Lithium battery recycling equipment is at the forefront of sustainable technology, addressing the growing demand for lithium-ion batteries while mitigating environmental impact. As the world increasingly relies on electric vehicles and electronic devices, the need to efficiently recycle these batteries becomes paramount. This specialized machinery not only recovers valuable materials like lithium, cobalt, and nickel but also ensures safety and minimal environmental hazards. With the global lithium market projected to expand dramatically, understanding and investing in lithium battery recycling equipment is crucial for industries and policymakers aiming to build a circular economy.
What Is Lithium Battery Recycling Equipment?
Lithium battery recycling equipment refers to specialized machinery designed to safely dismantle, process, and recover valuable materials from used lithium-ion batteries (e.g., from EVs, electronics). These systems employ mechanical, chemical, or hydrometallurgical methods to extract metals like lithium, cobalt, nickel, and copper while minimizing environmental hazards.
Key Components Include:
- Pre-treatment Modules: Discharge units to neutralize residual electricity.
- Size Reduction Systems: Shredders/crushers to break down battery casings.
- Separation Technologies: Magnetic/eddy current separators, sieves, and airflow classifiers to isolate materials.
- Purification Systems: Chemical leaching or smelting units for high-purity metal recovery.
Why It Matters: With global lithium demand projected to grow 40-fold by 2040 (IEA), this equipment enables circular economies by reclaiming >90% of battery materials.
Step-by-Step Workflow: How Lithium Battery Recycling Equipment Processes Batteries
Step 1: Battery Collection & Sorting
- Input: Used batteries (EV packs, consumer electronics) are tested and categorized by chemistry (LiFePO4, NMC, etc.).
- Safety: Batteries are discharged to 0V to prevent thermal runaway.
Step 2: Mechanical Processing
- Shredding: Batteries are shredded under inert gas (nitrogen) to prevent fires.
- Crushing: Hammer mills reduce fragments to <10mm particles.
- Screening: Vibrating sieves separate plastics/metals.
Step 3: Material Recovery
- Magnetic Separation: Recovers iron/nickel foils.
- Eddy Current Separation: Extracts aluminum and copper.
- Hydrometallurgy: Leaches lithium/cobalt from “black mass” via acids (e.g., H2SO4 + H2O2).
Step 4: Refining
- Electrowinning or precipitation purifies metals to battery-grade (≥99.5% purity).
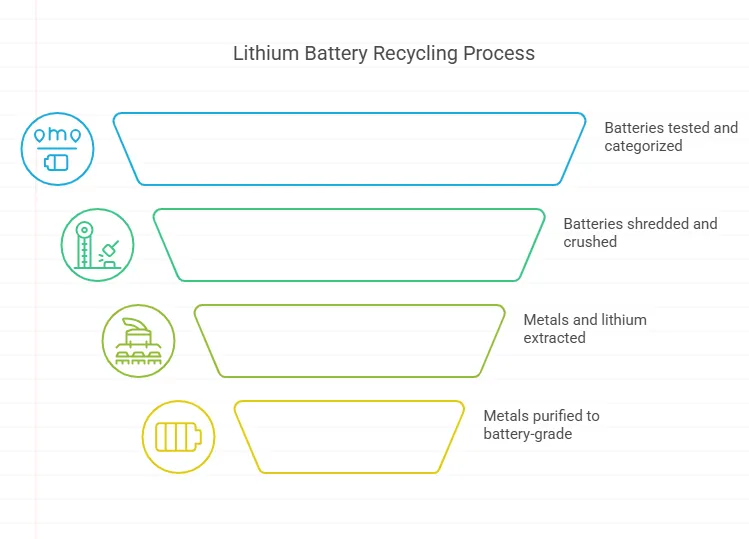
How the Shredding, Crushing, and Sorting Modules Work
Shredding Module
- Function: Tears batteries into 50–100mm pieces using rotary shear shredders.
-
Safety Features:
- Nitrogen inertization prevents explosions.
- Water-cooling systems manage heat.
Crushing Module
- Process: Secondary crushing via jaw crushers/ball mills pulverizes materials to <3mm.
- Output: “Black mass” (anode/cathode powder) + mixed metals.
Sorting Module
-
Technologies Applied:
- Airflow Separation: Lightweight plastics vs. heavy metals.
- Vibrating Screens: Segregate particles by size.
- Optical Sorters: AI cameras identify and separate material types.
Efficiency: Modern systems achieve >95% metal recovery rates (UNEP 2023 data).
Which Industries Benefit Most from Lithium Battery Recycling Machines?
1. Electric Vehicle (EV) Manufacturers
- Why: Recovered nickel/cobalt reduces reliance on mining; lowers production costs by 20–30%.
- Example: Tesla’s closed-loop system recycles 1,300+ tons of scrap annually.
2. Electronics Producers
- Application: Recovers lithium from smartphones/laptops for reuse in new devices.
3. Waste Management Companies
- Revenue Stream: Selling extracted metals (e.g., cobalt at $35,000/ton) creates profit from e-waste.
4. Battery Material Suppliers
- Advantage: Recycled lithium carbonate costs 60% less than mined lithium (BloombergNEF).
5. Government Recycling Programs
- Compliance: Meets EU Battery Regulation 2023 mandates (50% Li recovery by 2027).
What Is the Ideal Site Layout and Space Requirements for Installing Recycling Equipment?
Installing lithium battery recycling equipment requires careful planning to ensure safety, efficiency, and regulatory compliance.
Key Space Requirements
- Minimum Floor Space: 500–2,000 sqm (varies by capacity; e.g., 1 ton/hr systems need ~800 sqm).
- Ceiling Height: ≥6m to accommodate shredding and conveyor systems.
- Ventilation: Explosion-proof exhaust systems for gas dispersion (ATEX Zone 1 standards).
Optimal Layout Design
- Incoming Battery Storage – Dedicated area with fire-resistant containers (≥10m from processing).
- Pre-Treatment Zone – Discharge units and manual dismantling stations.
- Mechanical Processing Area – Shredders/crushers placed on vibration-dampening foundations.
- Sorting & Recovery Section – Magnetic separators + hydrometallurgical reactors (spaced to prevent cross-contamination).
- Waste Handling – Secure storage for hazardous byproducts (e.g., electrolyte sludge).
Why It Matters: Poor layout increases downtime by 30% (NREL study) and raises fire risks.
How Manufacturers Test Lithium Battery Recycling Machines Before Delivery
Step-by-Step Quality Assurance Process
-
Material Compatibility Testing
- Machines process sample batteries (NMC, LFP) to verify recovery rates (>90% for Co/Ni).
-
Safety Stress Tests
- Overload shredders with 150% capacity for 24 hours to check motor resilience.
- Simulate thermal runaway with punctured cells in an inert chamber.
-
Emission Control Checks
- Measure airborne particulates (must be <1mg/m³ per EPA guidelines).
-
Automation Validation
- Run 50+ cycles with AI sorting systems to ensure >98% material recognition accuracy.
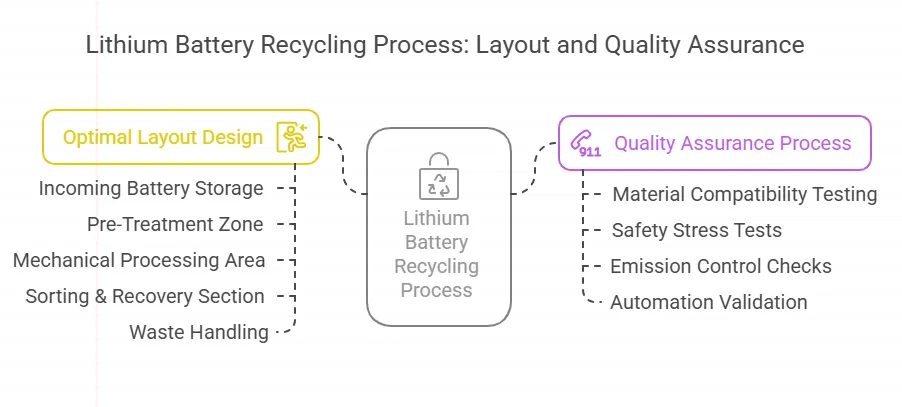
Data-Driven: Manufacturers like BHS and Redux provide third-party test reports with each machine.
Common Operator Mistakes and How to Avoid Them
Mistake #1: Skipping Battery Discharge
- Risk: Residual voltage causes fires in shredders.
- Solution: Use automated discharge racks (≤0.05V residual).
Mistake #2: Overloading Crushers
- Risk: Motor burnout; downtime costs ~$5,000/hr (industry average).
- Solution: Install load sensors with auto-shutoff at 90% capacity.
Mistake #3: Ignoring PPE
- Risk: Exposure to HF gas (from electrolyte decomposition).
- Solution: Mandate acid-resistant suits + real-time gas detectors.
Mistake #4: Improper Black Mass Handling
- Risk: Cross-contamination reduces lithium purity.
- Solution: Label storage bins and use sealed pneumatic transport.
Training Tip: VR simulations can reduce human errors by 40% (OSHA data).
How to Extend the Lifespan of Lithium Battery Recycling Machines
Maintenance Best Practices
-
Daily:
- Lubricate shredder bearings (high-temperature grease).
- Inspect conveyor belts for tears.
-
Weekly:
- Calibrate optical sorters with reference samples.
- Clean cyclone filters to maintain airflow.
-
Monthly:
- Replace wear parts (hammer mill tips, sieve meshes).
- Test emergency stop systems.
Environmental Controls
- Temperature: Keep processing areas at 15–25°C to prevent hydraulic fluid degradation.
- Humidity: Maintain <60% RH to avoid metal corrosion.
Cost Impact: Proactive maintenance cuts long-term repair costs by 50% (McKinsey analysis).
This comprehensive guide explores the essential components of lithium battery recycling equipment, including pre-treatment modules, mechanical processing systems, and purification units. We walk through the step-by-step workflow, from battery collection and sorting to material recovery and refining, emphasizing the importance of safety features and high recovery rates. The article also highlights the significant benefits for various industries, such as cost savings for EV manufacturers and revenue streams for waste management companies. Additionally, it covers key considerations for installing and maintaining this equipment, providing insights into quality assurance processes and common operator mistakes. As the demand for lithium continues to rise, lithium battery recycling equipment emerges as a vital solution for a sustainable future.