What Are Your Application Requirements and Why Do They Matter?
When choosing the best spot welding machine, the first step is to understand your application requirements. Different industries have unique welding needs, and selecting the right machine depends on the specific tasks you need to perform. For example, in the lithium battery assembly for electric vehicles (EVs), precision and consistency are critical to ensure battery safety and performance. On the other hand, welding solar panel connectors may require machines that can handle larger components with high durability.
At Topower, we specialize in providing tailored welding solutions for the new energy sector, including energy storage systems and battery packs. Our machines are designed to meet the rigorous demands of these applications, ensuring high-quality welds that enhance product reliability. Whether you’re working on EV batteries or renewable energy components, understanding your application requirements is the foundation for choosing the right spot welding machine.
How Does Material Compatibility Affect Your Choice of Spot Welding Machine?
The type of material you’re welding plays a significant role in determining the best spot welding machine for your needs. Copper, aluminum, and nickel alloys are commonly used in the new energy industry, but each material has unique properties that affect welding performance. For instance, aluminum requires a machine with precise heat control to avoid burn-through, while copper demands high current output for effective welding.
Our spot welding machines are engineered to handle advanced materials used in EV batteries and renewable energy components. Our machines offer adjustable settings to accommodate different material thicknesses and types, ensuring consistent and reliable welds. If you’re working with challenging materials, our Energy Storage Spot Welder is a perfect choice, offering unmatched adaptability and performance.
Why Are Power Output and Precision Control Critical in Spot Welding Machines?
The power output and precision control of a spot welding machine are crucial factors, especially in sensitive applications like battery welding or solar panel assembly. There are three main types of spot welders: AC, DC, and inverter-based. Each has its advantages, but inverter-based spot welders stand out for their energy efficiency and precise current control.
Our inverter spot welding machines are designed to deliver consistent and accurate welds, even in the most critical applications. For example, our Energy Storage Spot Welder features advanced current control technology, ensuring optimal weld quality for lithium-ion batteries and other high-precision components. If you’re looking for a machine that combines power and precision, our inverter-based models are the ideal solution.
How Can Automation Capabilities Enhance Your Welding Process?
In high-volume production environments, automation is key to improving efficiency and consistency. For industries like EV battery manufacturing, where thousands of welds are performed daily, robotic integration can significantly enhance productivity and reduce human error.
We offer automated welding systems that are specifically designed for the new energy sector. Our machines can be seamlessly integrated into robotic production lines, enabling scalable and efficient manufacturing processes. Whether you’re producing battery modules or energy storage systems, our automated solutions ensure high-quality welds at scale.
What Role Does Thermal Management and Safety Play in Spot Welding Machines?
Thermal management and safety are critical considerations, especially when welding sensitive components like battery cells. Overheating can lead to defects or even safety hazards, making it essential to choose a machine with effective cooling systems and safety certifications.
Our spot welding machines are equipped with advanced cooling systems to prevent overheating during prolonged use. Additionally, our machines meet CE and ISO standards, ensuring they are safe and reliable for use in demanding applications. For example, our Energy Storage Spot Welder features built-in thermal protection and real-time temperature monitoring, providing peace of mind for operators working on critical projects.
Step-by-Step Guide: How to Choose the Best Spot Welding Machine for Your Needs
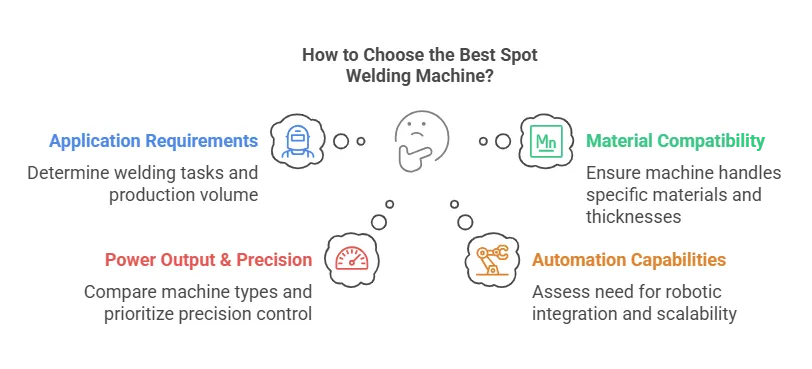
Choosing the right spot welding machine doesn’t have to be overwhelming. Follow these steps to make an informed decision:
-
Identify Your Application Requirements
- Determine the type of welding tasks you’ll be performing (e.g., battery assembly, solar panel connectors).
- Consider the volume of production (manual vs. automated systems).
-
Evaluate Material Compatibility
- Identify the materials you’ll be welding (e.g., copper, aluminum, nickel alloys).
- Check if the machine can handle the thickness and properties of these materials.
-
Assess Power Output and Precision Control
- Compare AC, DC, and inverter-based machines.
- Prioritize machines with precise current control for critical applications.
-
Consider Automation Capabilities
- Determine if you need robotic integration for high-volume production.
- Look for machines that offer scalability and flexibility.
-
Check Thermal Management and Safety Features
- Ensure the machine has effective cooling systems.
- Verify safety certifications like CE and ISO.
How Does Electrode Design and Durability Impact Weld Quality?
The electrode design and material are critical factors that directly affect weld quality and the longevity of your spot welding machine. Electrodes made from tungsten-copper alloys are highly durable and offer excellent thermal and electrical conductivity, making them ideal for high-cycle production environments. These materials resist wear and deformation, ensuring consistent weld quality over time.
We provide custom electrode solutions tailored to your specific welding needs. Whether you’re working on EV battery assembly or energy storage systems, our electrodes are designed to withstand the rigors of high-volume production. By choosing the right electrode materials and design, you can significantly extend the lifespan of your welding machine and reduce maintenance costs.
Why Is Energy Efficiency and Sustainability Important in Spot Welding?
As industries worldwide shift toward green manufacturing, energy efficiency has become a top priority. Traditional AC welders are known for their high energy consumption, which can lead to increased operational costs and a larger carbon footprint. In contrast, mid-frequency inverter DC welders, like those offered by Topower, are designed to be energy-efficient and environmentally friendly.
Our inverter-based spot welding machines consume up to 30% less energy compared to traditional AC welders, aligning with sustainable manufacturing practices. By reducing energy consumption, our machines not only lower your operational costs but also contribute to a greener future. We are committed to providing eco-friendly industrial equipment that meets the demands of modern manufacturing while minimizing environmental impact.
How Can IoT and Smart Manufacturing Enhance Your Welding Process?
The integration of IoT (Internet of Things) and smart manufacturing technologies is revolutionizing the welding industry. Machines with Industry 4.0 compatibility offer features like real-time data monitoring, predictive maintenance, and cloud connectivity, enabling manufacturers to optimize their processes and improve product quality.
Our smart welding machines are equipped with advanced IoT capabilities. For example, our machines can connect to cloud-based platforms, allowing you to monitor weld quality and machine performance in real time. This data-driven approach helps you identify potential issues before they escalate, reducing downtime and improving overall efficiency. By embracing smart manufacturing, you can stay ahead in the competitive new energy sector.
What Role Does After-Sales Support and Training Play in Your Welding Operations?
Investing in a high-quality spot welding machine is just the first step. To maximize the value of your investment, after-sales support and technical training are essential. Proper training ensures that your operators can use the machine effectively, while reliable support guarantees minimal downtime in case of issues.
At Topower, we offer comprehensive after-sales services, including:
- Technical training for operators and maintenance staff.
- Spare parts availability to minimize production interruptions.
- A global service network covering 50+ countries, ensuring prompt assistance wherever you are.
Our dedicated support team is always ready to assist with installation, troubleshooting, and maintenance, ensuring your welding operations run smoothly.
How to Calculate the Total Cost of Ownership (TCO) for a Spot Welding Machine
When choosing a spot welding machine, it’s important to consider not just the upfront cost but also the long-term total cost of ownership (TCO). Factors like energy consumption, maintenance costs, and downtime reduction can significantly impact your ROI.
For example, while traditional AC welders may have a lower initial price, their higher energy consumption and maintenance requirements can lead to greater long-term costs. In contrast, Topower’s mid-frequency inverter DC welders offer:
- Lower energy consumption, reducing utility bills.
- Minimal maintenance needs, thanks to durable components.
- Reduced downtime, ensuring higher productivity.
By evaluating the TCO, you can make a more informed decision and choose a spot welding machine that delivers long-term value for your business. We’re here to help you optimize your welding operations and achieve your production goals.