Spot welding machines have revolutionized the manufacturing industry with their ability to join metal surfaces quickly and efficiently. Whether you’re in automotive, electronics, or aerospace, understanding the intricacies of spot welding can significantly enhance your production capabilities. In this blog, we’ll delve into the fundamentals of spot welding machines, their key components, the step-by-step welding process, and how to choose the right machine for your needs. We’ll also explore the latest advancements in automated spot welding and compare spot welding with other welding techniques.
What is a Spot Welding Machine?
A spot welding machine is a specialized device used to join metal surfaces together by applying heat and pressure at specific points. This type of welding is commonly used in industries where thin metal sheets need to be joined quickly and efficiently. The process involves passing an electric current through the metal pieces, which generates heat at the contact points, melting the metal and forming a weld nugget. Once the current is stopped, the metal cools and solidifies, creating a strong bond. Spot welding machines are widely used in automotive manufacturing, electronics, and aerospace industries due to their speed, precision, and ability to produce consistent welds.
Key Components of a Spot Welding Machine
A spot welding machine consists of several critical components that work together to ensure efficient and accurate welding. Here are the main parts:
- Electrodes: These are the tools that deliver the electric current to the metal surfaces. They are typically made of copper or copper alloys due to their high conductivity and durability.
- Transformer: The transformer is responsible for converting the input voltage into a lower voltage but higher current, which is necessary for generating the heat required for welding.
- Control Panel: This allows the operator to adjust settings such as welding time, current, and pressure to achieve the desired weld quality.
- Cooling System: Spot welding generates significant heat, so a cooling system (often water-based) is essential to prevent overheating of the electrodes and other components.
- Frame and Arm: The frame provides structural support, while the arm holds the electrodes and applies the necessary pressure during the welding process.
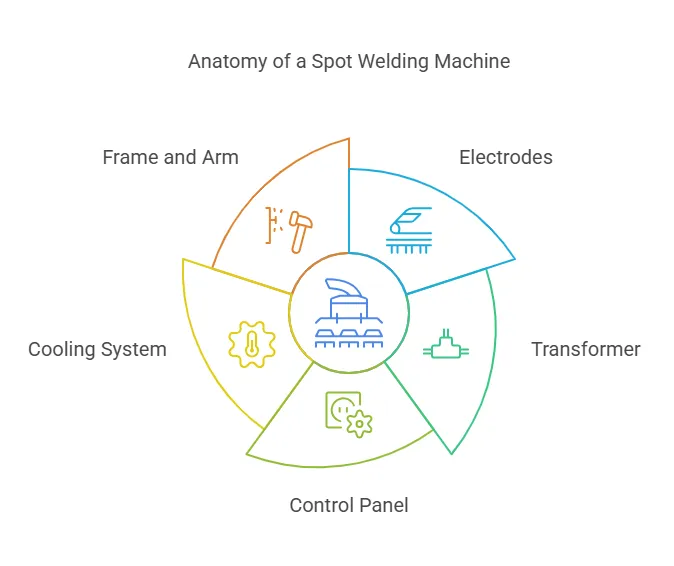
How Does a Spot Welding Machine Work?
The operation of a spot welding machine can be broken down into a step-by-step process:
- Preparation: The metal pieces to be welded are cleaned and positioned between the electrodes.
- Application of Pressure: The electrodes press the metal sheets together with a predetermined force to ensure proper contact.
- Electric Current Flow: A high electric current is passed through the electrodes, generating heat at the contact points due to electrical resistance.
- Melting and Formation of Weld Nugget: The heat melts the metal at the contact points, forming a molten pool that solidifies into a weld nugget once the current is stopped.
- Cooling and Solidification: The electrodes maintain pressure until the weld nugget cools and solidifies, creating a strong bond.
This process is highly efficient and can be completed in a matter of seconds, making it ideal for high-volume production environments.
Spot Welding Machine Applications in Various Industries
Spot welding machines are versatile tools used across a wide range of industries. Here are some key applications:
- Automotive Industry: Spot welding is extensively used in the assembly of car bodies, where it joins sheet metal components quickly and reliably.
- Electronics: In the electronics industry, spot welding is used to assemble battery packs, circuit boards, and other small components.
- Aerospace: The aerospace industry relies on spot welding for joining thin metal sheets in the construction of aircraft components.
- Appliances: Household appliances such as refrigerators, washing machines, and microwaves often use spot welding in their manufacturing processes.
- Construction: Spot welding is used in the fabrication of metal structures, such as steel frames and reinforcements.
Factors Affecting Spot Welding Quality
The quality of a spot weld depends on several factors, which must be carefully controlled to ensure strong and consistent welds. Here are the key factors:
- Electrode Force: The pressure applied by the electrodes must be sufficient to ensure proper contact between the metal pieces. Too little force can result in weak welds, while too much force can deform the metal.
- Welding Current: The amount of current passed through the electrodes determines the heat generated. Insufficient current can lead to incomplete welds, while excessive current can cause burn-through or electrode damage.
- Welding Time: The duration of the current flow must be precisely controlled. Too short a time may not allow the metal to melt properly, while too long a time can cause overheating.
- Material Properties: The type and thickness of the metal being welded affect the welding process. Different materials require different settings for optimal results.
- Electrode Condition: Worn or contaminated electrodes can lead to poor weld quality. Regular maintenance and replacement of electrodes are essential.
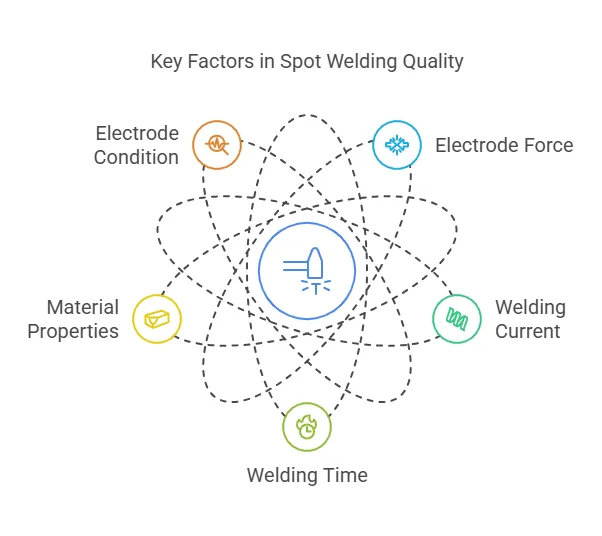
By carefully managing these factors, operators can ensure high-quality spot welds that meet industry standards.
Spot Welding Machine Setup and Adjustment Guide
Setting up and adjusting a spot welding machine correctly is crucial for achieving optimal performance and high-quality welds. Here’s a step-by-step guide to help you get started:
- Unbox and Inspect: Carefully unbox the machine and inspect all components for any damage during shipping. Ensure all parts, including electrodes, cables, and the control panel, are present.
- Position the Machine: Place the machine on a stable, level surface in a well-ventilated area. Ensure there is enough space for operation and maintenance.
- Connect Power Supply: Follow the manufacturer’s instructions to connect the machine to the appropriate power source. Ensure the voltage and current ratings match the machine’s requirements.
- Install Electrodes: Attach the electrodes to the welding arms, ensuring they are aligned properly and securely fastened.
- Adjust Settings: Use the control panel to set the welding time, current, and electrode force based on the material type and thickness. Refer to the machine’s manual for recommended settings.
- Test the Machine: Perform a test weld on scrap material to check the settings. Inspect the weld for quality and make adjustments as needed.
- Calibrate Regularly: Regularly calibrate the machine to maintain accuracy and consistency in welding performance.
By following these steps, you can ensure your spot welding machine is set up and adjusted for optimal performance.
Safety Precautions When Using Spot Welding Machines
Using a spot welding machine involves high currents and heat, making safety a top priority. Here are essential safety precautions to follow:
- Wear Protective Gear: Always wear safety glasses, gloves, and flame-resistant clothing to protect against sparks and heat.
- Inspect Equipment: Before use, inspect the machine, cables, and electrodes for any damage or wear. Replace any faulty components immediately.
- Ensure Proper Ventilation: Work in a well-ventilated area to avoid inhaling fumes generated during welding.
- Avoid Water: Keep the machine and work area dry to prevent electrical shocks or short circuits.
- Use Insulated Tools: Always use insulated tools to handle electrodes and other components to avoid electrical hazards.
- Follow Manufacturer Guidelines: Adhere to the manufacturer’s instructions for operation, maintenance, and safety procedures.
- Emergency Preparedness: Keep a fire extinguisher and first aid kit nearby in case of emergencies.
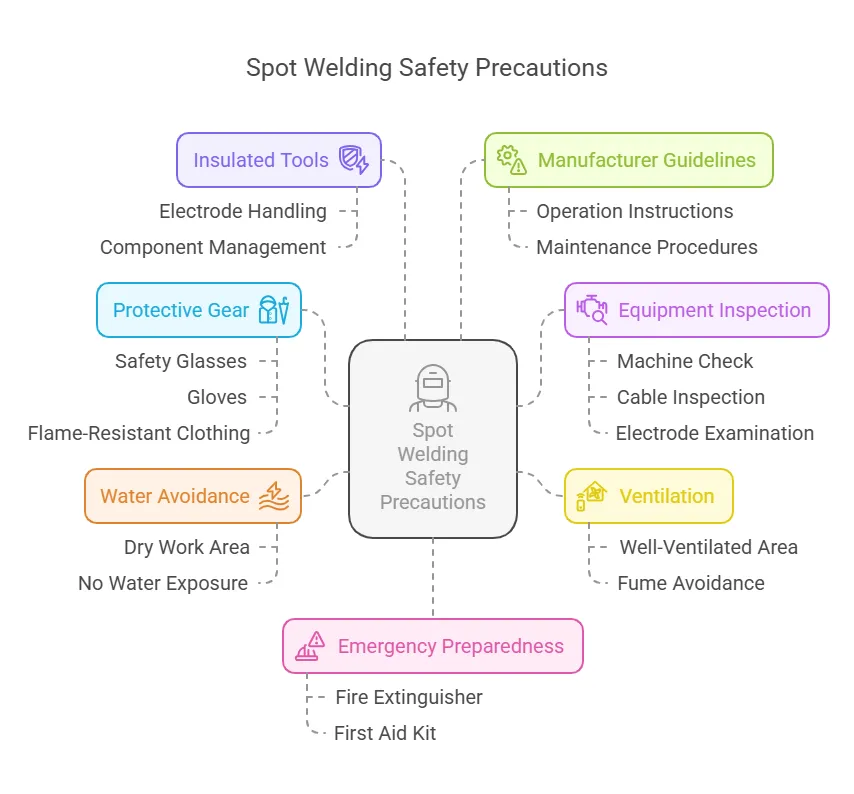
By following these safety precautions, you can minimize risks and ensure a safe working environment.
Common Troubleshooting Tips for Spot Welding Machines
Even with proper maintenance, spot welding machines can encounter issues. Here are some common problems and troubleshooting tips:
-
Weak or Incomplete Welds:
- Cause: Insufficient current or pressure.
- Solution: Increase the welding current or electrode force and ensure proper contact between the electrodes and material.
-
Electrode Sticking:
- Cause: Excessive heat or worn electrodes.
- Solution: Reduce the welding time or current and replace worn electrodes.
-
Overheating:
- Cause: Inadequate cooling or excessive use.
- Solution: Check the cooling system for blockages and ensure proper water flow. Allow the machine to cool down between uses.
-
Inconsistent Welds:
- Cause: Misaligned electrodes or uneven pressure.
- Solution: Realign the electrodes and ensure consistent pressure application.
-
Machine Not Powering On:
- Cause: Faulty power connection or internal component failure.
- Solution: Check the power supply and connections. If the issue persists, consult a professional technician.
Regular maintenance and timely troubleshooting can help keep your spot welding machine in optimal condition.
How to Choose the Right Spot Welding Machine for Your Needs
Selecting the right spot welding machine depends on several factors. Here’s a guide to help you make an informed decision:
- Material Type and Thickness: Determine the type and thickness of the materials you will be welding. Different machines are designed for specific materials and thicknesses.
- Welding Capacity: Consider the machine’s welding capacity, including the maximum current and electrode force it can deliver.
- Duty Cycle: Check the machine’s duty cycle, which indicates how long it can operate continuously without overheating.
- Portability: If you need to move the machine frequently, consider a portable model with wheels or a compact design.
- Ease of Use: Look for machines with user-friendly controls and clear instructions for setup and operation.
- Budget: Determine your budget and compare different models to find one that offers the best value for your needs.
- Brand and Support: Choose a reputable brand with good customer support and warranty options.
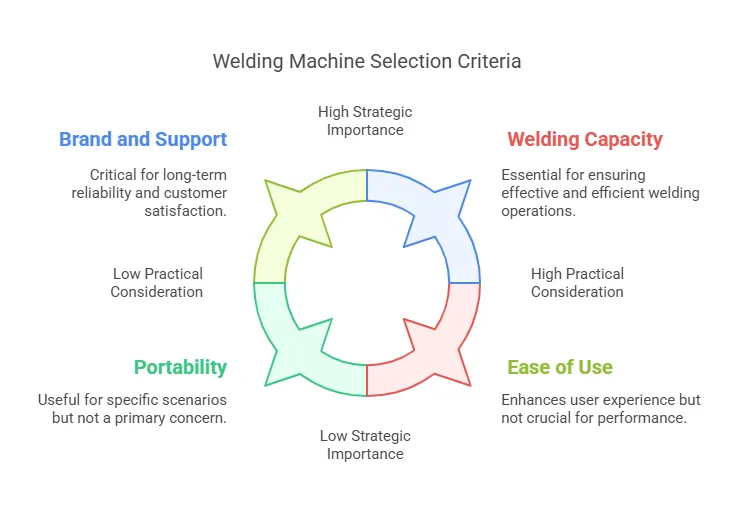
By considering these factors, you can select a spot welding machine that meets your specific requirements.
Spot Welding vs. Other Types of Welding: A Comparison
Spot welding is just one of many welding techniques available. Here’s a comparison of spot welding with other common types of welding:
-
Spot Welding:
- Process: Joins metal surfaces at specific points using heat and pressure.
- Advantages: Fast, efficient, and ideal for thin metal sheets.
- Applications: Automotive, electronics, and appliance manufacturing.
-
MIG Welding (Metal Inert Gas):
- Process: Uses a continuous wire electrode and shielding gas to join metals.
- Advantages: Versatile and suitable for a wide range of materials and thicknesses.
- Applications: Construction, automotive repair, and fabrication.
-
TIG Welding (Tungsten Inert Gas):
- Process: Uses a non-consumable tungsten electrode and shielding gas.
- Advantages: Produces high-quality, precise welds.
- Applications: Aerospace, art, and high-precision manufacturing.
-
Arc Welding:
- Process: Uses an electric arc to melt and join metals.
- Advantages: Simple and cost-effective.
- Applications: General fabrication, repair, and construction.
-
Laser Welding:
- Process: Uses a laser beam to join metals.
- Advantages: High precision and minimal heat-affected zones.
- Applications: Medical devices, electronics, and precision engineering.
Each welding method has its strengths and is suited to specific applications. Understanding these differences can help you choose the right technique for your project.
Spot welding machines are essential tools for joining thin metal sheets in various industries. They work by applying heat and pressure at specific points, creating strong and consistent welds. The key components include electrodes, a transformer, a control panel, a cooling system, and a frame with an arm. The welding process involves preparation, application of pressure, electric current flow, melting and formation of the weld nugget, and cooling. Factors such as electrode force, welding current, and material properties significantly affect weld quality. Setting up and adjusting the machine correctly is crucial for optimal performance. Safety precautions are also vital due to the high currents and heat involved. Troubleshooting common issues like weak welds or overheating can help maintain machine efficiency. When choosing a spot welding machine, consider factors like material type, welding capacity, duty cycle, portability, ease of use, and budget. Automated spot welding systems offer increased production rates, consistent quality, and enhanced safety. By understanding these aspects, manufacturers can make informed decisions to optimize their welding processes.