The lithium battery welder has emerged as a critical tool in the advanced manufacturing landscape, particularly within the realms of energy storage and electric vehicles. Unlike conventional welding methods, these specialized devices offer unparalleled precision and safety, ensuring that delicate lithium-ion components are joined without compromising their integrity. From preventing thermal damage with non-invasive technology to achieving microsecond precision for consistent welds, the lithium battery welder is a game-changer in battery assembly. This blog will explore the inner workings of these innovative machines, their diverse applications, and best practices for maintenance and troubleshooting.
What Is a Lithium Battery Welder?
A lithium battery welder is a specialized device designed to join battery cells, tabs, and connectors through precise heat application. Unlike traditional welders, it uses controlled energy pulses (ultrasonic, laser, or resistance) to create strong bonds without damaging sensitive lithium-ion components.
Key Features:
- Non-invasive technology: Prevents thermal damage to electrolyte materials.
- Microsecond precision: Ensures consistent weld depth for thin foils (as thin as 0.1mm).
- Automated calibration: Adjusts parameters (current/pressure) based on material thickness.
Why It’s Unique: Lithium welders integrate safety protocols like real-time resistance monitoring to avoid short circuits during the process.
How Does a Lithium Battery Welder Work? A Step-by-Step Breakdown
Step 1: Material Preparation
- Clean electrode surfaces (nickel, aluminum, or copper) to remove oxides.
Step 2: Parameter Setting
- Input material type/thickness; the machine auto-selects:
- Pulse duration (e.g., 3–10ms)
- Current (50–300A)
- Electrode pressure (0.2–0.6MPa)
Step 3: Welding Execution
- Electrodes clamp the stacked foils.
- A microcurrent creates localized heat (1,500–2,500°C) at contact points.
- Molten pools solidify into nuggets within milliseconds.
Critical Parameters Table:
Factor | Impact | Optimal Range |
---|---|---|
Current | Penetration depth | 100–200A |
Pressure | Nugget formation | 0.3–0.5MPa |
Time | Heat exposure | ≤10ms |
Why Use Ultrasonic Welding for Lithium Batteries?
Ultrasonic welding dominates lithium battery assembly due to:
1. Solid-State Bonding
- Vibrates materials at 20–40kHz, creating friction welds without melting—critical for heat-sensitive anodes.
2. Zero Contamination
- Eliminates flux/foreign particles that could cause dendrite growth.
3. Energy Efficiency
- Consumes 60% less power than laser welding (typical usage: 500W vs. 1,200W).
Example Application: Tesla’s 4680 cell production uses ultrasonic welding for tab-to-can connections.
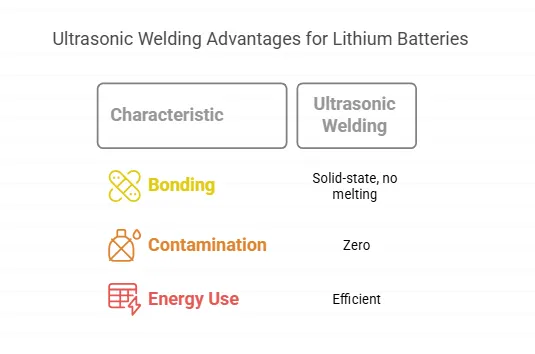
Where Are Lithium Battery Welders Applied?
Core Industries:
-
EV Manufacturing
- Module/pack assembly (e.g., busbar welding in BYD Blade batteries).
-
Consumer Electronics
- Smartphone pouch cell tab welding (0.05mm precision).
-
Energy Storage Systems
- Stacking prismatic cells for grid-scale ESS.
Emerging Uses:
- Solid-state battery prototyping (ceramic electrolyte compatible welders).
What Conditions Ensure Optimal Welding Performance?
Environmental Requirements:
- Humidity: Maintain <30% RH to prevent arcing.
- Temperature: 15–25°C ambient (prevents metal expansion).
-
Air Quality
- Class 100K cleanroom for critical welds.
- Nitrogen purging for copper welding.
Machine Maintenance Checklist (Weekly):
- Inspect tungsten electrodes for wear.
- Calibrate force sensors.
- Clean optical lenses (laser welders).
How to Test and Ensure Quality in Lithium Battery Welding
Why Quality Control Matters
Poor welds can lead to battery failure, overheating, or even combustion. Proper testing ensures:
- Consistent electrical conductivity
- Mechanical strength to withstand vibration
- No micro-cracks that could cause electrolyte leakage
Step-by-Step Testing Protocol:
-
Visual Inspection
- Check for surface defects (burrs, discoloration) using 10x magnification.
-
Peel Test
- Apply 90° angle force to welded tabs; a quality weld should withstand ≥5N/mm².
-
Resistance Measurement
- Use micro-ohmmeter; acceptable range: 50–200μΩ for copper-to-nickel joints.
-
X-ray Imaging
- Detect internal voids (>0.1mm voids fail ASTM E2935 standard).
Critical Parameters Table:
Test | Equipment | Pass Criteria |
---|---|---|
Shear Strength | Tensile tester | >15MPa |
Contact Resistance | 4-wire ohmmeter | <0.3mΩ |
Weld Nugget Diameter | Metallurgical microscope | ≥1.5x foil thickness |
What Safety Rules Must You Follow When Operating Lithium Battery Welders?
Non-Negotiable Precautions:
-
Personal Protection
- Wear IR-blocking goggles (laser welders emit 900–1,070nm wavelengths).
- Kevlar gloves for ultrasonic welders (20kHz vibrations can cause nerve damage).
-
Workspace Setup
- Install CO₂ fire extinguishers (Class D for lithium fires).
- Ground all equipment (static >100V can ignite electrolyte vapors).
Hazard-Specific Measures:
-
Laser Welding
- Enclose work area with interlocked curtains (OD 7+ optical density).
-
Resistance Welding
- Cool electrodes to <40°C to prevent material annealing.
How to Maintain Your Lithium Battery Welding Machine
Daily Maintenance Checklist:
-
Electrode Care
- Dress tungsten electrodes every 50 cycles (use diamond wheel grinder).
-
Cooling System
- Check chiller fluid level (50/50 water-glycol mix).
-
Calibration
- Verify force sensor accuracy with test weights (±2% tolerance).
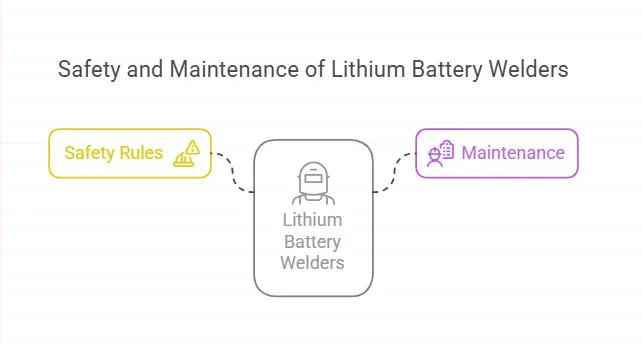
Monthly Deep Maintenance:
-
Ultrasonic Horn Inspection
- Crack test with red dye penetrant (replace if cracks >0.5mm appear).
-
Laser Optics Cleaning
- Wipe lenses with methanol and lint-free wipes (streak-free finish critical).
Common Wear Parts Replacement Schedule:
Part | Lifespan | Replacement Sign |
---|---|---|
Welding Tips | 10,000 cycles | Pitting >0.2mm depth |
Belts (Ultrasonic) | 6 months | Frequency drift >±0.3kHz |
Why Does Your Lithium Battery Welder Fail? Troubleshooting Guide
Top 5 Problems and Solutions:
-
Incomplete Welds
- Cause: Insufficient current/force.
- Fix: Increase power by 10% or recalibrate servo pressure.
-
Electrode Sticking
- Cause: Overheated copper tips (>300°C).
- Fix: Lower duty cycle to 30% or upgrade to zirconia electrodes.
-
Arcing
- Cause: Contaminated surfaces (oil/dust).
- Fix: Weld only after plasma cleaning.
-
Inconsistent Nugget Size
- Cause: Worn transformer taps.
- Fix: Replace after 500K discharges.
-
Software Errors (CNC Welders)
-
Reset Procedure:
- Power cycle controller.
- Reload weld parameter presets.
- Run dummy test cycle.
-
Reset Procedure:
How to Select the Right Lithium Battery Welder – 5 Key Factors
Decision-Making Criteria:
-
Material Compatibility
- For aluminum tabs: Laser welders (1064nm wavelength).
- Nickel-plated steel: Resistance welders (DC inverters preferred).
-
Production Volume
- <100 cells/day: Manual bench welders (3K–3K–8K).
- Mass production: Automated lines with vision systems ($50K+).
-
Precision Needs
- Thin-film welding (<0.1mm): Ultrasonic models with 10μm repeatability.
-
Safety Certifications
- Mandatory: CE (Europe), UL (USA), GB/T (China) for battery production.
-
After-Sales Support
- Demand <48hr response time for technical issues.
Cost Comparison Table:
Type | Price Range | Best For |
---|---|---|
Ultrasonic | 15K–15K–40K | Pouch cells |
Laser | 30K–30K–100K | Cylindrical cells |
Resistance | 5K–5K–20K | Busbar welding |
This in-depth guide delves into the world of lithium battery welders, highlighting their essential role in creating reliable and high-performance batteries. We break down the step-by-step process of how these welders work, emphasizing their unique features such as ultrasonic bonding, zero contamination, and energy efficiency. The blog also examines the wide range of applications for lithium battery welders, from EV manufacturing and consumer electronics to emerging uses in solid-state battery prototyping. Additionally, we provide critical insights into maintaining optimal welding performance through environmental control and regular maintenance routines. Safety protocols and troubleshooting tips are also covered to ensure smooth operations. Finally, we offer a comprehensive guide on selecting the right lithium battery welder, considering factors like material compatibility, production needs, precision requirements, safety certifications, and after-sales support. This blog is your ultimate resource for understanding and leveraging the power of lithium battery welders.