aspects of energy efficiency and environmental impact include:
- Energy-Efficient Equipment: Advanced technologies like low-energy shredders and automated sorting systems reduce power usage.
- Renewable Energy Integration: Some facilities use solar or wind power to further lower their carbon footprint.
- Waste Reduction: Efficient recycling processes minimize the amount of non-recyclable waste sent to landfills.
- Emission Control: Systems for capturing and treating harmful gases and particulates reduce air pollution.
- Water Usage: Closed-loop water systems minimize water consumption and prevent contamination.
By prioritizing energy efficiency and environmental sustainability, battery recycling lines can contribute to a cleaner, greener future while maintaining cost-effectiveness.
Battery recycling lines are specialized systems designed to extract valuable materials from used batteries, promoting sustainability and resource conservation. These systems consist of key components such as shredding units, sorting systems, and chemical leaching units, all working together to ensure efficient and safe processing. The workflow involves collection, sorting, shredding, separation, and purification of materials, followed by responsible waste management. They are essential in various industries, including electric vehicles, consumer electronics, and energy storage systems. However, challenges like diverse battery chemistries, hazardous materials, and high energy consumption must be addressed through advanced sorting technologies, robust safety protocols, and energy-efficient equipment. Innovations in AI, direct recycling methods, and modular systems are paving the way for a more sustainable future. By focusing on cost-efficiency, regulatory compliance, and environmental impact, battery recycling lines can significantly contribute to a greener economy.