Introduction
The battery pack assembly process is a cornerstone of modern manufacturing, essential for producing high-performance battery packs used in electric vehicles (EVs), portable electronics, and renewable energy systems. This intricate process combines precision engineering, advanced technologies, and stringent safety protocols to ensure the final product meets the demands of today’s energy-driven world. From sourcing raw materials to integrating sophisticated battery management systems (BMS), each step in the assembly process plays a critical role in determining the pack’s performance, safety, and longevity.
What is the Battery Pack Assembly Process?
The battery pack assembly process is a meticulously planned sequence of steps that transforms individual components into a fully functional battery pack. It begins with the procurement of high-quality materials, including battery cells, BMS, wiring, and protective casings. These components are then assembled in a controlled environment to ensure precision and safety. The process involves connecting battery cells in specific configurations (series or parallel) to achieve the desired voltage and capacity, integrating the BMS for performance monitoring, and encasing the assembly in a durable, thermally efficient enclosure. Each stage is governed by strict industry standards to guarantee the pack’s reliability, safety, and compliance with regulatory requirements.
Why is Battery Pack Assembly Important?
The significance of the battery pack assembly process lies in its direct impact on the performance and safety of the final product. A well-assembled battery pack ensures optimal energy storage, efficient power delivery, and long-term durability. Conversely, errors in assembly can lead to catastrophic failures, such as overheating, leakage, or even fires, posing risks to users and the environment. As the demand for high-capacity batteries surges—particularly in EVs and renewable energy systems—manufacturers must prioritize precision and quality control. Advanced automation and specialized equipment are increasingly employed to enhance efficiency, reduce human error, and meet the growing production demands of a rapidly evolving industry.
How is a Battery Pack Assembled? Step-by-Step Process
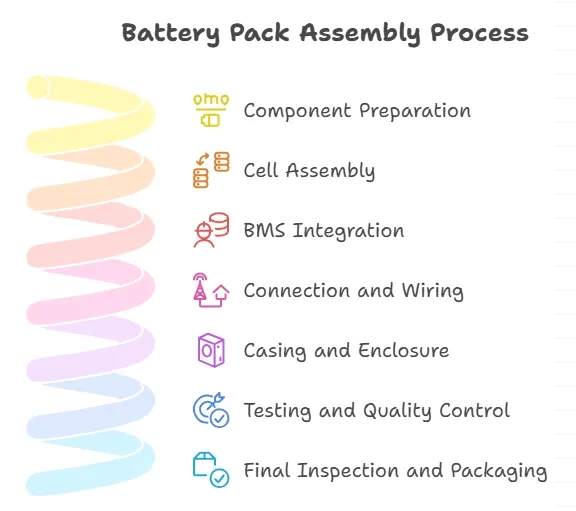
- Component Preparation: High-quality battery cells, BMS, wiring, and casings are inspected and prepared for assembly.
- Cell Assembly: Battery cells are arranged in series or parallel configurations to achieve the required voltage and capacity.
- BMS Integration: The BMS is installed to monitor voltage, temperature, and charging cycles, ensuring safe operation.
- Connection and Wiring: Cells and BMS are connected using precise wiring to prevent power loss or safety hazards.
- Casing and Enclosure: The assembled components are housed in a protective casing, often equipped with thermal management systems.
- Testing and Quality Control: The pack undergoes rigorous testing for performance, safety, and durability.
- Final Inspection and Packaging: Approved packs are inspected, packaged, and prepared for shipment.
What are the Key Applications of Battery Packs?
Battery packs are integral to numerous industries, each with unique power requirements:
- Electric Vehicles (EVs): High-energy-density packs power EVs, enabling long-range travel and fast charging.
- Portable Electronics: Compact, lightweight packs provide reliable energy for smartphones, laptops, and wearables.
- Energy Storage Systems: Large-scale packs store renewable energy for grid stabilization and off-grid applications.
- Renewable Energy: Battery packs support solar and wind energy systems, ensuring consistent power supply.
How is Quality Control Ensured During Battery Pack Assembly?
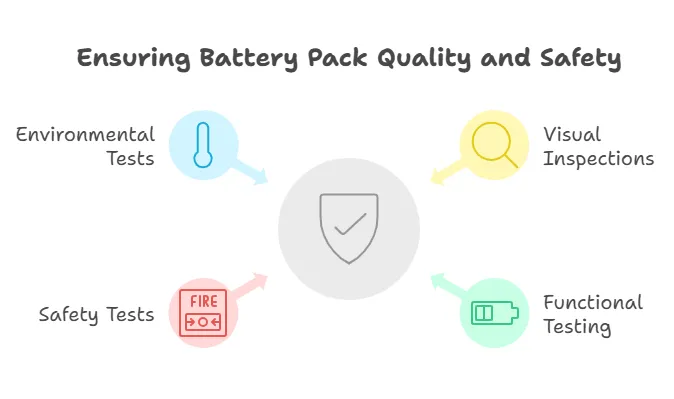
Quality control is paramount in battery pack assembly to prevent defects and ensure safety. Key measures include:
- Visual Inspections: Checking for physical defects like damaged cells or faulty wiring.
- Functional Testing: Verifying electrical properties such as voltage, capacity, and charging cycles.
- Safety Tests: Conducting overcharge, short-circuit, and thermal stability tests.
- Environmental Tests: Evaluating performance under extreme temperatures and humidity.
How is a Battery Pack Assembled? A Step-by-Step Breakdown
Assembling a battery pack involves several critical steps to ensure its performance and safety:
Component Preparation
The first step involves gathering and inspecting all necessary components, such as battery cells, the Battery Management System (BMS), wiring, connectors, and casings. This ensures that only high-quality, defect-free parts are used.
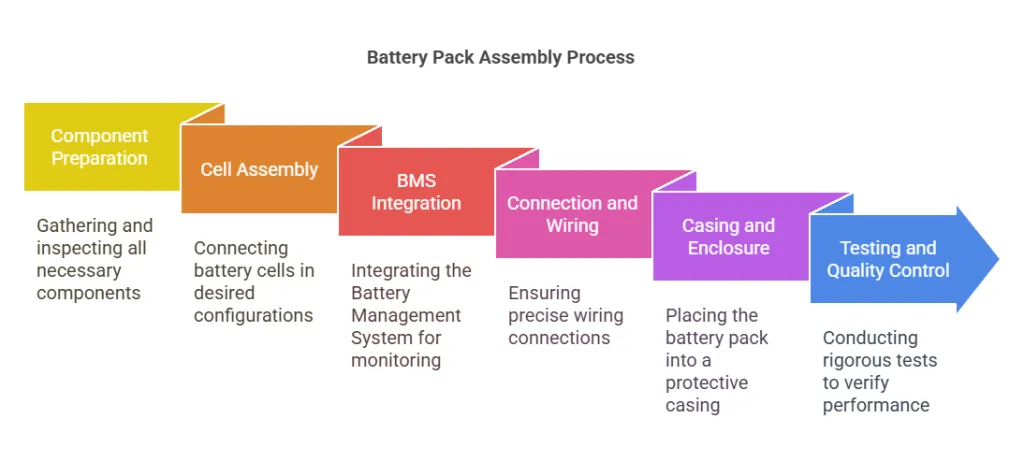
Cell Assembly
Battery cells are then connected in series or parallel configurations, depending on the desired voltage and capacity of the final pack. Proper cell arrangement is essential for optimal performance.
BMS Integration
The BMS, which monitors the health and performance of the battery pack, is integrated into the assembly. This system tracks key parameters like voltage, temperature, and charging cycles to ensure safe operation.
Connection and Wiring
The cells and BMS are connected using precise wiring. This step ensures there are no loose connections that could lead to power loss or safety issues.
Casing and Enclosure
Once the components are connected, the battery pack is placed into a protective casing. This not only provides physical protection but may also include thermal management systems to prevent overheating.
Testing and Quality Control
The battery pack undergoes rigorous testing to verify its performance, including checks for voltage, capacity, and safety features. Any faulty units are rejected and sent back for reassembly.
What are the Key Applications of Battery Packs?
Battery packs play a crucial role across various industries, where reliable power storage and management are essential. Here are some of the most prominent applications:
Electric Vehicles (EVs)
Battery packs are the heart of electric vehicles, powering the motor and all onboard electrical systems. They are designed to offer high energy density, long lifespan, and fast charging capabilities, enabling efficient and sustainable transportation.
Portable Electronics
From smartphones and laptops to tablets and wearables, compact and lightweight battery packs are critical. These packs provide reliable power while maintaining the sleek and portable design of modern electronic devices.
Energy Storage Systems
Battery packs are integral to large-scale energy storage solutions. They store electricity generated from renewable sources like solar and wind, ensuring a steady supply of power even when the sun isn’t shining or the wind isn’t blowing.
Renewable Energy Applications
In off-grid power systems, battery packs serve as the backbone of sustainable energy solutions. They store excess energy generated by renewable sources, making it available for use during periods of high demand or when the primary energy source is unavailable.
Quality control is a vital aspect of battery pack assembly, especially considering the potential safety risks associated with faulty units. To ensure reliability and safety, manufacturers implement rigorous testing protocols. Key measures include:
Visual Inspections
Workers meticulously inspect each component for physical defects, such as damaged cells, faulty wiring, or improper connections, to ensure only flawless components are used.
Functional Testing
Each battery pack is tested to verify its electrical performance, including voltage output, capacity, and charging cycles. This step ensures the pack meets the required performance standards.
Safety Tests
Battery packs undergo extensive safety evaluations, including overcharge, short-circuit, and thermal stability tests, to ensure they can handle real-world conditions safely.
Environmental Tests
Battery packs are tested under extreme conditions, such as temperature fluctuations and high humidity, to confirm their reliability in diverse environments.
How is Battery Pack Assembly Automation Revolutionizing the Process?
With the growing demand for high-quality battery packs, many manufacturers are adopting automation to enhance the assembly process. Automation offers several key benefits:
Precision
Automated systems perform repetitive tasks with exceptional accuracy, minimizing human error and ensuring consistency across all production batches.
Speed
Automation accelerates the assembly process, enabling manufacturers to meet high production demands while maintaining quality.
Cost Efficiency
Although the initial investment in automated equipment is significant, automation reduces labor costs and lowers defect rates, resulting in long-term cost savings.
Conclusion
The battery pack assembly process is a sophisticated and highly specialized field that underpins the success of modern energy storage solutions. From electric vehicles to renewable energy systems, the demand for high-performance battery packs continues to grow, driving innovations in assembly techniques and quality control. By leveraging advanced technologies, automation, and stringent testing protocols, manufacturers can produce battery packs that are safe, reliable, and efficient. As the industry evolves, a deep understanding of the assembly process will remain crucial for delivering products that meet the rigorous demands of today’s energy landscape. For manufacturers and engineers, mastering this process is not just a technical challenge but a gateway to shaping the future of sustainable energy.
Call to Action
For manufacturers and engineers looking to optimize their battery pack assembly processes, investing in advanced technologies and automation is key. Explore our range of cutting-edge solutions designed to enhance precision, efficiency, and safety in battery production. Contact us today to learn how we can help you meet the growing demands of the energy storage industry.