O enrolamento refere-se a um processo de produção em que folhas de eletrodos, separadores e fitas de terminação com dimensões correspondentes, que foram cortadas em tiras, são enroladas em rolo de gelatina controlando fatores como velocidade, tensão, tamanho e desvio das folhas de eletrodos.
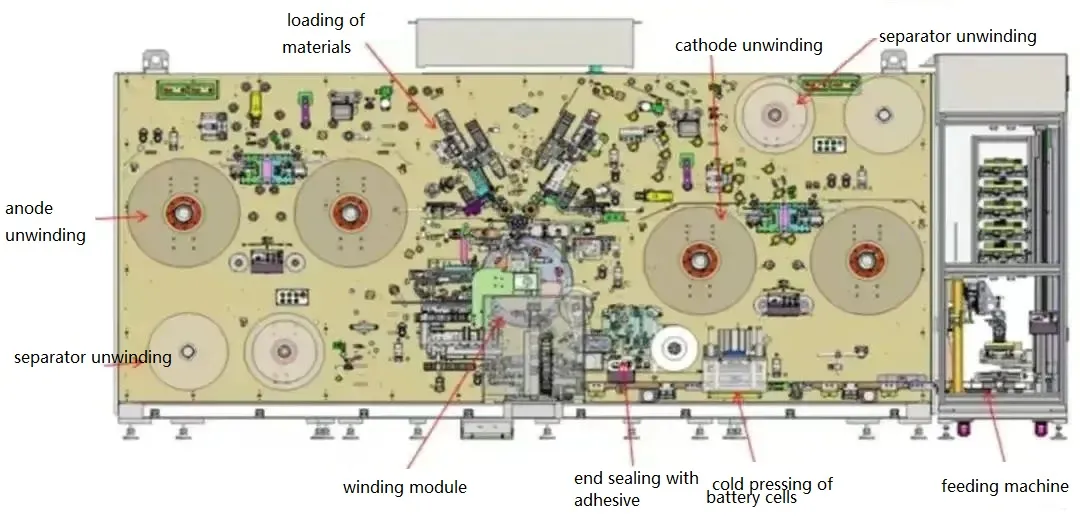
01. Visão geral da classificação do equipamento de enrolamento
Classificação de máquinas de enrolamento convencionais
As máquinas de enrolamento de bateria de lítio são usadas para enrolar células de bateria de lítio e são máquinas que montam a folha de eletrodo positivo, a folha de eletrodo negativo e o separador em um pacote de núcleo por meio de rotação contínua. A máquina de enrolamento consiste em unidades de alimentação de eletrodos positivos e negativos, e a parte onde os separadores de eletrodos positivos e negativos são enrolados juntos é chamada de agulha de enrolamento.
Com base nas diferentes formas dos pacotes de núcleo enrolado, o equipamento de enrolamento pode ser dividido principalmente em duas categorias: enrolamento prismático e enrolamento cilíndrico. O enrolamento prismático pode ser dividido em máquinas de enrolamento automáticas prismáticas e máquinas de enrolamento prismáticas de abas. As células de bateria produzidas por meio de enrolamento prismático são usadas principalmente para a fabricação de baterias prismáticas de energia/armazenamento de energia, baterias digitais e assim por diante. Vários tipos de equipamentos de enrolamento de bateria são mostrados na Figura.
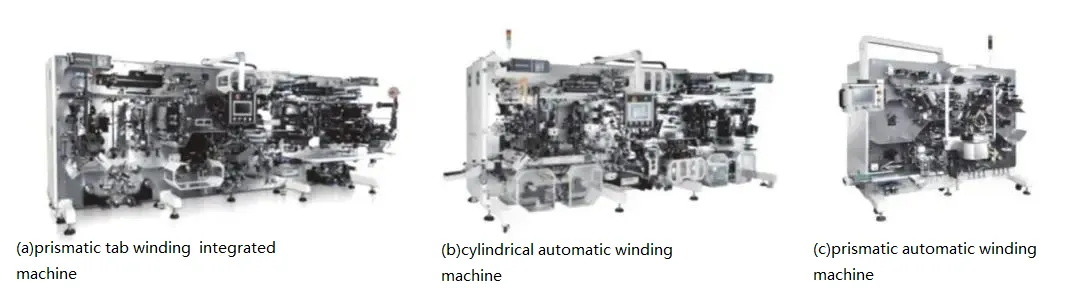
As máquinas de enrolamento podem ser classificadas em categorias com base em seu nível de automação, como máquinas manuais, semiautomáticas, totalmente automáticas e integradas. Eles também podem ser categorizados com base no tamanho dos pacotes principais que produzem, incluindo pequeno, médio, grande e extragrande.
Tabela 1: Tabela de comparação de especificações da máquina de enrolamento e tamanhos de pacotes principais

O surgimento de equipamentos de produção automatizados para baterias de lítio começou com o desenvolvimento bem-sucedido da primeira máquina de enrolamento de bateria de lítio prismática pela Kaido, uma empresa japonesa, em 1990. Em 1999, a empresa coreana Koem desenvolveu com sucesso máquinas de enrolamento de baterias de lítio e máquinas de montagem. Posteriormente, iniciou-se o desenvolvimento de equipamentos de produção automatizada para baterias de lítio, com o Japão e a Coréia permanecendo líderes neste campo, ocupando a maior participação de mercado devido à sua excelente tecnologia e reputação. O equipamento de fabricação de enrolamento doméstico na China começou em 2006, inicialmente com máquinas de enrolamento circulares e prismáticas semiautomáticas, seguidas por máquinas automatizadas de fabricação de abas e enrolamento integradas.
1.2 Desafios no Desenvolvimento de Processos de Enrolamento
É inegável que o processo de enrolamento apresenta vantagens significativas em termos de equipamentos de produção, processos tecnológicos, eficiência e custo, com base em anos de acumulação tecnológica. No entanto, com a crescente demanda por padronização, alta capacidade e baterias de energia automotivas de grande porte, o processo de enrolamento está enfrentando desafios e limitações.
O texto descreve as características estruturais padrão de uma célula enrolada, com regiões de canto arredondado em ambas as extremidades. Durante os processos de carga e descarga da bateria, expansão e contração inconsistentes podem levar a um aumento no espaço entre as placas do eletrodo e o separador. Quando o eletrólito não é suficiente nesta área, ele pode afetar o desempenho da capacidade, e o uso a longo prazo pode representar problemas de segurança relacionados ao revestimento de lítio. Além disso, com a crescente demanda por maior densidade de energia, os materiais de ânodo à base de silício estão sendo gradualmente introduzidos. No entanto, devido à expansão significativa dos ânodos à base de silício, existe o risco de quebra da placa interna do eletrodo no conjunto do eletrodo enrolado, o que afeta a vida útil da bateria e limita a quantidade de material de silício que pode ser adicionado.
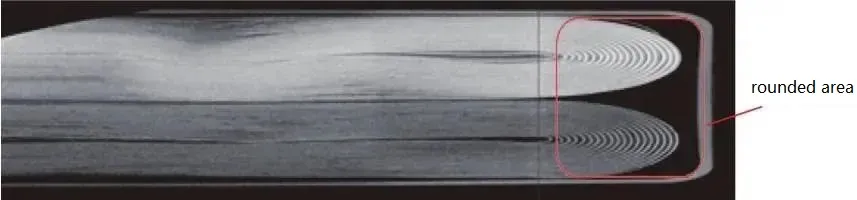
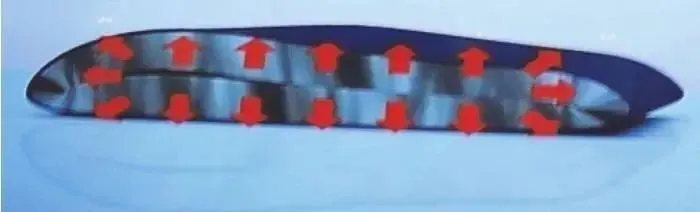

1.3 Direção de desenvolvimento futuro da máquina de enrolamento
(1) Alta velocidade e alta precisão: A velocidade linear das peças do eletrodo de enrolamento aumentará da corrente 2-3m / s para 5m / s, e a precisão do alinhamento das peças do eletrodo de enrolamento será melhorada da corrente ±0,3 mm para ± (0,1-0,2) mm.
(2) Alta taxa de qualificação: O CPK aumentará de 1,33 para 1,67 e, eventualmente, atingirá acima de 2,0, alcançando um nível de defeito zero.
(3) Estabilidade: Aumente o tempo médio entre falhas, das atuais dezenas ou centenas de horas para milhares ou dezenas de milhares de horas.
(4) Controle digital e inteligente do equipamento: Monitoramento on-line da tensão do enrolamento, alinhamento das peças e separadores do eletrodo, otimização em circuito fechado dos parâmetros do enrolamento e dos parâmetros finais de desempenho da bateria, levando a uma melhoria na taxa de qualificação do enrolamento.
(5) Integração de corte e enrolamento a laser: Integração de processos de corte e enrolamento a laser para alcançar a integração de equipamentos.
(6) Máquina de enrolamento de alta velocidade: Avanços na tecnologia de movimento contínuo e uniforme do separador resultarão em uma duplicação da eficiência do enrolamento.
02. Princípio do Equipamento, Composição e Estruturas-Chave
2.1 Princípio da máquina de enrolamento
A máquina de enrolamento é usada principalmente para o enrolamento automático de células de bateria nuas prismáticas ou cilíndricas. O equipamento adota uma estrutura com duas ou mais agulhas de enrolamento e extração de agulha de lado único. As peças e separadores de eletrodos positivos e negativos são desenrolados ativamente, e a troca de rolos separador de peça de eletrodo, correção automática de alinhamento e detecção e controle automáticos de tensão são realizadas. As peças de eletrodo são introduzidas na seção de enrolamento pelo mecanismo de acionamento do rolo de fixação e são enroladas automaticamente junto com o separador de acordo com os requisitos do processo. Após a conclusão do enrolamento, ele muda automaticamente para a próxima estação, corta o separador e aplica a fita do terminal. A célula de bateria nua acabada é descarregada automaticamente, passa por pré-prensagem e varredura, e os produtos qualificados são transferidos automaticamente para uma bandeja e depois para os processos subsequentes. As células de bateria nuas defeituosas são descarregadas automaticamente na área de coleta de células de bateria nuas defeituosas.
2.2 Explicação do mecanismo da máquina de enrolamento
(1) Pré-enrolamento: Este é o processo de alimentação inicial das peças de eletrodo positivo e negativo. Durante este processo, as peças do eletrodo positivo e negativo são alimentadas por um motor a uma velocidade constante. A velocidade de rotação das agulhas de enrolamento precisa ser sincronizada com a velocidade de alimentação das peças do eletrodo. Este processo envolve seis motores. Existem dois tipos de sincronização envolvidos: sincronização entre a velocidade de desenrolamento do separador e a velocidade das agulhas de enrolamento e sincronização entre a velocidade de alimentação das peças do eletrodo e a velocidade das agulhas de enrolamento.
(2) Processo de enrolamento: Após a conclusão do processo de alimentação inicial das peças do eletrodo positivo e negativo, o separador envolve firmemente as peças do eletrodo e inicia o processo de enrolamento enrolando as agulhas de enrolamento por uma revolução. Durante este processo, a velocidade de alimentação das peças do eletrodo é ajustada detectando a tensão do rolo de material. Este ajuste garante uma tensão constante do rolo de material durante o processo de enrolamento.
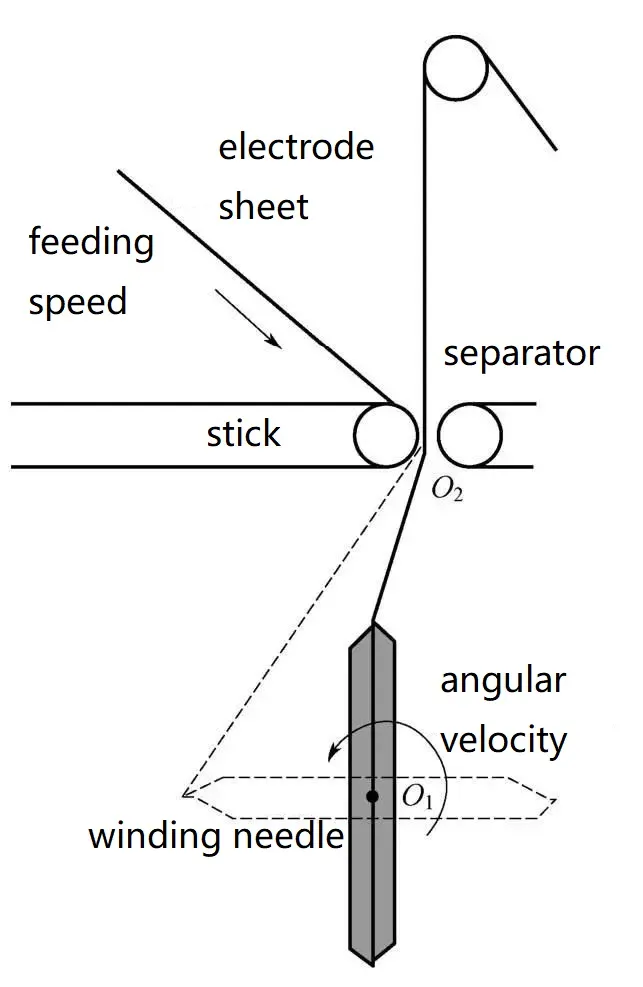
Diagrama Esquemático do Processo de Enrolamento
O diagrama esquemático do processo de enrolamento é mostrado na Figura. Este processo envolve seis motores. Existem dois tipos de sincronização: sincronização entre a velocidade de desenrolamento do separador e a velocidade da agulha de enrolamento e sincronização entre a velocidade de alimentação da peça do eletrodo e a velocidade da agulha de enrolamento. Os problemas de controle no estágio de pré-enrolamento pertencem a problemas de controle de malha aberta, pois não há calibração de feedback para sincronização verdadeira entre os dois. Isso exige que estabeleçamos um modelo preciso de velocidade de enrolamento. A medição da tensão do rolo de material está presente durante o enrolamento, permitindo o uso de técnicas de controle de feedback de circuito fechado no processo de controle.
No processo de enrolamento, nós realmente controlamos a frequência de rotação de cada motor, enquanto a velocidade real é uma função do raio do rolo de material e da agulha de enrolamento, que muda dinamicamente ao longo do tempo. Atualmente, na ausência de sensores reais para medição, assumimos que a mudança no raio intermediário do rolo de material após um processo de carregamento segue a lei espiral de Arquimedes, sem considerar o impacto da troca manual do rolo. Além disso, o raio inicial do material de enrolamento é predeterminado no programa.
(3) Modelagem Dinâmica do Processo de Enrolamento: Como o processo de pré-enrolamento pertence ao controle de malha aberta, um modelo matemático preciso é crucial para determinar o sucesso ou o fracasso do sistema.
2.3 Composição do equipamento e estruturas-chave
Os principais módulos do equipamento incluem: Módulo de desenrolamento automático de eletrodo/separador, módulo de troca de rolo de eletrodo/separador, módulo de correção automática de alinhamento, módulo de rolo guia, módulo de guia e achatamento de guia de eletrodo, módulo de acionamento principal, módulo de controle de tensão, módulo de medição/exibição de tensão e módulo de armazenamento, módulo de alimentação de eletrodo, dispositivo de remoção eletrostática separador, módulo de dobra/dobra de aba de eletrodo e detecção de danos ao eletrodo, módulo de inspeção on-line CCD, módulo de corte de eletrodo, sistema de remoção de poeira, módulo de rejeição para eletrodo defeituoso e rolos separadores, conjunto de cabeça de enrolamento, módulo de corte separador, módulo de adsorção separador, módulo de aplicação de fita terminal, módulo de descarga automática, módulo de pré-prensagem de célula nua, módulo de descarga, estrutura de equipamento e módulo do painel principal.
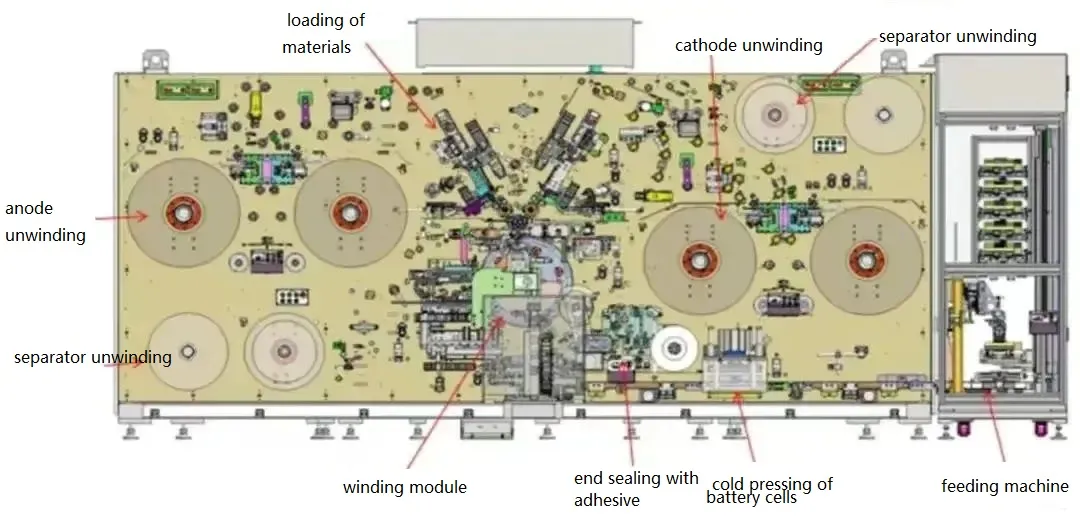
As principais estruturas são as seguintes:
1. Sistema de desenrolamento automático de eletrodo/separador: Consiste no eixo de desenrolamento automático do eletrodo/separador, componentes de alimentação da correia e correção de alinhamento de desenrolamento. Ele alcança funções como fixação, desenrolamento automático e troca automática de rolos de eletrodo/separador. O eixo de desenrolamento adota métodos de expansão mecânica ou pneumática, e os blocos auxiliares e os mecanismos de detecção de borda facilitam o posicionamento rápido.
2. Módulo de correção automática de borda: Consiste em mecanismos de correção de vários níveis, que podem empregar vários métodos, como movimento do eixo suspenso, oscilação do rolo guia e acionamento do rolo de nip para correção da borda. Por detecção, controle e exibição em tempo real da borda do material durante o movimento da correia, ele realiza a correção em tempo real da borda do material. O posicionamento dos sensores é projetado para evitar o acúmulo de poeira que pode afetar a precisão da detecção do valor da borda. Os principais parâmetros incluem precisão de alinhamento de desenrolamento de ±0,2 mm e precisão de alinhamento em processo de ±0,1 mm.
3. Sistema de controle de tensão: Consiste em sensores de detecção de tensão, mecanismos de controle de tensão e um módulo de exibição/armazenamento. Os mecanismos de controle de tensão podem incluir motores lineares, cilindros de baixo atrito ou servomotores. O mecanismo de detecção de tensão é posicionado o mais próximo possível do mecanismo da agulha de enrolamento. Ao controlar efetivamente a tensão do material durante o movimento da correia, permite o ajuste e ajuste da tensão para cada ciclo de enrolamento. Para obter um controle preciso, é importante evitar a deformação do eletrodo nu devido a problemas de tensão do enrolamento. À medida que o diâmetro do enrolamento aumenta gradualmente durante o processo de enrolamento, a tensão precisa ser aumentada para garantir a estanqueidade do eletrodo. Dentro de cada ciclo de enrolamento, é necessário controlar a flutuação da tensão dentro de uma determinada faixa.
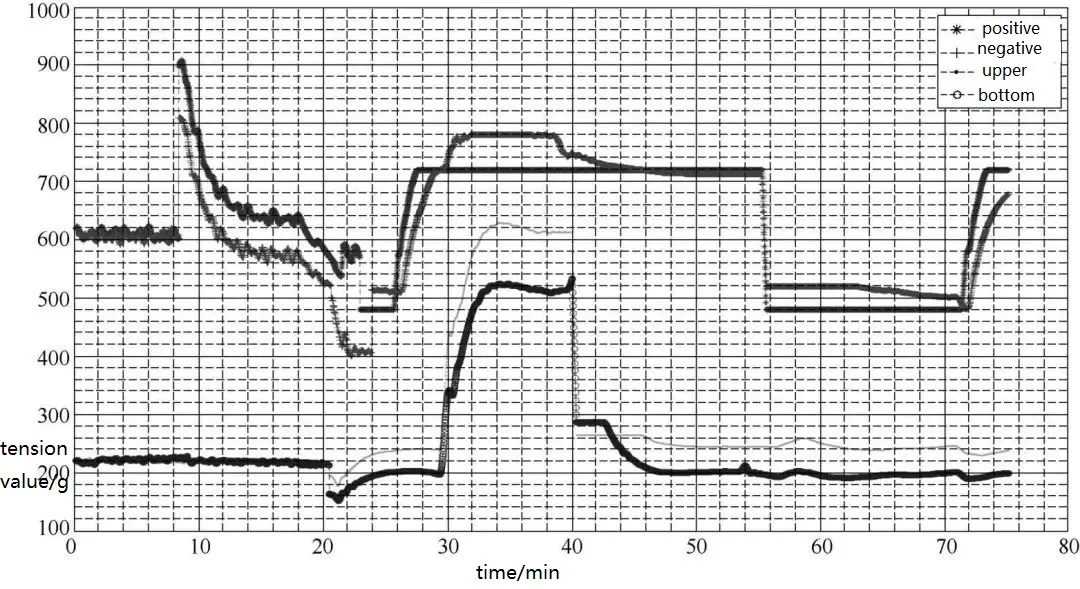
4. Módulo de alimentação do eletrodo: Consiste no mecanismo de acionamento do rolo de nip do eletrodo positivo e negativo e no mecanismo de alimentação, responsável pela alimentação dos eletrodos antes do processo de enrolamento. Durante o processo de enrolamento, a posição de alimentação e a posição relativa do material permanecem inalteradas. É desejável que os rolos de alimentação e o comprimento livre do eletrodo antes de ser alimentado sejam o mais curtos possível, garantindo a alimentação e o rejeito adequados. A área de alimentação do eletrodo tem a funcionalidade de sopro e orientação de ar, com monitoramento digital de pressão. A direção do sopro e orientação do ar é ajustável e equipada com uma escala de ângulo. Além disso, a alimentação do eletrodo é eficiente, silenciosa, livre de poluição e permite um ajuste fácil e quantificável do ângulo de inclinação.
5. Módulo de corte de eletrodo: Consiste nos mecanismos de prensagem e corte de eletrodos positivos e negativos, capazes de detectar automaticamente o orifício de marcação na extremidade do eletrodo (produzido por corte e vinco a laser). Uma vez atingido o número definido de abas de eletrodo ou reconhecendo o espaçamento entre as abas, o módulo pode cortar o eletrodo em um comprimento predeterminado. Também permite a funcionalidade de cortar eletrodos em comprimentos específicos. Recomenda-se que a lâmina de corte seja feita de materiais duros, como aço de tungstênio, e tanto a lâmina móvel quanto a lâmina fixa têm ângulos específicos. Além disso, a área de corte deve ter escudos de proteção de isolamento e sinais de alerta, além de ser tratada para evitar aderência.
6. Módulo para Remoção de Eletrodo e Separador Defeituoso em Bobinas Individuais: Consiste em um servo motor, acoplamento e mecanismo de guia linear e é programado para executar funções de remoção independentes. Ele permite a remoção separada de bobinas de eletrodo positivo e negativo defeituosos sem separadores. Quando um defeito é detectado no eletrodo positivo ou negativo, ele pode remover automaticamente a bobina junto com o separador ou removê-los separadamente de forma independente. Os produtos defeituosos são descarregados em um mecanismo separado e coletados em uma caixa de rejeição. Durante o processo de remoção de uma bobina sem separadores, o eletrodo não interfere ou esfrega contra outros componentes, garantindo que não afete o alinhamento do próximo material.
7. Módulo de enrolamento: Consiste em um mecanismo de estação dupla ou multiestação equipado com servomotores duplos ou servomotores múltiplos para acionar os mecanismos de enrolamento. Cada conjunto corresponde a 2 ou mais mecanismos de agulha de enrolamento. Também é equipado com um mecanismo de travamento e posicionamento para rotação da torre após a mudança de estação. Este módulo permite o enrolamento de células de bateria e a comutação automática entre diferentes estações de enrolamento, mantendo uma velocidade de linha constante durante o enrolamento. Ele pode realizar funções como enrolar primeiro o eletrodo positivo ou negativo, bem como alimentação e enrolamento simultâneos de ambos os eletrodos.
Evitar a geração de dobras internas dentro da célula da bateria durante o processo de enrolamento é crucial. As dobras internas podem levar ao revestimento de lítio local durante o uso real da bateria, apresentando riscos de segurança significativos.
Existe uma lei das rugas sinuosas em relação à geração de rugas: Para diferentes tipos de agulhas de enrolamento, existe a possibilidade de rugas entre as camadas do núcleo da ferida. A razão para as rugas é que, à medida que o eletrodo se acumula em cada volta do enrolamento, o raio da camada intermediária do eletrodo aumenta em δ e o comprimento acumulado do eletrodo também aumenta. Quando a taxa de aumento no comprimento da circunferência acumulada do eletrodo não é igual à taxa de aumento no raio do enrolamento, ocorrem rugas no eletrodo interno após a agulha do enrolamento comprimir o núcleo. Isso é conhecido como a lei das rugas sinuosas.
Geralmente, as agulhas de enrolamento em forma de diamante, devido às suas características estruturais, sofrem flutuações significativas de tensão do eletrodo durante o processo de enrolamento. A taxa de crescimento da circunferência do eletrodo é inconsistente com a taxa de crescimento do rádio, o que pode levar à ocorrência de rugas entre as camadas. Em comparação, agulhas de enrolamento elípticas, ovais e circulares não têm o problema de rugas.
8. O módulo de corte de membrana consiste em um mecanismo de faca de corte a quente e um mecanismo de proteção, e pode cortar a membrana de acordo com o comprimento necessário para o produto. A peça de corte precisa ter alta temperatura e proteção de segurança da lâmina, juntamente com sinais de alerta, e deve ser equipada com um dispositivo de isolamento térmico. Possui funções como soprar ar e usar um fuso de torre rotativa para achatar a membrana cortada, evitando rugas na membrana. Depois que a membrana é cortada, ela precisa ser sugada imediatamente para evitar que a membrana se enrole devido à eletricidade estática, o que pode resultar em mau acabamento da membrana.
9. O módulo de colagem de fita de terminação consiste em um mecanismo automático de preparação de fita, um sensor de orifício de marca de fita e um rolo de aplicação de fita. Depois que o rolo de fita é desenrolado, ele é automaticamente preparado para o comprimento necessário. O módulo também detecta automaticamente o orifício da marca da fita e o aplica no canto ou na extremidade do núcleo do eletrodo nu. O mecanismo de colagem da fita de terminação foi projetado para ser adaptável, permitindo que o posicionamento da fita seja ajustado com base na posição do núcleo do eletrodo nu na agulha do enrolamento. O mecanismo de desenrolamento da fita tem capacidade de desenrolamento ativo e inclui uma função antiestática.
10. O módulo de pré-impressão e corte consiste em um mecanismo de descarga do núcleo do eletrodo nu, uma unidade de pré-prensagem do núcleo do eletrodo nu e um mecanismo de transferência do núcleo do eletrodo nu. Ele descarrega automaticamente o núcleo do eletrodo nu da agulha de enrolamento e aplica a pré-prensagem durante o processo de transporte do núcleo do eletrodo nu de boa qualidade. Após a pré-prensagem, o código QR na superfície do núcleo do eletrodo é escaneado para ligar as informações e, em seguida, o núcleo do eletrodo é transferido para a máquina de corte por meio de uma correia de transferência. A placa de pressão em contato com o núcleo do eletrodo nu é tratada para evitar a aderência e é equipada com um sensor de pressão de pré-prensagem para evitar danos ao núcleo do eletrodo nu.
11. Sistema de remoção de poeira: Consiste em um dispositivo de remoção de poeira no cortador de folhas de gravidade positiva, um dispositivo de escova, componentes de remoção de eletricidade estática, uma folha de gravidade positiva/haste magnética local, uma tampa de remoção de poeira separada e um sistema FFU. e a superfície da célula nua e evitar que o ambiente entre na célula nua. Além disso, o duto de entrada/saída do coletor de pó é feito de materiais reforçados e antiestáticos. A parede interna do tubo é lisa. O elemento filtrante é feito de material antiestático. O duto de entrada de ar deve evitar curvas em ângulo reto. A tampa fechada integral usa uma tampa transparente isolada e divisórias para isolar diferentes áreas, ou seja, a área do eletrodo de frente, a área de contato, a área de enrolamento e a área de descarga, para evitar a mistura entre armazéns e a mistura externa. Ao mesmo tempo, usando um sistema FFU para controlar o fluxo de ar dentro do equipamento, ele é mantido a uma pressão positiva ligeiramente mais alta do que o ambiente externo. Todos os conectores rotativos, fixadores, tampas e correias em áreas propensas a atrito e colisões devem usar uma combinação de materiais metálicos e não metálicos ou totalmente não metálicos. Componentes como elementos pneumáticos devem ser feitos de materiais livres de cobre e zinco e devem passar por tratamento de superfície para evitar a geração e contaminação de pó de cobre e zinco.
As tubulações de sucção de pressão negativa convergem para um duto de sucção principal e são então conduzidas para fora do equipamento. Todo o campo de fluxo de ar é simulado por meio de modelagem computacional. O duto de entrada requer uma certa velocidade do ar, evitando curvas fechadas. Se o ângulo de curvatura exceder 45 graus, é necessário um ponto de acesso para manutenção.
12. O sistema de detecção de processo de eletrodo consiste em vários conjuntos de câmeras industriais de alta resolução, fontes de iluminação de visão de máquina, estruturas de montagem, computadores industriais e monitores. As câmeras CCD de visão capturam imagens das posições do eletrodo catódico, eletrodo de ânodo, diafragmas superior e inferior e marcadores especificados nos quatro cantos da célula da bateria. O software de visão de máquina no PC analisa as distâncias bidimensionais entre as bordas ou limites do material e as posições dos marcadores. Cálculos em tempo real são realizados pelo computador para determinar os valores de deslocamento entre o mesmo círculo de ânodo e diafragma superior, mesmo círculo de cátodo e ânodo, mesmo círculo de cátodo AT9 e ânodo, mesmo círculo de diafragma inferior e cátodo e o círculo anterior de cátodo e o próximo círculo de ânodo. Esses valores são exibidos em tempo real como curvas e camadas de gráfico de dispersão em um monitor ou tela sensível ao toque. Além disso, o sistema monitora os valores de deslocamento das células da bateria.
O sistema processa os dados e calcula os valores máximos, mínimos e médios de deslocamento entre cada camada de núcleos de eletrodos nus. O alcance de detecção cobre do primeiro ao último círculo da célula da bateria, garantindo uma inspeção abrangente.
O esquema de detecção de CCD é mostrado na Figura. O sistema de detecção é instalado próximo ao lado externo da agulha de enrolamento da máquina de enrolamento, garantindo que não interfira no movimento e operação dos componentes do enrolamento. O ângulo e a distância da placa grande são continuamente ajustáveis. Os componentes estruturais precisam ter alta resistência e instalação firme para evitar afetar a precisão da medição. Tanto a câmera quanto a lente são projetadas com proteção contra colisões para evitar colisões acidentais que possam causar deslocamento ou danos aos componentes estruturais.
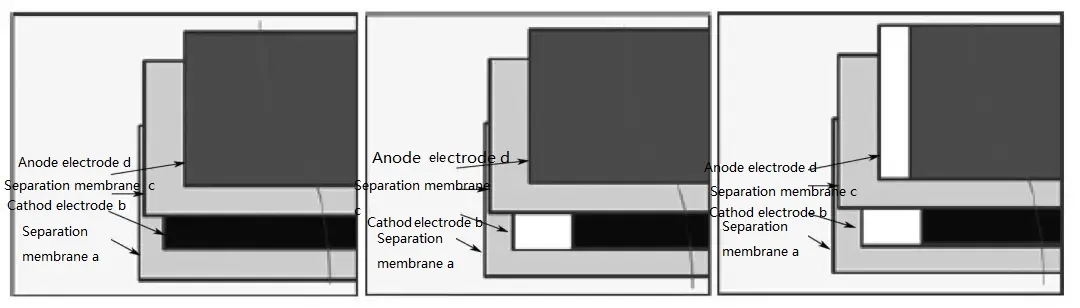
03. Seleção de dispositivos e casos de aplicação
(1) Esclarecer o processo de entrada
Confirme os requisitos de compatibilidade dos materiais recebidos, incluindo parâmetros como a faixa de largura e espessura das folhas de eletrodo positivo e negativo, bordas onduladas, curvas serpentinas, diâmetro da bobina e diâmetro interno da bobina.
(2) Esclareça as especificações do produto
(1) Confirme a compatibilidade das especificações da célula nua, incluindo parâmetros principais, como espessura da célula, largura, altura, etc.
Exemplo de especificações de célula

Dimensões da célula conforme mostrado no diagrama
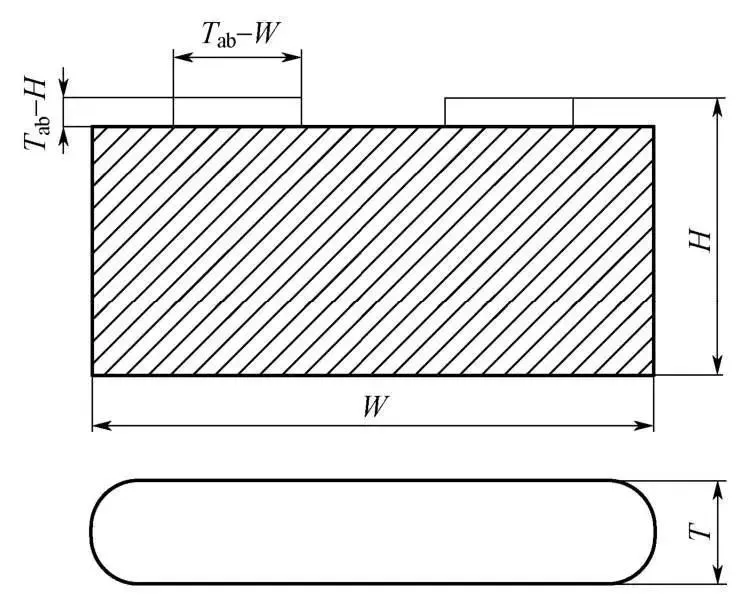
Esclareça o processo de aplicação do adesivo, seja usando adesivo de um lado ou de dois lados. Especifique dimensões como largura da fita e comprimento do adesivo.
(3) Esclareça a configuração do equipamento
(1) Configuração funcional: Com base no processo de entrada e nas especificações do produto, confirme os requisitos gerais de configuração do equipamento. A configuração de desenrolamento inclui desenrolamento duplo para eletrodos positivos e negativos com função de troca automática de bobina, desenrolamento de eixo duplo para membrana de separação e troca manual de bobina. O controle de desalinhamento inclui três ou mais níveis de correção de desalinhamento durante o processo do eletrodo. A cabeça de enrolamento adota acionamento direto e os tipos de agulhas de enrolamento incluem agulhas em forma de diamante, elípticas ou circulares, com opção de configuração de agulha dupla ou tripla. A alimentação da agulha emprega um mecanismo de garra dupla para alimentação. Após a alimentação celular, a pré-prensagem é realizada antes do processo de alimentação subsequente.
(2) Estabelecer e fazer cumprir especificações gerais para sistemas mecânicos, elétricos e de informação.