As baterias de íons de lítio são normalmente combinadas em série ou paralelamente para formar uma bateria de energia para atender aos requisitos de desempenho. À medida que o número de baterias individuais aumenta, a questão da consistência da bateria se torna mais proeminente. A inconsistência nas baterias pode levar a uma série de problemas, como redução da vida útil da bateria, diminuição do desempenho e comprometimento da segurança da bateria. A inconsistência das baterias individuais decorre principalmente do processo de fabricação ou armazenamento, bem como do processo de uso.
Durante o processo de produção, a inconsistência é frequentemente reduzida indiretamente pelo controle da precisão do processo de fabricação. No entanto, isso só pode minimizar as diferenças iniciais de parâmetros e não pode eliminá-las completamente. A consistência das baterias exibe transitividade e cumulatividade, pois é influenciada por vários fatores que interagem. Mesmo pequenas diferenças nos parâmetros iniciais podem ser bastante ampliadas durante o uso.
Para melhorar essa situação, podemos adotar uma abordagem combinada de vários aspectos, como produção de baterias, classificação de baterias, balanceamento de baterias e gerenciamento térmico da bateria de energia. Este artigo compartilha os dados de teste do processo de produção de baterias de íon de lítio de enrolamento prismático de todas as abas e analisa sua consistência.
O design específico e o processo de produção da bateria são os seguintes: O material do eletrodo positivo da bateria usa um sistema ternário, enquanto o eletrodo negativo usa grafite artificial. A bateria é montada de maneira sinuosa e envolta em um invólucro de alumínio. O processo de folhas de eletrodos, rolos de gelatina de enrolamento e montagem da bateria é mostrado na Figura 1.
Durante o enrolamento da bateria de todas as abas, a disposição das folhas e separadores de eletrodos é mostrada na Figura 1. As bordas laterais da folha de eletrodo positivo (15) sem revestimento durante a aplicação de material de eletrodo positivo (30) e o lado em branco (14) da folha de eletrodo negativo durante a aplicação de material de eletrodo negativo (40) são respectivamente soldados como abas de orelha nos coletores de corrente positiva e negativa. As folhas de eletrodo positivo e negativo são separadas por um separador (170) e os coletores de corrente positiva e negativa são expostos em ambos os lados do rolo de gelatina do enrolamento, diretamente conectados aos eletrodos positivo e negativo da bateria.
Ao melhorar as características de potência do ponto de vista das guias, a distância do fluxo de corrente é reduzida, resultando em uma distribuição uniforme da densidade de corrente em altas taxas de descarga, permitindo alta densidade de potência e reduzindo a geração de calor das folhas de eletrodos.
Após a montagem da tampa superior, a aba do eletrodo positivo com coletor de corrente em branco é soldada ao barramento positivo e a aba do eletrodo negativo com coletor de corrente em branco é soldada ao barramento negativo usando soldagem a laser ou soldagem por resistência. Quando a capacidade de projeto é grande, dois rolos de gelatina de enrolamento podem ser conectados em paralelo. Durante o processo de soldagem, vários rolos de geléia de enrolamento podem ser conectados primeiro em paralelo e depois soldados, ou cada rolo de geléia de enrolamento pode ser soldado individualmente e, em seguida, vários rolos de geléia de enrolamento são conectados em paralelo após a soldagem a laser.
Os rolos de gelatina de enrolamento com abas soldadas revestidas de filme isoladas são inseridos no invólucro, e a tampa superior e o invólucro são soldados usando soldagem a laser. Depois que a bateria é seca, ela é preenchida com eletrólito e pré-carregada. A abertura da bateria é selada com um prego de vedação, coberto com um bujão de vedação de alumínio e, em seguida, o bujão de vedação é soldado na tampa superior da bateria para selar completamente a célula.
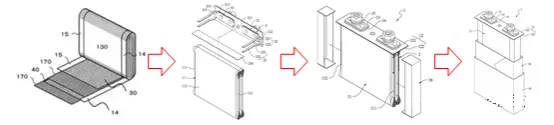
Consistência na produção de folhas de eletrodos
As folhas de eletrodo positivo e negativo são revestidas usando uma técnica de revestimento por extrusão de matriz de ranhura, com modecalandragem de folga constante usando um laminador servo hidráulico.
Durante o processo de revestimento e calandragem do eletrodo, as folhas de eletrodo com um comprimento de aproximadamente 500m são coletadas como um rolo e passam por inspeções iniciais e finais como um lote. Um amostrador corta amostras circulares com um diâmetro de φ60mm, e o peso e a espessura das folhas de eletrodo são medidos. A densidade superficial e a densidade compacta das folhas de eletrodo são calculadas, com 3 amostras coletadas para teste e cálculo de dados por lote.
Os dados de teste para as folhas de eletrodos positivos são mostrados na Figura 2 e na Figura 3. A densidade média da superfície das folhas de eletrodo em ambos os lados é de 36,89 mg/cm2, indicando boa estabilidade do revestimento. A calandragem das folhas de eletrodos determina a densidade compacta do revestimento, controlando a espessura das folhas de eletrodos. Após a calandragem, a densidade compacta do eletrodo positivo é controlada em 3,00 g/cm3, com flutuações mínimas de espessura e boa estabilidade.
Os dados de teste para as folhas de eletrodos positivos são mostrados na Figura 2 e na Figura 3. A densidade média da superfície das folhas de eletrodo em ambos os lados é de 36,89 mg/cm2, indicando boa estabilidade do revestimento. A calandragem das folhas de eletrodos determina a densidade compacta do revestimento, controlando a espessura das folhas de eletrodos. Após a calandragem, a densidade compacta do eletrodo positivo é controlada em 3,00 g/cm3, com flutuações mínimas de espessura e boa estabilidade.
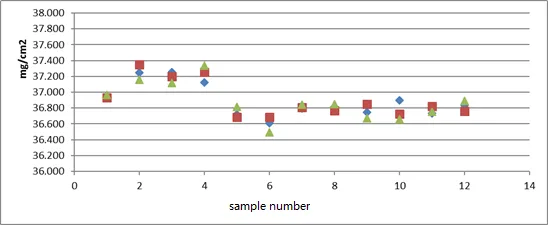
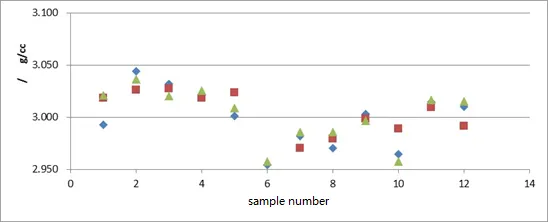
Os dados de teste para as folhas de eletrodos negativos são mostrados na Figura 4 e na Figura 5. A densidade média da superfície das folhas de eletrodo em ambos os lados é de 16,13 mg/cm2, indicando boa estabilidade do revestimento. A calandragem das folhas de eletrodos determina a densidade compacta do revestimento, controlando a espessura das folhas de eletrodos. Após a calandragem, a densidade compacta do eletrodo negativo é controlada em 1,62 g/cm3, com flutuações mínimas de espessura e boa estabilidade. Por fim, os intervalos, médias e desvios padrão da densidade superficial e da densidade compacta para as folhas de eletrodos positivos e negativos estão resumidos na Tabela 1.

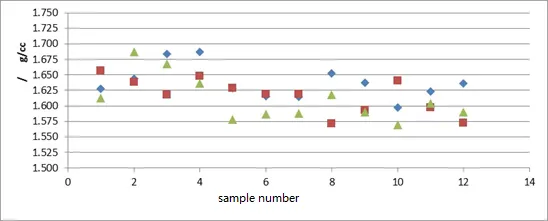
Tabela 1: Densidade de superfície e densidade compacta de folhas de eletrodos positivos e negativos
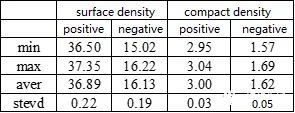
Após o enrolamento, o rolo de gelatina requer testes extensivos para garantir a qualidade do produto, incluindo:
(1) Dimensões da célula, incluindo altura, largura, espessura, largura e posição da fita, alinhamento dos coletores de aba, etc. Essas dimensões podem ser medidas diretamente e estão relacionadas ao processo de enrolamento e à precisão do equipamento.
(2) Comprimento das folhas e separadores de eletrodos.
(3) Largura das folhas de eletrodos. Na direção da largura, o eletrodo negativo precisa exceder o eletrodo positivo em uma certa margem e o separador precisa exceder o eletrodo negativo em uma certa margem. O alinhamento na direção da largura é determinado diretamente pela precisão do processo de enrolamento. Quando a precisão é alta, as dimensões da margem podem ser menores, resultando em maior densidade de energia da bateria. No entanto, a margem de segurança da bateria diminui e é crucial garantir a precisão do processo para evitar riscos significativos à segurança. O alinhamento de cada camada de folhas de eletrodo na célula geralmente é obtido por inspeção por raios-X de todos os quatro cantos da célula. Quando a dimensão da largura relativa entre os eletrodos positivo e negativo não atende aos requisitos, o equipamento emite automaticamente o alarme e rejeita os produtos defeituosos.
(4) qualidade do rolo de gelatina.
(5) Rebarbas em folhas de eletrodos. A faca de corte usada para o corte da chapa do eletrodo pode sofrer desgaste com o tempo, afetando a qualidade do corte. Portanto, a faca de corte precisa ser gerenciada por sua vida útil e inspeções regulares da qualidade do corte precisam ser realizadas para evitar rebarbas. O processo típico para observar rebarbas é pegar uma folha de eletrodo cortada e examinar a superfície cortada sob um microscópio óptico para detectar a presença de rebarbas. O padrão de controle para rebarbas é geralmente que o tamanho da rebarba deve ser menor que a metade da espessura do separador. No entanto, alguns fabricantes têm requisitos de controle mais rígidos, onde as rebarbas não devem exceder o revestimento.
(6) Outros defeitos internos no rolo de gelatina, como dobra da folha do eletrodo, orientação do revestimento, objetos estranhos, etc.
A análise da seleção da qualidade do rolo de gelatina é mostrada no histograma de dados na Figura 6. O histograma é processado usando dados coletados do rolo de gelatina para refletir a distribuição da qualidade do produto, permitindo a avaliação e previsão da qualidade do produto e das taxas de não conformidade. Ao analisar dados estatísticos, os dados são divididos em vários grupos com base em diferentes intervalos, e o número de grupos é referido como o número de compartimentos. A distribuição da qualidade do rolo de gelatina segue uma distribuição normal, com massa média de 179,86g. Há uma quantidade maior de rolos de gelatina dentro da faixa de massa de 177,955-178,155g, desviando-se da distribuição normal.
Durante o processamento das folhas de eletrodo, são feitas marcações em folhas defeituosas com problemas como revestimento de um lado ou folha exposta, e essas folhas defeituosas são removidas durante o enrolamento. No entanto, folhas defeituosas ainda aparecem ocasionalmente no rolo de gelatina. A realização de inspeções de qualidade nos rolos de gelatina e a remoção de produtos não conformes podem garantir ainda mais a qualidade do produto.
A principal causa de resultados anormais de inspeção de qualidade é a geração de folhas defeituosas durante o processamento da folha de eletrodo, como inconsistências de revestimento, revestimento de um lado e a presença de defeitos de fita nas folhas de eletrodo.
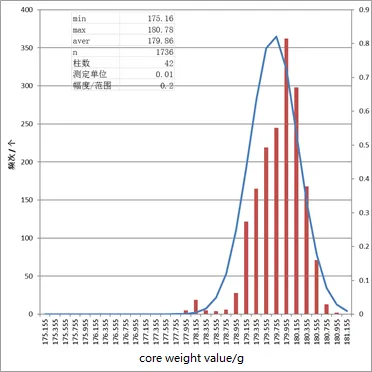
Foram realizados testes destrutivos de desmontagem parcial do rolo de gelatina, analisando principalmente os dados de comprimento do eletrodo positivo, eletrodo negativo e separador. Os resultados específicos são mostrados na Figura 7, com o comprimento do eletrodo positivo de aproximadamente 2,20 m e o comprimento do eletrodo negativo de aproximadamente 2,37 m. Para que os íons de lítio do eletrodo positivo se difundam e sejam acomodados na rede do eletrodo negativo, o eletrodo negativo deve envolver totalmente o eletrodo positivo com uma certa margem de tamanho. Além disso, para evitar curtos-circuitos, o separador deve encapsular o eletrodo negativo. Na direção do comprimento da célula enrolada, é necessário garantir que o eletrodo negativo tenha uma margem em comparação com o eletrodo positivo, e o separador deve envolver o eletrodo negativo. O posicionamento relativo das folhas de eletrodos é crucial, incluindo parâmetros como comprimento do separador, dimensões relativas ao eletrodo negativo e o posicionamento relativo entre os eletrodos positivo e negativo. Essas dimensões são influenciadas pelas especificações de revestimento do eletrodo, processos de enrolamento e outros fatores.
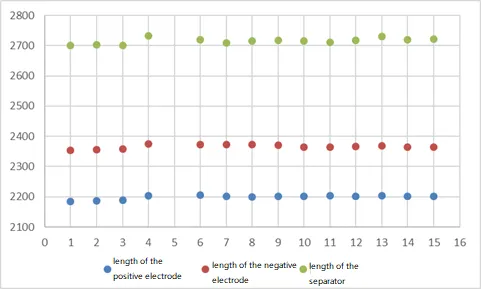
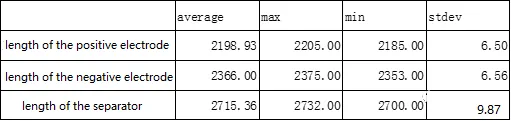
Após a montagem da bateria, carregue e descarregue para testar a capacidade da bateria, resistência interna DC e outros parâmetros. A distribuição de capacidade é o acúmulo de todos os fatores que influenciam o processo da bateria. Este parâmetro pode ser usado para analisar a consistência da bateria e integrar os erros de todos os processos. A distribuição da capacidade da bateria é mostrada na Figura 8 e na Tabela 2. A capacidade do processo é a capacidade de um processo de garantir a qualidade do produto quando está em estado estacionário. É amplamente afetado e restrito por fatores como operadores, máquinas e equipamentos, matérias-primas, métodos de processo e ambiente de trabalho no processo. Isso se reflete em dois aspectos: se a qualidade do produto é estável e se a precisão da qualidade do produto é suficiente. Conforme mostrado na Figura 9, com base nos dados de capacidade da bateria, a capacidade do processo de produção da bateria é analisada de forma abrangente, CP=1,085, e a capacidade de produção da bateria atende aos requisitos.
Determinação da capacidade do processo:
1.Cp>1.33. Quando Cp>1.33, indica que a capacidade do processo é suficiente. Neste momento, é necessário controlar a estabilidade do processo para evitar mudanças significativas na capacidade do processo. Se a capacidade do processo for considerada muito grande, os requisitos padrão e as condições do processo devem ser analisados. Por um lado, os requisitos podem ser reduzidos para evitar o desperdício de precisão do equipamento. Por outro lado, os padrões também podem ser revisados para melhorar a qualidade do produto.
2. 1.0<cp≤1.33. Quando o índice de capacidade do processo está entre 1,0 e 1,33, ele indica que a capacidade do processo atende aos requisitos, mas não é suficiente. Quando o valor de cp é muito próximo de 1, existe o risco de ultrapassar a tolerância, devendo ser tomadas medidas para fortalecer o controle do processo. < span=""></cp≤1.33. Quando o índice de capacidade do processo está entre 1,0 e 1,33, ele indica que a capacidade do processo atende aos requisitos, mas não é suficiente. Quando o valor de cp é muito próximo de 1, existe o risco de ultrapassar a tolerância, devendo ser tomadas medidas para fortalecer o controle do processo.
3. 0,67<cp≤1,0. Quando o índice de capacidade do processo está entre 0,67 e 1,0, indica que a capacidade do processo é insuficiente e não pode atender às necessidades das normas. Medidas de melhoria devem ser tomadas, alterando as condições do processo, revisando padrões ou realizando inspeções completas, etc. < span=""></cp≤1.0. Quando o índice de capacidade do processo está entre 0,67 e 1,0, indica que a capacidade do processo é insuficiente e não pode atender às necessidades das normas. Medidas de melhoria devem ser tomadas, alterando as condições do processo, revisando padrões ou conduzindo rigorosamente inspeções completas, etc.
4. Cp≤0,67. Quando o índice de capacidade do processo é inferior a 0,67, isso indica que a capacidade do processo é seriamente insuficiente e o trabalho deve ser interrompido para retificação, se necessário.
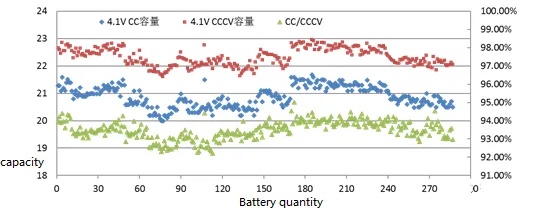
Tabela 2 Dados de distribuição da capacidade da bateria
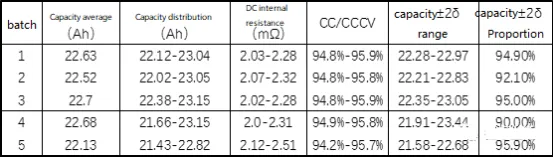
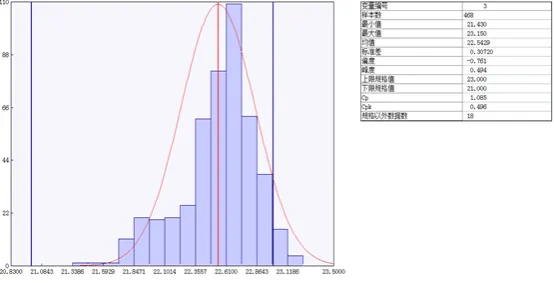