As the world increasingly relies on batteries to power everything from smartphones to electric vehicles, the importance of battery recycling technology cannot be overstated. This cutting-edge field is revolutionizing how we manage waste and conserve valuable resources. From advanced extraction methods like pyrometallurgy and hydrometallurgy to the intricate processes of sorting and refining, battery recycling technology is at the forefront of environmental sustainability. Join us as we explore the inner workings of this transformative industry and discover how it is shaping a greener, more circular economy.
1. What Is Battery Recycling Technology?
Battery recycling technology refers to advanced processes that recover valuable materials from used batteries, preventing environmental pollution and conserving natural resources. As batteries contain toxic heavy metals (e.g., lead, lithium, cadmium) and reusable components (e.g., cobalt, nickel), recycling mitigates landfill waste and supports a circular economy.
Modern methods include:
- Pyrometallurgy: High-temperature smelting to extract metals.
- Hydrometallurgy: Chemical leaching to separate materials.
- Mechanical Separation: Crushing/sorting batteries into raw components.
This technology is critical for industries like electric vehicles (EVs) and consumer electronics, ensuring sustainable material sourcing.
2. How Is a Battery Recycling System Built?
A battery recycling system integrates specialized machinery and processes to handle diverse battery types (Li-ion, lead-acid, etc.). Key components include:
-
Collection & Sorting
- Automated sensors classify batteries by chemistry/size.
- Manual removal of damaged units for safety.
-
Discharge & Dismantling
- Residual energy is neutralized to prevent fires.
- Robots or shredders break down battery casings.
-
Material Recovery
- Magnetic separators isolate ferrous metals.
- Solvent extraction purifies lithium/cobalt.
-
Purification
- Electrolysis or filtration removes impurities.
These systems prioritize safety (explosion-proof design) and efficiency (AI-driven sorting).
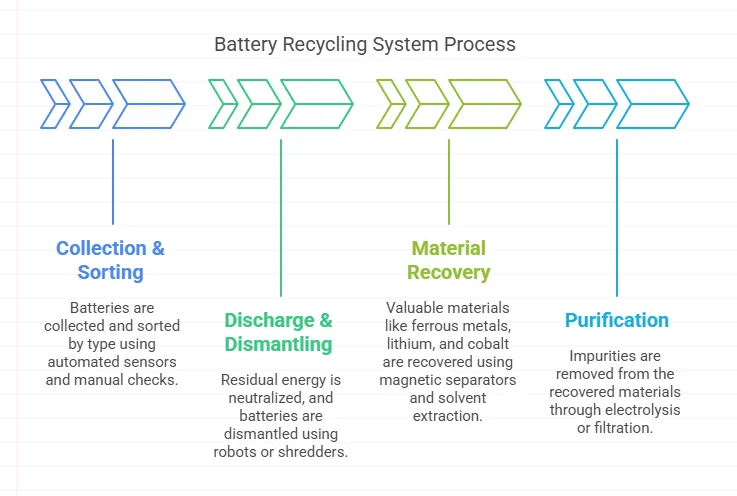
3. Battery Recycling Workflow: Step-by-Step Process
Here’s a detailed breakdown of how batteries are recycled:
Step 1: Collection
- Drop-off centers, retailers, or e-waste programs gather used batteries.
Step 2: Sorting
- Batteries are categorized by:
- Type (Li-ion, Ni-Cd, etc.).
- Condition (intact/damaged).
Step 3: Discharge
- Energy is drained via saltwater baths or resistors.
Step 4: Shredding
- Industrial shredders pulverize batteries into “black mass.”
Step 5: Separation
- Physical: Sieves/magnets split plastics/metals.
- Chemical: Acids dissolve precious metals.
Step 6: Refining
- Recovered materials are processed into industrial-grade compounds.
4. How Do Battery Recycling Machines Work? Technical Principles
Battery recycling machines leverage physics and chemistry to extract materials:
- Shredders & Crushers: Reduce batteries to small pieces for easier processing.
- Pyrolysis Units: Heat organic components (e.g., electrolytes) into inert gas.
- Hydrometallurgical Reactors: Use acids (e.g., sulfuric acid) to dissolve metals.
- Electrorefiners: Apply electric currents to purify metals like copper.
Advanced systems employ:
- AI Vision: Identifies battery chemistries for precise sorting.
- Closed-Loop Systems: Minimize chemical waste via recycling solvents.
5. What Are the Applications of Battery Recycling Technology?
Recycled battery materials are reused in:
- New Batteries: 60–70% of cobalt in EVs comes from recycled sources.
- Electronics: Recovered lithium powers smartphones/laptops.
- Industrial Alloys: Nickel from batteries strengthens stainless steel.
- Renewable Energy Storage: Recycled lead-acid batteries support solar grids.
Emerging uses include 3D-printing powders from recycled metals and graphene production.
6. What Is the Work Environment Like in Battery Recycling Facilities?
Battery recycling facilities are designed to handle hazardous materials safely while maximizing efficiency. Due to the toxic and flammable nature of battery components, these environments require strict controls:
-
Safety Measures:
- Explosion-proof ventilation systems to prevent gas buildup.
- Fire suppression systems (e.g., CO₂ or foam-based) for lithium-ion fires.
- Personal protective equipment (PPE) like chemical-resistant suits and respirators.
-
Operational Zones:
- Sorting Area: Dry, well-lit spaces with automated conveyor belts.
- Processing Area: Sealed chambers for shredding to contain toxic dust.
- Chemical Treatment Labs: Fume hoods and corrosion-resistant equipment.
-
Regulatory Compliance:
- Facilities follow OSHA (U.S.) or EU-REACH standards for worker safety.
- Continuous air/water quality monitoring to prevent environmental leaks.
7. How Is Testing and Quality Control Done in Battery Recycling?
To ensure recovered materials meet industry standards, rigorous testing protocols are applied:
Step-by-Step Quality Control Process:
-
Incoming Inspection:
- X-ray fluorescence (XRF) analyzers verify battery chemistry.
- Capacity testing for reusable batteries.
-
Post-Processing Checks:
- Purity Testing: Spectrometers detect contamination in recovered metals (e.g., <0.5% impurities for cobalt).
- Efficiency Metrics: Track recovery rates (e.g., 95%+ lithium extraction).
-
Final Product Validation:
- Recycled materials are tested against OEM specifications.
- Batch samples sent to third-party labs for ISO certification.
Why It Matters: Poor quality control can lead to battery performance issues or supply chain recalls.
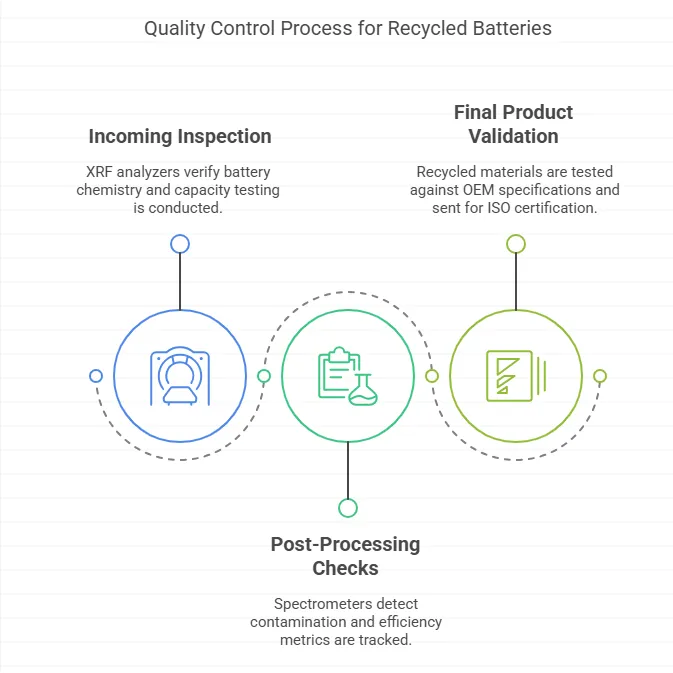
8. What Precautions Are Needed When Using Battery Recycling Equipment?
Handling battery recycling machinery requires strict precautions due to chemical, electrical, and mechanical hazards:
Key Safety Protocols:
-
Pre-Operation:
- Inspect equipment for damage (e.g., frayed wires in shredders).
- Ensure emergency stop buttons are functional.
-
During Operation:
- Never bypass safety interlocks on crushing machines.
- Use insulated tools to prevent short-circuiting live batteries.
-
Post-Operation:
- Decontaminate surfaces with neutralizing agents (e.g., baking soda for acid spills).
- Store processed materials in fireproof containers.
Risks to Avoid:
- Thermal runaway (Li-ion batteries can ignite if crushed incorrectly).
- Exposure to hydrofluoric acid (generated when lithium reacts with water).
9. How to Maintain and Care for Battery Recycling Systems?
Regular maintenance ensures longevity and prevents costly breakdowns:
Routine Tasks (Daily/Weekly):
-
Mechanical Components:
- Lubricate shredder blades to reduce wear.
- Check hydraulic systems for leaks.
-
Chemical Systems:
- Flush pipes in hydrometallurgical units to prevent clogging.
- Replace filters in gas-scrubbing systems.
Scheduled Servicing (Monthly/Annually):
-
Belt and Conveyor Inspection:
- Align misadjusted tracks to prevent jams.
- Replace cracked rollers.
-
Electrical Systems:
- Test ground-fault circuit interrupters (GFCIs).
- Calibrate sensors (e.g., thermal cameras for overheating).
Pro Tip: Use OEM spare parts to avoid compatibility issues with sensitive machinery.
Battery recycling technology is a game-changer in today’s rapidly evolving world. It involves sophisticated methods such as pyrometallurgy, hydrometallurgy, and mechanical separation to extract valuable materials from used batteries, reducing landfill waste and conserving natural resources. Modern recycling systems integrate specialized machinery for collection, sorting, discharge, dismantling, and material recovery, prioritizing safety and efficiency. The applications of recycled materials are vast, including new batteries, electronics, industrial alloys, and renewable energy storage. By supporting a circular economy, battery recycling technology not only mitigates environmental impact but also ensures the sustainable sourcing of critical materials, paving the way for a more sustainable future.