Lithium ion battery construction is a marvel of modern engineering, powering everything from our smartphones to electric vehicles. But what exactly goes into building these energy-dense and reliable power sources? In this blog, we unravel the complexities behind lithium ion battery construction, exploring the key components that drive performance, the different structural forms that suit various applications, and the meticulous manufacturing processes that ensure safety and longevity. Whether you’re a tech enthusiast or simply curious about the technology that powers your daily life, join us as we dive deep into the world of lithium ion batteries.
1. What Is Lithium-Ion Battery Construction and Why It Matters?
Lithium-ion (Li-ion) batteries power everything from smartphones to electric vehicles (EVs). But what exactly goes into their construction, and why does it matter for performance and safety?
Key Components of Li-Ion Battery Construction
- Anode: Typically made of graphite, it stores lithium ions during charging.
- Cathode: Composed of lithium metal oxides (e.g., NMC, LFP), it determines energy density.
- Separator: A porous polymer film preventing short circuits while allowing ion flow.
- Electrolyte: A lithium salt solution facilitating ion movement between electrodes.
- Housing: Protects cells from physical damage (metal for cylindrical/prismatic, foil for pouch).
Why Construction Matters
- Energy Density: Compact designs (e.g., pouch cells) maximize space efficiency.
- Safety: Robust separators prevent thermal runaway.
- Lifespan: High-quality materials reduce degradation over cycles.
2. Structure Comparison: Cylindrical vs. Prismatic vs. Pouch Cells
Different Li-ion battery shapes suit different applications. Here’s how their constructions compare:
Cylindrical Cells
- Structure: Steel/aluminum casing with spiral-wound electrodes (e.g., Tesla’s 21700 cells).
-
Pros:
- Mechanically stable
- Easy thermal management
-
Cons:
- Wasted space in packs
Prismatic Cells
- Structure: Rectangular metal casing with stacked electrodes.
-
Pros:
- Better space utilization than cylindrical
- Higher capacity per unit
-
Cons:
- More expensive to manufacture
Pouch Cells
- Structure: Flexible laminated foil with stacked electrodes.
-
Pros:
- Lightweight and customizable shapes
- Highest energy density
-
Cons:
- Requires external support to prevent swelling
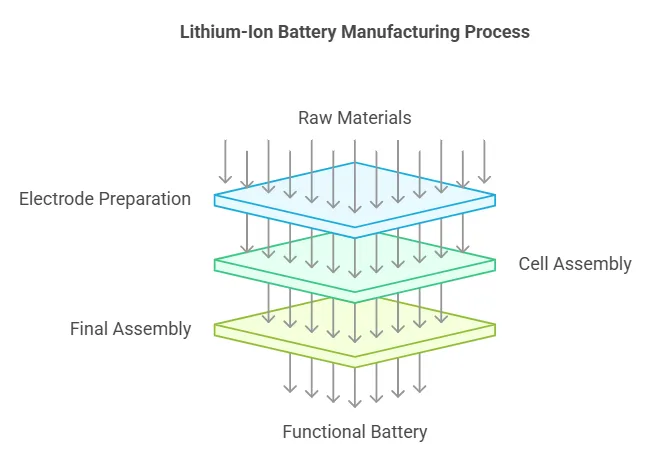
3. Step-by-Step Lithium-Ion Battery Manufacturing Process
Li-ion battery production involves precision engineering. Here’s how it’s done:
Step 1: Electrode Preparation
- Mixing: Active materials (anode/cathode), binders, and solvents form a slurry.
- Coating: Slurry is applied to copper (anode) or aluminum (cathode) foils.
- Drying & Calendering: Electrodes are dried and compressed for uniform thickness.
Step 2: Cell Assembly
- Slitting: Electrodes are cut into strips.
- Stacking/Winding: Layers are assembled (stacked for pouch/prismatic, wound for cylindrical).
- Adding Separator: A polymer film is placed between anode and cathode.
Step 3: Final Assembly
- Filling Electrolyte: Liquid electrolyte is injected into the sealed cell.
- Formation Cycling: The battery is charged/discharged to stabilize performance.
4. How Lithium-Ion Batteries Store and Release Energy
Li-ion batteries work via electrochemical reactions. Here’s how energy storage/release happens:
Charging (Energy Storage)
- Lithium ions move from the cathode to the anode through the electrolyte.
- Electrons flow via the external circuit, storing energy in the anode.
Discharging (Energy Release)
- Ions return to the cathode, releasing electrons to power devices.
- The cycle repeats, with efficiency depending on electrode materials.
Key Factors:
- Cathode Chemistry: LFP (safer) vs. NMC (higher energy).
- Anode Innovations: Silicon anodes boost capacity but reduce lifespan.
5. How Battery Construction Varies by Application (EV, Power Tools, ESS)
Li-ion batteries are tailored for specific uses. Here’s how construction differs:
Electric Vehicles (EVs)
- Design: High-energy cylindrical (Tesla) or prismatic/pouch (others).
- Materials: NMC/NCA cathodes for long range.
- Cooling: Liquid cooling systems to manage heat.
Power Tools
- Design: Durable cylindrical cells (e.g., 18650).
- Materials: High-power cathodes for rapid discharge.
Energy Storage Systems (ESS)
- Design: Prismatic/pouch cells with LFP cathodes.
- Priorities: Safety and cycle life over energy density.
6. Why Environmental Controls Are Critical in Lithium-Ion Battery Assembly
Lithium-ion batteries are highly sensitive to moisture and contaminants. Even trace amounts of water or airborne particles can degrade electrolyte performance, increase internal resistance, or trigger dangerous side reactions.
Key Controls in Battery Manufacturing:
- Humidity (<1% dew point): Prevents lithium salt decomposition in electrolytes.
- Cleanroom (ISO 8 or better): Minimizes metal dust and particulates that could pierce separators.
- Inert gas (Argon/Nitrogen) filling: Reduces oxidation during electrode stacking.
Step-by-Step Protection Process:
- Material Pre-Drying: Electrodes and separators are baked at 120°C+ to remove residual moisture.
- Glovebox Assembly: Electrolyte injection happens in oxygen-free environments.
- Laser Sealing: Ensures moisture cannot penetrate cell casings post-production.
Without these measures, batteries risk premature capacity fade or swelling due to gas generation from hydrolysis.
7. How Inline Inspection Technologies Prevent Battery Defects
Modern battery factories integrate real-time inspection tools to catch flaws before cells leave production. Three technologies dominate:
1. X-Ray Imaging
- What it detects: Misaligned electrodes, foreign objects, or uneven coating.
- Why it matters: Even a 50µm electrode misalignment can cause localized overheating.
2. Open-Circuit Voltage (OCV) Testing
- How it works: Each cell is charged to 3.7V post-assembly; outliers indicate internal shorts.
- Data-driven rejection: Cells outside ±5mV tolerance are scrapped.
3. Electrochemical Impedance Spectroscopy (EIS)
- Key metric: Measures ion transport resistance at 1kHz frequency.
- Hidden flaw identifier: High impedance often reveals dry spots in electrodes.
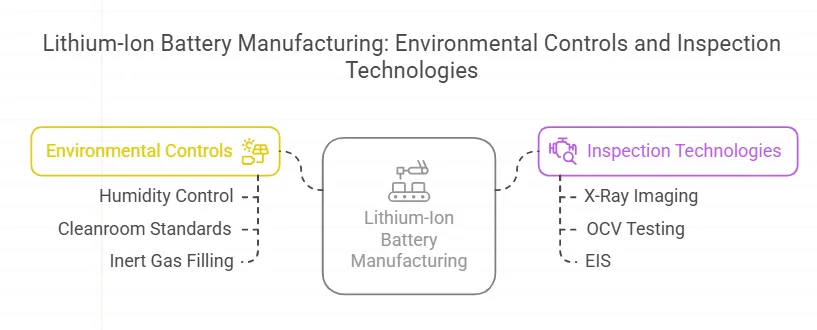
8. How Poor Construction Triggers Battery Swelling and Thermal Runaway
A single flaw in cell assembly can cascade into catastrophic failure. Here’s the science behind common risks:
Root Causes and Effects:
Construction Flaw | Consequence |
---|---|
Wrinkle in separator | Dendrite penetration → internal short |
Underfilled electrolyte | Dry electrode zones → lithium plating |
Miswelded tabs | High resistance → joule heating |
Chain Reaction Example:
- A particle contaminant punctures the separator during winding.
- Over cycles, lithium dendrites grow toward the cathode.
- Dendrites bridge electrodes, causing a micro-short.
- Localized heat vaporizes electrolyte, expanding the pouch cell (swelling).
- At 150°C, the anode reacts with electrolyte, igniting thermal runaway.
9. How Precision Construction Extends Battery Lifespan (Reducing Maintenance)
Well-built lithium-ion cells exhibit 3X longer cycle life versus poorly assembled units. Critical design optimizations include:
Construction Features That Minimize Degradation:
-
Uniform Electrode Calendering
- Why: Prevents lithium metal buildup in low-density zones.
- How: Rollers compress electrodes to ±2µm thickness tolerance.
-
Laser-Notched Electrodes
- Benefit: Eliminates uneven current distribution at edges.
-
Pre-Tensioned Stacking
- Process: Separators are stretched 1-2% before stacking to accommodate expansion.
Maintenance Savings Example:
- A Tesla Module with laser-aligned tabs maintains <5% capacity loss after 1,000 cycles, versus 15% loss in misaligned counterparts.
This blog provides an in-depth look at lithium ion battery construction, starting with the essential components like the anode, cathode, separator, and electrolyte. We compare the structures of cylindrical, prismatic, and pouch cells, each with its own set of advantages and drawbacks. The manufacturing process is also examined in detail, from electrode preparation to final assembly, highlighting the precision required to create high-quality batteries. Additionally, we explore how construction varies by application, from electric vehicles to power tools and energy storage systems. Finally, we emphasize the importance of environmental controls and inspection technologies in maintaining battery performance and safety. By the end of this blog, you’ll have a comprehensive understanding of the intricate architecture behind lithium ion batteries.