In the heart of modern technology lies the lithium-ion battery, a marvel of engineering that powers our daily lives. But what goes into the manufacturing of these energy-dense powerhouses? This blog takes you on a journey through the intricate world of lithium-ion battery assembly, where precision meets innovation. From the meticulous preparation of electrodes to the rigorous testing that ensures safety and longevity, we explore the key stages that bring these batteries to life. Join us as we uncover the secrets behind the assembly process, the critical components involved, and the stringent safety standards that make lithium-ion batteries the backbone of our electrified future.
What Is Lithium-Ion Battery Manufacturing?
Lithium-ion battery manufacturing is the process of producing rechargeable batteries that power modern devices like smartphones, EVs, and grid storage systems. The industry has grown exponentially due to high energy density, longevity, and efficiency demands.
Key Stages of Production:
-
Electrode Preparation:
- Anode: Typically graphite-coated copper foil.
- Cathode: Lithium metal oxides (e.g., NMC, LFP) on aluminum foil.
-
Cell Assembly:
- Electrodes are separated by a porous polymer separator soaked in electrolyte.
- Stacked (prismatic/pouch) or wound (cylindrical) into cells.
-
Formation & Testing:
- Initial charge/discharge cycles activate electrochemical properties.
- Quality checks for capacity, leakage, and thermal stability.
Why It Matters:
Manufacturing precision directly impacts battery performance and safety, making process control critical for industries like automotive and aerospace.
Lithium-Ion Battery Cell Structure and Key Components
What’s Inside a Li-ion Cell?
- Cathode: Determines capacity/voltage (e.g., LiCoO₂ for high energy).
- Anode: Graphite or silicon-based materials for ion storage.
- Electrolyte: Liquid/polymer facilitating ion movement between electrodes.
- Separator: Prevents short circuits while allowing ion flow.
Why Materials Matter:
- Cathode choice affects cost (LFP vs. NCA) and thermal runaway risks.
- Nano-engineered anodes (e.g., silicon blends) boost energy density by 20–40%.
How Components Interact:
During charging, lithium ions move from cathode to anode; discharging reverses the flow, generating electricity.
How Lithium-Ion Batteries Work: Electrochemical Reactions Explained
Step-by-Step Energy Storage Process:
-
Charging Phase:
- External voltage pushes lithium ions from cathode to anode.
- Electrons flow via external circuit (e.g., charger).
- Anode reaction: Li⁺ + e⁻ + C₆ → LiC₆ (lithium intercalation).
-
Discharging Phase:
- Ions return to cathode through electrolyte.
- Electrons power connected devices.
- Cathode reaction: LiCoO₂ → Li₁₋ₓCoO₂ + xLi⁺ + xe⁻.
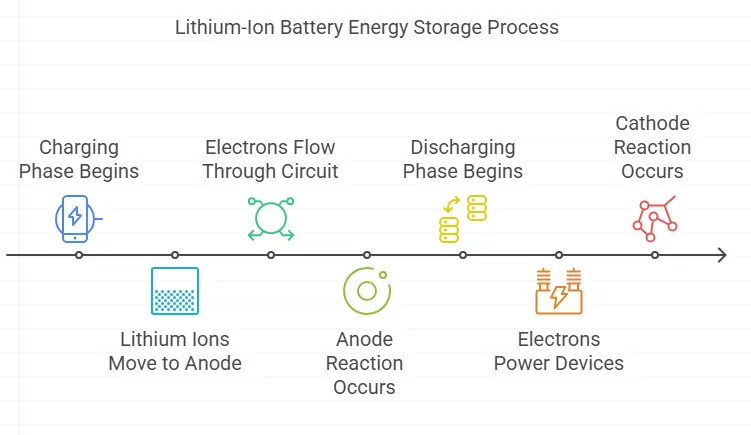
Why Efficiency Varies:
- Voltage hysteresis and side reactions (e.g., SEI layer formation) reduce usable capacity over time.
Lithium-Ion Battery Applications in EVs, Consumer Electronics, and Energy Storage
Where Are They Used?
-
Electric Vehicles:
- High-energy NMC/NCA batteries for longer range (e.g., Tesla’s 4680 cells).
- Fast-charging requires advanced thermal management.
-
Consumer Electronics:
- LCO (LiCoO₂) in smartphones for compact size.
- Polymer electrolytes enable flexible designs (e.g., wearables).
-
Grid Storage:
- LFP batteries dominate due to safety and 10,000+ cycle life.
Why Growth Is Explosive:
Global demand for EVs (projected 26M annual sales by 2030) and renewable integration drive innovation.
Safety Standards and Certifications in Battery Manufacturing Plants
How Factories Mitigate Risks:
-
Step-by-Step Safety Protocols:
-
Material Handling:
- Dry rooms (<1% humidity) prevent electrolyte reactions.
-
Assembly:
- Inert gas (argon) filling reduces combustion risks.
-
Testing:
- UN38.3 (transport), IEC 62133 (consumer), and UL 2580 (EV) certifications mandatory.
-
Material Handling:
Why Compliance Is Non-Negotiable:
- Thermal runaway incidents (e.g., Samsung Note 7) highlight need for:
- Flame-retardant additives.
- Pressure vents in cylindrical cells.
Key Certifications:
- ISO 9001 (quality management), ISO 14001 (environmental), and regional standards like GB/T (China).
Key Testing Stages in Lithium-ion Battery Manufacturing (OCV, IR, Aging, Cycle Tests)
Why Testing Is Critical
Defective batteries can cause thermal runaway, making rigorous testing non-negotiable for safety and performance.
Step-by-Step Testing Protocol:
-
Open Circuit Voltage (OCV) Test:
- What: Measures voltage without load.
- Why: Identifies cell imbalances (>10mV deviation = reject).
-
Internal Resistance (IR) Test:
- How: Applies AC/DC current to measure opposition to flow.
- Standard: <100mΩ for 18650 cells (higher = risk of overheating).
-
Aging Test:
- Procedure: Stores cells at 45°C/80% SOC for 7 days.
- Pass Criteria: Capacity loss <5%.
-
Cycle Life Test:
- Method: Charges/discharges 1,000+ times (80% capacity retention = industry benchmark).
Emerging Tools:
AI-powered predictive models now correlate test data with field failure rates (e.g., Tesla’s in-house analytics).
How Manufacturing Decisions Affect Battery Safety and Longevity
What Factors Matter Most?
-
Electrode Coating Uniformity:
- Impact: ±2μm variation reduces cycle life by 15%.
- Solution: Laser thickness gauges with real-time adjustments.
-
Moisture Control:
- Why: H₂O + LiPF₆ electrolyte → HF gas (toxic).
- Standard: <20ppm dew point in dry rooms.
Material Selection Trade-offs:
Parameter | Safety-First Choice | Cost-First Choice |
---|---|---|
Cathode | LiFePO₄ (LFP) | NMC 811 |
Separator | Ceramic-coated PE | Standard PE |
Electrolyte | Additive-rich (VC/FEC) | Basic LiPF₆ |
Case Study:
GM’s Ultium cells use 100% ultrasonic welding (vs laser) to minimize particle generation that could puncture separators.
How to Maintain Lithium-ion Battery Manufacturing Equipment
Critical Maintenance Checklist:
Daily:
- Calibrate slurry viscosity sensors (±5% tolerance).
- Clean electrode coater nozzles (prevent clogging → coating defects).
Weekly:
- Degas electrolyte filling systems (avoid air bubbles in cells).
- Inspect welding heads for carbon buildup (affects joint resistance).
Monthly:
- Replace HEPA filters in dry rooms (ISO Class 5 required).
- Validate glovebox oxygen levels (<10ppm for moisture-sensitive processes).
Why Predictive Maintenance Wins:
Vibration sensors on winding machines can detect bearing wear 3 weeks before failure (saving $50k/hour in downtime).
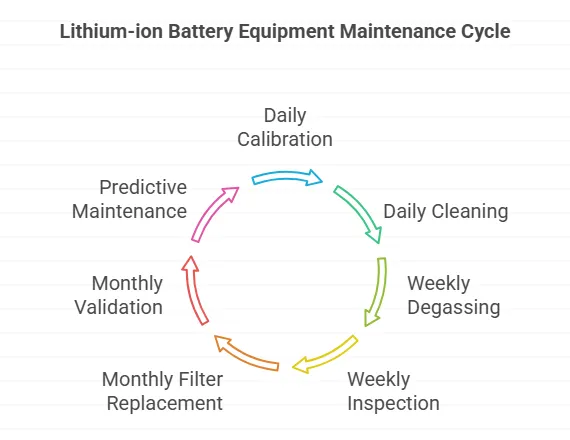
Lithium-ion Battery Manufacturing Costs and How to Reduce Them
Cost Breakdown (Per 1kWh Cell):
- Cathode: $82 (43%)
- Anode: $28 (15%)
- Separator: $15 (8%)
- Assembly: $65 (34%)
5 Proven Cost-Reduction Strategies:
-
Localize Supply Chains:
- CATL cuts 12% costs by sourcing lithium from Chinese brine lakes vs Australian imports.
-
Thicker Electrodes:
- 200μm coatings (vs 150μm) reduce stacking labor by 25% (but require advanced calendering).
-
Dry Electrode Process:
- Tesla’s acquisition of Maxwell Tech eliminates solvent drying ($3/kWh savings).
-
Recycled Materials:
- Redwood Materials’ cathode scrap reuse lowers nickel costs by 30%.
-
AI-Optimized Energy Use:
- Siemens’ machine learning reduces furnace power consumption by 18%.
Hidden Savings:
Automated optical inspection (AOI) reduces scrap rates from 5% to 0.7% at Panasonic’s Nevada Gigafactory.
This in-depth article delves into the complexities of lithium-ion battery manufacturing, focusing on the assembly process that transforms raw materials into high-performance cells. We walk through the key stages, from electrode preparation and cell assembly to formation and testing, highlighting the importance of precision and quality control. We also examine the critical components—cathode, anode, electrolyte, and separator—exploring how material choices impact performance, cost, and safety. Additionally, we discuss the essential safety standards and certifications that manufacturing plants must meet, as well as emerging trends and cost-reduction strategies shaping the industry. Whether you’re a tech enthusiast or a professional in the field, this article provides a comprehensive look at the art and science of lithium-ion battery assembly.