O corte, também conhecido como corte e rebobinamento, refere-se ao processo de cortar longitudinalmente um filme revestido de grande largura em várias tiras e rebobinar As lâminas de corte consistem principalmente em lâminas de disco circular superior e inferior, que são instaladas no eixo da faca da máquina de corte e usam o princípio de cisalhamento de rolamento para cortar produtos como folha de alumínio, folha de cobre e folhas de eletrodo positivo e negativo com espessura de 0.01-0.1 mm. A qualidade das lâminas de corte, o ângulo da lâmina e a tensão do filme são os principais fatores que afetam o processo de corte. Após o corte, as folhas de eletrodo não devem apresentar rugas ou derramamento de pó. É necessária alta precisão para as dimensões de corte, e as rebarbas nas bordas das folhas de eletrodo devem ser mínimas. Caso contrário, os dendritos podem penetrar no separador devido às rebarbas, causando um curto-circuito dentro da bateria.
01 Indicadores do equipamento de corte longitudinal
Um dispositivo de corte, também conhecido como cortador longitudinal ou cortador, refere-se a um equipamento de produção que corta eletrodos de bateria de íons de lítio, folhas de eletrodo de bateria de polímero, folhas de eletrodo de bateria de níquel-hidreto metálico, bem como chapas ou bobinas de metal coloridas, nas especificações de tamanho exigidas, mantendo uma tensão constante e atendendo a certos requisitos do processo. O corte dos eletrodos da bateria requer alta precisão dimensional e as bordas dos eletrodos devem ter rebarbas mínimas. Caso contrário, os dendritos podem penetrar no separador, causando um curto-circuito dentro da bateria. Os indicadores de desempenho do dispositivo de corte incluem principalmente precisão de corte, precisão do equipamento de corte e a faixa de ajustes da lâmina e da matriz.
- Corte exatidão
Após o corte, as rebarbas longitudinais do eletrodo devem ser de ≤7μm e as rebarbas transversais devem ser de ≤12μm. Não deve haver delaminação ou rugas nas bordas cortadas do eletrodo. As dimensões geométricas devem atender aos requisitos de tolerância linear dos processos de fabricação de baterias. Isso se refere principalmente à tolerância de tamanho e excentricidade do eixo da faca e lâminas de corte, bem como sua coaxialidade.
- Precisão de corte e instalação
A precisão dos roletes intermediários e do módulo de lâmina durante o teste sem carga após a montagem e depuração do equipamento de corte refere-se principalmente aos seguintes critérios:
Rugosidade da superfície do rolo intermediário: Ra ≤ 0,4.
Cilindricidade do rolo intermediário: ≤ 0,03 mm.
Batimento total do rolo intermediário após a instalação: ≤ 0,05 mm.
Saída do conjunto do módulo lâmina: ≤ 10μm.
- Faixa de ajuste da lâmina
A faixa de distância ajustável entre as lâminas superior e inferior do equipamento de corte na seção do material de corte.
02 A composição e a estrutura chave da máquina de corte
2.1 Composição da máquina de corte
O equipamento de corte consiste principalmente em dispositivo de desenrolamento, controle de tensão de desenrolamento, controle de alinhamento de borda de desenrolamento, guia de banda, sistema de detecção de defeitos de aparência CCD, corte, sistema de detecção de largura pós-corte, remoção de poeira, detecção de tensão de rebobinamento, dispositivo de rotulagem, dispositivo de rebobinamento e sistema elétrico.
A configuração padrão de um equipamento de corte de bateria de lítio totalmente automático é montada verticalmente na estrutura. Ele usa um eixo diferencial de deslizamento duplo com o mesmo método de enrolamento central de direção para rolos superiores e inferiores. A fixação do rebobinamento e desenrolamento, bem como as ações do módulo da lâmina e dos rolos de pressão, são todos controlados pneumaticamente, tornando a operação simples e rápida. É acionado por um único motor com acionamento de conversão de frequência e transmissão por correia síncrona, garantindo uma operação suave e confiável com baixo ruído. O desenrolamento é controlado por um freio de embreagem de pó magnético, que fornece alta precisão de controle de tensão, resposta rápida e uma ampla faixa ajustável. A composição do equipamento de corte é mostrada abaixo.
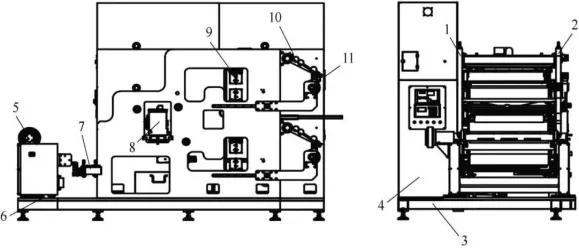
1 – Painel de parede traseiro;2 – Painel de parede frontal;3 – Base;4 – Armário elétrico;5 – Dispositivo de desenrolamento;6 – Dispositivo de alinhamento de borda;7 – Plataforma de guia de teia;8 – Lâmina de corte;9 – Dispositivo de escovação em pó;10 – Dispositivo de rolo de pressão de rebobinamento;11 – Dispositivo de eixo diferencial de deslizamento de rebobinamento
- –Corpo da máquina: Feito de aço estrutural de carbono de alta qualidade, é usado para apoiar a estrutura e o gabinete elétrico do equipamento de corte. Os painéis de parede frontal e traseiro são conectados por vigas de conexão e fixados verticalmente na base.
- –Dispositivo de desenrolamento: O desenrolamento é feito usando um método de eixo de expansão de ar. Ao conectar um freio de pó magnético à extremidade do eixo de expansão do ar desenrolado, uma resistência controlável oposta à direção de tração é aplicada para obter a tensão de desenrolamento.
- – Dispositivo de alinhamento de borda: Adota uma única detecção de borda de sonda indutiva para alinhamento de borda. Um sistema de alinhamento de borda de alta precisão é usado com uma precisão de alinhamento de ±0,1 mm e um curso de alinhamento de ≥120 mm. O mecanismo de ajuste da posição do sensor é ajustado usando um parafuso e está equipado com uma escala de display digital e um mecanismo de travamento do tipo alça.
- Plataforma de alimentação da correia:A largura da folga da plataforma de alimentação da correia é de 1 mm, com uma profundidade superior a 10 mm. A haste de pressão pneumática pressiona a placa de contato. Uma placa de aço preta de 5,0 mm é adicionada à plataforma de alimentação da correia, juntamente com uma régua de escala. O ponto de referência "0" na escala corresponde à largura da luva de folga entre o ponto de referência da matriz de corte. O processo de junção de material é feito manualmente. É necessário garantir que a distância entre a plataforma de alimentação da correia e a barra de pressão seja de 10 mm quando a placa de contato estiver alimentando adequadamente a correia. Medidas de segurança adicionais são implementadas. Se a haste de pressão estiver na posição para baixo ao ligar a máquina, uma função de alarme e prompt deve ser ativada e o alarme deve ser apagado antes que a máquina possa ser iniciada.
- –Corte Morrer:A folga entre a lâmina superior e a lâmina inferior é convenientemente fixada. A matriz de corte adota um acionamento de eixo único. Os dois eixos principais são feitos de material 40Cr e a placa de base e o suporte são feitos de aço S136. A superfície é endurecida com dureza HRC50 ou superior. A aparência geral da matriz de corte deve estar livre de manchas de ferrugem. É necessária a indicação da escala no rolo de ajuste para a entrada da matriz de corte. O diâmetro do rolo de alimentação é de φ50mm. Quando o ponto mais baixo do rolo está na mesma posição horizontal que o ponto mais alto da lâmina inferior, a indicação da escala é zero. O ajuste para cima é indicado como positivo e o ajuste para baixo é indicado como negativo. A escala no rolo de ajuste da matriz de corte deve ser feita com uma faixa de ±5 mm. O rolo de ajuste é feito de liga de alumínio e a superfície é tratada com anodização marrom, com dureza não inferior a HRB300. Os dois suportes finais adotam uma estrutura de parafuso e podem ser ajustados para cima e para baixo. A indicação da escala é zero. O ajuste do rolo de desvio em relação à posição zero é indicado por ângulos positivos e negativos, com uma faixa de ajuste de ±3°.
- – Dispositivo de escovação de pó:O dispositivo usa um rolo de escova destacável com uma instalação estilo braçadeira. O orifício do eixo é fixo e o acionamento é obtido por um mecanismo de pino, facilitando a montagem e desmontagem. As cerdas do rolo da escova são feitas de cerdas de nylon macias para evitar danos à placa de contato devido à dureza excessiva. O rolo da escova adota uma colocação de cerdas do tipo enrolamento, garantindo uma alta densidade de cerdas para uma remoção eficaz de poeira. A escova gira na direção oposta do movimento da placa de contato para aumentar o efeito de remoção de poeira. Durante a operação, as escovas esquerda e direita do dispositivo de remoção de poeira são embutidas uma na outra para garantir o contato efetivo entre as cerdas e a placa de contato, aplicando certa pressão, mantendo elasticidade suficiente para garantir a eficácia da remoção de poeira. A profundidade na qual as duas escovas são embutidas uma na outra é de 2 a 3 mm (controlada ajustando a espessura do material de vedação na borda da caixa de remoção de poeira). A distância central entre os dois pincéis precisa ser indicada por uma escala. A escova pode ser ajustada para cima e para baixo em 50 mm para facilitar o enfiamento, e há uma posição de ajuste precisa em 10 mm, o que é benéfico para ajustar o efeito de remoção de poeira. A velocidade de rotação da escova é ajustável de 0 a 300r/min.
- – Dispositivo de rolo de pressão de rebobinamento:Existe um conjunto de eixos de rebobinamento superior e inferior com mecanismos de rolo de pressão. A superfície dos rolos de pressão é cromada ou tratada com revestimento cerâmico para evitar a inversão da borda após o corte.
- – Dispositivo de eixo diferencial deslizante de rebobinamento:Existem dois eixos diferenciais de deslizamento de rebobinamento superior e inferior, que facilitam o enrolamento com velocidade diferencial. É equipado com placas de camada intermediária e permite o ajuste quantitativo da tensão multiplicada pelo número de tiras. Ele ajusta automaticamente a base de tensão de acordo com diferentes larguras de corte e pode definir a base de tensão por si só para garantir uma tensão constante e estável, evitando a quebra da correia durante o corte contínuo.
2.2 Estruturas-chave da máquina de corte
Os principais componentes do equipamento de corte incluem o mecanismo de controle de tensão constante para desenrolamento e rebobinamento, o mecanismo do eixo diferencial de deslizamento e o mecanismo de alinhamento da borda.
- Estrutura de controle de tensão constante
(1) Princípio de controle de tensão constante.O princípio do controle constante da tensão é essencial para os processos de desenrolamento e rebobinamento em operações de corte. À medida que o diâmetro do desenrolamento diminui e o diâmetro do rebobinamento aumenta, a tensão mudará continuamente devido ao controle constante da velocidade do motor. Essa variação na tensão pode levar ao enrugamento ou quebra do material se a tensão for muito baixa ou muito alta, respectivamente. Para evitar esses problemas, é necessário manter uma tensão constante durante o processo de desenrolamento e rebobinamento.
A essência do controle de tensão constante é ajustar o torque de saída do motor à medida que o diâmetro muda, mantendo a tensão inalterada. O controle de torque do motor é obtido através de um conversor de frequência e um motor assíncrono trifásico. O conversor de frequência da série Delta V fornece três portas de entrada analógica: AUI, AVI e ACI. Essas portas podem ser definidas para várias funções, com uma servindo como referência de torque e outra como limitação de velocidade.
Uma faixa de tensão de 0-10V corresponde a uma faixa de saída de 0 para o torque nominal do motor. Ajustando a tensão dentro da faixa de 0-10V, o controle de tensão constante pode ser alcançado.
- Cálculo de tensão e torque.A partir da análise cinética na Figura abaixo:
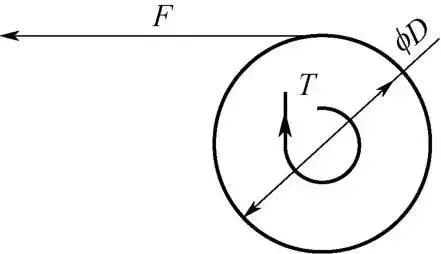
FD/2=Ti
Na equação, F representa tensão, D representa diâmetro, T representa torque do motor e i representa a relação de redução de engrenagem.
A expressão para o torque nominal do motor é:
T = 9550P/n
Na equação, T representa o torque nominal do motor em Newton-metros (N·m),
P representa a potência nominal do motor em quilowatts (kW) e n representa a velocidade nominal do motor em rotações por minuto (r/min).
(3) Cálculo da velocidade síncrona do motor:
O cálculo para a velocidade síncrona do motor é o seguinte:
n = 60f/p = 60 × 2/2 = 60 r/min
Na equação, f representa a frequência da fonte de alimentação em Hertz (Hz), n representa a velocidade do motor de rebobinamento em rotações por minuto (r / min) e p representa o número de pares de pólos do motor.
(4) Velocidade operação.Ao usar o controle de tensão no sistema, é necessário limitar a velocidade da máquina de corte para evitar fugas. A expressão para a velocidade de corrida V do rebobinamento é a seguinte:
V = πDn/i
Na equação, V representa a velocidade de funcionamento da máquina de corte em metros por minuto (m / min), D representa o diâmetro máximo do rebobinamento em metros (m), n representa a velocidade em rotações por minuto (r / min) e
Acessórios (5)UmControlador de tensão automático.O controlador automático de tensão consiste principalmente em um sensor de tensão, conversores A/D e D/A de alta precisão, um microcontrolador de alto desempenho e outros componentes. Este controlador automático de tensão constante opera comparando a tensão medida do material da banda do sensor de tensão com o ponto de ajuste de tensão alvo. Em seguida, ele utiliza cálculos PID realizados pelo microcontrolador para ajustar automaticamente a saída D/A, alterando assim a corrente de excitação da embreagem/freio de pó magnético ou o torque de um servo motor. Isso garante uma tensão constante no material da banda. O controlador automático de tensão pode ser amplamente utilizado em várias aplicações que requerem medição e controle precisos da tensão. Oferece flexibilidade na operação e possui uma ampla gama de aplicações. Ele permite a alternância perfeita entre os modos automático e manual, permitindo que os operadores alternem entre esses modos com base em seus requisitos específicos.
(6) Rebobinamento de tensão cônica. No processo de corte e rebobinamento do filme polarizador, o método de controle comum é adotar o enrolamento de tensão constante. Isso significa que a máquina de desenrolamento mantém uma tensão constante durante todo o processo, incluindo o início do enrolamento, o enrolamento contínuo e o fim do enrolamento. No entanto, ao enrolar o material em um núcleo ou mandril, há uma força reativa perceptível exercida pelo núcleo. Se o enrolamento de tensão constante for aplicado, pode facilmente resultar no fenômeno do filme saliente no centro do rolo e pode até danificar o equipamento. Para resolver esse problema, um esquema de controle de tensão cônica pode ser empregado. Essa abordagem alivia muito o problema acima mencionado. A curva de tensão cônica, conforme mostrado na Figura abaixo, se assemelha a um cone com um topo pontiagudo. Ele cria maior tensão no centro do rolo e diminui gradualmente a tensão em direção às camadas externas à medida que o diâmetro do rolo de material aumenta. Ao controlar a tensão, pode-se obter um enrolamento "mais apertado por dentro, mais solto por fora" do material, atendendo aos requisitos do processo para o enrolamento do material.
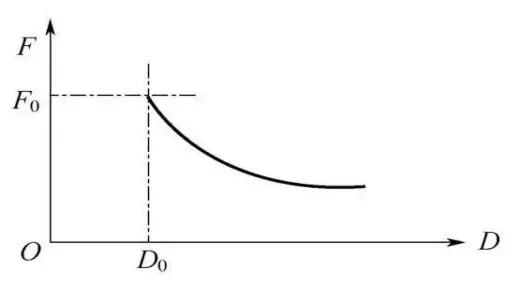
A fórmula da conicidade de tensão é expressa da seguinte forma:
F = F0 × [1 – K(1 – D0/D)]
Na equação, F representa a tensão de saída real em Newtons (N), F0 representa a tensão definida em Newtons (N), K representa o coeficiente de conicidade de tensão, D0 representa o diâmetro mínimo em metros (m) e D representa o diâmetro atual em metros (m).
2) UMAcorreção de alinhamento
(1) O fenômeno do "desvio".Durante o processo de corte e rebobinamento do filme polarizador, vários fatores, como revestimento irregular, tensão longitudinal irregular, bordas irregulares do filme, desalinhamento entre os rolos de transporte e atrito excessivo entre o filme cônico e a superfície do rolo podem fazer com que o filme sofra "desvio" durante o transporte. Para evitar esse fenômeno de desvio, uma correção de alinhamento de borda é instalada no equipamento de corte e rebobinamento.
(2) Métodos de correção.De acordo com a posição de instalação do equipamento de correção, ele pode ser dividido em dois tipos: correção bilateral e correção unilateral.
DCorreção de borda ual Em particular, para filmes polarizadores com bordas irregulares, desalinhamento ou formato de torre, ou quando é difícil alinhar o filme com a linha central da máquina durante o desenrolamento, dispositivos de correção de borda dupla são comumente usados em máquinas de desenrolamento. Geralmente, existem duas formas de correção de borda dupla.
Um método é o sistema de cabeçote de detecção dupla, também conhecido como Controle de Posição Central (CPC), conforme mostrado na Figura abaixo. Dois conjuntos de cabeçotes de detecção são posicionados simetricamente ao longo da linha central da máquina. Eles são acionados por um motor de passo através de um parafuso de avanço bidirecional, permitindo movimento síncrono para dentro ou para fora. Quando o filme entra na máquina, os cabeçotes de detecção se movem para dentro. Se apenas um dos cabeçotes detectar a borda do filme, isso indica que o filme se desviou nessa direção e um sinal é enviado para mover a máquina de desenrolamento e ajustar a posição do filme até que ambos os cabeçotes de detecção detectem as bordas do filme e emitam sinais iguais. Nesse ponto, os cabeçotes de detecção e a máquina de desenrolamento param de se mover e o filme fica na posição central. A vantagem desse método é que ele centraliza automaticamente o filme durante o processo de desenrolamento, sem a necessidade de considerar a largura do material.
O outro método é o Controle de Posição da Borda (EPC), que controla a posição das bordas do filme detectando-as. A estrutura do cabeçote de detecção é montada no lado da transmissão da máquina. As posições dos cabeçotes de detecção são predefinidas com base na largura do material recebido. Quando o filme de desenrolamento entra na máquina, os cabeçotes de detecção enviam sinais com base na extensão da cobertura (totalmente coberta, totalmente exposta ou parcialmente coberta) pelo filme. A máquina de desenrolamento se move para garantir que um lado da borda do filme permaneça em uma posição parcialmente coberta pelo cabeçote de detecção. A vantagem desse método é que ele requer apenas um único cabeçote de detecção, tornando o dispositivo relativamente mais simples. No entanto, a posição original do cabeçote de detecção precisa ser ajustada com antecedência com base nas diferentes larguras do material antes da operação.
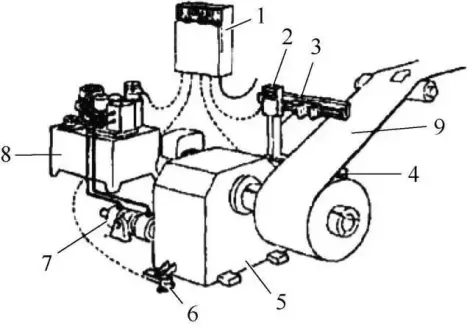
1-Gabinete de controle;2—Detector de controle de posição;3—Estrutura em forma de C;4—Fonte de luz transmissora;5—Máquina de desenrolamento;6—Detector de posição central;7—Cilindro hidráulico móvel;8—Estação hidráulica/servoválvula;9—Filme polarizador
Correção unilateral:Para filmes polarizadores com bordas relativamente uniformes, a correção de borda única é comumente usada. Filmes com bordas lisas são menos propensos a danos durante o transporte e manuseio. Para obter um enrolamento uniforme, um único conjunto de cabeçotes de detecção é usado para detectar as bordas do filme. O detector de controle de posição pode ser montado em um braço que se estende da máquina de desenrolamento e se move junto com a máquina de rebobinamento. Alternativamente, um suporte de cabeçote separado pode ser instalado próximo ao rolo de deflexão de saída da máquina. Um conjunto de parafusos acionados por um motor de passo move o cabeçote de detecção ou todo o suporte do cabeçote, que inclui um sensor de posição. O processo de trabalho desses dois métodos é o seguinte: Quando o filme é carregado no núcleo do enrolamento e preso, o cabeçote de detecção se move até detectar que a borda do filme cobre parcialmente a fonte de luz. Ao mesmo tempo, o sistema de controle de circuito fechado é acionado automaticamente. À medida que a posição da borda do filme muda, o cabeçote de detecção continua a seguir e insere o valor de deslocamento no sistema de controle. Isso faz com que o cilindro hidráulico de correção de borda da máquina de desenrolamento se mova na mesma direção e na mesma distância, obtendo um resultado de rebobinamento uniforme.
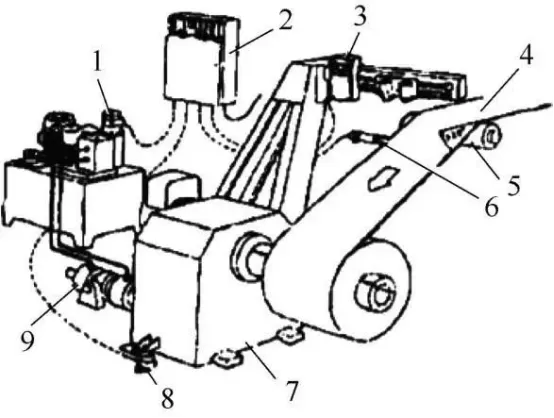
1 - Estação hidráulica / servoválvula; 2 - Gabinete de controle; 3 - Detector de controle de posição; 4 - Filme polarizador; 5 - Rolo de deflexão; 6 - Fonte de luz transmissora; 7 - Máquina de rebobinamento; 8 - Detector de posição central; 9 - Cilindro hidráulico em movimento
- Estrutura de corte de eixo deslizante
(1) Princípio de funcionamento.O eixo deslizante é baseado no princípio de deslizamento de vários anéis coletores no eixo para manter o equilíbrio da tensão entre vários rolos de material no eixo, facilitando o processo de corte e rebobinamento. O principal objetivo do eixo deslizante é ajustar a tensão do material durante o processo de rebobinamento. Ao manter a tensão adequada em todos os rolos durante a operação do eixo, o eixo deslizante melhora muito o rendimento e reduz os custos de produção, especialmente na aplicação de filme polarizador de bateria. É um componente importante da máquina de corte de bateria de lítio (talhadeira).
(2) Estrutura principal.O eixo deslizante possui uma estrutura especial composta por vários anéis coletores. Durante a operação, os anéis coletores são controlados para escorregar com um determinado valor de torque, compensando com precisão a diferença de velocidade gerada. Isso permite um controle preciso da tensão de cada rolo de material, garantindo um enrolamento de tensão constante e garantindo a qualidade do enrolamento. Pode ser aplicado em uma ampla faixa de tensão, de níveis muito baixos a altos. O eixo deslizante é adequado para aplicações que exigem altas velocidades, grandes variações de espessura do material, controle de tensão em vários estágios, controle de tensão de alta precisão e enrolamento de face final. É particularmente adequado para uso em máquinas de corte longitudinal de enrolamento central de eixo duplo.
(3)Produtos representativos.O eixo deslizante Tōshin do Japão e o eixo deslizante Nishimura são conhecidos por sua alta precisão de controle, embora tenham um custo relativamente mais alto. A unidade principal do eixo deslizante é a unidade de expansão pneumática, que consiste em uma câmara, placa inferior inclinada, pistão, vedação de ar, rolamentos, molas e placas de expansão. Cada unidade tem um comprimento de 40 mm e as 18 unidades podem ser trocadas e substituídas independentemente em qualquer posição, melhorando assim a vida útil e a facilidade de manutenção.
(4) Tecnologia de materiais.O corpo principal do produto é feito de aço de molde temperado e temperado ou liga de alumínio com revestimento anodizado duro. As placas de expansão de borracha são feitas de material de poliuretano resistente a altas temperaturas e ao desgaste e são vulcanizadas de acordo, dependendo dos requisitos de tensão máxima. Diferentes tamanhos de eixos deslizantes podem ser personalizados com base em requisitos específicos, incluindo componentes como eixo principal, unidade de expansão pneumática, placas de expansão, molas e juntas universais.
(5)Instruções de uso.O eixo deslizante aumenta significativamente a velocidade, a precisão do rebobinamento, o nível de automação, reduz o tempo de configuração e melhora a facilidade de uso da máquina de corte. A aplicação de eixos deslizantes no rebobinamento melhora muito o rendimento de produtos de qualidade e reduz os custos de produção. Nosso eixo deslizante garante a mais alta qualidade dos rolos de material, mantendo a tensão adequada em todos os rolos durante a operação.
2.3 Qual é a diferença entre o corte da folha do eletrodo e o outro corte comum da placa de metal?
Comparado ao processo de corte de materiais de chapa metálica, o método de corte para discos de eletrodo de bateria de lítio tem características completamente diferentes:
Durante o corte do disco de eletrodo, as lâminas circulares superior e inferior têm um ângulo de inclinação negativo, semelhante às lâminas da tesoura, com uma largura de borda muito pequena. Não há folga horizontal entre as lâminas circulares superior e inferior (o parâmetro c no diagrama é equivalente a um valor negativo), mas sim, as lâminas superior e inferior entram em contato umas com as outras e exercem pressão lateral.
No corte de material de folha, existem rolos de suporte de borracha acima e abaixo, que equilibram a força de cisalhamento e o torque de cisalhamento gerado durante o corte, evitando assim a deformação significativa do material de folha. No entanto, no corte de disco de eletrodo, não há rolos de suporte superior e inferior.
O revestimento do disco do eletrodo é um material compósito composto de partículas e tem pouca capacidade de deformação plástica. Quando a tensão interna gerada pelas lâminas circulares superior e inferior excede a força coesiva entre as partículas de revestimento, rachaduras se formam no revestimento e se propagam, levando à separação.
2.4 Quais são os pontos-chave do corte?
1. Influência das propriedades físicas e mecânicas dos materiais
Em geral, materiais com boa plasticidade tendem a retardar o aparecimento de fissuras durante o cisalhamento, resultando em uma maior profundidade do material sendo cisalhado e uma maior proporção de zona de cisalhamento brilhante. Por outro lado, materiais com baixa plasticidade são mais propensos a fraturas sob as mesmas condições de parâmetros, resultando em uma maior proporção de zona de rasgo na superfície de fratura e uma zona de cisalhamento brilhante naturalmente menor.
- A influência dos pares superior e inferior na pressão lateral da ferramenta
No processo de corte de discos de eletrodos, a pressão lateral exercida pela ferramenta é um dos principais fatores que afetam a qualidade do corte. Durante o cisalhamento, o alinhamento das fissuras superior e inferior na superfície da fratura e o estado tensão-deformação da força de corte estão intimamente relacionados com a magnitude da pressão lateral. Se a pressão lateral for muito baixa, podem ocorrer defeitos como superfícies de corte irregulares e perda de material durante o corte dos discos dos eletrodos. Por outro lado, se a pressão for muito alta, a ferramenta estará mais propensa a desgaste, resultando em uma vida útil mais curta.
- A influência da quantidade de sobreposição das ferramentas emparelhadas superior e inferior (parâmetro δ na figura acima)
A configuração da quantidade de sobreposição está relacionada principalmente à espessura do disco do eletrodo. Uma quantidade razoável de sobreposição é benéfica para o engate da ferramenta e tem impacto na qualidade do corte, no tamanho das rebarbas e na taxa de desgaste da aresta da ferramenta.
- Influência do ângulo de mordida (parâmetro α na figura acima)
No corte a disco, o ângulo de mordida refere-se ao ângulo entre o segmento de corte e a linha central da folha que está sendo cortada. À medida que o ângulo de mordida aumenta, o componente horizontal da força de corte também aumenta. Se a força horizontal exceder a tensão de alimentação do disco do eletrodo, o material da folha pode escorregar ou arquear na frente da lâmina circular, impossibilitando a execução do corte. Por outro lado, reduzir o ângulo de mordida requer um aumento no diâmetro da lâmina, o que, por sua vez, requer dimensões maiores para a máquina de corte. Portanto, o equilíbrio do ângulo de mordida, diâmetro da lâmina, espessura da chapa e quantidade de sobreposição deve ser determinado com base nas condições reais de trabalho.
2.5 Defeitos
Os principais defeitos no corte da folha do eletrodo incluem o seguinte:
- Rebarba
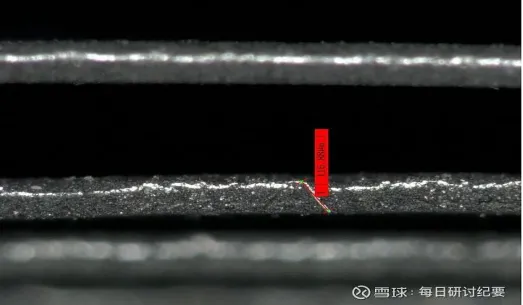
As rebarbas, especialmente as de metal, representam um risco significativo para as baterias de lítio. Rebarbas de metal maiores podem penetrar diretamente no separador, causando um curto-circuito entre os eletrodos positivo e negativo. O processo de corte de discos de eletrodo é a principal fonte de geração de rebarbas na fabricação de baterias de íons de lítio. A imagem acima mostra a morfologia típica das rebarbas metálicas geradas durante o corte dos discos dos eletrodos. Devido ao controle de tensão instável durante o corte, ocorre o corte secundário, resultando em rebarbas de folha com dimensões superiores a 100μm. Para evitar essa situação, é crucial encontrar a pressão lateral e a sobreposição da ferramenta mais adequadas com base nas propriedades e espessura do disco do eletrodo durante o ajuste da ferramenta. Além disso, chanfrar a lâmina e ajustar a tensão da bobina pode ajudar a melhorar a qualidade da borda do disco do eletrodo.
borda 2.wavy
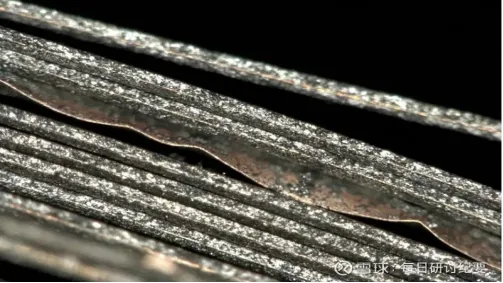
Durante o corte dos discos dos eletrodos, a sobreposição e a pressão inadequadas da ferramenta podem resultar em bordas onduladas e delaminação do revestimento no corte. Quando ocorrem bordas onduladas, pode haver desvio de borda e vibração durante o corte e enrolamento dos discos dos eletrodos, levando a uma diminuição na precisão do processo. Além disso, pode ter um impacto negativo na espessura final e na aparência da bateria.
03 Casos de seleção e aplicação de máquina de corte
(1) Seleção de equipamentos:
A seleção de uma máquina de corte deve considerar fatores como precisão de corte, precisão do equipamento de corte e faixa de ajuste da lâmina.
(2) Caso de aplicação:
Tomando a máquina de corte ZY750-C600-C50 da Chaoyang Machinery Manufacturing Co., Ltd. como exemplo, é um equipamento de corte de bateria de lítio totalmente automático do tipo C com uma largura máxima de entrada de 750 mm, um diâmetro de rebobinamento e desenrolamento de φ600 mm, uma largura mínima de corte de 30 mm e uma velocidade de operação de 50 m/min. O equipamento está equipado com um sistema de detecção CCD para detectar problemas como danos e rugas no disco do eletrodo.
04 Uso e manutenção da máquina de corte
(1) Uso da máquina de corte:
Tomando o exemplo da máquina de corte modelo 65 de uma determinada empresa, o uso da máquina de corte é descrito. A figura abaixo mostra a interface principal do sistema. Ao clicar em "Entrar no sistema", você pode acessar o sistema. A interface do botão operacional é mostrada na Figura abaixo, e as explicações de cada botão funcional são as seguintes.
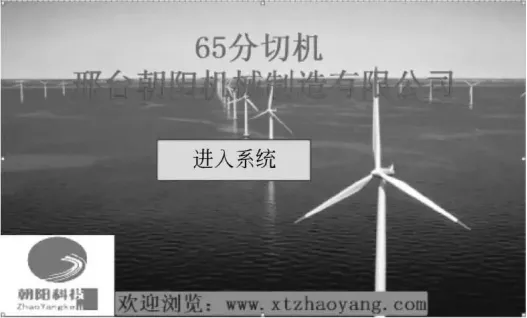
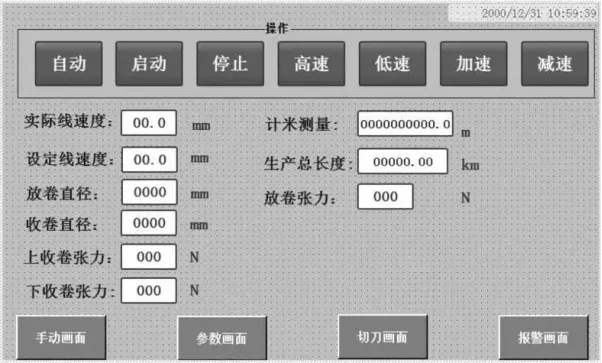
Medição de comprimento: O comprimento produzido no modo de operação automática pode ser zerado.
Comprimento total de produção: O comprimento acumulado durante o modo de operação automática, que não pode ser zerado.
Definir velocidade da linha: A velocidade de operação atual definida pelo usuário através da IHM (ou controlador de velocidade).
Velocidade real da linha: A velocidade em tempo real na qual a máquina está funcionando no momento.
Aumento de velocidade (+): Pressionar este botão aumenta a velocidade atual em 1m/min (o valor de incremento pode ser definido).
Diminuição de velocidade (-): Pressionar este botão diminui a velocidade atual em 1m/min (o valor de decréscimo pode ser definido).
Tensão de desenrolamento: A tensão em tempo real detectada pelo sensor de tensão de desenrolamento.
Diâmetro de rebobinamento: O diâmetro em tempo real do material rebobinado.
Tensão de rebobinamento superior: A tensão em tempo real do rebobinamento superior.
Tensão de rebobinamento inferior: A tensão em tempo real do rebobinamento inferior.
Tela de parâmetros: Acessando a tela de parâmetros para definir parâmetros como velocidade de tração, tensão de desenrolamento, tensão de rebobinamento, torque de tração, etc.
Tela do cortador: Acessando a tela do cortador para definir o comprimento de uso do cortador, redefinir vários valores de comprimento e determinar se o cortador deve ser ativado.
Manual: Acessando a tela de operação de depuração manual para controlar manualmente funções como desenrolar, retroceder, escovar e parar/iniciar a lâmina.
Automático: Selecionando o modo automático.
Início: Iniciando toda a linha (válido no modo automático).
Parar: Parando toda a linha (válido no modo automático).
Alta velocidade: Executando a máquina em alta velocidade.
Baixa velocidade: Executando a máquina em baixa velocidade.
(2) Instalação e comissionamento da máquina de corte:
A operação da máquina de corte envolve três etapas: ajuste de tensão, ajuste de correção de alinhamento EPC e comissionamento da válvula proporcional elétrica de rebobinamento. O comissionamento da válvula proporcional elétrica é uma etapa crítica e o procedimento é o seguinte:
- Conecte a fonte de alimentação de 24 V de acordo com os requisitos de fiação.
- Forneça ar comprimido para a válvula proporcional dentro da faixa de 0,5-0,65MPa.
- Pressione e segure o botão "Desbloquear" ou "Bloquear" por mais de 3 segundos até que a luz indicadora pisque.
- Pressione o botão SET intermitentemente para exibir GL.9/F01/F02 (F01 = limite inferior, F02 = limite superior).
- Quando F01 for exibido com um número piscando, pressione o botão diminuir ou aumentar para diminuir ou aumentar o número. Geralmente, F01 = 0,15-0,25.
- Quando F02 for exibido com um número piscando, pressione o botão diminuir ou aumentar para diminuir ou aumentar o número. Geralmente, F02 = 0,45-0,50.
- Pressione o botão SET após concluir o processo de depuração.
(3) Precauções e manutenção para operar uma máquina de corte:
1) Os operadores devem receber treinamento antes de iniciar o trabalho e estar familiarizados com a operação da máquina de corte, desempenho do equipamento e métodos gerais de manutenção. Pessoal que não é treinado para este trabalho não deve operar a máquina.
2) Tome as medidas de proteção do trabalho necessárias antes de ligar a máquina. Prepare ferramentas e materiais auxiliares (como ferramentas de ajuste de faca, caixas necessárias, tubos de papel, facas de corte, fita adesiva, etc.) e coloque-os em uma posição adequada na máquina.
3) Certifique-se de que o equipamento esteja em condições seguras. Ligue o interruptor elétrico, verifique se há fases ausentes no circuito e certifique-se de que o circuito de ar esteja desobstruído. Execute a máquina em uma operação de teste e verifique se os equipamentos elétricos, pneumáticos e mecânicos estão funcionando corretamente.
4) Verifique se os dispositivos mecânicos de segurança estão no lugar. Durante a operação, evite esmagar, arranhar ou ficar preso em engrenagens rotativas, correntes e rolos.
5) Ajuste da faca: Ajuste a distância da faca com precisão de acordo com os requisitos do trabalho e preste atenção à direção da lâmina. Se necessário, remova a faca inferior e reorganize-a. Repare ou substitua a lâmina se estiver danificada ou não afiada.
6) Verifique a conexão do dispositivo de eliminação estática e o fio de aterramento da máquina para garantir que a eletricidade estática seja eliminada durante a operação. Coloque resíduos de papel sob a máquina para evitar o acúmulo de poeira.
7) Preste atenção à segurança ao alimentar materiais. Empurre o material para a posição apropriada para a inflação e preste atenção ao sentido de rotação do material. Não carregue o material ao contrário.
8) Rosqueamento do material e alinhamento da borda: Rosqueie o material do desenrolamento para o rebobinamento de acordo com a direção definida pelo equipamento, ajuste o alinhamento da borda e certifique-se de que ambos os lados do produto acabado tenham adesivo. Preste atenção ao alinhamento da borda durante a alimentação. Deve ser alinhado no meio do curso de alinhamento. Se o material não puder ser cortado na borda quando exceder o traçado, tome medidas imediatas para resolver o problema.
9) Coloque o tubo de papel necessário no eixo de rebobinamento e alinhe o material. Se for necessária fita dupla-face, certifique-se de que ela seja aplicada corretamente. Ajuste a tensão apropriada para rebobinar e desenrolar e execute o corte e o rebobinamento da borda.
10) Durante o processo de rebobinamento, inspecione cuidadosamente a qualidade do produto. Evite rolar em produtos defeituosos ou residuais, sujeira ou guarnições de borda. Controle rigorosamente o comprimento.
11) Após o desligamento, desligue a energia e o suprimento de ar e execute a limpeza e manutenção necessárias na máquina. Evite usar uma faca para raspar o rolo de transferência. Limpe qualquer adesivo do equipamento com solvente.
12) Em caso de problemas durante a operação, pare a máquina para solução de problemas. Se não for possível parar a máquina, trate a situação com cuidado e reduza a velocidade, se necessário.