Spot welding machine for battery is a crucial piece of equipment in the modern battery manufacturing landscape. This specialized tool is designed to join metal surfaces with precision and efficiency, creating strong, localized bonds that are essential for assembling battery packs. From electric vehicles and power tools to portable electronics, spot welding ensures reliable electrical conductivity without damaging sensitive battery components. In this blog, we’ll explore how spot welding machines work, their key components, and why they are indispensable in various industries.
What Is a Spot Welding Machine for Battery?
A spot welding machine for batteries is a specialized device that joins metal surfaces by applying heat and pressure at specific points. Unlike traditional welding, it doesn’t melt the entire workpiece—instead, it creates small, precise welds to connect battery cells, tabs, or terminals. This method is critical in assembling battery packs for applications like electric vehicles (EVs), power tools, and portable electronics, ensuring strong electrical conductivity without damaging sensitive battery materials.
Spot welding machines for batteries often use resistance welding technology, where an electric current passes through electrodes to generate localized heat. The result is a fast, efficient, and clean bonding process, minimizing thermal distortion and preserving battery integrity.
Key Components of a Battery Spot Welding Machine
A high-performance battery spot welding machine consists of several essential parts:
- Power Supply: Delivers controlled electrical current (DC or AC) to generate heat.
- Electrodes: Copper alloy tips apply pressure and conduct current to the welding spot.
- Controller: Microprocessor-based system adjusts welding time, current, and pressure.
- Cooling System: Prevents overheating in high-duty cycles (e.g., water or air cooling).
- Foot Pedal/Trigger: Allows the operator to initiate the welding process precisely.
Advanced machines may also include programmable settings for different battery types (e.g., lithium-ion, NiMH) and thicknesses.
Step-by-Step Guide: How Spot Welding Is Performed on Batteries
Spot welding batteries requires precision to avoid overheating or weak joints. Here’s a simplified breakdown:
-
Preparation:
- Clean the battery terminals and nickel strips to remove oxidation.
- Set the welding parameters (current, pulse duration) based on material thickness.
-
Positioning:
- Place the electrode tips on the target welding area (e.g., battery tab + nickel strip).
-
Welding:
- Press the foot pedal/trigger to apply pressure and send a short current pulse (1–10 ms).
- The resistance creates instant heat, fusing the metals.
-
Inspection:
- Check for a solid, shiny weld—not burnt or loose.
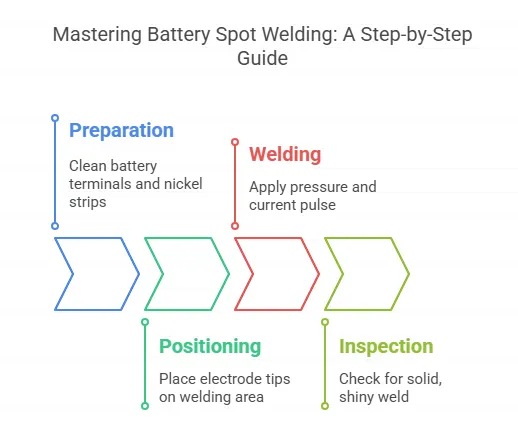
Pro Tip: Use a test piece first to fine-tune settings!
How Heat and Pressure Work in Spot Welding
Spot welding relies on two critical factors:
-
Heat Generation:
- When current flows through the electrodes, resistance at the contact point produces heat (Joule’s Law: Heat = I²Rt).
- Thin materials require less current than thick ones.
-
Pressure Application:
- Electrodes clamp the metals tightly to ensure proper contact and reduce electrical resistance.
- Too little pressure causes sparks; too much may deform the battery.
Balancing these factors prevents issues like cracks, weak joints, or battery damage.
Industries Using Battery Spot Welding Machines
Spot welding is vital in manufacturing batteries for:
- Electric Vehicles (EVs): Joining thousands of cells in battery modules.
- Power Tools: Ensuring durable connections in high-current battery packs.
- Energy Storage Systems: Building large-scale lithium-ion banks.
- Consumer Electronics: Assembling compact batteries for phones, laptops.
Each industry demands specific weld quality standards, pushing advancements in automation and precision.
What Are the Safety Standards for Operating Spot Welders in Battery Production?
Spot welding in battery production involves high currents and heat, making safety protocols critical. Key standards include:
-
Electrical Safety:
- Use insulated gloves and tools to prevent shocks.
- Ensure proper grounding of the welding machine.
-
Thermal Protection:
- Wear heat-resistant clothing to guard against sparks.
- Keep flammable materials away from the work area.
-
Ventilation:
- Fumes from melted metals (e.g., nickel, copper) require extraction systems.
-
Training:
- Operators must be trained in emergency shutdown procedures.
Compliance with OSHA, ANSI, and IEC standards minimizes risks like short circuits, fires, or toxic exposure.
Common Tests for Battery Spot Welds: Strength, Continuity, and Inspection
To ensure reliable welds, manufacturers perform these tests:
-
Weld Strength Test:
- Peel test: Measures resistance to mechanical separation.
- Shear test: Evaluates joint durability under lateral force.
-
Electrical Continuity Test:
- Use a multimeter to check for low resistance (<0.1Ω) at weld points.
-
Visual Inspection:
- Look for:
- Uniform, shiny weld nuggets (no cracks or discoloration).
- No excessive indentation from electrodes.
- Look for:
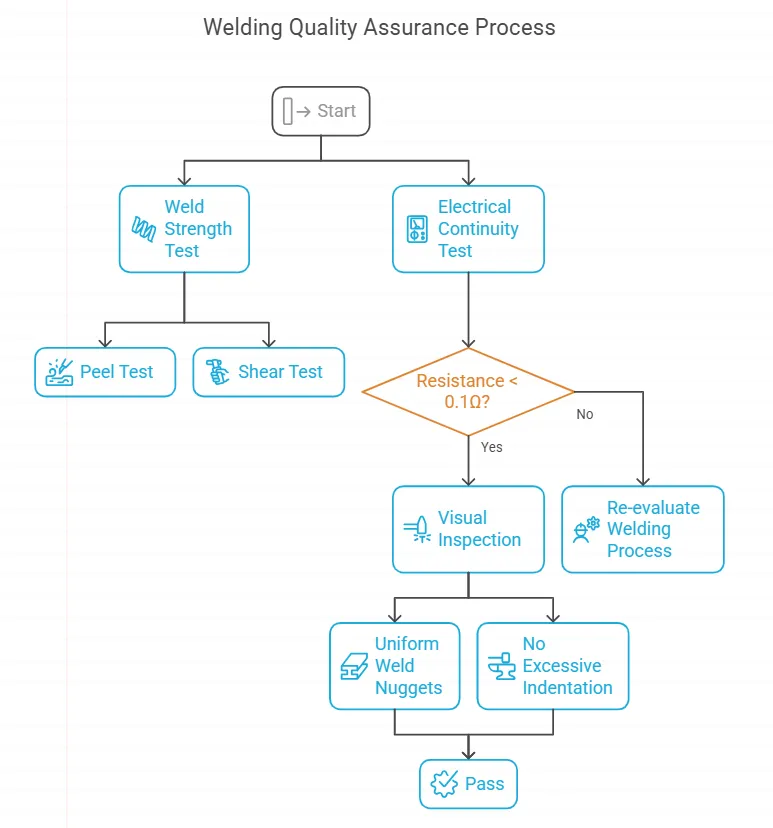
Failed tests indicate improper settings (e.g., low current, misaligned electrodes).
How to Avoid Poor Weld Quality in Battery Spot Welding
Common weld defects and solutions:
-
Low Conductivity:
- Cause: Insufficient current or dirty surfaces.
- Fix: Increase current slightly; clean terminals with alcohol.
-
Overheating/Burn-Through:
- Cause: Excessive current or long pulse duration.
- Fix: Reduce current/weld time; use pulsed welding mode.
-
Weak Joints:
- Cause: Inadequate electrode pressure.
- Fix: Adjust spring tension or pneumatic pressure.
Pro Tip: Maintain a weld log to track parameter adjustments.
Step-by-Step: How to Extend Electrode Lifespan in Spot Welding
Copper electrodes degrade due to heat and contamination. Follow these steps to prolong their life:
-
Regular Cleaning:
- Polish electrodes with a wire brush or sandpaper every 50–100 welds.
-
Proper Alignment:
- Ensure electrodes meet parallel to distribute pressure evenly.
-
Cooling Intervals:
- Allow 10–15 seconds between welds in high-duty cycles.
-
Material Choice:
- Use tungsten-copper (CuW) alloys for high-temperature resistance.
Replacing electrodes promptly prevents poor weld quality and energy waste.
Laser Welding vs. Spot Welding for Batteries: Key Differences
Factor | Spot Welding | Laser Welding |
---|---|---|
Heat Input | Localized, moderate heat | Highly concentrated heat |
Precision | Suitable for thick tabs | Better for ultra-thin materials |
Speed | Faster for repetitive welds | Slower due to beam positioning |
Cost | Lower equipment/maintenance costs | Higher initial investment |
Applications | EVs, power tools | Medical devices, micro-batteries |
Spot welding dominates high-volume production, while laser welding excels where precision outweighs cost.
Spot welding machine for battery is a vital tool in battery manufacturing, leveraging resistance welding technology to create precise and efficient bonds. These machines consist of essential components such as power supplies, electrodes, controllers, and cooling systems, all working together to ensure high-quality welds. The spot welding process involves careful preparation, precise positioning, and controlled execution, with safety protocols in place to manage risks associated with high currents and heat. Industries like electric vehicles, power tools, and consumer electronics rely heavily on spot welding to meet their battery assembly needs. Regular testing, maintenance, and adherence to safety standards ensure reliable welds and extended equipment lifespan. While laser welding offers precision for specialized applications, spot welding remains the preferred choice for high-volume production, balancing cost, speed, and reliability.