In the dynamic landscape of modern manufacturing, the mounting machine has emerged as a cornerstone of precision and efficiency. These specialized devices are responsible for securely attaching components to substrates like printed circuit boards (PCBs), ensuring that everything from smartphones to spacecraft operates seamlessly. But what makes a mounting machine so crucial? In this blog, we will explore the inner workings of these remarkable tools, from their key components and operational processes to the diverse industries that rely on them. Whether you’re an engineer, a manufacturer, or simply curious about the technology behind your everyday devices, understanding the role of mounting machines can provide valuable insights into how modern production thrives. Join us as we dive deep into the world of mounting machines and discover how they drive innovation and reliability in manufacturing.
What is a Mounting Machine?
A mounting machine is a specialized piece of equipment designed to securely attach or “mount” components onto a substrate, such as a printed circuit board (PCB). These machines are essential in industries where precision and efficiency are paramount, such as electronics manufacturing, automotive, and aerospace. Mounting machines can handle a variety of tasks, including placing surface-mount devices (SMDs), through-hole components, and even more complex assemblies. They are often automated to ensure high-speed, accurate placement of components, reducing human error and increasing production throughput.
Key Components and Structure of a Mounting Machine
Mounting machines are complex systems composed of several key components that work together to achieve precise component placement. Here are the main parts:
- Feeder System: This component holds and supplies the components to the machine. It can be tape, tray, or stick feeders, depending on the type of components being mounted.
- Pick-and-Place Head: The heart of the machine, this part picks up components from the feeder and places them onto the substrate. It often includes a vacuum nozzle or gripper for handling delicate parts.
- Vision System: High-resolution cameras and sensors ensure that components are correctly aligned and placed. This system is crucial for maintaining accuracy, especially with miniaturized components.
- Conveyor System: This moves the PCBs or other substrates through the machine, ensuring a continuous workflow.
- Control System: The brain of the machine, often a computer or PLC (Programmable Logic Controller), which manages the entire operation, from component picking to placement.
- Nozzle Changer: Some advanced machines have an automatic nozzle changer to handle different component sizes and shapes without manual intervention.
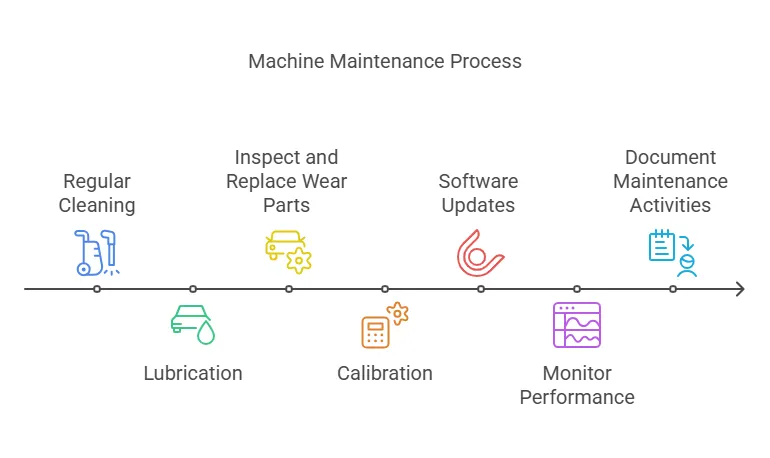
How Does a Mounting Machine Work?
Mounting machines operate through a series of well-coordinated steps to ensure precise component placement. Here’s a step-by-step breakdown of how they work:
- Component Feeding: The feeder system supplies components to the machine. Depending on the type of feeder, components are either rolled out on tape, picked from trays, or fed from sticks.
- Component Picking: The pick-and-place head moves to the feeder location, where it uses a vacuum nozzle or gripper to pick up the component.
- Component Inspection: The vision system inspects the component to ensure it is the correct type and orientation. If any discrepancies are found, the component is rejected.
- Component Placement: The head moves to the designated location on the substrate and places the component with precision. The vision system may perform a final check to ensure accurate placement.
- Substrate Movement: The conveyor system moves the substrate to the next position, ready for the next component to be placed.
- Repeat: The process repeats until all components are placed on the substrate.
Mounting Machine Workflow and Process Steps
The workflow of a mounting machine is designed to maximize efficiency and accuracy. Here’s a detailed look at the process steps:
- Preparation: Load the components into the feeder system and the substrates onto the conveyor.
- Setup: Configure the machine settings, such as component type, placement location, and speed, via the control system.
- Feeding: The feeder system supplies components to the pick-and-place head.
- Picking: The head picks up the component using a vacuum nozzle or gripper.
- Inspection: The vision system checks the component for correct type and orientation.
- Placement: The head places the component onto the substrate at the precise location.
- Verification: The vision system may perform a final check to ensure accurate placement.
- Movement: The conveyor system moves the substrate to the next position.
- Completion: The process repeats until all components are placed, and the substrate is ready for the next stage of production.
Applications of Mounting Machines in Different Industries
Mounting machines are versatile and find applications across various industries. Here are some key sectors where these machines are indispensable:
- Electronics Manufacturing: Mounting machines are crucial for placing components on PCBs in devices like smartphones, computers, and home appliances. They ensure high precision and speed, which are essential for mass production.
- Automotive Industry: In the automotive sector, mounting machines are used to assemble electronic control units (ECUs), sensors, and other critical components. The reliability and accuracy of these machines are vital for vehicle safety and performance.
- Aerospace: The aerospace industry requires extremely high precision and reliability. Mounting machines are used to assemble avionics, sensors, and other electronic components that must withstand harsh conditions.
- Medical Devices: In the medical field, mounting machines are used to assemble devices like pacemakers, imaging equipment, and diagnostic tools. The precision of these machines ensures the reliability and safety of medical devices.
- Consumer Goods: From wearable technology to household appliances, mounting machines play a key role in assembling the electronic components that power modern consumer goods.
- Industrial Equipment: Mounting machines are also used in the production of industrial machinery, where they help assemble control panels, sensors, and other electronic components.
By understanding the various applications and functionalities of mounting machines, industries can leverage their capabilities to enhance production efficiency and product quality.
What is the Optimal Work Environment for Mounting Machines?
Creating an optimal work environment for mounting machines is essential to ensure their efficiency, accuracy, and longevity. Here are the key factors to consider:
- Temperature and Humidity Control: Mounting machines operate best in a controlled environment with stable temperature and humidity levels. Extreme temperatures or high humidity can affect the machine’s performance and the quality of component placement.
- Cleanliness: Dust and debris can interfere with the machine’s moving parts and vision systems. A cleanroom or dust-free environment is ideal, especially for high-precision tasks.
- Vibration-Free Surface: Mounting machines should be placed on stable, vibration-free surfaces to prevent misalignment during operation. Anti-vibration pads or tables can be used to minimize disturbances.
- Adequate Lighting: Proper lighting is crucial for the vision system to accurately detect and place components. Avoid direct sunlight or harsh lighting that could cause glare.
- Power Supply Stability: Ensure a consistent and stable power supply to prevent disruptions. Voltage fluctuations can damage sensitive components and affect the machine’s performance.
- Space for Maintenance: Allow sufficient space around the machine for easy access during maintenance and repairs. Crowded workspaces can lead to accidents or delays in servicing.
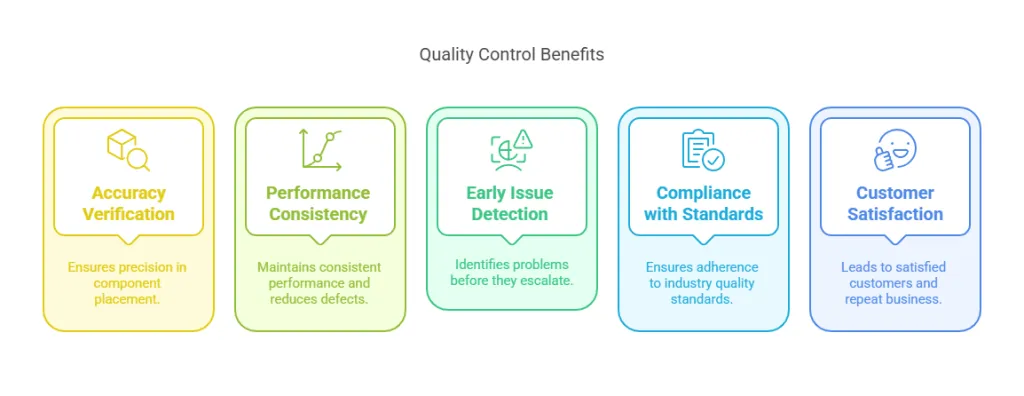
Why is Testing and Quality Control Important for Mounting Machines?
Testing and quality control are critical to ensuring that mounting machines perform reliably and produce high-quality outputs. Here’s why they matter:
- Accuracy Verification: Regular testing ensures that the machine places components with the required precision. This is especially important for miniaturized components where even a slight misalignment can lead to product failure.
- Performance Consistency: Quality control checks help maintain consistent performance over time, reducing the risk of defects and rework.
- Early Issue Detection: Testing can identify potential problems before they escalate, saving time and costs associated with machine downtime or product recalls.
- Compliance with Standards: Many industries have strict quality standards. Regular testing ensures that the mounting machine complies with these standards, avoiding legal or regulatory issues.
- Customer Satisfaction: High-quality outputs lead to satisfied customers, enhancing the reputation of the manufacturer and increasing repeat business.
How to Ensure Safety When Using Mounting Machines
Safety is paramount when operating mounting machines to protect both operators and equipment. Follow these safety precautions:
- Training: Ensure all operators are thoroughly trained on how to use the machine, including emergency procedures.
- Personal Protective Equipment (PPE): Operators should wear appropriate PPE, such as safety glasses, gloves, and anti-static wristbands, to prevent injuries and electrostatic discharge.
- Machine Guards: Use guards and barriers to prevent accidental contact with moving parts during operation.
- Regular Inspections: Conduct routine inspections to identify and address potential safety hazards, such as loose components or worn-out parts.
- Emergency Stop Button: Ensure the machine is equipped with an easily accessible emergency stop button to halt operations immediately in case of an issue.
- Clear Workspace: Keep the workspace organized and free of clutter to avoid accidents and ensure smooth operation.
- Follow Manufacturer Guidelines: Always adhere to the manufacturer’s safety instructions and recommendations.
Maintenance Tips for Extending the Life of Mounting Machines
Proper maintenance is key to extending the lifespan of mounting machines and ensuring their optimal performance. Here are some essential tips:
- Regular Cleaning: Clean the machine regularly to remove dust, debris, and residue that can affect its performance. Pay special attention to the feeder system, nozzles, and vision system.
- Lubrication: Lubricate moving parts as recommended by the manufacturer to reduce friction and wear.
- Inspect and Replace Wear Parts: Regularly inspect components like nozzles, belts, and feeders for signs of wear and replace them as needed.
- Calibration: Periodically calibrate the machine to ensure accurate component placement. This includes checking the vision system and alignment mechanisms.
- Software Updates: Keep the machine’s software up to date to benefit from the latest features and bug fixes.
- Monitor Performance: Use diagnostic tools to monitor the machine’s performance and identify potential issues early.
- Document Maintenance Activities: Keep a log of all maintenance activities, including dates, tasks performed, and any issues identified. This helps track the machine’s condition over time.
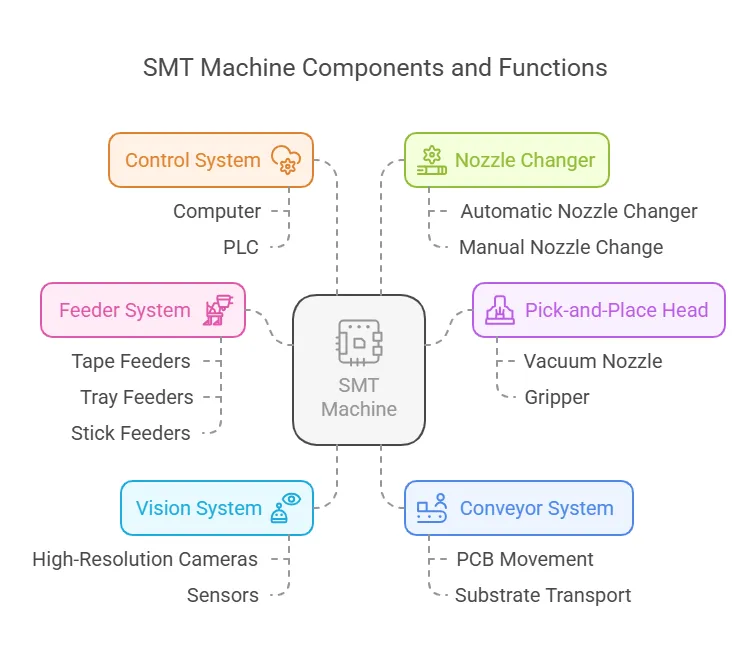
How to Troubleshoot Common Issues in Mounting Machines
Even with proper maintenance, mounting machines can encounter issues. Here’s a step-by-step guide to troubleshooting common problems:
-
Component Misplacement:
- Check the vision system for calibration issues.
- Inspect the nozzle for wear or damage.
- Verify that the feeder is supplying components correctly.
-
Machine Stops Unexpectedly:
- Check for error messages on the control panel.
- Inspect the power supply for stability.
- Ensure there are no obstructions in the conveyor system.
-
Poor Adhesion of Components:
- Verify that the substrate is clean and free of contaminants.
- Check the placement pressure and adjust if necessary.
- Ensure the adhesive or solder paste is applied correctly.
-
Feeder Issues:
- Inspect the feeder for jams or misaligned components.
- Clean the feeder to remove dust or debris.
- Replace worn-out feeder parts.
-
Vision System Errors:
- Clean the camera lenses and sensors.
- Recalibrate the vision system.
- Check the lighting conditions and adjust if necessary.
-
Nozzle Problems:
- Inspect the nozzle for clogs or damage.
- Replace the nozzle if necessary.
- Ensure the nozzle changer is functioning correctly.
By following these troubleshooting steps, operators can quickly resolve common issues and minimize downtime, ensuring the mounting machine operates efficiently.
Mounting machines are indispensable tools in modern manufacturing, designed to precisely attach components to substrates like PCBs. These machines consist of key components such as feeder systems, pick-and-place heads, vision systems, conveyor systems, and control systems, all working together to ensure accurate and efficient placement. They operate through a series of coordinated steps, including component feeding, picking, inspection, placement, and substrate movement. Mounting machines are widely used in industries like electronics, automotive, aerospace, medical devices, consumer goods, and industrial equipment, where precision and reliability are crucial. Creating an optimal work environment, conducting regular testing and quality control, ensuring safety, and performing proper maintenance are vital for maximizing their performance and longevity. Troubleshooting common issues can help minimize downtime and maintain efficiency. Overall, mounting machines are essential in enhancing production efficiency and product quality across various sectors.