A tecnologia de revestimento é um processo baseado no estudo das propriedades do fluido, que envolve a aplicação de uma ou várias camadas de líquido em um substrato. O substrato é normalmente um filme ou papel flexível. O revestimento líquido é então seco ou curado usando métodos como secagem em forno para formar uma camada com funcionalidade especial, como no caso do revestimento do eletrodo da bateria de íons de lítio. Atualmente, os principais métodos para revestir eletrodos de bateria de íons de lítio são o revestimento de transferência de rolo de vírgula e o revestimento de extrusão de matriz de ranhura.
01 Princípio e classificação da máquina de revestimento
O princípio do equipamento de revestimento de eletrodo envolve a mistura uniforme de materiais necessários para a formulação do eletrodo positivo ou negativo, seguida pela aplicação ou laminação na frente e no verso da folha de alumínio ou folha de cobre. Se necessário, um dispositivo eletromecânico integrado pode ser usado para atender aos requisitos técnicos do cliente, evaporando o solvente da pasta por meio da condução de energia.
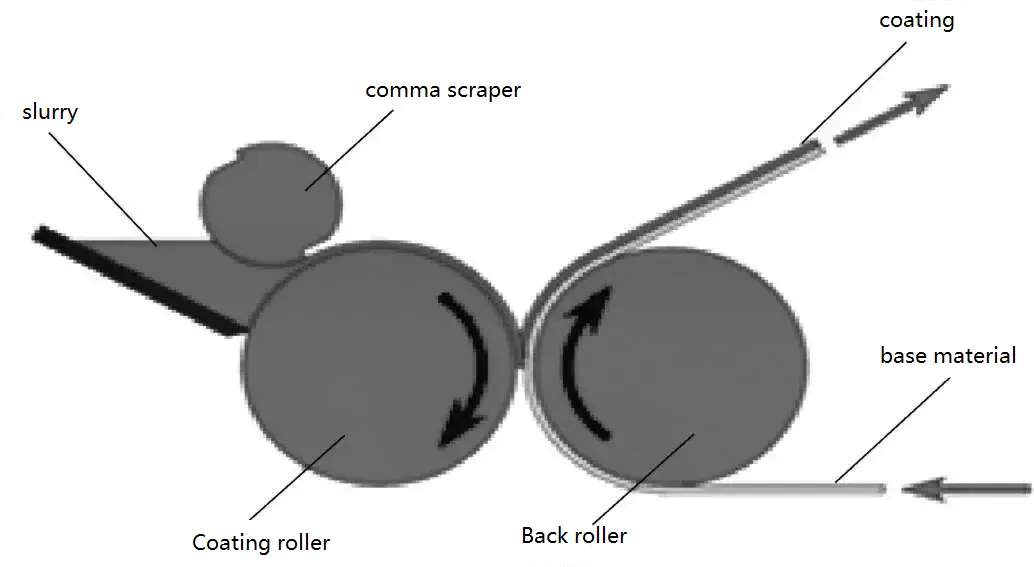
Ajustando a folga entre o rolo de revestimento e a lâmina de vírgula, a pasta é medida no rolo de revestimento. Em seguida, ajustando a folga entre o rolo traseiro e o rolo de revestimento, toda a pasta medida no rolo de revestimento é transferida para a folha.
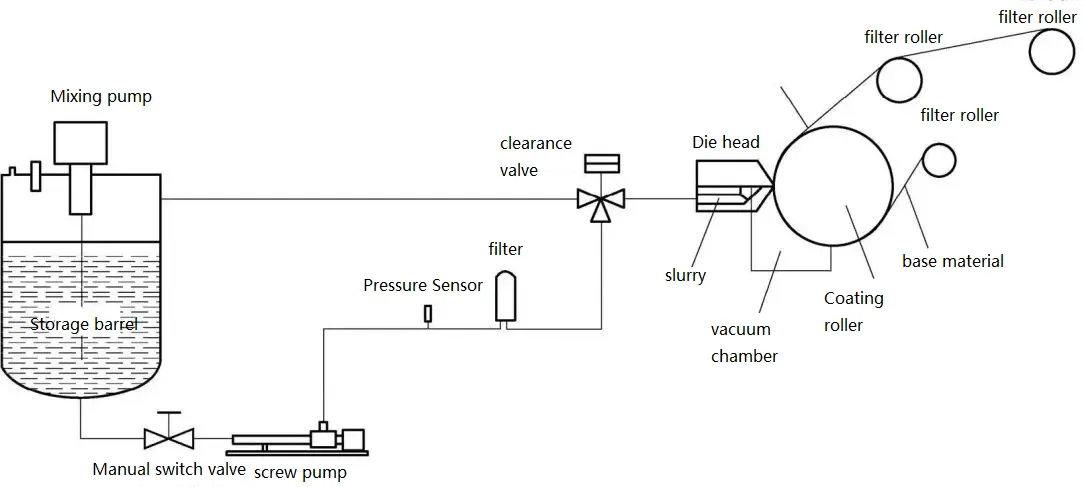
Este é um dispositivo para revestimento dosado de alta precisão, que aplica uniformemente pastas de fluido newtoniano ou não newtoniano na superfície de um substrato por meio de uma bomba dosadora e uma matriz de ranhura. A fórmula para calcular a espessura do revestimento é a seguinte:
Espessura do revestimento = Taxa de fluxo da bomba dosadora / (Largura do revestimento * Velocidade do revestimento)
Além disso, a matriz é um componente crucial do método de revestimento de matriz de ranhura e é um dos principais fatores que determinam a precisão do revestimento. À medida que as velocidades de revestimento aumentam, alguns clientes agora estão usando mecanismos de câmara de vácuo para garantir a qualidade do revestimento durante os processos de revestimento de alta velocidade. Normalmente, quando a velocidade do revestimento é de ≥30m/min, a estrutura desta câmara de pressão negativa precisa ser considerada.
O projeto da matriz deve considerar os seguintes fatores:
Cálculo e simulação da cavidade do canal de fluxo com base nos parâmetros reológicos da pasta.
Requisitos para o nivelamento e retidão dos lábios superior e inferior.
Seleção de material para a matriz, de preferência usando aço inoxidável.
Prevenção da geração de partículas metálicas estranhas durante o uso. Se inevitável, a proteção adequada deve ser implementada para evitar que partículas estranhas entrem na pasta.
Facilidade de desmontagem e limpeza.
Princípio da preparação do eletrodo do método seco (conforme mostrado no diagrama):
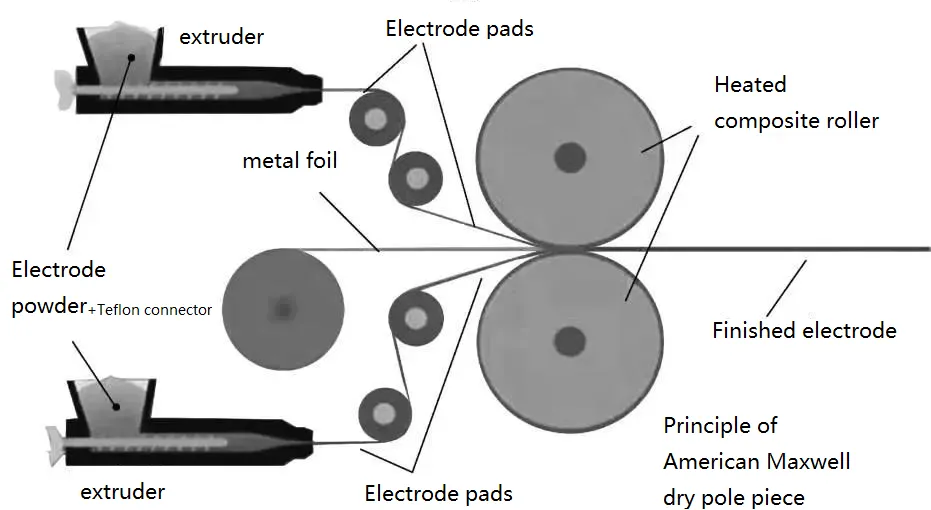
A tecnologia de revestimento tem o potencial de ser uma inovação disruptiva, especialmente quando combinada com a tecnologia de bateria de estado sólido, para atender às necessidades de futuras baterias de lítio avançadas. Por exemplo, a combinação de eletrólitos de estado sólido de sulfeto e tecnologia de eletrodo de método seco é uma grande promessa. As vantagens desta tecnologia são as seguintes:
Ele pode atender aos rigorosos requisitos ambientais da Europa, tornando o processo de produção ecologicamente correto.
Garante segurança durante a produção. As pastas tradicionais de revestimento catódico de bateria de lítio usam NMP (N-Metil-2-pirrolidona) como solvente, que possui características de segurança ruins.
O custo de investimento do equipamento é baixo e requer uma pegada menor com requisitos reduzidos de umidade ambiental.
Ele permite a produção de filmes de eletrodos mais espessos, o que permite a mesma capacidade de energia volumétrica enquanto economiza em materiais de folha e separador. Isso oferece vantagens significativas em termos de custo da lista de materiais (BOM).
02 Composição do equipamento e estrutura principal
O equipamento consiste em cinco partes principais: unidade de desenrolamento, unidade de revestimento (incluindo sistema de alimentação), unidade de secagem, unidade de descarga e unidade de enrolamento. A configuração da unidade da máquina de revestimento é mostrada no diagrama.
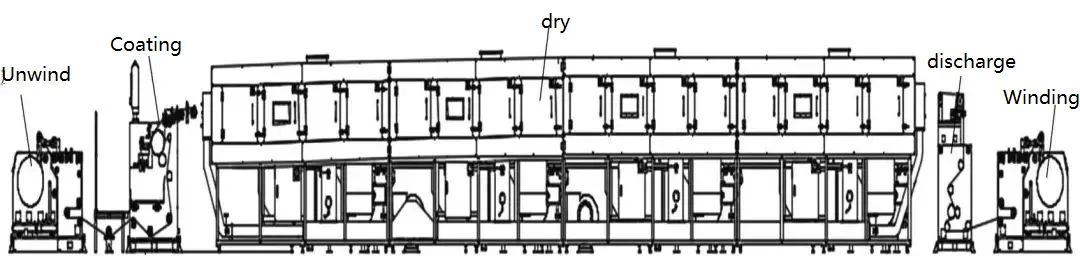
2.1 Unidade de desenrolamento
Existem dois métodos de desenrolamento: emenda automática de fita e emenda manual de fita. A unidade manual de emenda e desenrolamento de fita é mostrada na figura.

O material a ser processado é instalado no eixo de desenrolamento e é guiado para a seção de revestimento após passar pelo alinhamento da borda e controle de tensão. Os principais pontos de controle do dispositivo são o alinhamento da borda de desenrolamento e o controle de tensão.
O alinhamento da borda é obtido por uma unidade dedicada de controle de posição da borda (EPC). Um sensor ultrassônico de detecção de posição (capaz de detectar filmes transparentes) monitora continuamente a posição da borda do material. O dispositivo de desenrolamento é acionado por um motor para se mover para a esquerda ou para a direita, garantindo uma posição relativa constante entre a borda do material e o sensor de alinhamento da borda.
Existem três modos de alinhamento de borda: totalmente automático, onde o sistema ativa automaticamente o alinhamento de borda ao ligar (com base no feedback do sensor para acionar o motor); semiautomático, onde o sistema aciona o alinhamento da borda durante a operação automática (revestimento e tração) e o alinhamento manual da borda durante a parada; e modo manual, onde o mecanismo de alinhamento de borda só pode ser operado manualmente, independentemente do status do sistema.
O controle de tensão consiste em duas partes: controle de posição do rolo flutuante e controle de detecção de tensão real. O princípio do controle da posição do rolo flutuante é o seguinte: durante a operação automática, o controlador PLC ajusta a velocidade do motor do eixo de desenrolamento usando um algoritmo PID baseado no sinal de feedback em tempo real (0% a 100%) do potenciômetro, com o objetivo de manter uma posição constante do rolo flutuante (a posição padrão é definida em 50%).
2.2 Unidade de revestimento e sistema de válvula de alimentação e intermitente
(1) Unidade de revestimento
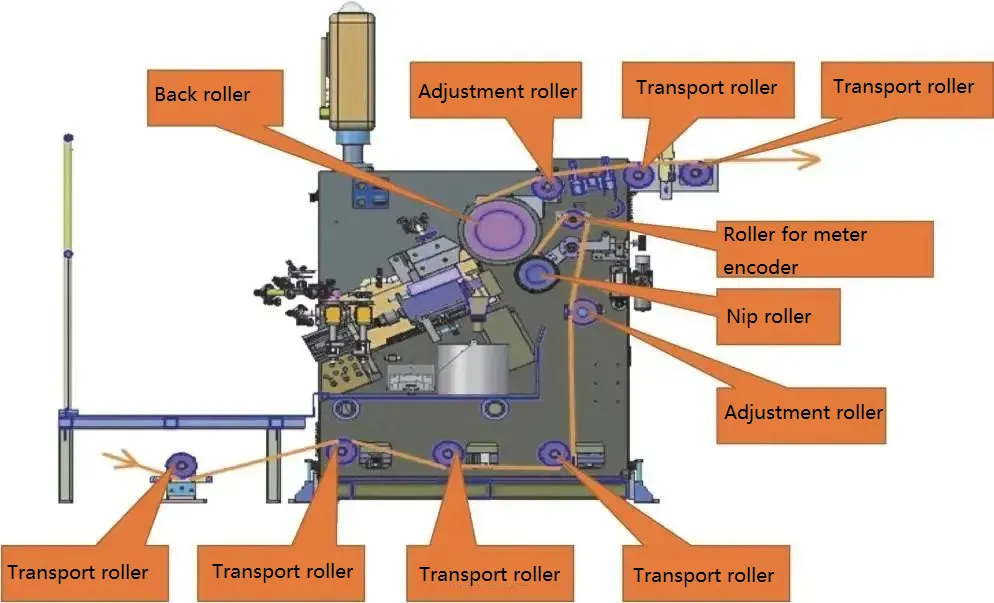
Depois que o material é alimentado no rolo de revestimento da unidade de desenrolamento, ele passa pelo rolo de pressão de alimentação para isolamento de tensão (separando a tensão entre desenrolamento e descarga) e, em seguida, passa pelo rolo de revestimento antes de ser guiado para o forno de secagem. Os principais pontos de controle deste dispositivo são a estabilidade da velocidade geral da máquina e o valor da folga entre a matriz e o rolo de apoio.
O deslocamento entre a matriz e o rolo de apoio é acionado por duas partes. O movimento em grande escala é obtido através de cilindros (para frente e para trás), enquanto o posicionamento preciso é acionado por servomotores nos lados esquerdo e direito (deslocamento real detectado por codificadores lineares de alta precisão com resolução de 0,1 μm).
(2) Sistema de alimentação
O sistema de alimentação inclui um tanque de armazenamento de material, bomba dosadora, removedor de ferro, filtro e tubos conectados. Inicialmente, a pasta é adicionada ao tanque de armazenamento. Uma vez iniciado o revestimento, a pasta no tanque de armazenamento é bombeada através dos tubos conectados, removedor de ferro e filtro para a matriz da ranhura para revestimento. Quando o sensor de nível detecta que a pasta no tanque de armazenamento atinge o nível especificado, a alimentação para o tanque de armazenamento começa. Quando a pasta atinge o nível designado, o sensor de nível envia um comando para parar de alimentar o tanque de armazenamento.
2.1 Unidade de secagem
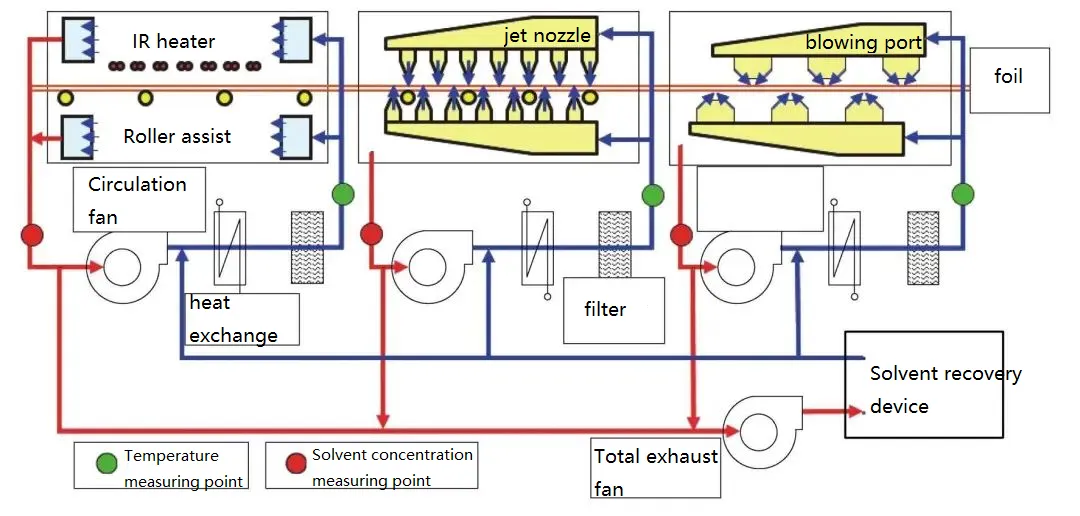
O diagrama esquemático do princípio de secagem é mostrado na figura
A pasta contendo componentes de solvente líquido, produzida pela unidade de revestimento, entra no forno de secagem junto com o filme. Para evaporar o solvente com segurança e eficácia, é necessário controlar a temperatura, o suprimento de ar, o volume de exaustão e outros parâmetros em cada seção do forno de secagem. O sistema de controle de temperatura de seção única consiste em elementos de aquecimento e ventiladores de circulação. Os ventiladores são acionados por motores de frequência variável, e o volume e a velocidade do ar podem ser ajustados definindo a frequência (que é diretamente proporcional à frequência). A temperatura de aquecimento é mantida através de controle constante com base nas mudanças de temperatura nos pontos de controle de temperatura detectados por sensores, garantindo a qualidade do processo de secagem.
2.2 Unidade de descarga
Após a secagem, o filme entra no dispositivo de descarga. O dispositivo de descarga controla a tensão e a posição da borda do filme dentro do forno de secagem. Os principais pontos de controle deste dispositivo são o alinhamento das bordas e o controle de tensão na área de secagem.
O alinhamento da borda é semelhante à unidade de desenrolamento, utilizando um sistema dedicado de controle de posição da borda (EPC). Um sensor de detecção de posição de borda monitora continuamente a posição da borda do filme, e o dispositivo de descarga ajusta sua posição para manter uma posição relativa constante entre a borda do filme e o sensor de alinhamento de borda.
2.3 Unidade de rebobinamento
Existem dois métodos de enrolamento: corda automática e corda manual.
Após a conclusão da produção, o filme acabado passa pelo alinhamento da borda e controle de tensão antes de ser guiado para o eixo do enrolamento. Os principais pontos de controle deste dispositivo são o alinhamento da borda e o controle de tensão durante o processo de enrolamento, que são semelhantes à unidade de desenrolamento.
Durante o processo de enrolamento, para evitar o deslizamento entre as camadas e evitar aperto excessivo ou tração do núcleo, é necessário ajustar a conicidade da tensão do enrolamento.
03 Seleção de equipamentos
3.1 Princípios de seleção de equipamentos
(1) Segurança em primeiro lugar:
Devido à presença de solvente orgânico NMP em nossa máquina de revestimento, requisitos rigorosos à prova de explosão devem ser atendidos, de acordo com o padrão da indústria "Padrão de design para fábricas de baterias de íons de lítio" (GB 51377-2019).
(2) Garantir a segurança da bateria e evitar a contaminação por metais estranhos:
Durante o processo de produção de baterias de íons de lítio, é crucial evitar a introdução de partículas metálicas estranhas. Portanto, os componentes que entram em contato com a pasta e as folhas de eletrodo ou estão próximos a eles não devem ser feitos de cobre, zinco ou estanho.
(3) Seleção de equipamentos e parâmetros:
Atualmente, o método de revestimento de matriz de ranhura é usado principalmente.
(4) Seleção da matriz de revestimento:
(1) Como a pasta da bateria é um fluido não newtoniano, é necessário o teste de parâmetros reológicos. Reômetros especializados são normalmente usados para determinar esses parâmetros. A forma do canal de fluxo da matriz de revestimento deve ser projetada com base nos parâmetros reológicos calculados e nos resultados da simulação para garantir a precisão do revestimento.
(2) Recomenda-se instalar a matriz de revestimento em um ângulo ascendente de 25°. Isso permite a liberação rápida de ar das tubulações e cavidades após a limpeza da matriz e evita o uso de um tubo de fluxo de retorno da matriz como substituto da função de exaustão de ar.
(3) Seleção da bomba de alimentação:
Normalmente, uma bomba de parafuso dosadora de alta precisão é usada. As especificações e o modelo da bomba são selecionados com base na vazão necessária. Para melhorar a precisão do bombeamento, recomenda-se uma estrutura de bomba dupla, que reduz a pulsação e garante alta precisão.
(4) Seleção do forno de secagem:
(1) Comprimento total e comprimento de cada seção:
Primeiro, determine o comprimento de cada seção do forno de secagem. Recomenda-se que o comprimento de cada seção não seja inferior a 4m. Quanto mais rápida a velocidade de secagem, maior deve ser o comprimento da seção. No entanto, deve-se levar em consideração a viabilidade de transporte e montagem. Recomenda-se que o comprimento máximo de cada seção não exceda 5m. A determinação do comprimento total do forno de secagem é baseada no processo de secagem e nos parâmetros de velocidade do revestimento, que normalmente são fornecidos pelo usuário. O fabricante do equipamento atende a esses requisitos de processo.
(2) Faixa de temperatura para secagem no forno:
A faixa de temperatura recomendada é de temperatura ambiente a 140°C. Se houver requisitos específicos do processo, a personalização pode ser considerada. Geralmente, a temperatura máxima não deve exceder 160°C.
(3) Faixa de velocidade do ar de secagem no forno:
Recomenda-se uma faixa de 5 a 20 m/s, com precisão do bico entre ±20%.
(5) Transporte de substrato no forno de secagem:
(1) Para substratos de folha de cobre/alumínio com espessura superior a 6-10μm, recomenda-se o uso de uma combinação de rolos-guia ativos e um forno de secagem flutuante.
(2) Para substratos de folha de cobre/alumínio com espessura inferior a 6-10μm, devido à resistência à tração reduzida, recomenda-se o uso de rolos-guia ativos.
Seleção do diâmetro do enrolamento:
Como o diâmetro do desenrolamento é combinado com base no diâmetro do material de entrada, não fornecerei uma explicação detalhada aqui. No entanto, existem técnicas para selecionar o diâmetro do enrolamento. Recomenda-se determinar o comprimento do rolo grande com base no comprimento cumulativo de folhas de eletrodos individuais obtidas por corte ou corte e, em seguida, convertê-lo em um diâmetro de enrolamento. A fórmula de cálculo é a seguinte:
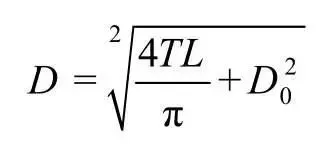
Na fórmula, D é o diâmetro da bobina; D0 é o diâmetro do cilindro inferior; T é a espessura da folha do eletrodo; L é o comprimento da folha do eletrodo.
Só assim a taxa de utilização de materiais pode ser aumentada, o desperdício reduzido e os custos reduzidos. Devido à melhoria na automação, de acordo com a fórmula, pode-se ver que aumentar o diâmetro do cilindro inferior pode aumentar melhor o comprimento de todo o rolo da folha do eletrodo e, ao mesmo tempo, reduzir a pressão da folha do eletrodo inferior. Melhore a qualidade do enrolamento.