Lithium battery recycling technology is at the forefront of a global movement towards sustainability. With the exponential growth of electric vehicles and renewable energy, the need to efficiently recover valuable materials from spent lithium-ion batteries has never been more critical. This blog explores the advanced methods and processes that drive lithium battery recycling, from hydrometallurgy and pyrometallurgy to direct recycling and emerging innovations. Discover how these technologies are not only reducing environmental harm but also conserving finite resources and supporting a circular economy.
1. What Is Lithium Battery Recycling Technology?
Lithium battery recycling technology refers to the process of recovering valuable materials—such as lithium, cobalt, nickel, and copper—from used or end-of-life lithium-ion batteries. With the rapid growth of electric vehicles (EVs), consumer electronics, and renewable energy storage, recycling these batteries has become essential to reduce environmental harm, conserve finite resources, and support a circular economy.
Advanced recycling methods include:
- Hydrometallurgy: Using chemical solutions to dissolve and extract metals.
- Pyrometallurgy: High-temperature smelting to recover metals.
- Direct Recycling: Restoring cathode materials for reuse in new batteries.
This technology not only prevents hazardous waste but also reduces reliance on mining, making it a key sustainability solution.
2. How Does the Lithium Battery Recycling Process Work? (Step by Step)
The recycling process involves multiple stages to ensure safety and efficiency:
Step 1: Collection & Sorting
- Used batteries are gathered from recycling centers, manufacturers, or consumers.
- Batteries are sorted by chemistry (e.g., Li-ion, LiPo) and condition.
Step 2: Discharge & Dismantling
- Residual energy is safely discharged.
- Batteries are manually or mechanically disassembled to separate casings, wires, and cells.
Step 3: Shredding & Separation
- Cells are crushed into small pieces.
- Materials like plastics, aluminum, and copper are separated using sieves or magnets.
Step 4: Chemical/Metal Recovery
- Hydrometallurgy: Acids leach out lithium/cobalt for purification.
- Pyrometallurgy: Smelting extracts nickel/cobalt alloys.
Step 5: Purification & Reuse
- Recovered metals are refined into battery-grade materials.
- Recycled materials are sold to manufacturers for new products.
3. Why Are Key Technologies Important in Lithium Battery Recycling?
Efficient recycling relies on innovative technologies to maximize recovery rates and minimize environmental impact:
Hydrometallurgy
- How it works: Uses solvents (e.g., sulfuric acid) to dissolve metals.
- Advantage: High-purity lithium recovery (~90%).
Pyrometallurgy
- How it works: Burns organic materials at high temps (>1,400°C) to extract metals.
- Advantage: Effective for mixed battery types but loses lithium in slag.
Direct Recycling
- How it works: Preserves cathode materials (e.g., NMC) via relithiation.
- Advantage: Low energy cost; ideal for EV battery reuse.
Emerging methods like bioleaching (using bacteria) and electrodialysis (membrane-based separation) are also gaining traction for greener processing.
4. Where Are Recycled Lithium Battery Materials Used?
Recycled materials re-enter production cycles across industries:
- New Batteries: 95% of cobalt/nickel from recycled batteries is reused in EV/power storage cells.
- Electronics: Recovered lithium powers smartphones, laptops, and tablets.
- Metal Industry: Copper/aluminum foils are repurposed for wiring or construction.
- Renewable Energy: Solar/wind storage systems use recycled battery components.
This closed-loop system cuts costs, lowers carbon footprints, and meets ethical sourcing demands.
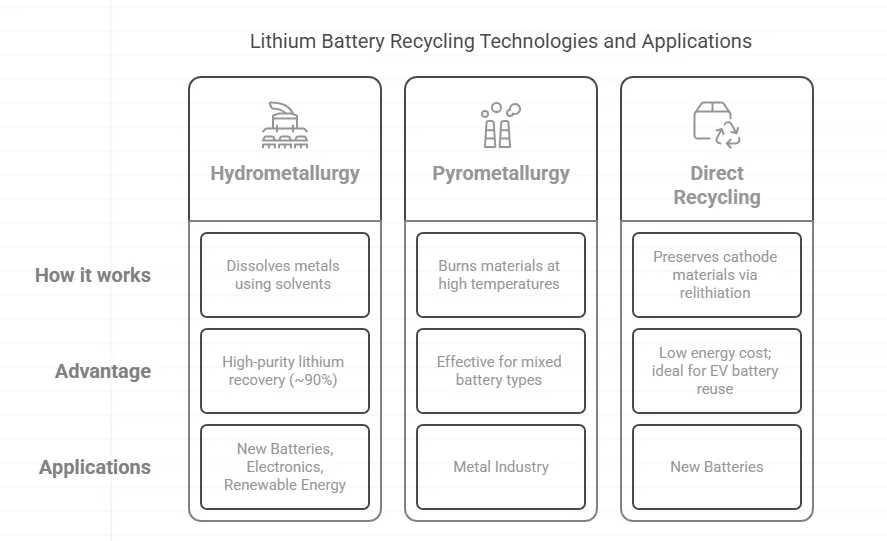
5. What Are the Industry Standards and Safety Measures?
Lithium battery recycling must comply with strict regulations to ensure worker safety and environmental protection:
Key Standards
- UN 38.3: Ensures safe transport of lithium batteries.
- EPA RCRA: U.S. rules for hazardous waste handling.
- EU Battery Directive: Mandates 50% recycling efficiency by 2025.
Safety Protocols
- Fireproof storage for spent batteries.
- Automated dismantling to reduce human exposure to toxic substances.
- Air filtration systems to capture harmful fumes during smelting.
Companies like Li-Cycle and Redwood Materials follow these guidelines while pioneering zero-waste recycling models.
1. How Is Testing and Quality Control Performed in Lithium Battery Recycling?
Testing and quality control (QC) are critical to ensuring recycled materials meet industry standards for reuse. Here’s how it works:
Step-by-Step QC Process:
-
Incoming Inspection
- Batteries are checked for damage, voltage, and chemistry type.
- Defective or swollen batteries are isolated for safe handling.
-
Material Analysis
- X-ray fluorescence (XRF) and atomic absorption spectroscopy (AAS) test metal purity.
- Inductively coupled plasma (ICP) measures lithium/cobalt/nickel concentrations.
-
Process Monitoring
- Real-time sensors track temperature, pH, and chemical reactions during leaching/smelting.
- Automated sorting removes impurities (e.g., plastics, aluminum).
-
Final Product Validation
- Recycled metals are compared to virgin material benchmarks.
- Battery manufacturers conduct performance tests (e.g., cycle life, energy density).
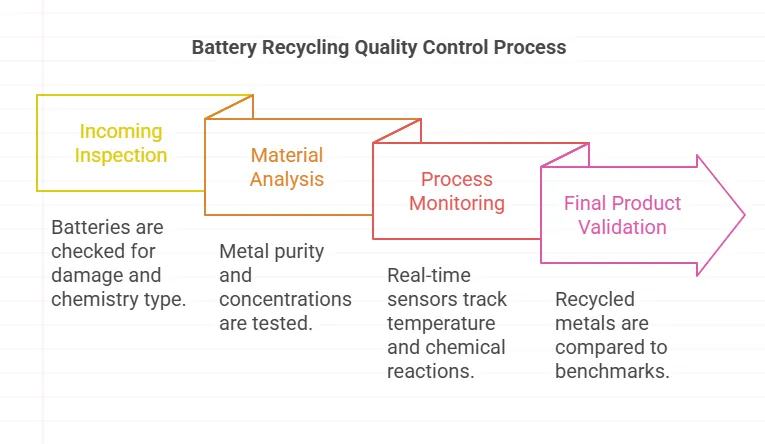
Why It Matters: Poor QC can lead to battery failures or contamination, making rigorous testing essential for safety and efficiency.
2. What Are the Key Safety Risks and Usage Precautions in Lithium Battery Recycling?
Lithium battery recycling involves hazards like fires, toxic leaks, and explosions. Key precautions include:
Major Risks & Mitigation Strategies:
-
Thermal Runaway
- Cause: Damaged batteries short-circuit, releasing heat.
- Prevention: Store batteries in fireproof containers with sand/CO₂ extinguishers nearby.
-
Toxic Chemical Exposure
- Cause: Electrolytes (e.g., LiPF₆) degrade into hydrofluoric acid (HF).
- Prevention: Use PPE (gloves, respirators) and automated dismantling robots.
-
Explosive Gases
- Cause: Shredding releases flammable solvents (e.g., ethylene carbonate).
- Prevention: Operate in nitrogen-filled chambers to suppress combustion.
Best Practices:
✔ Train workers in OSHA/ISO 14001 safety protocols.
✔ Install gas detectors and ventilation systems.
✔ Partner with certified e-waste recyclers (e.g., R2 or e-Stewards certified).
3. How to Maintain and Optimize Lithium Battery Recycling Equipment?
Recycling machinery (shredders, smelters, sorters) requires regular upkeep to maximize efficiency:
Maintenance Checklist:
- Daily: Inspect blades for wear, clean filters, and calibrate sensors.
- Weekly: Lubricate conveyor belts, check hydraulic systems for leaks.
- Monthly: Replace pyrolysis furnace linings, test emergency shutdown systems.
Optimization Tips:
- AI Sorting: Use machine learning to improve metal separation accuracy.
- Energy Recovery: Capture heat from smelting to power other processes.
- Predictive Maintenance: IoT sensors alert teams before breakdowns occur.
Example: Redwood Materials’ facilities achieve ~95% uptime via real-time equipment monitoring.
4. Why Is Lithium Battery Recycling Economically and Environmentally Beneficial?
Economic Advantages:
- Cost Savings: Recycled cobalt/nickel are 30–50% cheaper than mined metals.
- Revenue Streams: Selling recovered materials to battery OEMs (e.g., Tesla, Panasonic).
- Government Incentives: Tax credits (U.S. Bipartisan Infrastructure Law) fund recycling R&D.
Environmental Benefits:
- Resource Conservation: Recycling 1 ton of Li-ion batteries saves 5 tons of mined ore.
- CO₂ Reduction: Producing lithium from recycling emits 75% less GHG than mining.
- Waste Reduction: Prevents soil/water pollution from landfill leaching.
Case Study: Umicore’s closed-loop system recovers 17+ metals while cutting energy use by 70%.
5. What Are the Future Trends and Innovations in Lithium Battery Recycling?
Emerging technologies aim to make recycling faster, cheaper, and greener:
Key Innovations:
- Solid-State Battery Recycling: New methods to handle solid electrolytes (e.g., sulfide glass).
- Bioleaching: Bacteria (like Acidithiobacillus) extract metals with near-zero emissions.
- Blockchain Tracking: Digital IDs for batteries to streamline collection and recycling history.
Market Predictions:
- By 2030, the global lithium battery recycling market will exceed $24 billion (CAGR 21.6%).
- Direct recycling could supply 30% of EV battery materials by 2035 (DOE estimates).
Pioneers to Watch:
- Li-Cycle: Hub-and-spoke model for decentralized recycling.
- Battery Resourcers: Patented cathode-rejuvenation tech.
Lithium battery recycling technology is essential for managing the increasing volume of spent lithium-ion batteries. The process involves multiple stages, including collection, sorting, discharging, dismantling, and chemical recovery, with methods like hydrometallurgy and pyrometallurgy playing key roles. Innovations such as bioleaching and blockchain tracking are enhancing efficiency and sustainability. The economic and environmental benefits are significant, with recycled materials reducing costs and lowering carbon footprints. As the recycling market grows, companies like Li-Cycle and Redwood Materials are leading the way, setting new standards for a sustainable and circular economy.