Mistura (materiais ativos de eletrodo positivo e negativo + agente condutor + aglutinante + dispersante) – revestimento —– laminação ——- corte — soldagem de abas — – Enrolamento (ou junta) – Papel adesivo – Inserção do invólucro da bateria – Soldagem – Vedação – Formação, etc. Basicamente, o processo de produção de baterias em toda a indústria é semelhante, a principal diferença é a diferença de equipamentos ou produtos de bateria são diferentes. No caso das células de bolsa, elas são normalmente empilhadas, enquanto as células cilíndricas são enroladas e as células prismáticas podem envolver enrolamento e empilhamento. Isso resulta em diferentes processos durante o estágio de enrolamento da célula. As tecnologias mais importantes e essenciais estão nos processos de mistura e revestimento, bem como no processo de formação final.
O processo de produção de baterias de lítio é complexo e envolve principalmente três etapas principais: a etapa de fabricação do eletrodo (front-end) com mistura e revestimento, a etapa de montagem da célula (etapa intermediária) com enrolamento e injeção de eletrólitos e a etapa de embalagem e teste (back-end) com formação e vedação. A distribuição de valor (em termos de valor de aquisição) é de aproximadamente 35-40% para o front-end, 30-35% para o estágio intermediário e 30-35% para o back-end. De acordo com informações dos fornecedores de equipamentos de revestimento, as variações decorrem principalmente de diferentes fornecedores de equipamentos e da proporção de equipamentos importados para produzidos internamente. No entanto, o processo geral permanece relativamente consistente, com pequenos desvios na distribuição de valor, mas geralmente alinhando-se com as proporções mencionadas.
O equipamento de produção de baterias de lítio correspondente aos processos front-end inclui principalmente misturadores a vácuo,máquinas de revestimentoemáquinas de calandragem. Para os processos de estágio intermediário, o equipamento inclui máquinas de corte e vinco, máquinas de enrolamento, máquinas de empilhamento e máquinas de injeção de eletrólitos. Os processos de back-end envolvem máquinas de formação, equipamentos de teste de capacidade e armazenamento de processos e automação logística. Além disso, a produção de baterias requer equipamentos de automação de pacotes.
O resultado do processo de front-end na produção de baterias de lítio é a preparação das folhas de eletrodos positivos e negativos. A primeira etapa desse processo é a mistura, onde os materiais da bateria de estado sólido para os eletrodos positivo e negativo são misturados uniformemente e depois misturados com um solvente para formar uma pasta. A mistura dos ingredientes é a base dos processos subsequentes na produção de baterias de lítio. A mistura de alta qualidade é essencial para obter resultados de alta qualidade nos seguintes processos de revestimento e calandragem.
Após os processos de revestimento e calandragem, a próxima etapa é o corte, que envolve o corte do material revestido nas larguras desejadas. Se rebarbas ou arestas estiverem presentes durante o processo de corte, isso pode levar a problemas de montagem, problemas de injeção de eletrólitos e até mesmoRiscos de segurançadurante o uso da bateria. Portanto, o equipamento de front-end no processo de produção de baterias de lítio, como misturadores, máquinas de revestimento, máquinas de calandragem emáquinas de corte longitudinal, são as principais máquinas para fabricação de baterias. Eles afetam muito a qualidade de toda a linha de produção. Como resultado, o equipamento front-end detém o maior valor (em termos de quantidade) na linha de produção automatizada de baterias de lítio em geral, respondendo por aproximadamente 35%.
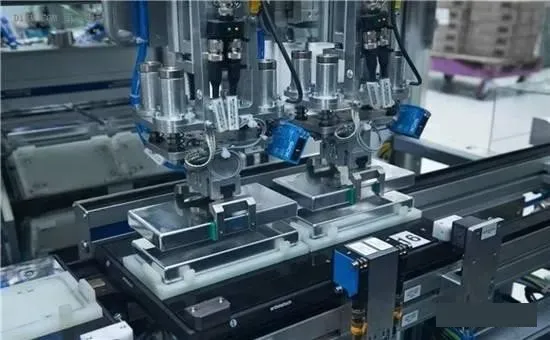
No processo de fabricação de baterias de lítio, os processos de estágio intermediário são focados principalmente na formação de baterias. Os principais processos nesta etapa incluem preparação de eletrodos, enrolamento de eletrodos, corte e vinco, enrolamento de células e empilhamento. Esta etapa é uma área altamente competitiva entre os fabricantes de equipamentos nacionais e representa aproximadamente 30% do valor de uma linha de produção de baterias de lítio.
Atualmente, os processos de fabricação de células de bateria de lítio de energia incluem principalmente enrolamento e empilhamento, correspondendo a três formas estruturais de bateria: cilíndrica, prismática e bolsa. As baterias cilíndricas e prismáticas são produzidas principalmente usando o processo de enrolamento, enquanto as baterias de bolsa utilizam principalmente o processo de empilhamento. As baterias cilíndricas são representadas por formatos como 18650 e 26650 (a Tesla desenvolveu de forma independente a bateria 21700, que está sendo amplamente promovida em toda a indústria). A principal diferença entre baterias prismáticas e de bolsa está no invólucro, com baterias prismáticas usando invólucros de alumínio rígido e baterias de bolsa utilizando filme de alumínio-plástico. O processo de fabricação de baterias de bolsa é principalmente empilhamento, enquanto para baterias de alumínio, é principalmente enrolamento.
De acordo com o entendimento, a estrutura de bolsa das baterias de lítio visa principalmente o mercado digital de médio a alto padrão, com margens de lucro relativamente mais altas por unidade de produto. Em condições de capacidade de produção equivalentes, a margem de lucro das baterias de bolsa é geralmente maior do que a das baterias de alumínio. No entanto, devido à facilidade de obter economias de escala e controlar as taxas e custos de qualificação do produto, as baterias de carcaça de alumínio também têm lucros significativos em seus respectivos domínios de mercado. É previsível que é improvável que as baterias de bolsa e de alumínio sejam completamente substituídas no futuro próximo.
Devido à capacidade de alcançar a produção de alta velocidade por meio da velocidade de rotação, o processo de enrolamento é atualmente o principal método usado na produção doméstica de baterias de lítio. Por outro lado, a melhoria de velocidade alcançável com a tecnologia de empilhamento é limitada. Como resultado, o volume de remessa das máquinas de enrolamento é atualmente maior do que o das máquinas de empilhamento. Os processos anteriores para a produção de enrolamento e empilhamento são a preparação do eletrodo e o corte e vinco. A preparação do eletrodo inclui processos como soldagem dos eletrodos/aba cortados, remoção de poeira do eletrodo, aplicação de fita adesiva protetora, encapsulamento das abas e enrolamento ou corte em um comprimento fixo. Os eletrodos enrolados são usados para o enrolamento totalmente automatizado subsequente, enquanto os eletrodos cortados no comprimento são usados para o enrolamento semiautomático. O corte e vinco envolve o corte e a modelagem dos eletrodos enrolados para processos de empilhamento subsequentes.
Em termos de soldagem por encapsulamento de bateria de lítio, os principais fabricantes de aplicações integradas, como Uwlaser, Hanslaser e Gdlaser, estão todos envolvidos no campo da tecnologia laser. Eles são capazes de atender à demanda sem a necessidade de importações.
Fluxo do processo de back-end da bateria de lítio: separação e formação de volume é o elo principal
Os processos de pós-produção em lítiofabricação de bateriasincluem principalmente classificação, formação, teste e embalagem para armazenamento, que representam aproximadamente 35% do valor da linha de produção. A formação e a classificação são os principais processos na fase de pós-produção, envolvendo o teste de ativação das baterias formadas. Devido ao longo ciclo de teste para carga e descarga da bateria, o equipamento utilizado nesses processos possui o maior valor. O principal objetivo do processo de formação é ativar as células seladas após a embalagem por injeção, carregando-as, enquanto o processo de classificação envolve testar a capacidade da bateria e outros parâmetros de desempenho elétrico após a ativação e, em seguida, classificá-los de acordo. A formação e a classificação são normalmente realizadas por sistemas automatizados que consistem em máquinas de formação e máquinas de classificação.
Processo de bateria de lítio: aparentemente simples, mas precisa ser combinado com um design sistemático
Um sistema de bateria de energia é composto por várias células de bateria individuais conectadas em série ou paralelamente, integrando sistemas de gerenciamento térmico e de energia. O pacote é um componente chave na produção, projeto e aplicação de sistemas de bateria de energia. Ele serve como elo entre a produção de células de bateria upstream e as aplicações de veículos downstream. Normalmente, os requisitos de design são propostos por fabricantes de células de bateria ou empresas automotivas e geralmente são preenchidos por fabricantes de baterias, empresas automotivas ou fabricantes de pacotes terceirizados.
A linha de produção de baterias de lítio é relativamente simples, com processos principais, incluindo carregamento de material, montagem de suportes, soldagem e testes. O equipamento principal inclui máquinas de solda a laser e vários tipos de adesivos e equipamentos de teste. Atualmente, o nível de automação na produção de embalagens é relativamente baixo. Isso ocorre principalmente porque o volume de vendas de modelos individuais de veículos de nova energia não é grande o suficiente para justificar o alto custo das linhas de produção automatizadas.
Fosfato de ferro e lítio e ternário: a densidade de energia é um tópico inevitável, diferentes materiais requerem um conjunto completo de investimentos em equipamentos
Atualmente, os principais materiais catódicos para baterias de lítio de energia na China são divididos em duas categorias: fosfato de ferro e lítio (LiFePO4) e materiais ternários. Entre eles, o fosfato de ferro e lítio é o material catódico mais seguro para baterias de íons de lítio, com um ciclo de vida típico de mais de 2000 ciclos. Além disso, devido à indústria madura e à diminuição dos preços e barreiras tecnológicas, muitos fabricantes escolhem baterias de fosfato de ferro e lítio por vários motivos. No entanto, as baterias de fosfato de ferro e lítio têm uma desvantagem notável em termos de densidade de energia. O principal fabricante de baterias de fosfato de ferro e lítio, a BYD, tem uma densidade de energia de 150Wh para suas células de fosfato de ferro e lítio, e eles esperavam aumentá-la para 160Wh até o final de 2017. Teoricamente, é difícil para o fosfato de ferro e lítio exceder uma densidade de energia de 200Wh/kg.
As baterias de lítio de polímero ternário referem-se a baterias de lítio que usam um material catódico composto de óxido de lítio-níquel-cobalto-manganês, com a proporção real de níquel, cobalto e manganês ajustada de acordo com as necessidades específicas. As baterias ternárias de lítio têm maior densidade de energia (atualmente, fabricantes de baterias de energia de primeira classe, como a CATL, podem atingir uma densidade de energia de 200Wh/kg-220Wh/kg, e projeta-se que, até 2020, a densidade de energia das baterias ternárias chegará a 300Wh/kg). Como resultado, o mercado de veículos de passageiros está mudando para baterias ternárias de lítio. Por outro lado, o fosfato de ferro e lítio é mais favorecido para aplicações com maiores requisitos de segurança, como em ônibus. Com o desenvolvimento de veículos de passageiros totalmente elétricos, as baterias ternárias de lítio ocupam cada vez mais uma posição importante.
Os dois materiais têm diferenças de densidade de energia e custo, e diferentes veículos e montadoras fazem escolhas diferentes. De acordo com o entendimento da Tucbol, o processo de produção de ambos os materiais é geralmente semelhante, mas as diferenças residem principalmente no uso e proporção de materiais, bem como em variações significativas em parâmetros específicos do processo. O equipamento não pode ser compartilhado para produção, e o custo de simplesmente adaptar ou mudar a capacidade de produção é alto (os materiais ternários têm requisitos rígidos para desumidificação a vácuo, que não eram necessários para as linhas de produção anteriores de fosfato de ferro e lítio). Portanto, muitos fabricantes de baterias planejam seu layout de capacidade de produção implantando simultaneamente e comprando separadamente equipamentos para ambos os materiais.