In an era where precision and efficiency are paramount, the labeling machine has become an indispensable tool across various industries. From food and beverage to pharmaceuticals, cosmetics, and logistics, these automated devices ensure that products are accurately labeled with essential information such as barcodes, expiration dates, and branding. This blog will dive deep into the world of labeling machines, exploring their types, applications, and the significant benefits they offer to modern manufacturing and packaging processes. Whether you are looking to optimize your production line or simply understand the technology behind these machines, this post will provide valuable insights.
What is a Labeling Machine?
A labeling machine is an automated device designed to apply labels to various products, packages, or containers with precision and efficiency. These machines are widely used in industries such as food and beverage, pharmaceuticals, cosmetics, and logistics to ensure that products are properly labeled with essential information like barcodes, expiration dates, and branding. Labeling machines not only enhance productivity but also reduce human error, ensuring consistency and accuracy in labeling processes.
Types of Labeling Machines and Their Applications
Labeling machines come in various types, each suited for specific applications. Here are some common types:
- Pressure-Sensitive Labelers: These machines use pre-cut labels with adhesive backing. They are ideal for industries like cosmetics and pharmaceuticals, where precision and clean application are crucial.
- Sleeve Labelers: Perfect for beverages and canned goods, sleeve labelers wrap a label around the entire product, providing 360-degree coverage.
- Glue-Based Labelers: These machines apply labels using adhesive glue. They are commonly used in the food and beverage industry for glass bottles and jars.
- Thermal Transfer Labelers: These are used for printing and applying labels in real-time, often seen in logistics and shipping industries.
- In-Mold Labelers: Integrated into the manufacturing process, these machines embed labels directly into plastic containers during molding, commonly used for packaging household products.
Each type of labeling machine is designed to meet specific industry needs, ensuring efficiency and adaptability.
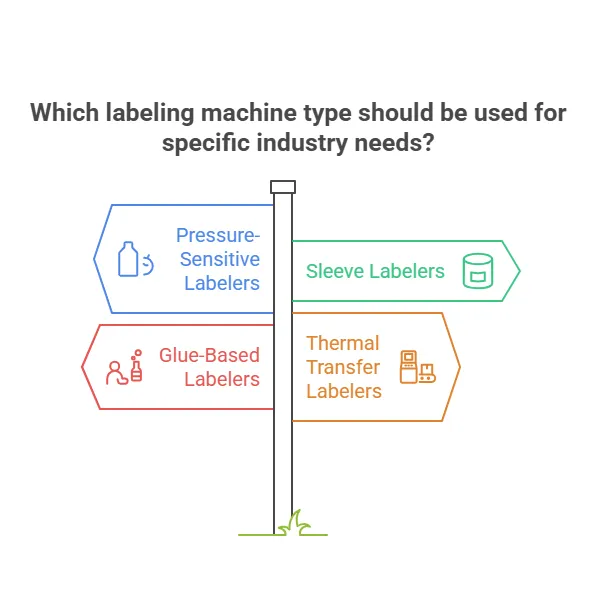
How Does a Labeling Machine Work?
Labeling machines operate through a series of well-coordinated steps to ensure accurate label application. Here’s a step-by-step breakdown:
- Product Feeding: Products are fed into the machine via a conveyor belt or manual placement.
- Label Dispensing: The machine dispenses a label from the roll or stack, ensuring it is properly aligned.
- Label Application: The label is applied to the product using mechanisms like rollers, air blowers, or adhesive applicators, depending on the machine type.
- Label Pressing: Once applied, the label is pressed firmly onto the product to ensure it adheres securely.
- Quality Check: Advanced machines may include sensors or cameras to verify label placement and accuracy.
- Product Discharge: The labeled product is discharged from the machine, ready for packaging or further processing.
This seamless process ensures high-speed, consistent, and error-free labeling.
Labeling Machine Structure and Components
A labeling machine is composed of several key components that work together to deliver efficient performance. Here’s a breakdown of its structure:
- Conveyor System: Transports products through the labeling process.
- Label Dispenser: Holds and dispenses labels from rolls or stacks.
- Application Mechanism: Applies the label to the product using rollers, brushes, or air pressure.
- Control Panel: Allows operators to adjust settings like speed, label placement, and timing.
- Sensors and Detectors: Ensure proper label alignment and detect errors.
- Adhesive System: Applies glue or activates adhesive backing for pressure-sensitive labels.
- Frame and Housing: Provides structural support and protects internal components.
Each component plays a critical role in ensuring the machine operates smoothly and delivers high-quality results.
Product Application Scope of Labeling Machines
Labeling machines are versatile and cater to a wide range of industries and products. Here are some common applications:
- Food and Beverage: Labeling bottles, cans, jars, and packages with nutritional information, branding, and barcodes.
- Pharmaceuticals: Applying labels to medicine bottles, blister packs, and syringes with critical information like dosage and expiration dates.
- Cosmetics: Labeling skincare, makeup, and haircare products with branding and ingredient lists.
- Logistics and Shipping: Printing and applying shipping labels, tracking codes, and handling instructions.
- Household Products: Labeling cleaning supplies, detergents, and other consumer goods.
- Electronics: Applying labels to cables, devices, and packaging for identification and branding.
The adaptability of labeling machines makes them indispensable in modern manufacturing and packaging processes.
How Labeling Machines Fit into the Production Workflow
Labeling machines play a crucial role in modern production workflows, ensuring that products are accurately and efficiently labeled before they reach the market. Here’s how they integrate into the process:
- Upstream Integration: Labeling machines are often connected to upstream processes like filling, capping, or packaging. For example, in a beverage production line, bottles are filled, capped, and then immediately labeled.
- Real-Time Labeling: In automated workflows, labeling machines apply labels in real-time as products move along the conveyor belt, ensuring seamless production without bottlenecks.
- Downstream Processes: After labeling, products are typically sent for additional packaging, quality checks, or shipping preparation. Labeling machines ensure that products are ready for these next steps.
- Data Integration: Advanced labeling machines can integrate with enterprise systems to print variable data like barcodes, batch numbers, or expiration dates, ensuring traceability and compliance.
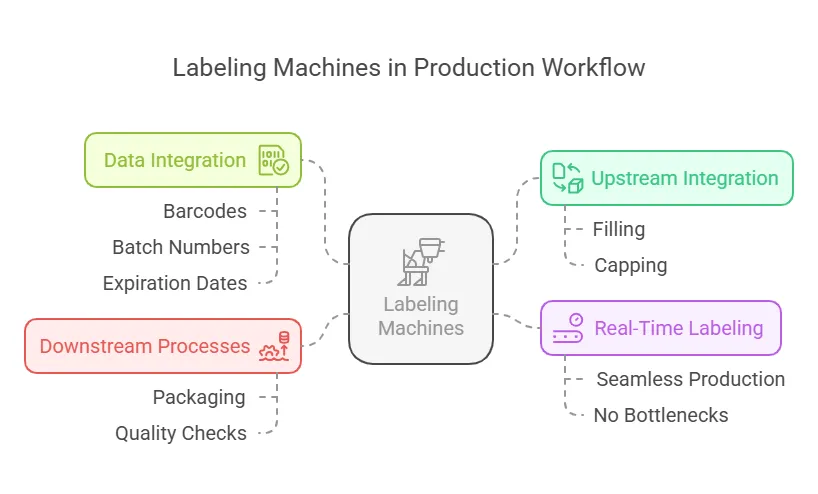
By streamlining the labeling process, these machines enhance overall production efficiency and reduce downtime.
Why Quality Testing and Performance Evaluation Matter for Labeling Machines
Quality testing and performance evaluation are essential to ensure that labeling machines operate at peak efficiency and deliver consistent results. Here’s why they matter:
- Accuracy: Testing ensures that labels are applied precisely, avoiding misalignment or wrinkles that could affect product appearance or functionality.
- Speed: Performance evaluation helps determine if the machine can handle the required production speed without compromising quality.
- Durability: Regular testing identifies wear and tear, ensuring the machine remains reliable over time.
- Compliance: In industries like pharmaceuticals and food, labeling must meet strict regulatory standards. Testing ensures compliance with these requirements.
- Cost Efficiency: Identifying and resolving issues early reduces downtime and maintenance costs, saving businesses money in the long run.
Performance evaluation typically involves running the machine under various conditions, monitoring output, and using sensors or cameras to detect errors.
How to Choose the Right Labeling Machine for Your Business
Selecting the right labeling machine is critical for optimizing your production process. Here’s a step-by-step guide to help you make the best choice:
-
Identify Your Needs:
- What type of products are you labeling? (e.g., bottles, boxes, flexible packaging)
- What label materials are you using? (e.g., paper, plastic, adhesive-backed)
- What is your production volume? (e.g., low, medium, high)
-
Consider Machine Types:
- Pressure-sensitive labelers for precision.
- Sleeve labelers for full-wrap labeling.
- Glue-based labelers for glass or rigid containers.
- Thermal transfer labelers for variable data printing.
-
Evaluate Features:
- Speed and throughput.
- Compatibility with label sizes and shapes.
- Ease of integration with existing production lines.
- Advanced features like vision systems for quality control.
-
Assess Budget and ROI:
- Compare upfront costs with long-term benefits like increased efficiency and reduced labor costs.
-
Check Vendor Reputation:
- Choose a reputable manufacturer with a track record of reliability and excellent customer support.
By following these steps, you can select a labeling machine that meets your specific business requirements.
Maintenance and Care Tips for Labeling Machines
Proper maintenance is key to ensuring the longevity and optimal performance of labeling machines. Here are some essential tips:
-
Regular Cleaning:
- Remove dust, adhesive residue, and debris from the machine daily to prevent malfunctions.
- Use recommended cleaning agents to avoid damaging sensitive components.
-
Lubrication:
- Lubricate moving parts like rollers and conveyors as per the manufacturer’s guidelines to reduce friction and wear.
-
Inspect Components:
- Check belts, sensors, and applicators for signs of wear or damage and replace them promptly.
-
Calibration:
- Regularly calibrate the machine to ensure accurate label placement and alignment.
-
Software Updates:
- Keep the machine’s software up to date to benefit from the latest features and bug fixes.
-
Training:
- Ensure operators are trained to use and maintain the machine correctly, reducing the risk of errors.

By following these maintenance practices, you can extend the lifespan of your labeling machine and minimize downtime.
Troubleshooting Common Issues in Labeling Machines
Even the most reliable labeling machines can encounter issues. Here’s how to troubleshoot some common problems:
-
Misaligned Labels:
- Cause: Incorrect label placement or sensor misalignment.
- Solution: Adjust the label sensor or recalibrate the machine.
-
Label Wrinkling:
- Cause: Improper tension or adhesive application.
- Solution: Adjust the tension settings or check the adhesive system.
-
Labels Not Sticking:
- Cause: Insufficient adhesive or incompatible label material.
- Solution: Ensure the adhesive is applied correctly or switch to a suitable label type.
-
Machine Jamming:
- Cause: Debris or misaligned components.
- Solution: Clean the machine and inspect for obstructions or misalignments.
-
Inconsistent Labeling Speed:
- Cause: Worn-out belts or motor issues.
- Solution: Replace belts or service the motor.
-
Error Messages:
- Cause: Software glitches or sensor malfunctions.
- Solution: Restart the machine or consult the user manual for error code explanations.
By addressing these issues promptly, you can maintain smooth operations and avoid costly production delays.
This article provides an in-depth exploration of labeling machines, highlighting their crucial role in modern production processes. It begins by defining what a labeling machine is and how it enhances productivity and accuracy in various industries. The article then examines the different types of labeling machines, including pressure-sensitive labelers, sleeve labelers, glue-based labelers, and thermal transfer labelers, each designed to meet specific industry needs. The step-by-step working mechanism of these machines is also detailed, along with their key components and integration into production workflows. Additionally, the importance of quality testing, maintenance, and troubleshooting is emphasized to ensure optimal performance and longevity. Finally, the article offers practical guidance on selecting the right labeling machine for your business. Overall, this comprehensive guide underscores the indispensable role of labeling machines in streamlining operations and ensuring compliance in today’s fast-paced industrial environment.