What is a Battery Manufacturing Machine?
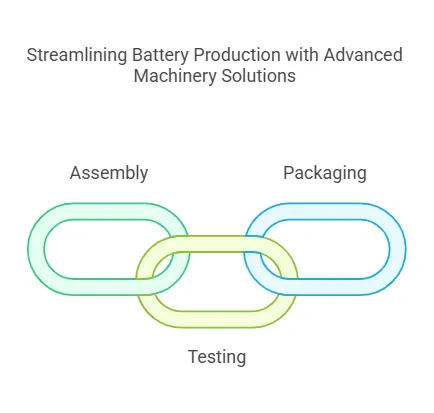
A battery manufacturing machine refers to a range of specialized equipment designed to produce batteries efficiently and precisely. These machines are integral to the battery production process, enabling the creation of various battery types, such as lithium-ion, lead-acid, and nickel-metal hydride batteries. The equipment includes:
- Assembly Machines: Used to assemble battery components like electrodes, separators, and casings.
- Testing Machines: Ensure the quality and performance of batteries by conducting capacity, voltage, and safety tests.
- Packaging Machines: Prepare finished batteries for distribution by labeling, sealing, and packaging them securely.
These machines are essential for meeting the growing demand for batteries in industries like electric vehicles, consumer electronics, and renewable energy storage.
What is the Product Structure and Workflow of Battery Manufacturing Machines?
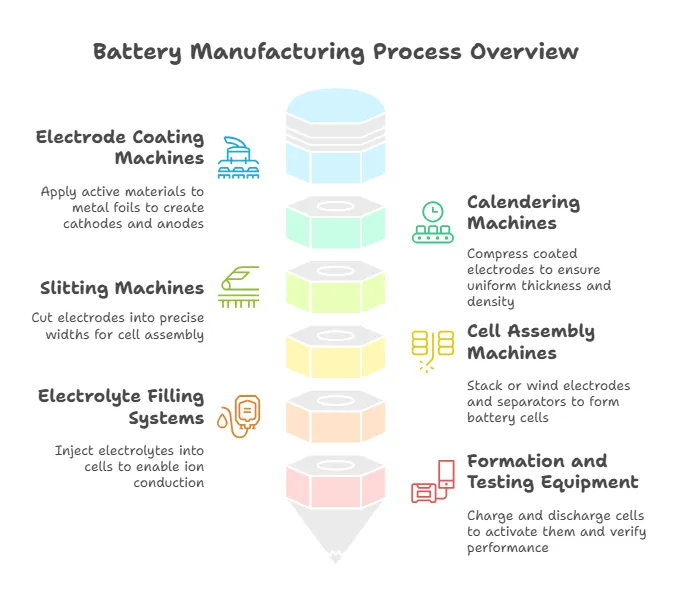
Battery manufacturing machines are complex systems composed of several key components that work together seamlessly. Here’s a breakdown of their structure and workflow:
Key Components:
- Electrode Coating Machines: Apply active materials to metal foils to create cathodes and anodes.
- Calendering Machines: Compress coated electrodes to ensure uniform thickness and density.
- Slitting Machines: Cut electrodes into precise widths for cell assembly.
- Cell Assembly Machines: Stack or wind electrodes and separators to form battery cells.
- Electrolyte Filling Systems: Inject electrolytes into cells to enable ion conduction.
- Formation and Testing Equipment: Charge and discharge cells to activate them and verify performance.
Workflow:
- Raw Material Preparation: Electrode materials are mixed, coated, and dried.
- Electrode Production: Coated foils are calendered and slit into desired dimensions.
- Cell Assembly: Electrodes, separators, and casings are assembled into cells.
- Electrolyte Filling: Cells are filled with electrolytes in a controlled environment.
- Sealing and Formation: Cells are sealed and undergo initial charging cycles.
- Testing and Packaging: Finished batteries are tested for quality and packaged for shipment.
This structured workflow ensures high precision and consistency in battery production.
How Do Battery Manufacturing Machines Work?
Battery manufacturing machines operate through a series of carefully coordinated steps, leveraging advanced technologies to ensure efficiency and accuracy. Here’s a step-by-step explanation of their working principle:
-
Electrode Preparation:
- Active materials are mixed with binders and solvents to form a slurry.
- The slurry is coated onto metal foils (copper for anodes, aluminum for cathodes).
- Coated foils are dried and compressed to achieve the desired thickness.
-
Cell Assembly:
- Electrodes and separators are stacked or wound into a jellyroll structure.
- The assembly is placed into a casing (cylindrical, prismatic, or pouch).
-
Electrolyte Filling:
- Electrolytes are injected into the casing under vacuum conditions to ensure proper saturation.
-
Sealing:
- The cell is sealed to prevent leakage and contamination.
-
Formation:
- The cell undergoes initial charge and discharge cycles to stabilize its electrochemical properties.
-
Testing:
- Automated testing systems evaluate capacity, voltage, and safety parameters.
Advanced technologies like robotics, AI, and IoT are often integrated into these machines to enhance precision, reduce waste, and improve production speed.
What is the Product Application Scope of Battery Manufacturing Machines?
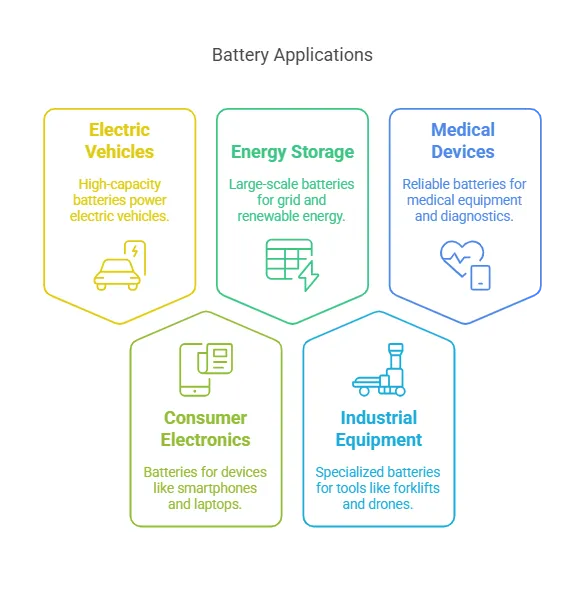
Battery manufacturing machines play a critical role in producing batteries for a wide range of industries. Here are some key applications:
-
Electric Vehicles (EVs):
High-capacity lithium-ion batteries are essential for powering EVs, and manufacturing machines ensure their mass production with consistent quality. -
Consumer Electronics:
Batteries for smartphones, laptops, and wearable devices are produced using compact and efficient manufacturing equipment. -
Energy Storage Systems:
Large-scale batteries for grid storage and renewable energy integration rely on advanced manufacturing machines for production. -
Industrial Equipment:
Batteries used in forklifts, drones, and other industrial tools are manufactured using specialized equipment. -
Medical Devices:
Reliable batteries for medical equipment like pacemakers and portable diagnostic devices are produced in controlled environments.
These applications highlight the versatility and importance of battery manufacturing machines in modern technology.
What is the Ideal Work Environment for Battery Manufacturing Machines?
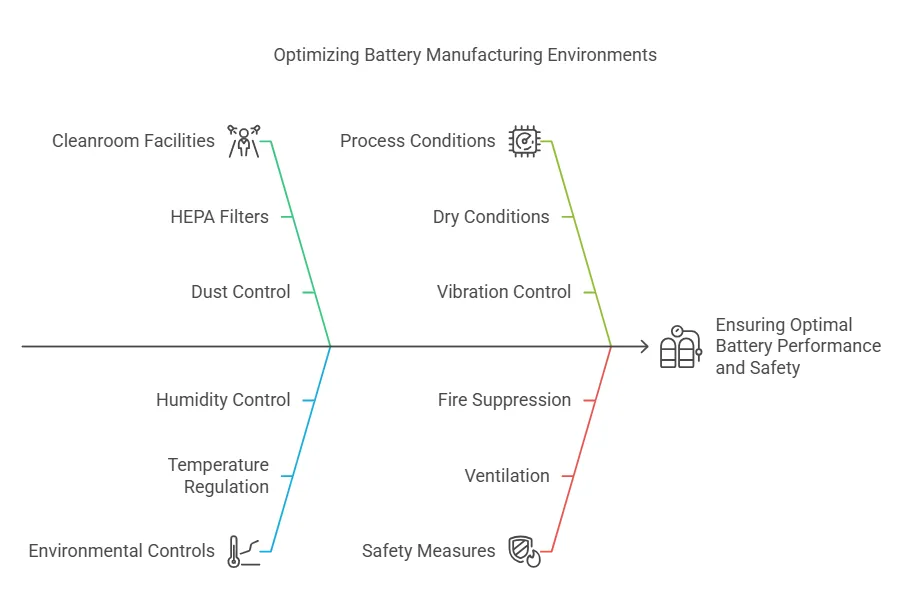
To ensure optimal performance and product quality, battery manufacturing machines require a carefully controlled work environment. Key factors include:
-
Cleanroom Facilities:
Dust and particulate contamination can compromise battery performance, so cleanrooms with HEPA filters are essential. -
Temperature and Humidity Control:
Maintaining stable temperature (typically 20-25°C) and humidity levels (below 1% relative humidity for some processes) prevents material degradation and ensures consistency. -
Dry Rooms:
Certain processes, like electrolyte filling, require ultra-dry conditions to avoid moisture-induced reactions. -
Vibration and Noise Control:
Minimizing vibrations and noise ensures precision in assembly and testing processes. -
Safety Measures:
Proper ventilation, fire suppression systems, and explosion-proof equipment are critical due to the flammable nature of battery materials.
By maintaining these environmental conditions, manufacturers can maximize the efficiency and longevity of their battery production equipment.
What is Product Testing and Quality Control in Battery Manufacturing?
Product testing and quality control are critical stages in battery manufacturing to ensure safety, reliability, and performance. Battery manufacturing machines are equipped with advanced testing systems to conduct a variety of assessments:
Key Tests in Battery Manufacturing:
-
Performance Testing:
- Capacity Testing: Measures the energy storage capacity of the battery.
- Cycle Life Testing: Evaluates how many charge-discharge cycles a battery can endure before performance degrades.
- Internal Resistance Testing: Checks the resistance within the battery, which affects efficiency and heat generation.
-
Safety Testing:
- Overcharge and Over-Discharge Tests: Ensures the battery can handle extreme conditions without failure.
- Short Circuit Testing: Verifies the battery’s response to short circuits, ensuring it doesn’t overheat or explode.
- Crush and Impact Tests: Assesses the battery’s durability under physical stress.
-
Reliability Testing:
- Temperature Tolerance Testing: Exposes batteries to extreme temperatures to evaluate performance under harsh conditions.
- Vibration and Shock Testing: Simulates real-world conditions to ensure the battery can withstand transportation and usage stresses.
How Machines Ensure Quality:
- Automated testing systems integrated into manufacturing machines provide real-time data and feedback.
- AI-driven algorithms detect defects early in the production process, reducing waste and improving yield.
- Consistent monitoring ensures every battery meets industry standards and customer expectations.
Rigorous testing and quality control are essential to producing batteries that are safe, reliable, and high-performing.
What are the Usage Precautions for Battery Manufacturing Machines?
Operating battery manufacturing machines requires strict adherence to safety protocols to prevent accidents and ensure smooth production. Here are key precautions:
Handling Hazardous Materials:
- Wear appropriate personal protective equipment (PPE), such as gloves, goggles, and lab coats, when handling electrolytes and other chemicals.
- Store flammable materials in designated, well-ventilated areas away from heat sources.
Operating Machinery Safely:
- Ensure all operators are trained in machine operation and emergency procedures.
- Follow the manufacturer’s guidelines for machine setup, operation, and shutdown.
- Use safety interlocks and emergency stop buttons to prevent accidents.
Minimizing Contamination:
- Maintain cleanroom standards to prevent dust and particulate contamination.
- Regularly clean and inspect machines to avoid material buildup or corrosion.
Preventing Malfunctions:
- Conduct regular inspections to identify and address wear and tear.
- Avoid overloading machines beyond their specified capacity.
By following these precautions, manufacturers can ensure a safe and efficient production environment.
How to Maintain and Care for Battery Manufacturing Machines?
Proper maintenance is essential to keep battery manufacturing machines running efficiently and extend their lifespan. Here are some maintenance tips:
Regular Servicing:
- Schedule routine inspections by qualified technicians to identify potential issues early.
- Replace worn-out parts, such as belts, bearings, and seals, to prevent breakdowns.
Cleaning:
- Clean machines regularly to remove dust, debris, and chemical residues.
- Use approved cleaning agents to avoid damaging sensitive components.
Calibration:
- Calibrate sensors, actuators, and testing equipment periodically to ensure accuracy.
- Verify alignment of mechanical components to maintain precision in production.
Troubleshooting:
- Train operators to recognize common issues, such as abnormal noises or performance drops.
- Keep a log of maintenance activities and repairs for future reference.
By implementing these practices, manufacturers can minimize downtime and maximize productivity.
How to Choose the Right Battery Manufacturing Machine for Your Business?
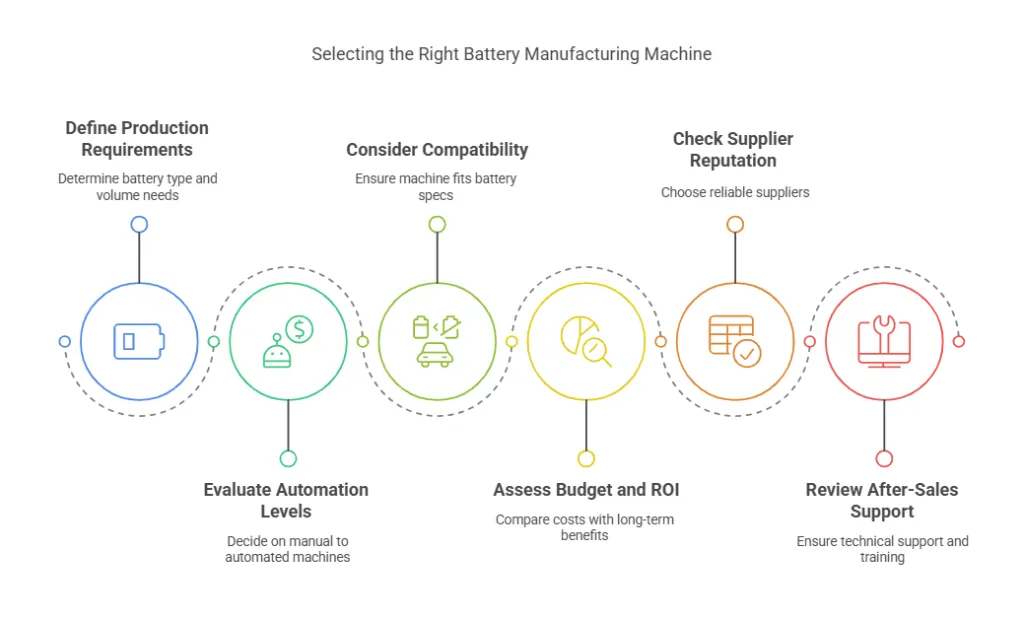
Selecting the right battery manufacturing machine depends on several factors tailored to your business needs. Here’s a step-by-step guide:
-
Define Your Production Requirements:
- Determine the type of batteries you plan to produce (e.g., lithium-ion, lead-acid).
- Estimate your production volume and scalability needs.
-
Evaluate Automation Levels:
- Decide between manual, semi-automated, or fully automated machines based on your budget and labor availability.
-
Consider Compatibility:
- Ensure the machine is compatible with your battery chemistry and design specifications.
-
Assess Budget and ROI:
- Compare the initial investment with long-term benefits, such as increased efficiency and reduced labor costs.
-
Check Supplier Reputation:
- Choose a reputable supplier with a track record of delivering reliable and high-quality equipment.
-
Review After-Sales Support:
- Ensure the supplier offers technical support, training, and spare parts availability.
By carefully evaluating these factors, you can select a machine that meets your production goals and budget.
What are the Future Trends in Battery Manufacturing Machines?
The battery manufacturing industry is evolving rapidly, driven by technological advancements and growing demand for sustainable energy solutions. Here are some key trends:
-
Automation and Robotics:
- Increased use of robotics for tasks like electrode stacking, cell assembly, and packaging to improve precision and reduce labor costs.
-
AI-Driven Quality Control:
- AI algorithms analyze production data in real-time to detect defects, optimize processes, and predict maintenance needs.
-
Advanced Battery Chemistries:
- Development of solid-state batteries and other next-generation chemistries requires specialized manufacturing equipment.
-
Sustainable Manufacturing Practices:
- Adoption of energy-efficient machines and recycling systems to minimize environmental impact.
-
Modular and Scalable Systems:
- Flexible manufacturing systems that can be easily upgraded or reconfigured for different battery types and production volumes.
-
Integration with IoT:
- Smart machines connected to the Internet of Things (IoT) enable remote monitoring, data analytics, and predictive maintenance.
These trends are shaping the future of battery manufacturing, making it more efficient, sustainable, and adaptable to emerging technologies.