In an era where energy storage is becoming increasingly vital, the battery production line stands as the backbone of innovation and efficiency. This intricate system transforms raw materials into powerful energy sources, powering everything from smartphones to electric vehicles. But what exactly is a battery production line, and why is it so crucial? In this blog, we’ll dive deep into the inner workings of these manufacturing marvels, exploring their components, workflow, and impact on various industries. From the precision of electrode manufacturing to the importance of quality control, we’ll uncover how battery production lines are shaping the future of energy.
What is a Battery Production Line?
A battery production line is a specialized manufacturing system designed to produce batteries efficiently and at scale. It involves a series of interconnected processes and machinery that transform raw materials into fully functional batteries. These production lines are essential for meeting the growing demand for batteries in industries such as consumer electronics, automotive, and renewable energy storage. The production line typically includes stages like electrode preparation, cell assembly, electrolyte filling, sealing, formation, and testing. Each stage is meticulously controlled to ensure the final product meets stringent quality and performance standards.
Key Components of a Battery Production Line
A battery production line consists of several critical components that work together to ensure seamless operation. Here are the main elements:
- Electrode Manufacturing Equipment: This includes mixers, coaters, and calendaring machines used to prepare the anode and cathode materials.
- Cell Assembly Machines: These machines stack or wind the electrodes and separators to form the battery cell.
- Electrolyte Filling Systems: Precision equipment that fills the battery cells with the appropriate electrolyte solution.
- Sealing and Casing Units: Machines that seal the battery cells and encase them in protective housing.
- Formation and Testing Systems: Equipment that charges and tests the batteries to ensure they meet performance and safety standards.
- Automation and Robotics: Advanced robotics and automation systems that handle material transport, assembly, and quality control.
Each component plays a vital role in ensuring the efficiency, accuracy, and consistency of the battery production process.
Workflow of a Battery Production Line
The workflow of a battery production line is a carefully orchestrated sequence of steps designed to maximize efficiency and quality. Here’s a step-by-step breakdown:
- Material Preparation: Raw materials like lithium, cobalt, and graphite are processed into electrode materials.
- Electrode Coating: The electrode materials are coated onto metal foils using precision coaters.
- Drying and Calendaring: The coated electrodes are dried and compressed to achieve the desired thickness and density.
- Cell Assembly: The electrodes and separators are assembled into cells using stacking or winding techniques.
- Electrolyte Filling: The assembled cells are filled with electrolyte solution in a controlled environment.
- Sealing: The cells are sealed to prevent leakage and contamination.
- Formation: The sealed cells undergo an initial charge-discharge cycle to activate the battery chemistry.
- Testing and Quality Control: Each battery is tested for performance, capacity, and safety before packaging.
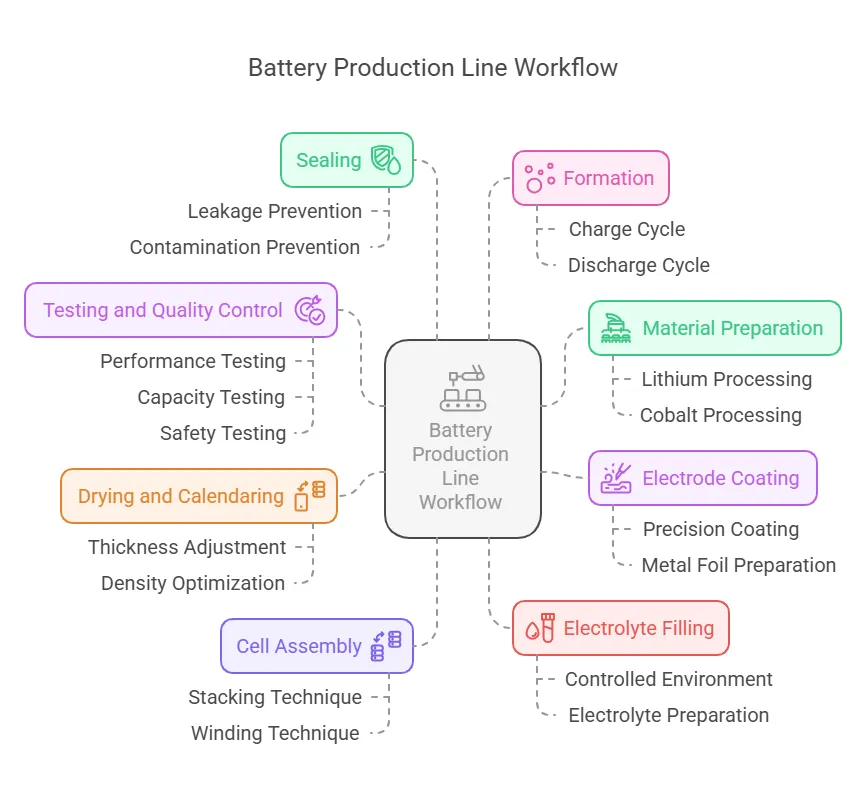
This workflow ensures that every battery produced meets the required specifications and standards.
How Does a Battery Production Line Work?
A battery production line operates through a combination of advanced machinery, automation, and precise control systems. Here’s how it works:
- Automated Material Handling: Raw materials are transported between stages using conveyor belts, robotic arms, or automated guided vehicles (AGVs).
- Precision Manufacturing: Each stage of the production process, from electrode coating to cell assembly, is carried out with high precision to ensure consistency.
- Quality Assurance: Sensors and cameras monitor the production process in real-time, detecting any defects or deviations from the standard.
- Data Integration: The entire production line is connected through a centralized control system that collects and analyzes data to optimize performance.
- Scalability: Modern battery production lines are designed to be scalable, allowing manufacturers to increase output as demand grows.
By integrating these elements, a battery production line can produce high-quality batteries efficiently and reliably.
Applications of Battery Production Lines in Different Industries
Battery production lines are crucial for supplying batteries to a wide range of industries. Here are some key applications:
- Consumer Electronics: Batteries for smartphones, laptops, and wearable devices are produced on specialized lines to meet high-volume demands.
- Automotive: Electric vehicles (EVs) rely on advanced battery production lines to manufacture high-capacity lithium-ion batteries.
- Renewable Energy Storage: Battery production lines produce large-scale energy storage systems for solar and wind power installations.
- Industrial Equipment: Batteries for forklifts, drones, and other industrial equipment are manufactured using robust production lines.
- Medical Devices: High-precision battery production lines are used to create batteries for medical devices like pacemakers and portable diagnostic equipment.
Each industry has unique requirements, and battery production lines are tailored to meet these specific needs, ensuring optimal performance and reliability.
Battery Production Line Design and Setup Considerations
Designing and setting up a battery production line requires careful planning to ensure efficiency, scalability, and cost-effectiveness. Here are the key considerations:
- Production Capacity: Determine the required output to meet market demand and plan the line’s capacity accordingly.
- Layout Optimization: Design the layout to minimize material handling and reduce production bottlenecks.
- Equipment Selection: Choose machinery that aligns with the type of batteries being produced (e.g., lithium-ion, solid-state).
- Automation Integration: Incorporate automation and robotics to enhance precision and reduce labor costs.
- Energy Efficiency: Implement energy-saving technologies to reduce operational costs and environmental impact.
- Scalability: Ensure the production line can be expanded or upgraded as demand grows.
- Regulatory Compliance: Design the line to meet industry safety and environmental regulations.
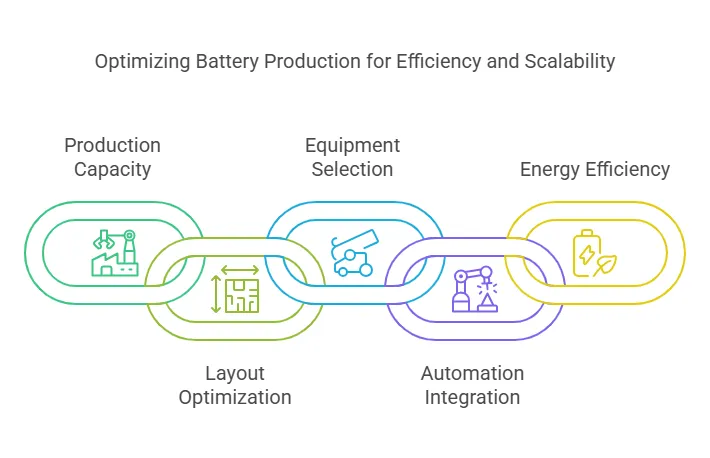
A well-designed production line not only improves efficiency but also ensures long-term operational success.
Importance of Quality Control in Battery Production
Quality control is critical in battery production to ensure safety, reliability, and performance. Here’s why it matters:
- Safety Assurance: Defective batteries can pose serious safety risks, including overheating or explosions.
- Performance Consistency: Quality control ensures that every battery meets the required performance standards.
- Customer Satisfaction: High-quality batteries enhance brand reputation and customer trust.
- Cost Savings: Detecting defects early reduces waste and avoids costly recalls.
How Quality Control is Implemented:
- In-Line Testing: Real-time monitoring of parameters like voltage, capacity, and internal resistance.
- End-of-Line Testing: Comprehensive testing of finished batteries to ensure they meet all specifications.
- Statistical Process Control (SPC): Using data analytics to identify and address production variations.
- Traceability Systems: Tracking each battery’s production history for accountability and continuous improvement.
By prioritizing quality control, manufacturers can deliver reliable and safe batteries to their customers.
Challenges in Scaling Battery Production Lines
Scaling battery production lines to meet growing demand is a complex task. Here are the main challenges:
- High Initial Investment: Expanding production lines requires significant capital for machinery, facilities, and technology.
- Supply Chain Constraints: Sourcing raw materials like lithium and cobalt can be difficult due to limited availability and geopolitical factors.
- Technical Complexity: Advanced battery technologies (e.g., solid-state batteries) require specialized equipment and expertise.
- Workforce Training: Scaling up often necessitates hiring and training skilled workers to operate advanced machinery.
- Regulatory Hurdles: Compliance with evolving safety and environmental regulations can slow down expansion efforts.
- Quality Maintenance: Ensuring consistent quality while increasing production volume is a major challenge.
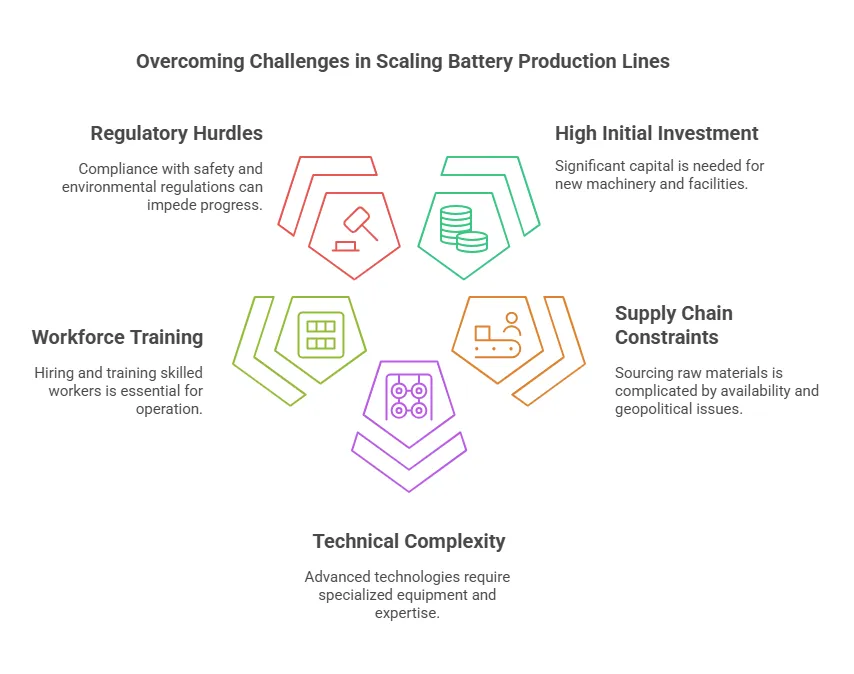
Steps to Overcome These Challenges:
- Partner with reliable suppliers to secure raw materials.
- Invest in modular and scalable production equipment.
- Implement advanced automation to reduce reliance on manual labor.
- Collaborate with regulatory bodies to stay ahead of compliance requirements.
Addressing these challenges is essential for successfully scaling battery production lines.
Automation in Battery Production: Benefits and Future Trends
Automation is revolutionizing battery production by enhancing efficiency, precision, and scalability. Here’s how:
Benefits of Automation:
- Increased Efficiency: Automated systems can operate 24/7, significantly boosting production output.
- Improved Precision: Robotics and AI ensure consistent quality by minimizing human error.
- Cost Savings: Automation reduces labor costs and material waste.
- Enhanced Safety: Automated systems can handle hazardous materials and processes, reducing risks to workers.
- Data-Driven Optimization: Automation enables real-time data collection and analysis for continuous process improvement.
Future Trends in Automation:
- AI and Machine Learning: Advanced algorithms will optimize production processes and predict maintenance needs.
- Collaborative Robots (Cobots): Cobots will work alongside humans to perform complex tasks.
- Digital Twins: Virtual replicas of production lines will enable simulation and testing before implementation.
- Sustainable Automation: Energy-efficient and eco-friendly automation technologies will gain prominence.
As automation continues to evolve, it will play an even greater role in shaping the future of battery production.
Safety Standards and Regulations for Battery Production Lines
Safety is paramount in battery production due to the potential risks associated with handling hazardous materials and high-energy processes. Here’s an overview of key safety standards and regulations:
- Material Safety: Regulations govern the handling, storage, and disposal of materials like lithium, cobalt, and electrolytes.
- Fire and Explosion Prevention: Production lines must incorporate fire suppression systems and explosion-proof equipment.
- Worker Safety: Personal protective equipment (PPE) and training programs are mandatory to protect workers from chemical exposure and mechanical hazards.
- Environmental Compliance: Regulations ensure that production processes minimize environmental impact, such as reducing emissions and waste.
- Product Safety: Batteries must undergo rigorous testing to comply with international standards like UN 38.3 (transportation safety) and IEC 62133 (safety of portable batteries).
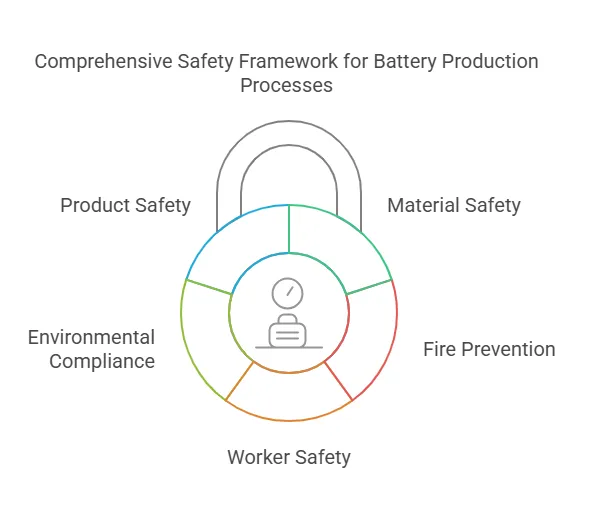
How to Ensure Compliance:
- Conduct regular safety audits and risk assessments.
- Implement robust training programs for employees.
- Stay updated on evolving regulations and industry best practices.
- Collaborate with regulatory bodies to ensure adherence to all requirements.
By prioritizing safety and compliance, manufacturers can protect their workers, customers, and the environment while maintaining operational integrity.
This article provides an in-depth exploration of battery production lines, highlighting their significance in modern manufacturing. It begins by defining what a battery production line is and its critical components, such as electrode manufacturing equipment, cell assembly machines, and automation systems. The workflow of a battery production line is meticulously detailed, from material preparation to final testing, emphasizing the importance of precision and quality control. The article further discusses the diverse applications of these production lines across industries like consumer electronics, automotive, renewable energy, and medical devices. It also addresses the challenges of scaling production lines, including high initial investment, supply chain constraints, and regulatory hurdles. The benefits of automation in battery production are highlighted, along with future trends such as AI, collaborative robots, and sustainable technologies. Finally, the importance of adhering to safety standards and regulations is emphasized to ensure worker protection, environmental compliance, and product safety. Overall, the article underscores the pivotal role of battery production lines in meeting the growing energy demands of our world.