As máquinas de fabricação de baterias são os heróis anônimos por trás do rápido avanço das tecnologias de armazenamento de energia. Essas máquinas altamente especializadas automatizam e agilizam a produção de baterias, garantindo precisão, eficiência e consistência em vários setores. De veículos elétricos a eletrônicos de consumo e sistemas de energia renovável, as máquinas de fabricação de baterias desempenham um papel fundamental no atendimento à crescente demanda por baterias de alto desempenho. Este blog investiga os meandros dessas máquinas, explorando seus tipos, componentes-chave, mecanismos de trabalho e aplicações. Além disso, destaca a importância de condições ideais de trabalho, medidas de controle de qualidade, precauções de segurança e manutenção de rotina para garantir desempenho e longevidade ideais. Seja você um profissional do setor ou um entusiasta curioso, este guia abrangente fornecerá informações valiosas sobre o mundo da fabricação de baterias.
O que é uma máquina de fabricação de baterias?
Uma máquina de fabricação de baterias é um equipamento especializado projetado para automatizar e agilizar a produção de baterias. Essas máquinas são essenciais na produção em massa de vários tipos de baterias, incluindo baterias de íons de lítio, chumbo-ácido e níquel-hidreto metálico. Eles lidam com vários estágios do processo de produção da bateria, desde a preparação do eletrodo até a montagem final, garantindo alta precisão, eficiência e consistência. Ao integrar tecnologias avançadas, como robótica, IA e IoT, as máquinas modernas de fabricação de baterias podem reduzir significativamente o erro humano, aumentar a velocidade de produção e melhorar a qualidade geral do produto.
Tipos de máquinas de fabricação de baterias
As máquinas de fabricação de baterias vêm em vários tipos, cada uma adaptada a estágios específicos do processo de produção de baterias. Aqui estão alguns tipos comuns:
- Máquinas de revestimento de eletrodos:Essas máquinas aplicam materiais ativos em folhas de metal para criar os eletrodos da bateria (ânodo e cátodo).
- Calandradoras:Usado para comprimir e alisar os eletrodos revestidos para garantir espessura e densidade uniformes.
- Máquinas de corte:Corte os eletrodos revestidos em larguras precisas para processamento posterior.
- Máquinas de empilhamento/enrolamento:Monte os eletrodos e separadores na estrutura de célula de bateria desejada (por exemplo, prismática, cilíndrica ou bolsa).
- Máquinas de montagem:Lidar com a montagem final das células da bateria, incluindo invólucro, vedação e enchimento de eletrólitos.
- Máquinas de formação e teste:Carregue e teste as baterias para garantir que atendam aos padrões de desempenho e segurança.
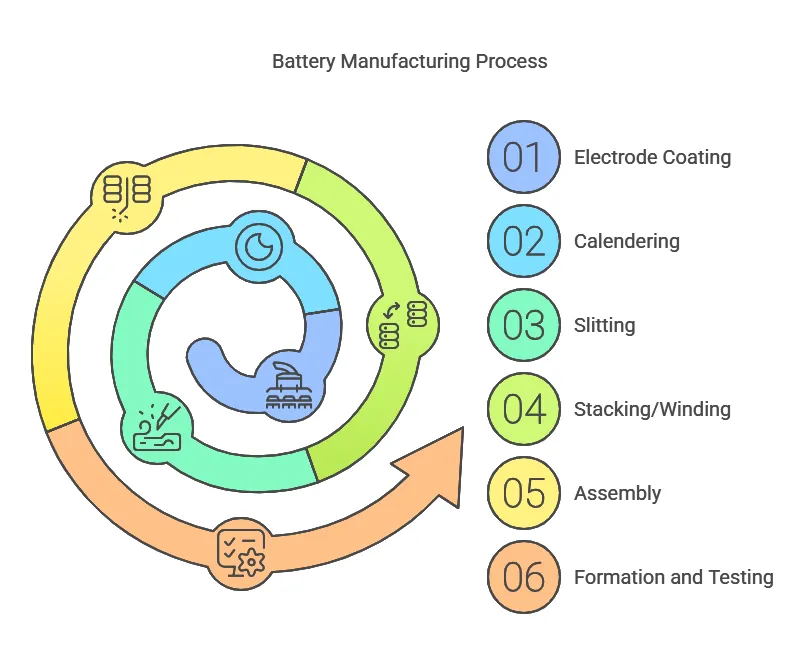
Cada tipo de máquina desempenha um papel crítico para garantir a eficiência e confiabilidade da linha de produção de baterias.
Como funciona uma máquina de fabricação de baterias?
As máquinas de fabricação de baterias operam por meio de uma série de processos automatizados que transformam matérias-primas em baterias totalmente funcionais. Aqui está um detalhamento passo a passo de como essas máquinas funcionam:
1. Preparação do eletrodo:
Matérias-primas como lítio, cobalto e grafite são misturadas em uma pasta.
A pasta é revestida em folhas de metal usando máquinas de revestimento de eletrodo.
As folhas revestidas são secas e comprimidas por máquinas de calandragem.
2. Corte do eletrodo:
As máquinas de corte cortam as folhas revestidas em tiras precisas.
3. Montagem da célula:
As máquinas de empilhamento ou enrolamento colocam os eletrodos e separadores em camadas para formar a célula da bateria.
A célula é então colocada em um invólucro.
4. Enchimento de eletrólitos:
As máquinas de montagem injetam a solução eletrolítica na célula.
5. Vedação e acabamento:
A célula é selada e preparada para o processo de formação.
6. Formação e teste:
As máquinas de formação carregam a bateria pela primeira vez.
As máquinas de teste avaliam o desempenho, a capacidade e a segurança da bateria.
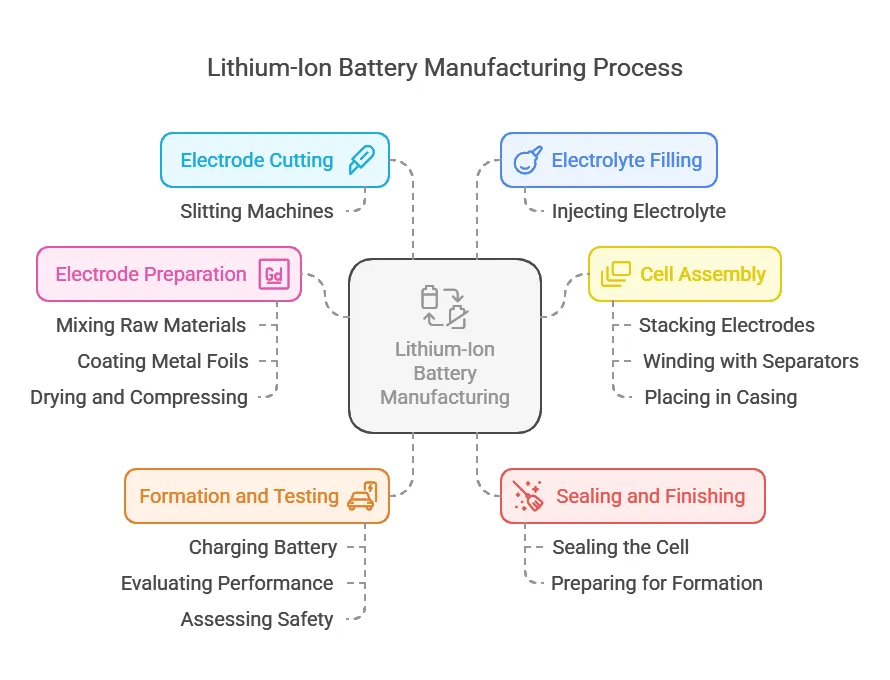
Ao automatizar essas etapas, as máquinas de fabricação de baterias garantem alta precisão, consistência e escalabilidade na produção.
Principais componentes de uma máquina de fabricação de baterias
As máquinas de fabricação de baterias são sistemas complexos compostos por vários componentes críticos. Esses componentes trabalham juntos para garantir a produção eficiente e precisa de baterias. Os principais componentes incluem:
- Cabeça de revestimento:Aplica a pasta do eletrodo em folhas de metal com alta precisão.
- Forno de secagem:Remove a umidade dos eletrodos revestidos para garantir a adesão adequada.
- Rolos de calandragem:Comprima os eletrodos para atingir a espessura e densidade desejadas.
- Lâminas de corte:Corte os eletrodos em larguras precisas para processamento posterior.
- Braços robóticos:Manuseie e monte os componentes da bateria com alta precisão.
- Sistema de enchimento de eletrólitos:Injeta com precisão o eletrólito na célula da bateria.
- Câmaras de formação:Fornecer ambientes controlados para o carregamento e descarregamento inicial de baterias.
- Sensores de controle de qualidade:Monitore e garanta a consistência e segurança do produto final.
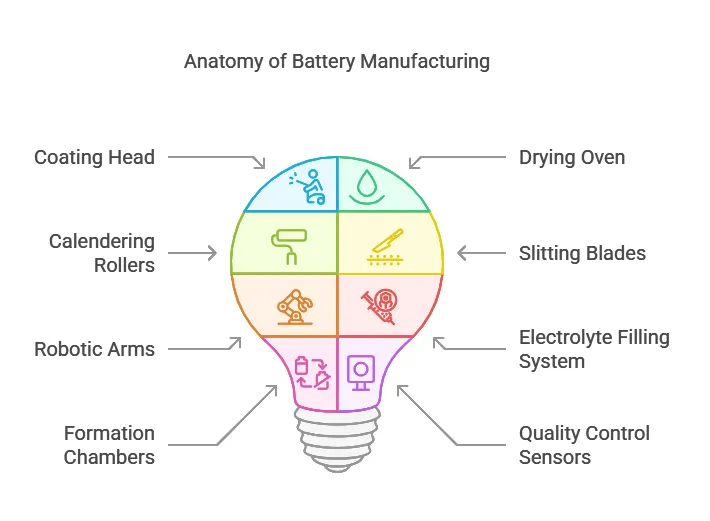
Cada componente é projetado para atender aos rigorosos requisitos de produção de baterias, garantindo alto desempenho e confiabilidade.
O processo de produção da bateria envolve várias etapas críticas, cada uma exigindo maquinário especializado e controle preciso. Aqui está um guia passo a passo detalhado:
1. Preparação da matéria-prima:
Misture materiais ativos, aglutinantes e solventes para criar pastas de eletrodos.
2. Revestimento do eletrodo:
Use máquinas de revestimento para aplicar a pasta em folhas de metal (ânodo e cátodo).
3. Secagem:
Passe as folhas revestidas pelos fornos de secagem para remover solventes e umidade.
4. Calandragem:
Comprima os eletrodos secos usando máquinas de calandragem para obter uma espessura uniforme.
5. Corte:
Corte os eletrodos em tiras precisas usando máquinas de corte.
6. Montagem da célula:
Empilhe ou enrole os eletrodos e separadores para formar a célula da bateria.
Coloque a célula em um invólucro.
7. Enchimento de eletrólitos:
Injete a solução eletrolítica na célula usando sistemas de enchimento automatizados.
8. Vedação:
Sele a célula para evitar vazamentos e garantir a segurança.
9. Formação:
Carregue e descarregue a bateria pela primeira vez para ativar suas propriedades eletroquímicas.
10. Teste e controle de qualidade:
Teste a capacidade da bateria, voltagem e segurança.
Classifique e embale as baterias para distribuição.
Seguindo essas etapas, as máquinas de fabricação de baterias garantem a produção de baterias de alta qualidade que atendem aos padrões da indústria.
Aplicações de máquinas de fabricação de baterias em diferentes indústrias
As máquinas de fabricação de baterias são ferramentas versáteis que desempenham um papel crucial em várias indústrias. Sua capacidade de produzir baterias de alta qualidade, eficientes e confiáveis as torna indispensáveis em setores como:
1. Indústria automotiva:
Usado para fabricar baterias para veículos elétricos (EVs), veículos híbridos e sistemas start-stop.
Garante a produção de baterias de íons de lítio de alta capacidade com longa vida útil.
2. Eletrônicos de consumo:
Produz baterias para smartphones, laptops, tablets e dispositivos vestíveis.
Concentra-se em baterias compactas, leves e de alta densidade de energia.
3. Armazenamento de energia renovável:
Fabrica baterias para sistemas de armazenamento de energia solar e eólica.
Permite armazenamento eficiente de energia e estabilização da rede.
4. Equipamento industrial:
Fornece baterias para empilhadeiras, veículos guiados automatizados (AGVs) e outras máquinas industriais.
Enfatiza a durabilidade e o alto desempenho em ambientes exigentes.
5. Dispositivos médicos:
Produz baterias para equipamentos médicos portáteis, como bombas de insulina e aparelhos auditivos.
Garante altos padrões de segurança e confiabilidade para aplicações críticas.
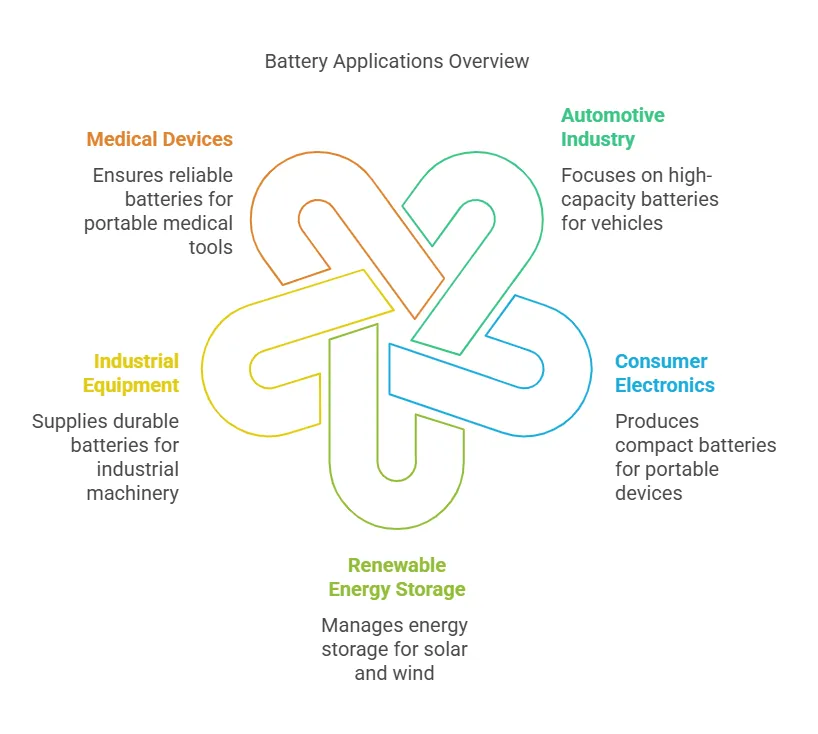
Ao atender a esses diversos setores, as máquinas de fabricação de baterias impulsionam a inovação e suportam a crescente demanda por soluções avançadas de armazenamento de energia.
Condições de trabalho ideais para máquinas de fabricação de baterias
Para garantir desempenho e longevidade ideais, as máquinas de fabricação de baterias requerem condições de trabalho específicas. Essas condições incluem:
1. Ambiente Controlado:
A temperatura e a umidade devem ser reguladas para evitar a degradação do material e garantir uma qualidade de produção consistente.
Faixa de temperatura ideal: 20–25°C (68–77°F).
Nível de umidade ideal: Abaixo de 30%.
2. Instalações de sala limpa:
Poeira e material particulado podem contaminar os componentes da bateria, levando a defeitos.
Salas limpas com padrões ISO Classe 5–7 são recomendadas.
3. Fonte de alimentação estável:
Flutuações na potência podem interromper as operações da máquina e afetar a qualidade do produto.
Os sistemas de fonte de alimentação ininterrupta (UPS) são frequentemente usados para manter a estabilidade.
4. Ventilação adequada:
É necessária ventilação adequada para dissipar o calor e remover os vapores gerados durante a produção.
5. Calibração regular:
As máquinas devem ser calibradas com frequência para manter a precisão e a exatidão.
Ao manter essas condições ideais de trabalho, os fabricantes podem maximizar a eficiência e a confiabilidade de suas linhas de produção de baterias.
Medidas comuns de controle de qualidade na fabricação de baterias
O controle de qualidade é um aspecto crítico da fabricação de baterias, garantindo que os produtos finais atendam aos padrões de segurança, desempenho e confiabilidade. Aqui estão algumas medidas comuns:
1. Inspeção de material:
As matérias-primas são testadas quanto à pureza, consistência e conformidade com as especificações.
2. Monitoramento em processo:
Sensores e câmeras são usados para monitorar a espessura do revestimento, o alinhamento do eletrodo e outros parâmetros durante a produção.
3. Verificações dimensionais:
Eletrodos e separadores são medidos para garantir que atendam a tolerâncias dimensionais precisas.
4. Precisão de enchimento de eletrólitos:
Os sistemas automatizados garantem que a quantidade correta de eletrólito seja injetada em cada célula.
5. Formação e teste:
As baterias passam por ciclos iniciais de carga e descarga para ativar suas propriedades eletroquímicas.
Métricas de desempenho como capacidade, tensão e resistência interna são medidas.
6. Teste de segurança:
As baterias são submetidas a testes de estresse, incluindo sobrecarga, curto-circuito e choque térmico, para garantir a segurança.
7. Inspeção final:
Inspeções visuais e automatizadas são realizadas para identificar defeitos antes da embalagem.
Essas medidas ajudam os fabricantes a fornecer baterias de alta qualidade que atendem aos padrões da indústria e às expectativas dos clientes.
Precauções de segurança ao operar uma máquina de fabricação de baterias
A operação de máquinas de fabricação de baterias envolve o manuseio de materiais perigosos e processos de alta energia, tornando a segurança uma prioridade. As principais precauções incluem:
1. Equipamento de Proteção Individual (EPI):
Os operadores devem usar luvas, óculos de proteção e roupas de proteção para evitar a exposição a produtos químicos e objetos pontiagudos.
2. Treinamento adequado:
Os operadores devem receber treinamento abrangente sobre operação da máquina, procedimentos de emergência e identificação de perigos.
3. Sistemas de ventilação:
Garanta ventilação adequada para remover vapores tóxicos e evitar o acúmulo de gases inflamáveis.
4. Medidas de segurança contra incêndio:
Instale extintores de incêndio, detectores de fumaça e sistemas de sprinklers na área de produção.
Use materiais não inflamáveis sempre que possível.
5. Proteção da máquina:
Equipe as máquinas com proteções de segurança para evitar o contato acidental com peças móveis.
6. Desligamento de emergência:
Certifique-se de que todas as máquinas tenham botões de parada de emergência facilmente acessíveis.
7. Inspeções regulares:
Realize inspeções de rotina para identificar e abordar possíveis riscos de segurança.
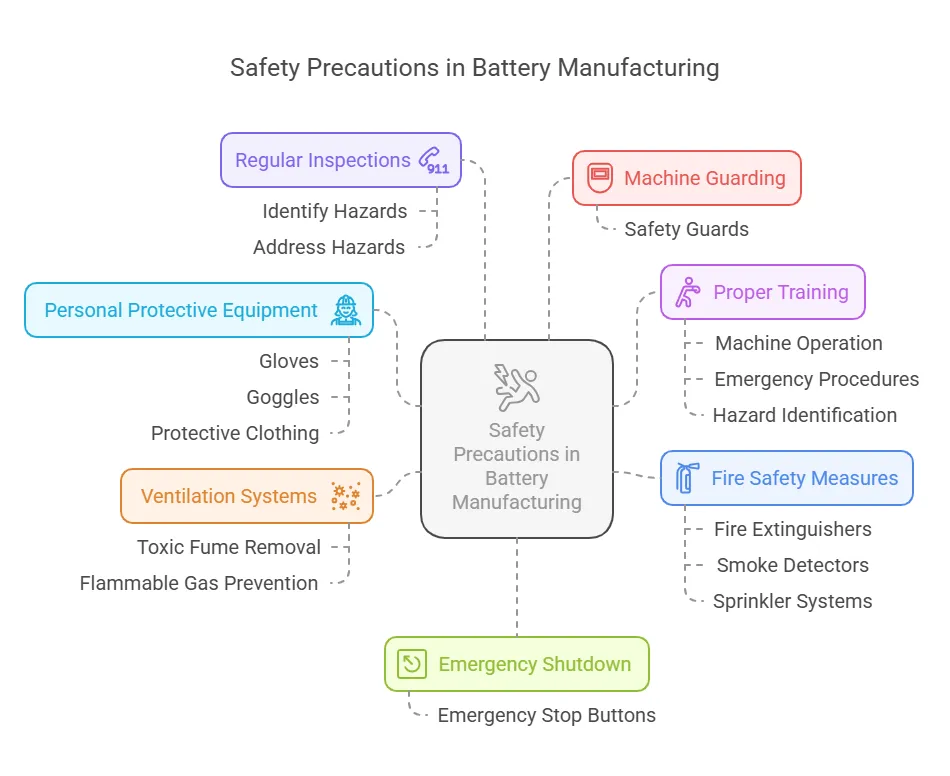
Seguindo essas precauções, os fabricantes podem criar um ambiente de trabalho mais seguro e reduzir o risco de acidentes.
Manutenção de rotina e solução de problemas para máquinas de fabricação de baterias
A manutenção regular e a solução de problemas oportuna são essenciais para manter as máquinas de fabricação de baterias funcionando sem problemas. Aqui está um guia passo a passo:
Manutenção de rotina:
1. Verificações diárias:
Inspecione as máquinas quanto a danos ou desgaste visíveis.
Limpe as superfícies para remover poeira e detritos.
2. Manutenção semanal:
Lubrifique as peças móveis para reduzir o atrito e evitar o desgaste.
Verifique e aperte os parafusos e conexões soltos.
3. Manutenção mensal:
Calibre sensores e dispositivos de medição para garantir a precisão.
Substitua componentes desgastados, como lâminas de corte ou cabeçotes de revestimento.
4. Manutenção trimestral:
Realize uma inspeção completa dos sistemas elétricos e da fiação.
Teste os recursos de segurança, incluindo botões de parada de emergência e alarmes.
Solução de problemas comuns:
1. Revestimento irregular:
Verifique a viscosidade da pasta e o alinhamento do cabeçote de revestimento.
Inspecione o forno de secagem quanto à consistência da temperatura.
2. Atolamentos da máquina:
Limpe quaisquer obstruções no caminho de alimentação do material.
Certifique-se de que as lâminas de corte estejam afiadas e alinhadas corretamente.
3. Falhas elétricas:
Inspecione a fiação e as conexões quanto a danos.
Teste a estabilidade da fonte de alimentação.
4. Qualidade de saída reduzida:
Verifique a calibração de sensores e dispositivos de medição.
Verifique se há desgaste em componentes críticos.
Seguindo essas etapas de manutenção e solução de problemas, os fabricantes podem minimizar o tempo de inatividade, prolongar a vida útil da máquina e manter uma qualidade de produção consistente.
Em conclusão, as máquinas de fabricação de baterias são ferramentas indispensáveis na produção de baterias de alta qualidade que alimentam nosso mundo moderno. Desde a preparação do eletrodo até a montagem final, essas máquinas automatizam processos complexos com precisão e eficiência, garantindo consistência e escalabilidade. Suas aplicações abrangem setores como automotivo, eletrônicos de consumo, energia renovável e dispositivos médicos, impulsionando a inovação e atendendo à demanda cada vez maior por soluções de armazenamento de energia. Para manter seu desempenho, é crucial operar essas máquinas em condições ideais, implementar rigorosas medidas de controle de qualidade e aderir a rígidos protocolos de segurança. A manutenção regular e a solução de problemas oportuna aumentam ainda mais sua confiabilidade e vida útil. À medida que o mundo continua a fazer a transição para a energia sustentável, as máquinas de fabricação de baterias permanecerão na vanguarda, permitindo a produção de baterias avançadas que moldam o futuro da tecnologia e do armazenamento de energia.