In today’s fast-paced world of energy storage and electrification, the cylindrical battery pack machine stands out as a critical enabler of innovation and efficiency. This specialized equipment is designed to automate the assembly of cylindrical battery cells into high-performance battery packs, ensuring precision, consistency, and safety in every step of the process. From electric vehicles and consumer electronics to renewable energy storage systems, the applications of these machines are vast and impactful. In this blog, we will explore the inner workings of the cylindrical battery pack machine, its key components, and how it revolutionizes battery production. We’ll also delve into the importance of maintaining optimal working conditions, implementing rigorous quality testing, and following essential safety precautions. Join us as we uncover the role of this remarkable machine in shaping the future of energy storage.
What is a Cylindrical Battery Pack Machine?
A cylindrical battery pack machine is a specialized piece of equipment designed for the automated assembly of cylindrical battery cells into battery packs. These machines are essential in the production of batteries used in various applications, including electric vehicles, consumer electronics, and renewable energy storage systems. The machine ensures precision, efficiency, and consistency in the assembly process, which is critical for the performance and safety of the final battery pack.
Structure and Components of a Cylindrical Battery Pack Machine
The cylindrical battery pack machine is composed of several key components that work together to achieve seamless assembly:
- Feeding System: This system is responsible for supplying cylindrical battery cells to the assembly line. It ensures a continuous and consistent flow of cells.
- Sorting and Orientation Unit: This unit sorts the cells and orients them correctly for the next stages of assembly.
- Welding Module: This module connects the cells using techniques such as laser welding or ultrasonic welding, ensuring strong and reliable connections.
- Testing and Inspection Unit: This unit performs various tests, including voltage, resistance, and capacity checks, to ensure each cell meets the required specifications.
- Packaging System: This system assembles the cells into the final battery pack, often including thermal management components and protective casing.
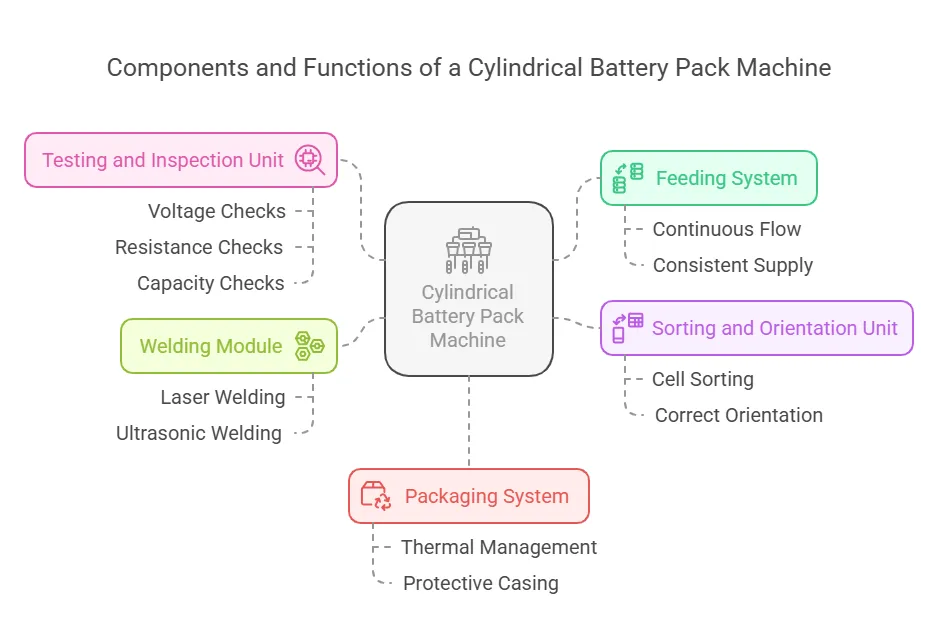
How Does a Cylindrical Battery Pack Machine Work?
The operation of a cylindrical battery pack machine can be broken down into several steps:
- Cell Feeding: The machine starts by feeding cylindrical cells into the assembly line. This is typically done using a conveyor belt or robotic arm.
- Sorting and Orientation: The cells are then sorted and oriented correctly. This step is crucial for ensuring that all cells are aligned properly for welding.
- Welding: The cells are welded together using advanced welding techniques. This step ensures that the electrical connections between cells are strong and reliable.
- Testing and Inspection: After welding, the cells undergo rigorous testing to ensure they meet the required specifications. Any defective cells are removed from the line.
- Packaging: Finally, the cells are assembled into the final battery pack, which may include additional components such as thermal management systems and protective casing.
Applications of Cylindrical Battery Pack Machines in Industries
Cylindrical battery pack machines are used in a variety of industries, including:
- Electric Vehicles (EVs): These machines are crucial for the production of battery packs used in electric cars, buses, and bikes.
- Consumer Electronics: They are used to assemble battery packs for devices such as laptops, smartphones, and power tools.
- Renewable Energy Storage: Cylindrical battery pack machines are also used in the production of batteries for solar and wind energy storage systems.
- Industrial Equipment: They are used in the assembly of batteries for industrial machinery and equipment.
Key Features and Benefits of Cylindrical Battery Pack Machines
Cylindrical battery pack machines offer several key features and benefits:
- High Precision: These machines ensure precise assembly, which is critical for the performance and safety of the battery pack.
- Efficiency: Automated assembly lines significantly reduce production time and labor costs.
- Consistency: The machines ensure consistent quality across all battery packs, reducing the risk of defects.
- Flexibility: Many machines are designed to handle different types and sizes of cylindrical cells, making them versatile for various applications.
- Safety: Advanced safety features, such as automated testing and inspection, help prevent defects and ensure the safety of the final product.
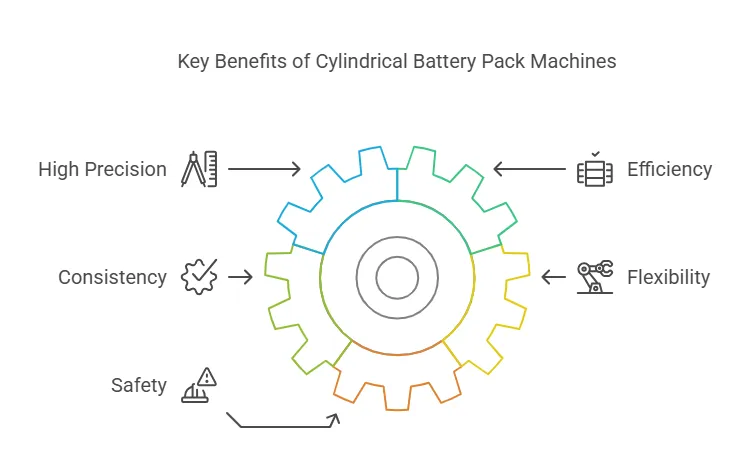
By understanding the structure, operation, and benefits of cylindrical battery pack machines, industries can make informed decisions about their battery production processes, ultimately leading to higher quality and more efficient battery packs.
What Are the Working Environment and Conditions for Cylindrical Battery Pack Machines?
Cylindrical battery pack machines operate in highly controlled environments to ensure optimal performance and product quality. Here are the key factors that define their working conditions:
- Temperature Control: The environment must maintain a stable temperature, typically between 20°C to 25°C, to prevent overheating or cooling of sensitive components.
- Humidity Levels: Relative humidity should be kept between 40% to 60% to avoid moisture-related issues, such as corrosion or electrical shorts.
- Cleanroom Standards: Many machines operate in cleanrooms to prevent contamination from dust or particles, which could affect the precision of the assembly process.
- Vibration-Free Zones: The machines should be installed in areas with minimal vibration to ensure accurate alignment and welding of battery cells.
- Power Supply Stability: A consistent and reliable power supply is critical to avoid disruptions in the assembly process.
How Are Quality Testing Methods Implemented in Cylindrical Battery Pack Machines?
Quality testing is a critical step in the production of cylindrical battery packs. Here’s how it’s typically done:
- Voltage Testing: Each cell is tested for its voltage output to ensure it meets the required specifications.
- Resistance Testing: The internal resistance of the cells is measured to identify any potential issues with conductivity.
- Capacity Testing: The machine checks the energy storage capacity of the cells to ensure they can deliver the expected performance.
- Visual Inspection: Automated cameras or sensors inspect the cells for physical defects, such as dents or scratches.
- Leakage Testing: The machine tests for any electrolyte leakage, which could compromise the safety and functionality of the battery pack.
These tests are performed at various stages of the assembly process to ensure that only high-quality cells are used in the final battery pack.
How to Maintain and Care for Cylindrical Battery Pack Machines
Proper maintenance is essential to keep cylindrical battery pack machines running efficiently. Here’s a step-by-step guide:
- Regular Cleaning: Clean the machine components, such as conveyors and welding heads, to prevent dust or debris buildup.
- Lubrication: Apply lubricant to moving parts to reduce friction and wear.
- Inspection of Welding Modules: Check the welding modules for signs of wear or damage and replace them as needed.
- Calibration: Regularly calibrate sensors and testing units to ensure accurate measurements.
- Software Updates: Keep the machine’s software up to date to benefit from the latest features and improvements.
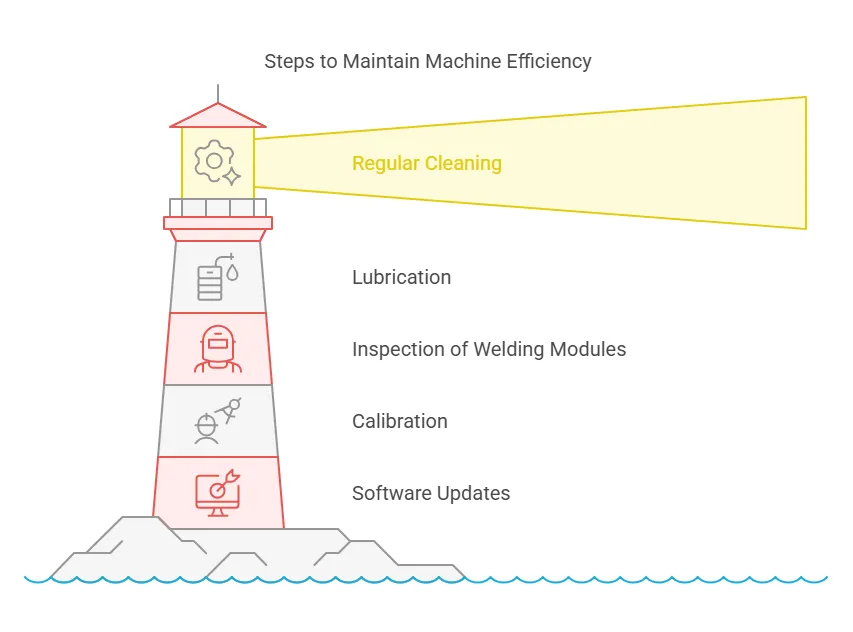
By following these steps, you can extend the lifespan of the machine and minimize downtime.
What Are Common Issues and Troubleshooting Tips for Cylindrical Battery Pack Machines?
Even with proper maintenance, issues can arise. Here are some common problems and how to address them:
- Misaligned Cells: If cells are not aligned properly, check the sorting and orientation unit for calibration issues.
- Weak Welds: Inspect the welding module for worn-out components and ensure the correct welding parameters are set.
- Testing Failures: If cells fail quality tests, verify the testing equipment for accuracy and recalibrate if necessary.
- Machine Jams: Clear any obstructions in the feeding system and ensure the conveyor belt is functioning smoothly.
- Power Fluctuations: Install a voltage stabilizer to prevent disruptions caused by inconsistent power supply.
Why Are Safety Precautions Critical When Using Cylindrical Battery Pack Machines?
Safety is paramount when operating cylindrical battery pack machines due to the risks associated with battery production. Here are key precautions to follow:
- Personal Protective Equipment (PPE): Operators should wear gloves, safety glasses, and protective clothing to prevent injuries.
- Fire Safety: Install fire extinguishers and smoke detectors in the working area, as battery cells can be flammable.
- Emergency Stop Buttons: Ensure the machine is equipped with easily accessible emergency stop buttons.
- Training: Provide thorough training to operators on safe machine operation and emergency procedures.
- Regular Safety Audits: Conduct periodic safety inspections to identify and address potential hazards.
By adhering to these safety measures, you can create a secure working environment and minimize the risk of accidents.
These machines automate the assembly of cylindrical battery cells into packs used in electric vehicles, consumer electronics, and renewable energy storage systems. We examined their key components, including feeding systems, welding modules, and testing units, and outlined the step-by-step process from cell feeding to final packaging. The importance of controlled working environments, quality testing methods, and regular maintenance was also highlighted to ensure optimal performance and safety. By understanding the capabilities and benefits of the cylindrical battery pack machine, industries can enhance their production processes and deliver higher-quality, more efficient battery solutions.