The battery spot welder has become an indispensable tool in modern electronics and battery manufacturing. This specialized device offers a precise and efficient way to join thin metal sheets to battery terminals, ensuring strong, low-resistance connections without damaging sensitive components. Unlike traditional soldering, spot welding uses high-current pulses to create localized, high-quality bonds. From the basics of how it works to the key components that make it effective, this blog will walk you through everything you need to know about battery spot welders. Whether you’re working on a DIY project or scaling up production, understanding this technology is crucial for achieving reliable and high-performance battery packs.
1. What Is a Battery Spot Welder and How Does It Work?
A battery spot welder is a specialized device used to join thin metal sheets, typically nickel strips, to battery terminals. Unlike traditional soldering, which uses heat to melt filler material, spot welding creates a strong bond by applying a high-current pulse for a short duration, melting the metals at the contact point without overheating the battery.
How It Works:
- Electrode Contact – Two copper electrodes press against the nickel strip and battery terminal.
- Current Pulse – A brief (milliseconds) high-current discharge flows through the metals.
- Localized Melting – Heat generated at the contact point fuses the metals.
- Solidification – The metals cool rapidly, forming a secure weld.
This method prevents battery damage (excessive heat degrades lithium-ion cells) and ensures low-resistance connections critical for high-performance battery packs.
2. Inside a Battery Spot Welder: Key Components and Their Functions
A battery spot welder’s efficiency depends on its internal design. Here’s what makes it work:
Key Components:
- Capacitor Bank – Stores and releases high-energy pulses (e.g., 1000+ amps) for welding.
- Control Circuit – Manages pulse duration/current (adjustable for material thickness).
- Copper Electrodes – Conduct current; pointed tips concentrate heat for precise welds.
- Trigger Mechanism – Activates welding (foot pedal or handheld button).
- Power Supply – Charges capacitors (often 12V–24V input).
Why These Matter: Poorly sized capacitors or corroded electrodes lead to weak welds. For example, lithium battery packs require <10ms pulses to avoid thermal damage—a feature ensured by the control board.
3. Why Nickel Strips Are Commonly Used in Battery Spot Welding
Nickel strips dominate battery welding due to their material properties:
Advantages of Nickel:
- Low Resistance – Minimizes energy loss in high-current applications (e.g., EV batteries).
- Oxidation Resistance – Unlike copper, nickel doesn’t corrode quickly, ensuring stable connections.
- Ductility – Easy to bend without cracking, ideal for flexible pack designs.
Note: Pure nickel (Ni200) is preferred over nickel-plated steel for critical applications, as steel’s higher resistance can generate excess heat.
4. Spot Welding in Portable Electronics: Phones, Power Banks, and More
From smartphones to medical devices, spot welding ensures reliable battery connections.
Step-by-Step Application in Electronics:
- Cell Arrangement – Align lithium-ion cells in series/parallel configurations.
- Nickel Strip Placement – Position strips over terminals (anode/cathode).
- Welding – Use micro-spot welders (↓5ms pulses) to attach strips.
- Testing – Check weld strength and electrical continuity.
Why Spot Welding?
- Precision: Avoids solder spills that could short-circuit tiny PCBs.
- Safety: No flux/lead fumes, critical for sealed devices like wireless earbuds.
Example: Power bank manufacturers use automated spot welders to assemble thousands of 18650 cells daily with consistent quality.
5. What Are the Key Safety Considerations in the Spot Welding Work Area?
Spot welding involves high currents and heat, so proper safety measures are critical to prevent accidents.
Essential Safety Practices:
- Electrical Safety – Ensure proper grounding of the welder to avoid shocks.
- Fire Prevention – Keep flammable materials away; have a Class D fire extinguisher (for metal fires) nearby.
- Ventilation – Work in a well-ventilated area to avoid inhaling fumes from heated metals.
-
Personal Protective Equipment (PPE) – Wear:
- Heat-resistant gloves
- Safety goggles (sparks can fly)
- Non-conductive footwear
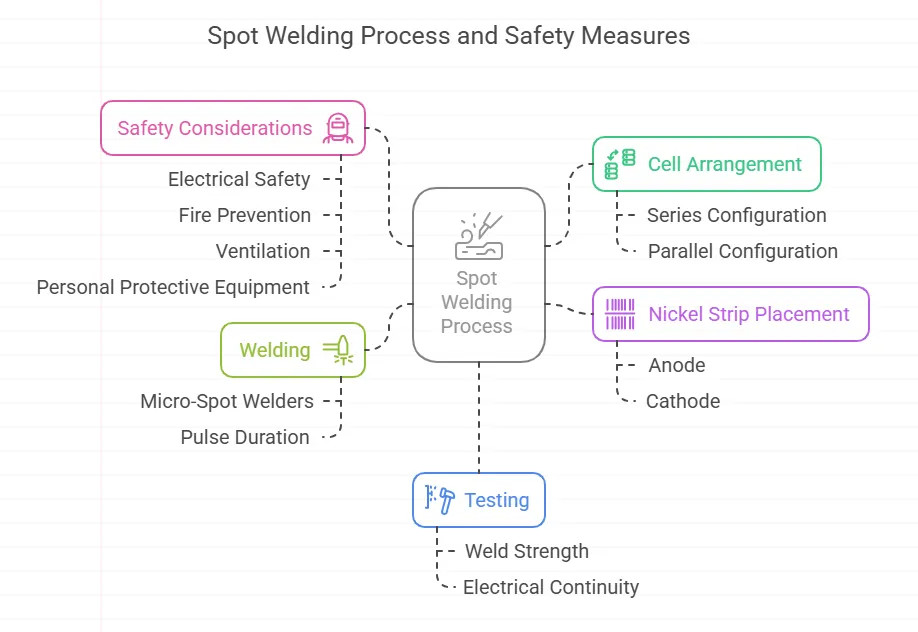
Why It Matters: Lithium batteries can ignite if overheated, and high-current welding poses electrical hazards. A controlled workspace minimizes risks.
6. How to Test Spot Weld Strength in Battery Pack Production
Weak welds lead to high resistance, overheating, or battery failure. Here’s how manufacturers ensure quality.
Step-by-Step Weld Testing:
- Visual Inspection – Check for consistent, round weld marks (no cracks or discoloration).
- Peel Test – Grip the nickel strip with pliers and peel it back. A good weld should tear the metal, not detach cleanly.
- Pull Test – Use a force gauge to measure resistance (≥50N is typical for 0.15mm nickel strips).
- Microscopic Analysis (Optional) – Inspect cross-sections for proper fusion depth (common in EV battery QC).
Why Testing Matters: Weak welds increase resistance, causing energy loss and potential thermal runaway in high-power applications.
7. What Are the Critical Safety Precautions When Operating a Battery Spot Welder?
Improper use of a spot welder can damage batteries or cause injuries. Follow these precautions:
Key Safety Steps:
-
Pre-Welding Checks:
- Verify electrode alignment (misaligned tips cause weak welds).
- Ensure capacitors are fully charged for consistent power output.
-
During Welding:
- Never touch electrodes while firing (risk of burns or shock).
- Avoid welding near battery vents (heat can trigger leaks).
-
Post-Welding:
- Let the welder cool between cycles to prevent overheating.
- Inspect welds before handling the battery pack.
Critical Note: Lithium-ion cells should never exceed 80°C during welding—infrared thermometers help monitor temperature.
8. Regular Maintenance Checklist for Battery Spot Welders
A well-maintained spot welder ensures consistent performance and longevity.
Maintenance Tasks (Weekly/Monthly):
-
Electrode Care:
- Clean oxidation off copper tips with a wire brush.
- Replace worn or pitted electrodes (poor contact weakens welds).
-
Capacitor Check:
- Test for proper charge/discharge cycles (weak capacitors reduce weld power).
-
Cable & Connection Inspection:
- Tighten loose terminals to prevent resistance buildup.
- Check for frayed wires or insulation damage.
-
Lubrication (If Applicable):
- Apply dielectric grease to moving parts (e.g., foot pedal hinges).
Why Maintenance Matters: Dirty electrodes or degraded capacitors lead to inconsistent welds, increasing failure rates in production.
This detailed guide provides an in-depth look at the battery spot welder, a critical tool for creating robust battery connections. We start by explaining its working principle, which involves using high-current pulses to melt and fuse metals at the contact point, ensuring a strong bond without overheating the battery. We then explore the key components, such as the capacitor bank, control circuit, and copper electrodes, that make spot welding precise and efficient. The blog also highlights the advantages of using nickel strips for their low resistance and durability. Practical applications in portable electronics are discussed, emphasizing the precision and safety benefits of spot welding over traditional soldering. Safety considerations and maintenance tips are covered to ensure users can operate these tools effectively and safely. Whether you’re a hobbyist or a professional, this guide offers valuable insights into maximizing the potential of battery spot welders.