Cell manufacturing is revolutionizing modern production by organizing workflows into efficient, self-contained units. This strategy not only streamlines processes but also enhances flexibility and productivity. Explore how cell manufacturing is transforming industries and driving innovation in this in-depth guide.
What is Cell Manufacturing?
Cell manufacturing is a production strategy that organizes the manufacturing process into small, self-contained units known as “cells.” Each cell is designed to handle a specific set of tasks or produce a particular product or component. This approach is often used in industries such as automotive, electronics, and aerospace, where efficiency and flexibility are critical. The primary goal of cell manufacturing is to streamline production, reduce waste, and improve overall productivity by minimizing the movement of materials and workers between different stages of production.
The Cell Manufacturing Process: Step-by-Step Breakdown
- Design the Cell Layout: The first step in cell manufacturing is to design the layout of the cell. This involves determining the optimal arrangement of machines, workstations, and equipment to ensure a smooth flow of materials and minimize unnecessary movement.
- Assign Tasks to the Cell: Once the layout is finalized, specific tasks are assigned to the cell. These tasks are typically related to a particular product or component, and the cell is designed to handle all the necessary operations from start to finish.
- Train the Workforce: Employees working within the cell must be trained to perform multiple tasks. This cross-training ensures that the cell can operate efficiently, even if one worker is absent or if there is a sudden change in production requirements.
- Implement Lean Manufacturing Principles: Cell manufacturing often incorporates lean manufacturing principles, such as just-in-time production and continuous improvement. These principles help to reduce waste, improve quality, and increase efficiency.
- Monitor and Optimize: Once the cell is operational, it is essential to continuously monitor its performance. This involves tracking key metrics such as production speed, quality, and downtime. Based on this data, adjustments can be made to further optimize the cell’s performance.
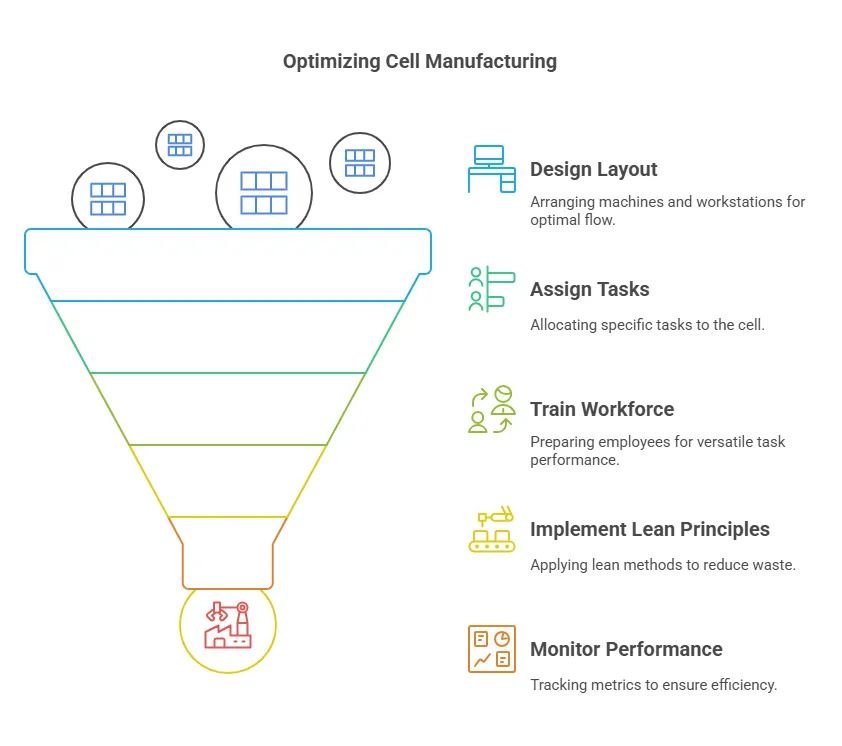
How Does a Cell Manufacturing Line Work?
A cell manufacturing line works by grouping together all the necessary equipment and personnel required to produce a specific product or component. The line is designed to allow for a continuous flow of materials, with each workstation or machine performing a specific task in the production process. The key to a successful cell manufacturing line is its ability to operate independently, with minimal reliance on other parts of the factory. This independence allows for greater flexibility and faster response times to changes in demand or production requirements.
Key Components of a Cell Manufacturing System
- Workstations: These are the individual stations within the cell where specific tasks are performed. Each workstation is equipped with the necessary tools and machinery to complete its assigned tasks.
- Material Handling Equipment: Efficient material handling is crucial in cell manufacturing. This includes conveyors, forklifts, and automated guided vehicles (AGVs) that move materials between workstations.
- Control Systems: Advanced control systems, such as programmable logic controllers (PLCs) and computer numerical control (CNC) machines, are used to automate and monitor the production process within the cell.
- Quality Control Stations: Quality control is an integral part of cell manufacturing. Each cell typically includes a station where products are inspected and tested to ensure they meet the required standards.
- Human Resources: Skilled workers are essential for the success of a cell manufacturing system. These workers must be trained to perform multiple tasks and work collaboratively within the cell.
Working Principles of Cell Manufacturing Machines
Cell manufacturing machines are designed to operate efficiently within the confined space of a cell. They are typically compact, versatile, and capable of performing multiple tasks. The working principles of these machines include:
- Modularity: Machines used in cell manufacturing are often modular, allowing them to be easily reconfigured or replaced as production needs change.
- Automation: Many cell manufacturing machines are automated, reducing the need for manual intervention and increasing production speed and consistency.
- Integration: Machines within a cell are designed to work seamlessly together, with minimal downtime between operations. This integration is often achieved through the use of advanced control systems and communication protocols.
- Flexibility: Cell manufacturing machines are designed to be flexible, allowing them to handle a variety of tasks and adapt to changes in production requirements. This flexibility is crucial for maintaining efficiency in a dynamic manufacturing environment.
By understanding these key aspects of cell manufacturing, businesses can better appreciate the benefits of this production strategy and implement it effectively in their operations.
Applications of Cell Manufacturing in Various Industries
Cell manufacturing is a versatile production strategy that has found applications across a wide range of industries. Here are some key examples:
- Automotive Industry: In the automotive sector, cell manufacturing is used to produce components such as engines, transmissions, and body panels. The flexibility of cell manufacturing allows automakers to quickly adapt to changes in demand or design specifications.
- Electronics Industry: Cell manufacturing is widely used in the production of electronic components, such as circuit boards and semiconductors. The precision and efficiency of cell manufacturing are particularly well-suited to the high-tech requirements of this industry.
- Aerospace Industry: The aerospace industry relies on cell manufacturing for the production of complex components, such as turbine blades and fuselage sections. The ability to maintain high quality and precision is critical in this sector.
- Medical Device Industry: Cell manufacturing is used to produce medical devices, such as surgical instruments and diagnostic equipment. The stringent quality control requirements of the medical industry make cell manufacturing an ideal choice.
- Consumer Goods Industry: From household appliances to sporting goods, cell manufacturing is used to produce a wide variety of consumer products. The efficiency and flexibility of cell manufacturing help manufacturers meet the diverse needs of consumers.
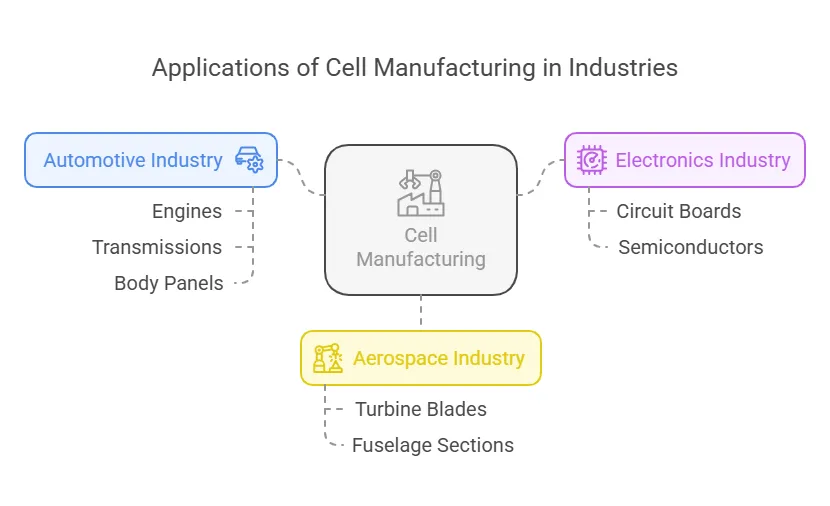
Exploring the Work Environment in a Cell Manufacturing Facility
The work environment in a cell manufacturing facility is designed to maximize efficiency and productivity. Here are some key features:
- Ergonomic Workstations: Workstations within a cell are designed to be ergonomic, reducing the risk of injury and increasing worker comfort. This includes adjustable chairs, workbenches, and tools.
- Clean and Organized Layout: The layout of a cell manufacturing facility is clean and organized, with a clear flow of materials and minimal clutter. This helps to reduce the risk of accidents and improve efficiency.
- Collaborative Atmosphere: Workers in a cell manufacturing facility often work in teams, fostering a collaborative atmosphere. This teamwork is essential for the smooth operation of the cell.
- Safety Measures: Safety is a top priority in cell manufacturing facilities. This includes the use of protective equipment, safety training, and regular safety audits.
- Continuous Improvement Culture: Cell manufacturing facilities often have a culture of continuous improvement, where workers are encouraged to suggest and implement changes that can improve efficiency and quality.
Cell Manufacturing Quality Control: Methods and Standards
Quality control is a critical aspect of cell manufacturing. Here are some methods and standards commonly used:
- In-Process Inspections: Regular inspections are conducted during the production process to identify and correct defects early. This helps to ensure that the final product meets quality standards.
- Statistical Process Control (SPC): SPC is a method of using statistical techniques to monitor and control the production process. This helps to identify trends and variations that could affect quality.
- Standard Operating Procedures (SOPs): SOPs are detailed, written instructions that outline the steps required to perform a task. These procedures help to ensure consistency and quality in the production process.
- Quality Management Systems (QMS): Many cell manufacturing facilities implement a QMS, such as ISO 9001, to ensure that quality control processes are standardized and consistently applied.
- Employee Training: Workers are trained in quality control methods and standards to ensure that they understand the importance of quality and how to achieve it.
Product Testing in Cell Manufacturing: Techniques and Best Practices
Product testing is an essential part of cell manufacturing to ensure that products meet the required specifications and standards. Here are some techniques and best practices:
- Functional Testing: This involves testing the product to ensure that it performs its intended function correctly. For example, a circuit board might be tested to ensure that all connections are working properly.
- Durability Testing: Products are subjected to stress tests to determine their durability and lifespan. This might include exposure to extreme temperatures, humidity, or mechanical stress.
- Compliance Testing: Products are tested to ensure that they comply with industry standards and regulations. This might include safety standards, environmental regulations, or performance criteria.
- User Testing: In some cases, products are tested by end-users to gather feedback on their performance and usability. This can help to identify any issues that were not detected during earlier testing stages.
- Automated Testing: Automated testing systems are often used in cell manufacturing to increase the speed and accuracy of testing. These systems can perform a wide range of tests quickly and consistently.
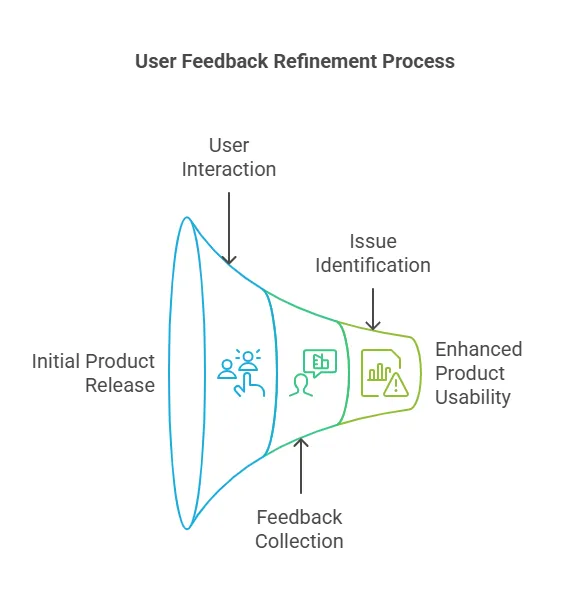
Common Challenges in Cell Manufacturing and How to Overcome Them
While cell manufacturing offers many benefits, it also comes with its own set of challenges. Here are some common challenges and how to overcome them:
- High Initial Investment: Setting up a cell manufacturing system can require a significant initial investment in equipment and training. To overcome this, companies can start with a pilot cell and gradually expand as they see the benefits.
- Complexity of Implementation: Implementing cell manufacturing can be complex, especially in facilities that are used to traditional production methods. Detailed planning and phased implementation can help to manage this complexity.
- Workforce Resistance: Workers may be resistant to the changes required by cell manufacturing, such as cross-training and new work processes. Clear communication and involving workers in the planning process can help to overcome this resistance.
- Maintaining Flexibility: While cell manufacturing is designed to be flexible, maintaining this flexibility can be challenging, especially as production requirements change. Regular reviews and adjustments to the cell layout and processes can help to maintain flexibility.
- Quality Control: Ensuring consistent quality in a cell manufacturing environment can be challenging. Implementing robust quality control methods and continuous improvement practices can help to maintain high standards.
By addressing these challenges and leveraging the strengths of cell manufacturing, companies can achieve greater efficiency, flexibility, and quality in their production processes.
Precautions in Cell Manufacturing: Ensuring Safety and Quality
Cell manufacturing requires strict adherence to safety and quality protocols to ensure both worker safety and product reliability. Here are some key precautions:
- Personal Protective Equipment (PPE): Workers must wear appropriate PPE, such as gloves, safety glasses, and helmets, to protect against potential hazards like chemical exposure or machinery accidents.
- Regular Safety Audits: Conducting frequent safety audits helps identify and mitigate risks in the manufacturing environment. This includes checking equipment, workflows, and emergency response systems.
- Proper Training: Employees should be thoroughly trained in operating machinery, handling materials, and following safety procedures. This reduces the likelihood of accidents and errors.
- Material Handling Protocols: Proper storage and handling of raw materials and finished products are essential to prevent contamination or damage. This includes using designated storage areas and following handling guidelines.
- Quality Checks at Every Stage: Implementing in-process quality checks ensures that defects are caught early, reducing waste and maintaining high product standards.
Maintenance and Care of Cell Manufacturing Equipment
Proper maintenance of cell manufacturing equipment is critical to ensure longevity, efficiency, and safety. Here’s how to maintain and care for these systems:
- Routine Inspections: Regularly inspect equipment for wear and tear, loose components, or signs of malfunction. This helps identify issues before they escalate.
- Scheduled Servicing: Follow the manufacturer’s recommended maintenance schedule for each piece of equipment. This includes lubrication, calibration, and replacement of worn parts.
- Cleaning Protocols: Keep equipment clean and free of debris to prevent malfunctions and contamination. Use appropriate cleaning agents and methods for different machinery.
- Training for Maintenance Staff: Ensure that maintenance personnel are well-trained and equipped to handle repairs and servicing. This minimizes downtime and extends equipment life.
- Documentation: Maintain detailed records of maintenance activities, including dates, issues addressed, and parts replaced. This helps track equipment performance and plan future maintenance.
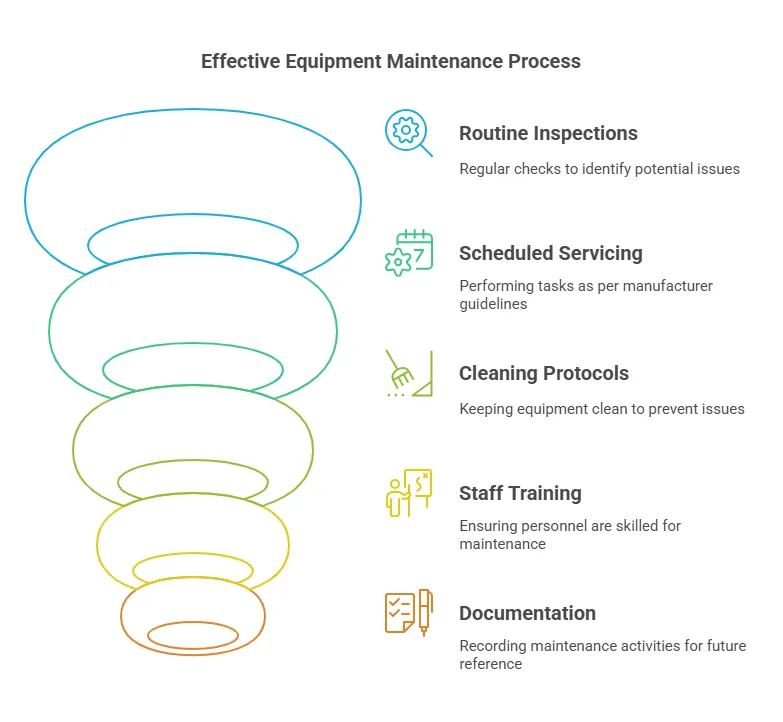
Innovations in Cell Manufacturing Technology
Cell manufacturing is evolving rapidly, driven by technological advancements. Here are some notable innovations:
- Advanced Robotics: Robots are increasingly used in cell manufacturing for tasks like assembly, welding, and material handling. They improve precision, speed, and consistency.
- Internet of Things (IoT): IoT-enabled devices collect and analyze real-time data from manufacturing equipment, enabling predictive maintenance and process optimization.
- Artificial Intelligence (AI): AI algorithms are used to optimize production schedules, predict equipment failures, and enhance quality control processes.
- Additive Manufacturing (3D Printing): 3D printing is being integrated into cell manufacturing for rapid prototyping and the production of complex components.
- Augmented Reality (AR): AR tools assist workers in assembly and maintenance tasks by providing real-time visual guidance and instructions.
How Automation is Transforming Cell Manufacturing
Automation is revolutionizing cell manufacturing by enhancing efficiency, reducing costs, and improving product quality. Here’s how:
- Increased Productivity: Automated systems can operate 24/7 without fatigue, significantly increasing output and reducing production time.
- Consistency and Precision: Automation ensures that each product is manufactured to the same high standard, minimizing human error and variability.
- Cost Savings: While the initial investment in automation can be high, the long-term savings in labor costs and reduced waste make it a cost-effective solution.
- Flexibility: Automated systems can be reprogrammed to handle different tasks, making it easier to adapt to changing production needs.
- Enhanced Safety: Automation reduces the need for workers to perform dangerous tasks, lowering the risk of workplace injuries.
Future Trends in Cell Manufacturing: What’s Next?
The future of cell manufacturing is shaped by emerging technologies and evolving industry demands. Here are some trends to watch:
- Smart Factories: The integration of AI, IoT, and big data analytics will lead to fully connected smart factories, where machines communicate and optimize production autonomously.
- Sustainable Manufacturing: There will be a greater focus on reducing waste, energy consumption, and carbon emissions through eco-friendly materials and processes.
- Customization at Scale: Advances in automation and additive manufacturing will enable mass customization, allowing manufacturers to produce personalized products efficiently.
- Human-Machine Collaboration: Collaborative robots (cobots) will work alongside humans, combining the strengths of both to improve productivity and innovation.
- Digital Twins: The use of digital twins—virtual replicas of physical systems—will become more widespread, enabling real-time monitoring and simulation of manufacturing processes.
By staying ahead of these trends and adopting innovative practices, manufacturers can ensure they remain competitive in the rapidly evolving landscape of cell manufacturing.
Cell manufacturing organizes production into self-contained units called “cells,” each designed to handle specific tasks or products. This approach minimizes material movement, reduces waste, and improves productivity. Key components include ergonomic workstations, advanced control systems, and quality control stations. Industries like automotive, electronics, and aerospace benefit from its flexibility and precision. Challenges such as high initial investment and workforce resistance can be overcome through phased implementation and training. Innovations like robotics, IoT, and AI are driving the future of cell manufacturing towards smart factories and sustainable production.