In the rapidly evolving world of battery technology, the cylindrical cell assembly machine stands out as a linchpin of modern manufacturing. Designed to automate the production of cylindrical battery cells, these machines are essential for industries ranging from electric vehicles to consumer electronics and energy storage systems. By integrating advanced automation and precision engineering, cylindrical cell assembly machines ensure that each battery cell is assembled with unparalleled accuracy and consistency. From electrode winding to electrolyte filling and final sealing, these machines handle every step with meticulous care. In this blog, we will delve into the inner workings of cylindrical cell assembly machines, exploring their key components, workflow, and the advanced technologies that drive their efficiency. We’ll also examine their wide-ranging applications and the critical role they play in powering the future of sustainable energy.
What is a Cylindrical Cell Assembly Machine?
A cylindrical cell assembly machine is a specialized piece of equipment designed for the automated production of cylindrical battery cells, which are commonly used in various applications such as electric vehicles, consumer electronics, and energy storage systems. This machine plays a crucial role in the battery manufacturing process by ensuring precision, efficiency, and consistency in assembling the components of a cylindrical cell, including the cathode, anode, separator, and electrolyte.
The machine is engineered to handle the delicate and intricate processes involved in battery assembly, such as electrode winding, tab welding, and cell sealing. By automating these tasks, it significantly reduces the risk of human error, enhances production speed, and maintains high-quality standards. As the demand for high-performance batteries continues to grow, the cylindrical cell assembly machine has become an indispensable tool in modern battery manufacturing facilities.
Product Structure and Key Components
The cylindrical cell assembly machine is composed of several critical components that work together to ensure seamless operation. Here’s a breakdown of its structure:
- Feeding System: This component is responsible for supplying the raw materials, such as electrode sheets and separators, to the assembly line. It ensures a continuous and consistent flow of materials.
- Winding Mechanism: The heart of the machine, this mechanism precisely winds the cathode, anode, and separator into a cylindrical shape. It is equipped with advanced sensors to maintain tight tolerances.
- Tab Welding Unit: This unit connects the electrode tabs to the cell casing using laser or ultrasonic welding technology, ensuring a strong and reliable electrical connection.
- Electrolyte Filling System: This system accurately dispenses the electrolyte into the cell, which is essential for the battery’s electrochemical performance.
- Sealing Module: After filling, the cell is sealed to prevent leakage and contamination. This module uses advanced techniques like crimping or laser welding to ensure a hermetic seal.
- Control System: The brain of the machine, this system integrates sensors, actuators, and software to monitor and control every step of the assembly process, ensuring precision and efficiency.
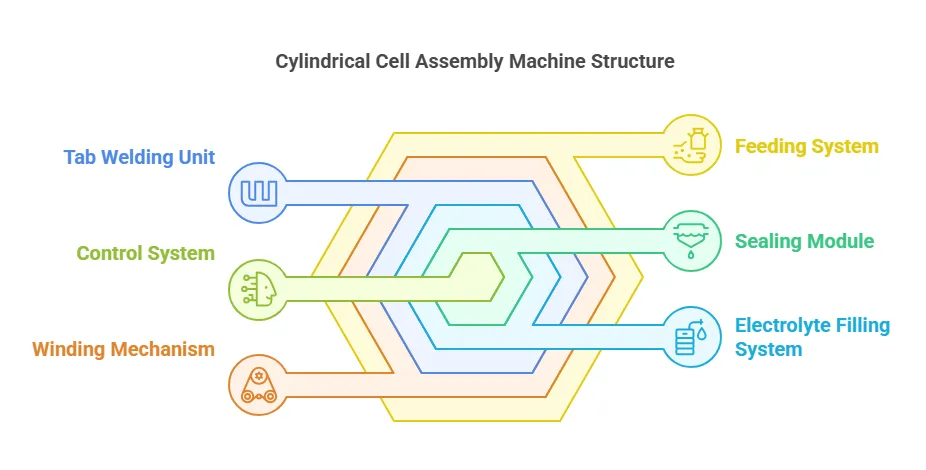
How Does the Workflow and Assembly Process Work?
The workflow of a cylindrical cell assembly machine is a meticulously designed sequence of steps that ensures the efficient production of high-quality battery cells. Here’s a step-by-step overview:
- Material Feeding: Electrode sheets and separators are fed into the machine from rolls, ensuring a continuous supply.
- Electrode Winding: The cathode, anode, and separator are wound together into a cylindrical shape using a precision winding mechanism.
- Tab Welding: The electrode tabs are welded to the cell casing to establish electrical connections.
- Electrolyte Filling: The wound cell is filled with a precise amount of electrolyte, which is critical for the battery’s performance.
- Cell Sealing: The cell is sealed to prevent electrolyte leakage and ensure long-term reliability.
- Quality Inspection: Automated inspection systems check for defects, such as improper winding, welding, or sealing, ensuring only high-quality cells proceed to the next stage.
- Output: The finished cylindrical cells are collected and prepared for further processing or packaging.
Working Principle and Automation Technology
The working principle of a cylindrical cell assembly machine revolves around automation and precision engineering. The machine leverages advanced technologies such as robotics, computer vision, and artificial intelligence to perform complex tasks with high accuracy and repeatability.
- Robotics: Robotic arms handle tasks like electrode winding and tab welding, ensuring consistent quality and reducing human intervention.
- Computer Vision: High-resolution cameras and image processing algorithms inspect components and assemblies in real-time, detecting defects and ensuring compliance with quality standards.
- Artificial Intelligence: AI algorithms optimize the assembly process by analyzing data from sensors and making real-time adjustments to improve efficiency and reduce waste.
- PLC Control: Programmable Logic Controllers (PLCs) manage the machine’s operations, ensuring synchronization between different components and processes.
By integrating these technologies, the cylindrical cell assembly machine achieves high levels of automation, making it a cornerstone of modern battery manufacturing.
Application Scope and Industry Use Cases
Cylindrical cell assembly machines are widely used across various industries due to their versatility and efficiency. Here are some key applications:
- Electric Vehicles (EVs): Cylindrical cells are a popular choice for EV batteries due to their high energy density and durability. The assembly machine ensures the mass production of reliable cells for this rapidly growing industry.
- Consumer Electronics: Devices like laptops, smartphones, and power tools rely on cylindrical cells for their compact size and long-lasting performance. The machine enables the production of cells that meet the stringent quality requirements of these applications.
- Energy Storage Systems: Cylindrical cells are used in large-scale energy storage systems for renewable energy integration and grid stabilization. The assembly machine supports the production of cells that can withstand harsh operating conditions.
- Medical Devices: Portable medical devices, such as insulin pumps and diagnostic equipment, often use cylindrical cells. The machine ensures the production of safe and reliable cells for these critical applications.
- Aerospace: Cylindrical cells are used in satellites and other aerospace applications where reliability and performance are paramount. The assembly machine delivers cells that meet the rigorous standards of the aerospace industry.
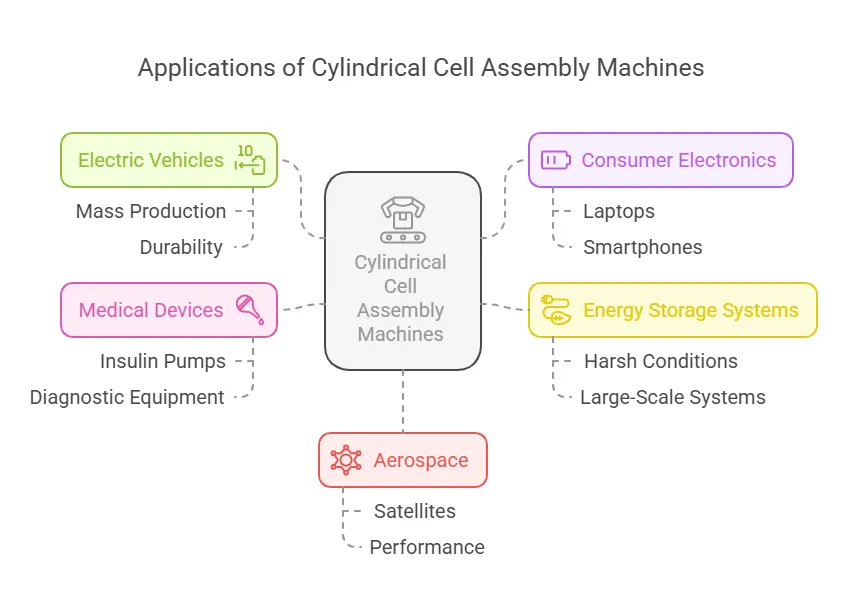
By catering to these diverse industries, the cylindrical cell assembly machine plays a vital role in advancing technology and supporting the global transition to clean energy.
What is the Ideal Work Environment and Operating Conditions for a Cylindrical Cell Assembly Machine?
To ensure optimal performance and longevity of a cylindrical cell assembly machine, it is crucial to operate it in an ideal work environment. The machine should be placed in a clean, dust-free, and temperature-controlled area. Excessive humidity or temperature fluctuations can negatively impact the precision of the assembly process. Additionally, the workspace should be well-ventilated to prevent the accumulation of harmful fumes or gases that may be emitted during battery production.
Why does the environment matter? A stable environment minimizes the risk of mechanical failures and ensures consistent product quality. For example, high humidity can cause corrosion in sensitive components, while extreme temperatures may affect the viscosity of adhesives or electrolytes used in the assembly process.
How can you create the ideal environment? Follow these steps:
- Install air conditioning or climate control systems to maintain a temperature range of 20-25°C
- Use dehumidifiers to keep humidity levels below 50%.
- Implement a regular cleaning schedule to prevent dust buildup.
- Ensure proper ventilation to dissipate any chemical vapors.
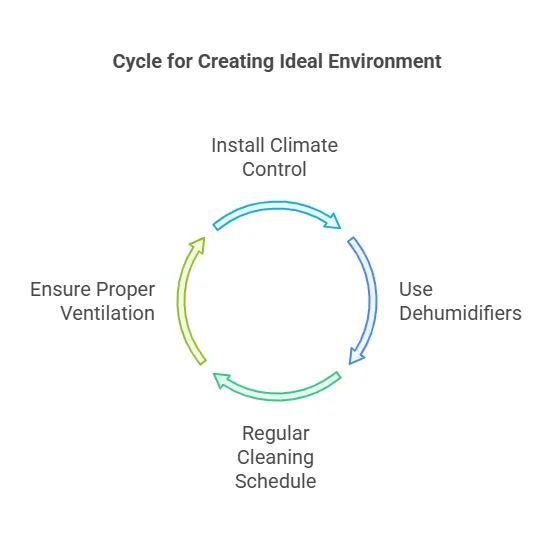
By maintaining these conditions, you can maximize the efficiency and lifespan of your cylindrical cell assembly machine.
Why is Product Testing and Quality Control Essential for Cylindrical Cell Assembly Machines?
Product testing and quality control are critical steps in the battery manufacturing process. A cylindrical cell assembly machine must produce cells that meet stringent safety and performance standards. Without rigorous testing, defects such as short circuits, leaks, or insufficient capacity may go unnoticed, leading to product recalls or safety hazards.
How is quality control implemented?
- Step 1: In-line Inspection – Use sensors and cameras to monitor the assembly process in real-time, detecting anomalies like misaligned components or improper sealing.
- Step 2: Electrical Testing – Conduct tests to measure voltage, resistance, and capacity to ensure each cell meets specifications.
- Step 3: Stress Testing – Subject samples to extreme conditions (e.g., high temperatures, rapid charging) to evaluate durability and safety.
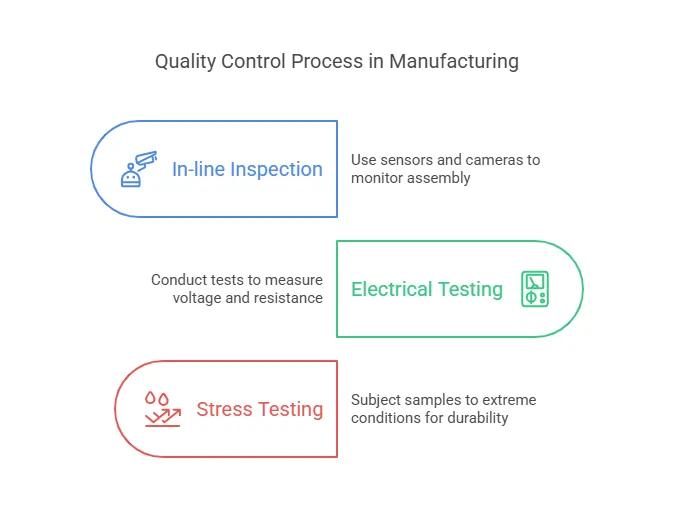
Why invest in quality control? It not only ensures compliance with industry standards but also builds trust with customers by delivering reliable and high-performing batteries.
What Are the Key Usage Precautions and Safety Measures for Cylindrical Cell Assembly Machines?
Operating a cylindrical cell assembly machine requires strict adherence to safety protocols to prevent accidents and ensure smooth operation. These machines handle sensitive materials like electrolytes and electrodes, which can be hazardous if mishandled.
Key precautions include:
- Wear Protective Gear: Operators should wear gloves, goggles, and lab coats to protect against chemical exposure.
- Avoid Static Electricity: Use anti-static mats and wrist straps to prevent sparks that could ignite flammable materials.
- Regular Training: Ensure all operators are trained in emergency procedures and machine operation.
Why are these measures important? They reduce the risk of fires, chemical spills, and injuries, creating a safer workplace and minimizing downtime.
How to Maintain and Care for Your Cylindrical Cell Assembly Machine
Proper maintenance is essential to keep your cylindrical cell assembly machine running efficiently. Neglecting maintenance can lead to costly repairs and production delays.
Step-by-step maintenance guide:
- Daily Checks: Inspect for loose bolts, worn-out belts, or unusual noises.
- Weekly Cleaning: Remove dust and debris from moving parts and sensors.
- Monthly Lubrication: Apply lubricant to gears and bearings to reduce friction.
- Quarterly Calibration: Verify the accuracy of alignment and pressure settings.
Why is maintenance important? It prevents unexpected breakdowns, extends the machine’s lifespan, and ensures consistent output quality.
What Innovations and Future Trends Are Shaping Cylindrical Cell Assembly Machines?
The battery industry is rapidly evolving, and cylindrical cell assembly machines are at the forefront of this transformation. Innovations such as AI-driven automation, advanced laser welding, and modular designs are revolutionizing the way batteries are produced.
Why are these trends significant?
- AI Automation: Enhances precision and reduces human error.
- Laser Welding: Improves joint strength and minimizes heat damage.
- Modular Designs: Allow for easier upgrades and customization.
How will these advancements impact the industry? They will enable faster production, higher energy densities, and more sustainable manufacturing processes, meeting the growing demand for electric vehicles and renewable energy storage.
How Does Cylindrical Cell Assembly Technology Compare with Other Battery Assembly Technologies?
Cylindrical cell assembly machines offer several advantages over other battery assembly methods, such as prismatic or pouch cell technologies.
Key comparisons:
Energy Density: Cylindrical cells typically have higher energy density due to their compact design.
Thermal Management: The cylindrical shape allows for better heat dissipation compared to pouch cells.
Manufacturing Speed: Automated cylindrical cell assembly machines can produce cells faster than manual or semi-automated prismatic cell lines.
Why choose cylindrical cell assembly? It is a proven, scalable, and cost-effective solution for high-volume battery production, making it a preferred choice for industries like electric vehicles and consumer electronics.
Cylindrical cell assembly machines are specialized systems designed to automate the production of cylindrical battery cells, ensuring precision, efficiency, and consistency. These machines are composed of several key components, including a feeding system, winding mechanism, tab welding unit, electrolyte filling system, and sealing module. The workflow involves a series of coordinated steps, from material feeding and electrode winding to electrolyte filling and quality inspection. By leveraging advanced technologies such as robotics, computer vision, and AI, these machines achieve high levels of automation, reducing human error and increasing production speed. Cylindrical cell assembly machines are widely used in electric vehicles, consumer electronics, energy storage systems, industrial equipment, and medical devices. Their ability to produce high-quality battery cells with long-term reliability makes them an indispensable tool in modern battery manufacturing, supporting the global transition to clean energy and advanced technology.