In the high-stakes world of lithium battery production, the lithium battery welding machine stands out as a cornerstone of precision and efficiency. These specialized machines are responsible for creating the robust and reliable connections within lithium-ion batteries, ensuring they meet the demanding standards required for consumer electronics, electric vehicles, and renewable energy storage. This blog takes a deep dive into the inner workings of lithium battery welding machines, exploring their key components, advanced technologies, and the critical role they play in various industries. Whether you’re a manufacturer seeking to optimize your production process or simply curious about the technology behind modern batteries, this guide will provide valuable insights into why these machines are essential for the future of energy storage.
What is a Lithium Battery Welding Machine?
A lithium battery welding machine is a specialized piece of equipment designed to join the components of lithium-ion batteries with precision and efficiency. These machines are crucial in the manufacturing process of lithium batteries, ensuring that the internal connections are secure and reliable. The welding process typically involves fusing the battery’s electrodes, tabs, and other critical parts using advanced techniques such as laser welding or ultrasonic welding. The result is a high-quality, durable battery that can withstand the demands of various applications, from consumer electronics to electric vehicles.
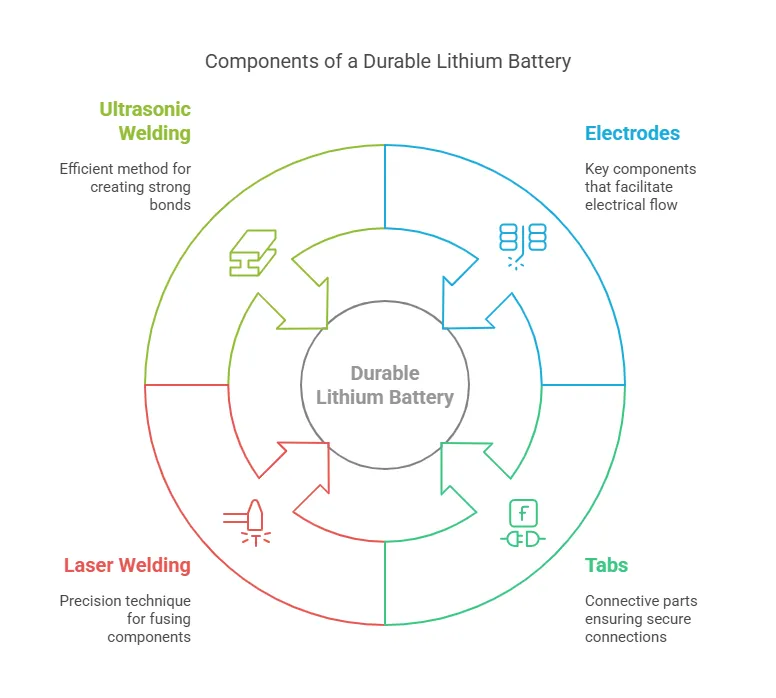
How Does a Lithium Battery Welding Machine Work?
Lithium battery welding machines operate by applying controlled energy to create a strong bond between battery components. The process begins with the precise alignment of the materials to be welded. Depending on the type of welding—laser, ultrasonic, or resistance—the machine then delivers a focused beam of light, high-frequency vibrations, or an electric current to the targeted area. This energy melts or fuses the materials together, forming a secure connection. The machine’s advanced sensors and software ensure that the welding parameters, such as temperature and pressure, are optimized for each specific battery design, resulting in consistent and reliable welds.
Key Components of a Lithium Battery Welding Machine
A lithium battery welding machine is composed of several critical components that work together to achieve precise and efficient welding. These include:
- Laser Source or Ultrasonic Generator: The core of the machine, responsible for generating the energy needed for welding.
- Welding Head: The part that directs the energy to the specific area where the weld is required.
- Control System: A sophisticated software and hardware setup that manages the welding parameters, ensuring accuracy and repeatability.
- Cooling System: Essential for maintaining the machine’s temperature during operation, preventing overheating and ensuring consistent performance.
- Feeding Mechanism: Automates the process of aligning and positioning the battery components for welding, enhancing efficiency and reducing human error.
The Welding Process in Lithium Battery Manufacturing
The welding process in lithium battery manufacturing is a critical step that ensures the integrity and performance of the final product. Here’s a step-by-step breakdown of how it typically works:
- Preparation: The battery components, such as electrodes and tabs, are cleaned and prepared to ensure a clean welding surface.
- Alignment: The components are precisely aligned using automated feeding mechanisms or robotic arms.
- Welding: The welding machine applies the appropriate energy (laser, ultrasonic, or resistance) to fuse the components together.
- Inspection: The welded joints are inspected for quality, using techniques such as visual inspection, X-ray, or ultrasonic testing.
- Post-Processing: Any necessary finishing touches, such as trimming or coating, are applied to the welded components.
Applications of Lithium Battery Welding Machines in Different Industries
Lithium battery welding machines are indispensable in various industries due to their ability to produce high-quality, reliable batteries. Some of the key applications include:
- Consumer Electronics: Used in the production of batteries for smartphones, laptops, and other portable devices, where precision and reliability are paramount.
- Electric Vehicles (EVs): Essential for manufacturing the large battery packs required for EVs, ensuring they can deliver the necessary power and range.
- Energy Storage Systems: Critical for creating batteries used in renewable energy storage, such as solar and wind power systems, where durability and efficiency are crucial.
- Medical Devices: Employed in the production of batteries for medical equipment, where safety and reliability are non-negotiable.
- Aerospace: Used in the manufacturing of batteries for satellites and other aerospace applications, where performance under extreme conditions is required.
By understanding the intricacies of lithium battery welding machines, industries can leverage their capabilities to produce batteries that meet the highest standards of quality and performance.
What Makes a Good Lithium Battery Welding Machine?
A good lithium battery welding machine is defined by its precision, reliability, and adaptability. Key characteristics include:
- High Precision: The machine must deliver consistent and accurate welds to ensure the integrity of battery connections, which are critical for performance and safety.
- Advanced Technology: Features like laser welding or ultrasonic welding capabilities ensure clean, strong, and efficient welds.
- User-Friendly Interface: Intuitive controls and software make it easier for operators to set parameters and monitor the welding process.
- Durability: Built with high-quality materials to withstand continuous use in industrial environments.
- Energy Efficiency: Optimized energy consumption reduces operational costs and environmental impact.
- Safety Features: Built-in safety mechanisms, such as temperature control and emergency stop functions, protect both the operator and the equipment.
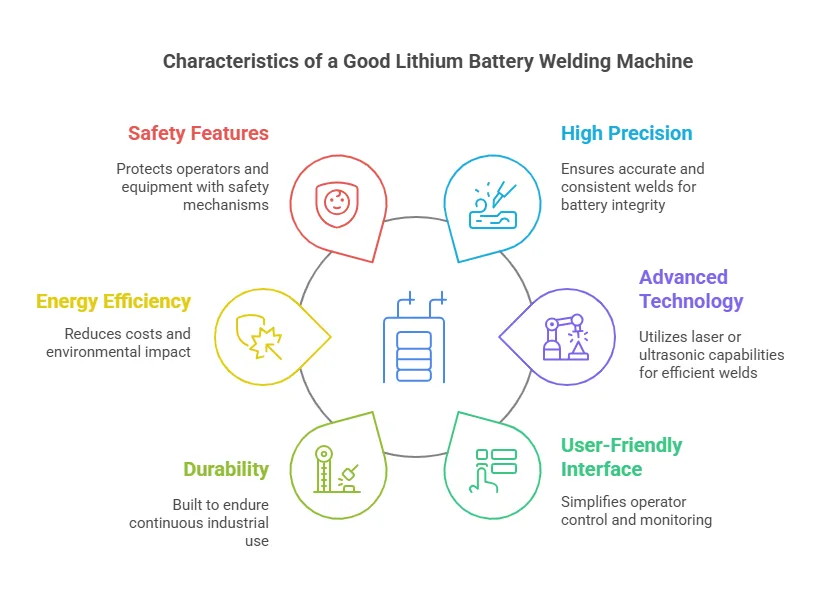
A good welding machine should also be compatible with various battery designs and materials, ensuring versatility across different manufacturing needs.
How to Choose the Right Welding Machine for Lithium Batteries
Selecting the right welding machine for lithium batteries requires careful consideration of several factors:
-
Type of Welding Technology:
- Laser Welding: Ideal for high-precision applications and thin materials.
- Ultrasonic Welding: Suitable for bonding dissimilar materials without heat.
- Resistance Welding: Best for high-volume production with consistent results.
-
Production Requirements:
- Determine the scale of production (small-scale vs. large-scale) and choose a machine that matches your output needs.
- Consider the size and complexity of the batteries you are manufacturing.
-
Material Compatibility:
- Ensure the machine can handle the specific materials used in your batteries, such as copper, aluminum, or nickel.
-
Automation Level:
- For high efficiency, consider machines with automated feeding systems and robotic integration.
-
Budget and ROI:
- Balance the initial investment with long-term benefits, such as reduced maintenance costs and increased productivity.
-
Supplier Reputation:
- Choose a reputable manufacturer with a track record of providing reliable and high-quality welding machines.
Factors Affecting the Performance of a Lithium Battery Welding Machine
Several factors can influence the performance of a lithium battery welding machine:
- Welding Parameters: Incorrect settings for power, speed, or pressure can lead to weak or inconsistent welds.
- Material Quality: Poor-quality materials or contaminants on the surface can hinder the welding process.
- Machine Calibration: Regular calibration is essential to maintain precision and accuracy.
- Environmental Conditions: Factors like humidity, temperature, and dust can affect the machine’s performance.
- Operator Skill: Proper training is crucial to ensure the machine is used correctly and efficiently.
- Maintenance Practices: Neglecting routine maintenance can lead to decreased performance and frequent breakdowns.
By addressing these factors, manufacturers can optimize the performance of their welding machines and ensure high-quality battery production.
Safety Precautions When Operating a Lithium Battery Welding Machine
Operating a lithium battery welding machine requires strict adherence to safety protocols to prevent accidents and ensure smooth operations. Key precautions include:
-
Personal Protective Equipment (PPE):
- Wear safety goggles, gloves, and protective clothing to shield against sparks, heat, and radiation.
-
Machine Inspection:
- Check the machine for any damage or malfunctions before starting operations.
-
Proper Ventilation:
- Ensure the workspace is well-ventilated to avoid inhaling fumes or gases produced during welding.
-
Fire Safety:
- Keep fire extinguishers nearby and avoid flammable materials in the welding area.
-
Training:
- Only trained personnel should operate the machine to minimize the risk of errors or accidents.
-
Emergency Procedures:
- Familiarize yourself with emergency stop buttons and evacuation routes in case of an incident.
-
Regular Maintenance:
- Schedule routine maintenance to prevent equipment failure and ensure safe operation.
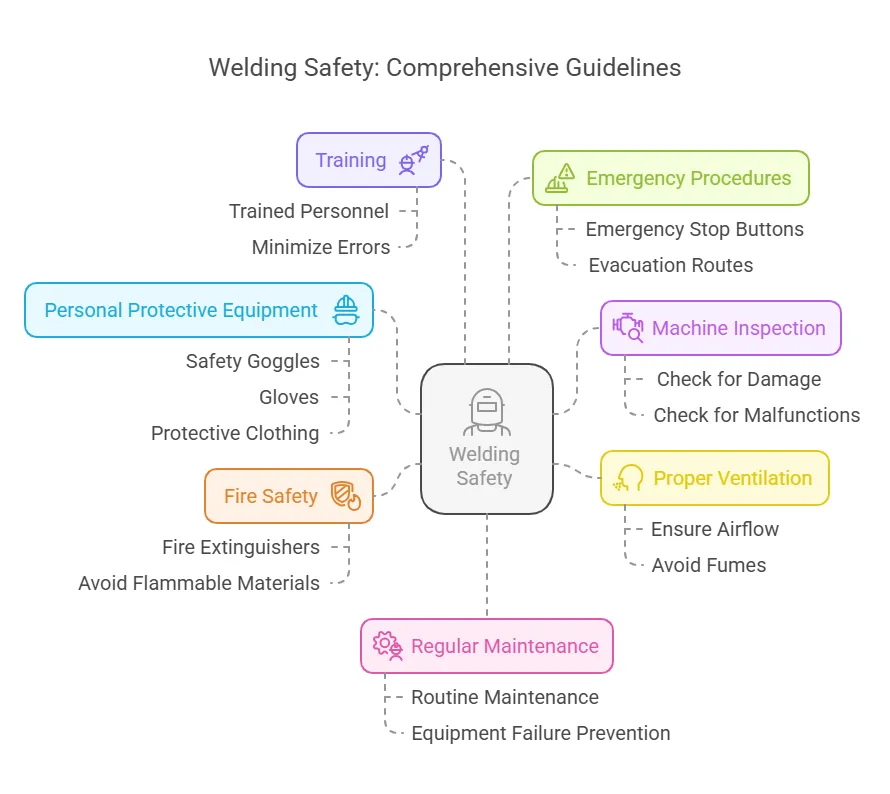
Maintenance and Troubleshooting Tips for Lithium Battery Welding Machines
Proper maintenance and timely troubleshooting are essential to keep a lithium battery welding machine running efficiently. Here’s a step-by-step guide:
Maintenance Tips:
-
Daily Checks:
- Inspect the welding head, cables, and connections for wear or damage.
- Clean the machine to remove dust and debris.
-
Weekly Maintenance:
- Lubricate moving parts to reduce friction and prevent wear.
- Check and tighten any loose bolts or screws.
-
Monthly Maintenance:
- Calibrate the machine to ensure accurate welding parameters.
- Replace worn-out components, such as electrodes or nozzles.
-
Annual Servicing:
- Conduct a thorough inspection of the entire machine.
- Replace any outdated or malfunctioning parts.
Troubleshooting Tips:
-
Weak Welds:
- Check and adjust the welding parameters (power, speed, pressure).
- Inspect the materials for contamination or poor quality.
-
Machine Not Starting:
- Verify the power supply and connections.
- Check for tripped circuit breakers or blown fuses.
-
Overheating:
- Ensure the cooling system is functioning properly.
- Reduce the workload or allow the machine to cool down.
-
Inconsistent Welds:
- Recalibrate the machine.
- Inspect the alignment of the components being welded.
By following these maintenance and troubleshooting tips, operators can extend the lifespan of their welding machines and minimize downtime.
This article offers a comprehensive look at the lithium battery welding machine, a vital tool in the production of high-quality lithium-ion batteries. These machines use advanced techniques like laser, ultrasonic, or resistance welding to create precise and durable connections within batteries. Key components include the laser source or ultrasonic generator, welding head, control system, cooling system, and feeding mechanism. The welding process involves preparation, alignment, welding, inspection, and post-processing to ensure consistent and reliable results. These machines are widely used in consumer electronics, electric vehicles, energy storage systems, medical devices, and aerospace applications. A good welding machine is characterized by precision, advanced technology, user-friendliness, durability, energy efficiency, and safety features. Choosing the right machine involves considering welding technology, production scale, material compatibility, automation level, budget, and supplier reputation. Factors affecting performance include welding parameters, material quality, machine calibration, environmental conditions, operator skill, and maintenance practices. Safety precautions and regular maintenance are crucial for optimal performance and longevity.