In today’s rapidly evolving tech landscape, lithium batteries have become the backbone of countless industries, from electric vehicles to renewable energy storage. But what exactly does it take to produce these high-performance power packs? In this blog, we delve into the world of lithium battery manufacturers, exploring their crucial role in the supply chain, the intricate production process, and the stringent safety measures that ensure these batteries are both reliable and safe. Whether you’re an industry insider or simply curious about the tech behind your gadgets, join us as we uncover the secrets of lithium battery manufacturing.
1. What is a Lithium Battery Manufacturer? Role and Value in the Supply Chain
A lithium battery manufacturer specializes in producing rechargeable lithium-ion (Li-ion) or lithium polymer (LiPo) batteries used in various industries. These companies play a critical role in the supply chain by converting raw materials like lithium, cobalt, and nickel into high-performance energy storage solutions.
Why Are They Important?
- Technology Enablers: They drive innovation in energy density, charging speed, and battery lifespan.
- Global Demand Support: With the rise of EVs and renewable energy storage, manufacturers ensure scalable production.
- Custom Solutions: They design batteries tailored for specific applications (e.g., medical devices vs. electric vehicles).
Key Contributions to the Supply Chain:
- Sourcing ethical raw materials to meet sustainability goals.
- Maintaining strict quality control for safety and performance.
- Collaborating with OEMs to integrate batteries into end products.
2. Inside a Lithium Battery Factory: From Raw Material to Final Pack
How Are Lithium Batteries Produced? Here’s a step-by-step look inside a factory:
-
Material Preparation
- Lithium, graphite, and electrolytes are purified and processed.
- Cathode (e.g., LiFePO4) and anode materials are coated onto metal foils.
-
Electrode Assembly
- Layers of cathodes, anodes, and separators are stacked or wound.
-
Cell Formation
- The assembly is placed in a casing, filled with electrolyte, and sealed.
-
Aging & Testing
- Cells undergo charge/discharge cycles to check capacity and stability.
-
Module/Pack Integration
- Cells are combined into modules with BMS (Battery Management Systems) for larger applications like EVs.
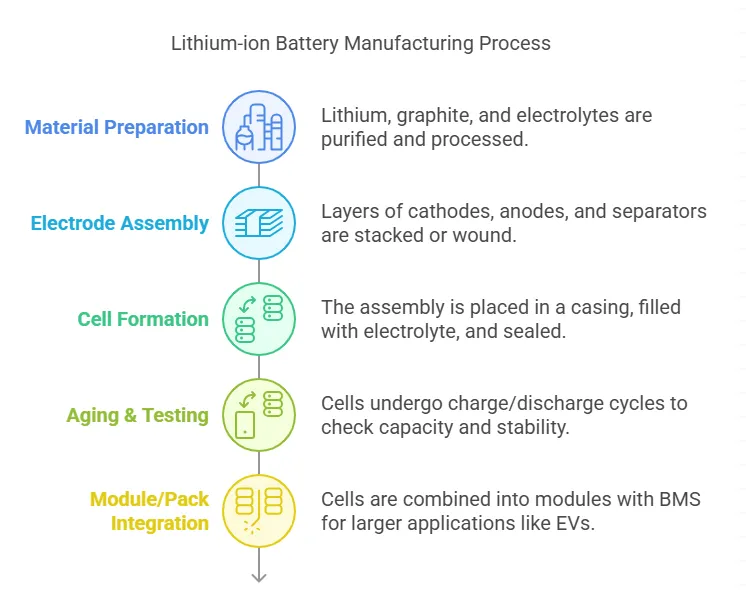
Safety Measures:
- Humidity-controlled cleanrooms prevent contamination.
- Automated systems minimize human error in welding and assembly.
3. How Lithium Batteries Are Made: A Technical Breakdown
What’s Inside a Lithium Battery?
- Cathode: Determines voltage/capacity (e.g., NMC, LCO).
- Anode: Typically graphite or silicon-based.
- Separator: Porous membrane preventing short circuits.
- Electrolyte: Liquid/polymer enabling ion movement.
Key Manufacturing Steps:
- Slurry Mixing: Active materials bind into a paste.
- Coating & Drying: Slurry is applied to foil current collectors.
- Calendaring: Electrodes are compressed for uniform thickness.
- Welding: Tabs connect electrodes to terminals.
Why Precision Matters:
- Even micron-level defects can cause overheating or failure.
4. Application of Lithium Batteries in EVs, ESS, Consumer Electronics
Where Are Lithium Batteries Used?
-
Electric Vehicles (EVs):
- High energy density extends driving range.
- Fast-charging capabilities reduce downtime.
-
Energy Storage Systems (ESS):
- Store solar/wind energy for grid stability.
- Power homes during outages (e.g., Tesla Powerwall).
-
Consumer Electronics:
- Smartphones, laptops, and wearables rely on lightweight Li-ion packs.
- Longer cycle life compared to traditional batteries.
Why Lithium Dominates:
✔ 30–50% lighter than lead-acid/NiMH alternatives.
✔ Low self-discharge rate (~5% per month).
5. Clean Room and Safety Standards in Lithium Battery Factories
Why Cleanrooms Are Non-Negotiable
Lithium batteries are sensitive to moisture and particles. Even tiny contaminants can:
- Cause internal short circuits.
- Reduce battery lifespan.
Key Safety Protocols:
- ISO 14644-1 Class 8+ Cleanrooms: Filtered air to limit dust.
- Humidity Control: Kept below 1% for moisture-sensitive processes.
-
Fire Prevention:
- Thermal runaway detection systems.
- Fireproof storage for volatile electrolytes.
Step-by-Step Safety Checks:
- Incoming material inspection (X-ray/chemical analysis).
- In-process quality tests (e.g., thickness gauges).
- Final product validation (nail penetration/overcharge tests).
6. Quality Control in Lithium Battery Production: Key Standards and Tools
Why Quality Control is Critical for Lithium Batteries
Defective lithium batteries can lead to safety hazards like thermal runaway, fires, or poor performance. Rigorous quality control (QC) ensures reliability, efficiency, and compliance with international standards.
Key QC Standards in Lithium Battery Manufacturing
- ISO 9001: Ensures consistent production processes.
- UL 1642 / IEC 62133: Safety certifications for cell-level testing.
- UN 38.3: Mandatory for transportation safety (vibration, shock, thermal tests).
How Manufacturers Implement QC: Step-by-Step
-
Raw Material Inspection
- X-ray fluorescence (XRF) analyzers verify material purity.
- Moisture content checks prevent electrolyte contamination.
-
In-Process Testing
- Electrode coating uniformity measured by laser micrometers.
- Automated optical inspection (AOI) detects defects in cell stacking.
-
Final Product Validation
- Capacity testing (charge/discharge cycles).
- Safety tests: nail penetration, overcharge, short-circuit simulation.
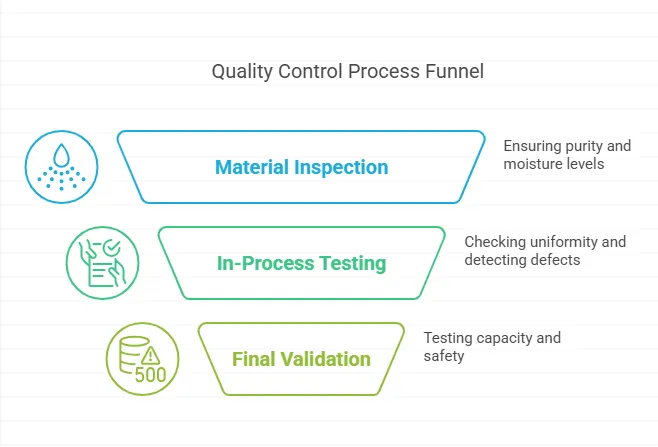
Tools Used for QC
✔ Cyclers: Measure battery performance over cycles.
✔ Environmental Chambers: Test operation under extreme temperatures (-40°C to 85°C).
✔ CT Scanners: Check internal structure without destruction.
7. Safety Precautions When Handling Lithium Battery Packs
Why Lithium Batteries Require Special Handling
Lithium is highly reactive. Damaged cells can leak electrolytes, overheat, or ignite. Proper handling minimizes risks in storage, transport, and usage.
Key Safety Measures
During Storage & Transport
- Temperature Control: Store at 15–25°C; avoid direct sunlight.
- Partial Charge (30–50%): Prevents degradation in long-term storage.
- Fireproof Containers: Use for bulk storage (especially for damaged cells).
During Assembly/Usage
- Anti-Static Gear: Prevents sparks near flammable electrolytes.
- No Metal Tools: Plastic or coated tools avoid short circuits.
- BMS Integration: Ensures overcharge/discharge protection.
What to Do in Case of Damage
- Isolate the battery in a non-flammable area.
- Wear PPE (gloves, goggles) if handling leaking cells.
- Use Class D fire extinguishers (for lithium fires).
8. How to Prolong the Lifespan of Lithium Batteries
What Degrades Lithium Batteries?
- High temperatures (>45°C).
- Deep discharges (below 20% capacity).
- Fast charging at high voltages.
Best Practices to Extend Battery Life
For Consumers (Phones, Laptops, EVs)
- Avoid 100% Charging: Keep charge between 20–80% for daily use.
- Store at Half-Charge: If unused for months, maintain ~50% charge.
- Use OEM Chargers: Incompatible chargers cause voltage spikes.
For Industrial/ESS Applications
- Temperature Management: Active cooling/heating systems.
- Balanced Charging: BMS ensures even cell voltage distribution.
- Cycle Depth Control: Limit depth of discharge (DoD) to 80% for ESS.
Step-by-Step Maintenance for EV Batteries
- Use slow charging (Level 2) for daily needs; reserve fast charging for trips.
- Park in shade/precondition battery in extreme weather.
- Schedule annual diagnostics to check cell balance.
9. How to Choose a Reliable Lithium Battery Manufacturer for Your Project
Why Supplier Selection Matters
A subpar manufacturer risks:
✖ Poor cycle life.
✖ Safety failures (recalls/fires).
✖ Delays due to non-compliance with regulations.
Key Evaluation Criteria
1. Certifications & Compliance
- Look for ISO 9001, IATF 16949 (auto-grade), and UL/IEC certifications.
2. Technical Capabilities
- Customization: Can they tailor batteries (size, chemistry, BMS)?
- R&D Investment: Ask about patents or partnerships with OEMs.
3. Quality Control Process
- Request audit reports or third-party test data (e.g., cycle life graphs).
- Check if they track materials via blockchain for ethical sourcing.
4. Supply Chain Stability
- Do they have long-term contracts with raw material suppliers?
- Backup production facilities to prevent shortages?
Red Flags to Avoid
- No transparency about cell origins.
- Lack of safety testing documentation.
- Overly cheap pricing (may indicate recycled/low-grade materials).
This article provides an in-depth look at the lithium battery manufacturing industry. It begins by explaining the role of lithium battery manufacturers in converting raw materials into advanced energy storage solutions, driving innovation in energy density and safety. The production process is then dissected step-by-step, from material preparation and electrode assembly to final testing and integration. Safety protocols, including the necessity of cleanrooms and fire prevention measures, are emphasized throughout. The article also explores the diverse applications of lithium batteries in electric vehicles, energy storage systems, and consumer electronics, highlighting their advantages over traditional batteries. Additionally, it covers quality control standards, handling precautions, and tips for prolonging battery life. Finally, it offers guidance on selecting a reliable manufacturer, stressing the importance of certifications, technical capabilities, and supply chain stability.