Baterias prismáticas referem-se a baterias com invólucros de alumínio. Eles usam tecnologia de vedação a laser e a tecnologia de invólucro de alumínio totalmente selada já está altamente madura. Possui baixos requisitos para indicadores de tecnologia de materiais, como geração e expansão de gás, tornando-se uma forma popularizada de bateria de energia na China. Em comparação com as outras duas formas de baterias de lítio (cilíndricas e bolsas), as baterias prismáticas têm vantagens proeminentes no uso no mercado, incluindo:
(1) Alta confiabilidade de embalagem.
(2) Alta eficiência de integração do sistema.
(3) Relativamente leve com alta densidade de energia.
(4) Estrutura simples e escalabilidade conveniente, tornando-a a principal escolha para células individuais de grande capacidade.
(5) Alta capacidade de célula individual, estrutura de sistema simples e fácil gerenciamento de bateria.
01 Principais funções e descrição do equipamento
A linha de montagem de baterias de lítio com invólucro de alumínio é usada para a montagem intermediária de baterias de energia e é uma parte importante do processo de produção de baterias de energia. Tem um impacto significativo no desempenho e na precisão da bateria. Como resultado, o nível de automação e a precisão operacional dessa linha de montagem estão atraindo cada vez mais a atenção do mercado. Nesta seção, apresentaremos uma linha de montagem de baterias altamente madura e comprovada no mercado que foi reconhecida e aceita. A linha de montagem tem as seguintes características:
1. Forte compatibilidade: Pode ser compatível com várias séries diferentes de produtos de acordo com os requisitos do cliente.
2. Design modular: Tempo de troca curto, menos peças e baixo custo.
3. Alta precisão de montagem: Posicionamento duplo usando métodos visuais e mecânicos para aumentar a precisão do posicionamento.
4. Personalização para diferentes tipos de células e rotas de processo específicas do cliente para obter linhas de montagem totalmente automatizadas.
5. Disposição razoável do equipamento: Linha Espaço-economia, inteiramente automatizada, e baixo custo laboral.
6. Garantia de qualidade alta da fabricação: Teste e monitoração completos do parâmetro.
7. Garantia de fabricação para segurança e consistência da bateria.
Esta linha de produção automatizada é usada para a montagem automática de células de bateria de íon de lítio prismáticas revestidas de alumínio após o enrolamento. A linha de produção consiste principalmente nos seguintes componentes principais: máquina de teste de prensagem a quente, máquina de raios-X, máquina de emparelhamento, máquina de solda ultrassônica, máquina de solda de abas, máquina de alinhamento de núcleo, máquina de solda de filme/selagem a quente/adesivo, máquina de solda pré-ponto para invólucro, máquina de solda de tampa a laser e máquina de teste de vazamento de hélio. Ele realiza funções como prensagem térmica de células de bateria, teste de raios-X, pré-soldagem e emparelhamento de abas de eletrodo, soldagem de conectores de aba, aplicação de adesivo traseiro, soldagem a laser de placas de cobertura, aplicação de adesivo, dobragem de aba e alinhamento de núcleo, encapsulamento, revestimento e soldagem de vedação de tampa, permitindo automação total em todo o processo.
1.2 Tendências futuras de desenvolvimento de linhas de montagem
A linha de produção de baterias de invólucro de alumínio (prismática) está em uso há muito tempo, a tecnologia correspondente é muito madura e a linha de montagem existente também é semelhante. A tendência de desenvolvimento futuro, além de continuar a melhorar os materiais e encontrar materiais de células de alto desempenho, para linhas de produção de montagem de baterias, alta eficiência e baixo custo ainda são as direções de desenvolvimento futuro das baterias de lítio de energia. Uma visão geral do desenvolvimento do mercado existente Depois de resumir, os seguintes pontos merecem atenção:
(1) O desempenho do corpo da bateria, como tamanho da bateria, densidade de energia, estrutura de várias guias, etc.
(2) Eficiência de produção de montagem, melhorar continuamente a eficiência da produção, garantindo que os custos do equipamento não mudem significativamente.
(3) A automação das linhas de montagem de baterias continua a melhorar e o rendimento da produção é mais fácil de controlar. O tempo de produção de cada processo é razoavelmente controlado, encurtando efetivamente o tempo de produção das baterias de lítio e melhorando muito os problemas de alta intensidade de trabalho para os trabalhadores e altos custos de produção.
(4) Melhor compatibilidade, adequada para uma gama mais ampla de produtos.
(5) A tecnologia modular é uma forma importante de melhorar a eficiência.
1.3 Projeto de invólucro de alumínio (prismático) produção e cadeia de fabricação da bateria de lítio
Ao projetar uma linha de montagem de produção de baterias de lítio com caixa de alumínio (prismática), diferentes designs são considerados com base nos requisitos do cliente. Tendo em conta os problemas encontrados e as práticas correspondentes no processo de produção, são considerados principalmente os seguintes aspetos:
1. Processo do produto: Isso inclui o tamanho da bateria, tamanho da aba e espessura da soldagem, entre outros.
2. Espaço da fábrica: Arranjo adequado das posições específicas do equipamento da linha de produção, otimização de mecanismos, consideração da ergonomia, facilidade de operação manual e facilidade de manutenção.
3. Projeto do equipamento: Quanto mais simples a estrutura, mais fácil a operação.
4. Alocação do ritmo da linha de produção: A ênfase é colocada na eficiência das estações de trabalho de gargalo. Se a eficiência não for atingida, as estações de trabalho individuais podem ser modificadas para estações de trabalho duplas ou múltiplas. O alto desempenho de segurança e o rendimento na primeira passagem também são considerações importantes.
5. Método de posicionamento do produto: Diferentes métodos de posicionamento do produto são usados para diferentes requisitos do cliente, como posicionamento lateral, posicionamento de linha de base nos dois lados e posicionamento do acessório.
6. Dispositivo de prevenção de poeira: Na linha de montagem de baterias cilíndricas, cada dispositivo que requer remoção de poeira é equipado com instalações correspondentes, como coletores de poeira e escovas.
7. Projeto de logística dentro do equipamento: Isso inclui transporte interno de equipamentos e transporte entre equipamentos.
8. Inspeção de qualidade: Toda a linha de montagem inclui inspeção CCD, medição de espessura de célula, inspeção de isolamento, detecção de curto-circuito e muito mais.
9. Consistência na aparência da linha de produção: Manter a aparência estética de todo o conjunto de equipamentos.
02 Composição do equipamento e estrutura principal
O layout geral da linha de montagem da bateria de lítio de alumínio é o seguinte:
(1) Dimensões de toda a linha: comprimento × largura × altura = 3700 mm × 7000 mm × 2400 mm (a altura não inclui luzes de alarme), altura da superfície operacional 900 mm, espaçamento do equipamento 800 ~ 1000 mm.
(2) Aparência: O chassi de suporte de tensão adota uma estrutura soldada de tubo quadrado, a estrutura de vedação superior adota uma estrutura de perfil de liga de alumínio e é selada com plexiglass. Toda a tampa do equipamento é coberta com chapa metálica.
(3) Interface de operação: Cada dispositivo é equipado com uma tela sensível ao toque operada de forma independente e as telas sensíveis ao toque de todos os dispositivos são incorporadas.
(4) Layout de toda a linha: O layout da linha de montagem da bateria do invólucro de chumbo é mostrado na Figura .
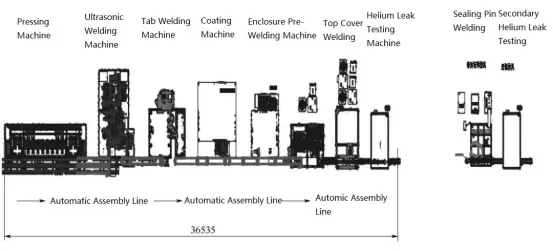
Esta linha de produção é uma linha de montagem totalmente automatizada que inclui todo o processo de produção de baterias com caixa de alumínio, desde a máquina de enrolamento até a máquina de teste de vazamento de hélio. O processo inclui: enrolamento para a linha de transporte de prensagem a quente (com 6 conjuntos de robôs de manuseio de materiais na máquina de enrolamento) → máquina de prensagem a quente → máquina de solda ultrassônica máquina de solda a laser de → guia máquina de solda a laser → máquina de embalagem de células → gabinete e máquina de solda pré-ponto → máquina de solda a laser de tampa → máquina de teste de estanqueidade.
2.1 Máquina de prensagem a quente
A máquina de prensagem a quente é usada para a moldagem por compressão térmica de células de bateria enroladas. Suas principais funções incluem leitura de código de barras de células, carregamento automático de células A/B, prensagem a quente, teste Hi-pot e rejeição de produtos defeituosos. A temperatura de prensagem a quente, pressão, tempo, parâmetros de teste Hi-pot e resultados são associados ao código de barras correspondente e carregados no sistema MES. O equipamento consiste principalmente em módulos para carga/descarga de células, detecção e prensagem a quente. Este equipamento é o primeiro processo de montagem de células de bateria com caixa de alumínio, e a qualidade da célula prensada a quente afeta diretamente a qualidade dos produtos processados subsequentes. Portanto, a eficiência, a precisão de trabalho e o nível de automação deste equipamento de montagem são considerações cruciais. O layout do equipamento e o fluxo de trabalho são mostrados no diagrama.
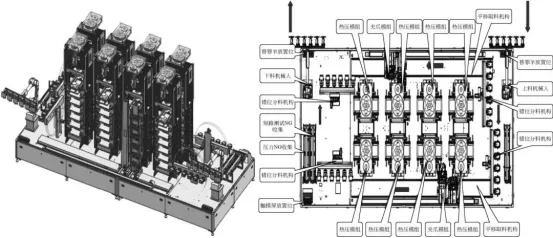
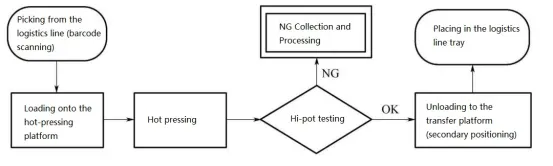
A partir do diagrama, fica claro o processo de operação das células da bateria enrolada na máquina de prensagem a quente. Durante o processo de trabalho, o equipamento realiza a prensagem a quente e subsequentes testes das células da bateria enroladas. Os resultados do teste, incluindo temperatura de prensagem a quente, pressão, tempo e Hi-pot, são carregados no sistema MES para monitoramento e feedback em tempo real. Produtos defeituosos são rejeitados para garantir a qualidade do processamento.
A partir do diagrama de layout do equipamento, pode-se ver que os principais componentes, como os braços robóticos de carga e descarga, transportadores de transferência, robôs de transferência, mecanismos de separação de desalinhamento e módulos de prensagem a quente, desempenham um papel crucial na montagem dos produtos semiacabados. Vamos fornecer explicações detalhadas para alguns desses componentes.
(1) Mecanismo de distribuição de deslocamento. A figura mostra o mecanismo de distribuição de material desalinhado. A função do módulo de posicionamento flip é: o mecanismo flip usa um servo acionamento por correia para realizar o acionamento do grampo e o flip síncrono da placa de conexão. A braçadeira permanece sempre na horizontal e a inversão é suave e confiável. O dispositivo de posicionamento usa um cilindro de mandíbula de fixação e um cilindro de link duplo para fixação e posicionamento; a superfície de contato com o núcleo da bateria usa material POM.
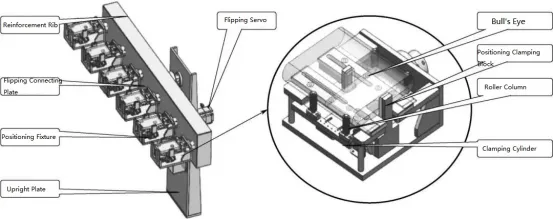
(2) Mova o módulo para cima e para baixo. O módulo de carga e descarga é mostrado na figura. Suas principais ações são: translação utilizando um servo módulo de correia síncrona e acionamento por correia dupla para aumentar a suavidade do movimento do módulo de carga e descarga; o módulo de carga e descarga usa um servo de correia para entrada e saída de materiais e um servo controle independente; as garras de fixação são levantadas e abaixadas usando um cilindro de parafuso; O mecanismo de mudança de passo usa um mecanismo de ligação servo-acionado, usando o link do meio como referência de posicionamento para obter uma mudança de passo síncrona. O servo pode controlar o tamanho equidistante das garras de fixação para obter diferentes condições de trabalho da prensa a quente. O módulo de translação de posição sincroniza o carregamento e descarregamento de materiais.
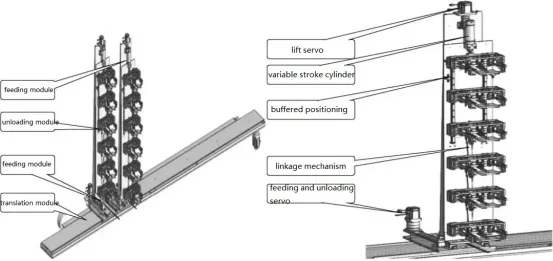
(3) Componentes de prensagem a quente. Os componentes de prensagem a quente do equipamento de prensagem a quente são mostrados na figura e sua descrição detalhada é a seguinte:
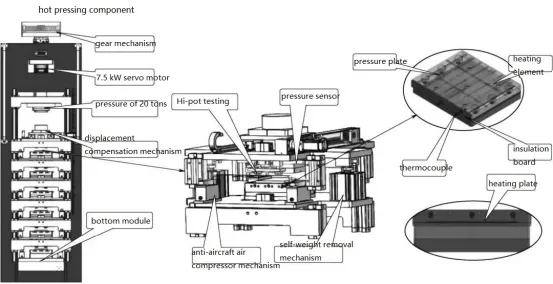
Componentes principais: Cilindro de reforço (pressão de 20 t, 6 camadas), tubo de aquecimento, controlador de temperatura, sensor de pressão, etc.
Procedimento operacional: Execute testes de prensagem a quente e Hi-pot nas células da bateria.
2.2 Máquina de solda ultrassônica
A máquina de solda ultrassônica completa principalmente a soldagem ultrassônica de células de bateria por meio de processos como varredura de células, emparelhamento automatizado de células por braços robóticos, calibração de células e detecção de polaridade, detecção e calibração de polaridade da placa adaptadora, acessórios de soldagem de placas adaptadoras, acessórios de soldagem de células, colocação de tampa protetora, soldagem ultrassônica e extração de poeira, modelagem de marca de solda, aplicação de adesivo e inspeção de adesivo e descarga automática. Este equipamento realiza varredura de células, soldagem ultrassônica, aplicação de adesivo e ligação de informações do emparelhamento de células ao encapsulamento. Inclui principalmente funções como digitalização de células na chegada, calibração e alimentação de células, calibração e alimentação de placas adaptadoras, inspeção de adesivos e upload de informações de ligação ao sistema MES.
O mecanismo de preensão é equipado com um sensor de cor para identificar as abas de polaridade das células da bateria, garantindo que as abas não estejam emparelhadas incorretamente. As células da bateria são agarradas pelo braço robótico da esteira transportadora de entrada. Após passarem pelo posicionamento secundário, eles são colocados na bandeja, garantindo um erro de desalinhamento de ≤±0,2 mm para abas de polaridade de células A/B. As células da bateria são colocadas na bandeja com alinhamento central. Antes de colocar as células, os clipes elásticos ao redor da bandeja são abertos e, em seguida, o braço robótico coloca as células na bandeja, após o que os clipes se fecham, posicionando as células no centro da bandeja.
Composição do equipamento e estruturas-chave
Módulo de carregamento de células, linha de ciclo de soldagem ultrassônica de células e módulo de fixação, folha adaptadora, módulo de carregamento de folha protetora, módulo de carga e descarga de tampa de folha protetora, módulo de soldagem de eletrodo positivo e negativo ultrassônico, módulo de achatamento de estampagem de solda, módulo de colagem do núcleo da bateria O módulo de cola protetora, o módulo de cola de proteção da célula da bateria, o módulo de descarga da célula da bateria e a detecção de cola são relativamente críticos e desempenham um papel vital em todo o montado produto semiacabado. Vários desses mecanismos são selecionados para introdução detalhada.
(1) Módulo de carregamento do núcleo da bateria (como mostrado na imagem). Tem as funções de carregamento automático de células de bateria, remoção de poeira de materiais recebidos, prevenção anti-tolo de materiais recebidos, buffer de materiais recebidos e funções de alarme de falta. Ele também tem a função de escanear o código para ligar as células da bateria.
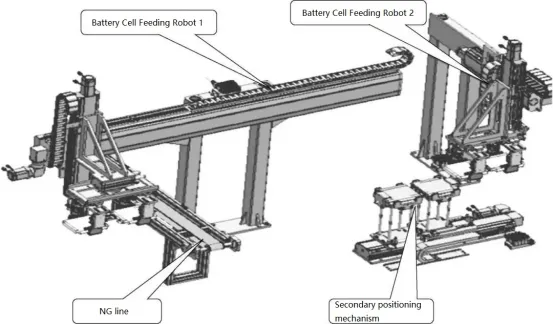
um. Componentes principais: Mecanismo de tradução + mecanismo de elevação, pinça de célula de bateria, etc.
b. Procedimento operacional: O processo de alimentação e manuseio da célula da bateria usa um módulo de correia. O robô de alimentação 1 pega um grupo de células de bateria do palete na linha de logística do cliente e as coloca no mecanismo de posicionamento secundário. Depois que as células da bateria são posicionadas secundariamente, o robô de manuseio 2 pega as células e as coloca na linha de ciclo. Se durante o processo de alimentação, for detectado que um par de células de bateria tem uma única célula NG (não boa), o robô de manuseio 1 colocará a célula NG de volta na linha NG, enquanto a célula OK (boa) será colocada no mecanismo de emparelhamento para correspondência adicional.
(2) linha de ciclo de soldagem ultrassônica de célula de bateria e módulo de fixação.
um. Componentes principais: Linha de ciclo, módulo, blocos de posicionamento de borda longa e curta, cilindros, trilhos de guia, etc.
b. Procedimento operacional (descrição funcional sem etapas operacionais específicas): O robô de manuseio 2 alimenta as células da bateria no dispositivo da linha de ciclo, que prende as células. O mecanismo de translação move o aparelho para a próxima estação de trabalho.
O diagrama esquemático da linha de ciclo de soldagem ultrassônica é mostrado na figura.
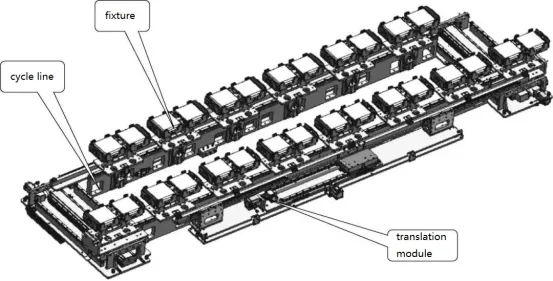
(3) O módulo para carregar placas adaptadoras e películas protetoras (conforme mostrado no diagrama).
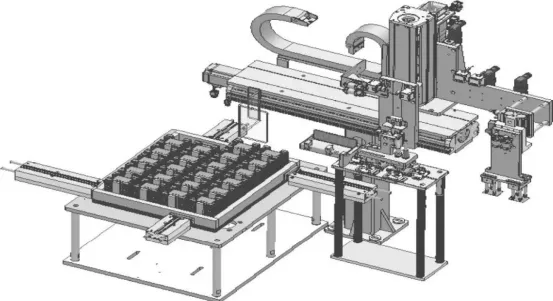
um. O carregamento de placas adaptadoras de cobre-alumínio inclui medidas para evitar extravio ou inserção reversa, como detecção de polaridade, para evitar erros humanos.
b. O carregamento das placas de conexão é equipado com uma escova para evitar sucção inadequada ou coleta de várias placas. Também inclui funções como sopro de ar e agitação a vácuo para garantir a separação e detecção adequadas de várias placas. Existe um mecanismo de eliminação de resíduos para armazenar as placas múltiplas rejeitadas.
c. A preparação de bandejas de película protetora envolve o carregamento manual no suporte do clipe. O bocal de sucção pega um conjunto de películas protetoras a cada vez, esgotando o suprimento na extremidade de alimentação. A mesa giratória (ou módulo móvel) gira para a próxima posição para garantir o fornecimento ininterrupto de películas protetoras.
d. Os principais componentes incluem servo motor, parafuso de avanço, cilindro e ventosa.
e. A preparação das bandejas de placas adaptadoras envolve o bocal de sucção pegando um conjunto de placas adaptadoras a cada vez, esgotando o suprimento na extremidade de alimentação. A bandeja gira para a próxima posição para garantir o fornecimento ininterrupto de placas adaptadoras.
f. Uma única carga pode sustentar a produção por 40 minutos.
(4) O módulo para carregar e descarregar tampas de película protetora (conforme mostrado no diagrama).
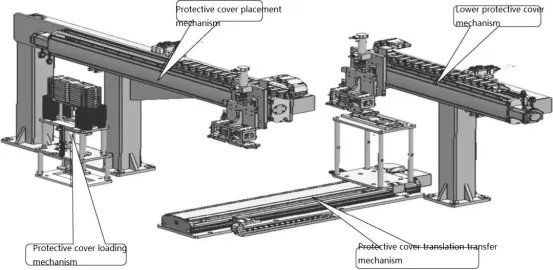
um. Componentes chave: Servo motor, parafuso de avanço, cilindro, trilho guia, etc.
b. Procedimento operacional: No estado inicial, as tampas de proteção são colocadas manualmente no mecanismo de preparação da tampa de proteção superior. O mecanismo de colocação da tampa protetora superior pega um conjunto de tampas protetoras e as move para a estação de trabalho da tampa protetora superior, garantindo que todas as placas de cobertura protetora estejam em um loop contínuo na linha de montagem. Ao remover a tampa protetora inferior, o mecanismo da tampa protetora inferior recupera a tampa do acessório na linha de montagem 2. A plataforma move a tampa protetora para o mecanismo de transferência da tampa protetora, que então se move para a posição superior da tampa protetora. O mecanismo de colocação da tampa protetora superior recupera a tampa protetora e a coloca no acessório correspondente na linha de montagem 1.
c. Uma única carga pode sustentar a produção por 40 minutos.
(5) Módulo de soldagem de eletrodo positivo e negativo ultrassônico (conforme mostrado no diagrama).

um. Componentes chave: Plataforma, máquina de solda ultrassônica, cilindro, etc.
b. Processo de operação: Após o posicionamento do acessório, o cilindro de elevação do eixo Z sobe e a cabeça de soldagem ultrassônica desce para concluir o processo de soldagem. A translação do eixo X e do eixo Y é ajustada usando servomotores para posicionar a máquina de solda e facilitar a troca de ferramentas. O deslocamento do eixo X e do eixo Y garante a conformidade com os requisitos dimensionais para troca de ferramentas.
(6) Módulo de achatamento de impressão de solda (conforme mostrado no diagrama). Este módulo garante que a película protetora permaneça plana e as abas dos terminais não sejam dobradas. O bloco de pressão é feito de material resistente ao desgaste chamado poliéter éter cetona (PEEK).
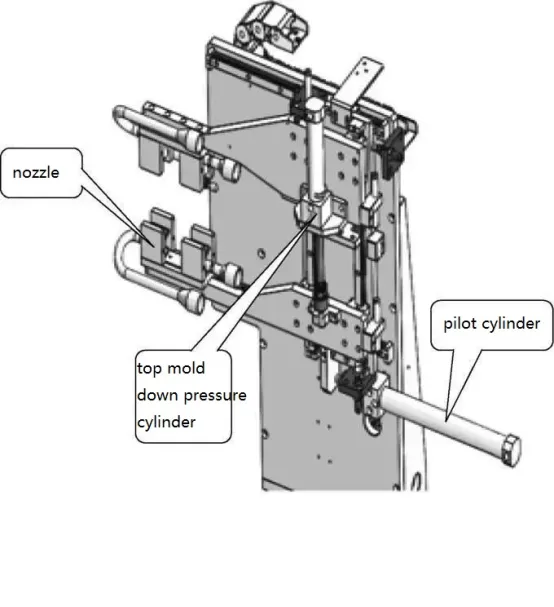
um. Componentes principais: trilho deslizante, cilindro, etc.
b. Processo de ação: Depois que a braçadeira no corpo da linha de circulação está no lugar, o cilindro de prevenção aciona os moldes superior e inferior para se estender para frente, então o molde inferior é empurrado para cima, o molde superior é pressionado para baixo e a marca de soldagem é nivelada. Posteriormente, o molde superior se move para cima, o molde inferior se move para baixo e o cilindro de prevenção aciona os moldes superior e inferior para retrair a braçadeira de prevenção de posição.
2.3 Máquina de solda a laser de placa adaptadora
1) Composição do equipamento
As principais funções do equipamento da máquina de solda a laser da placa adaptadora incluem o carregamento automático da tampa superior e das células da bateria e a soldagem da peça de conexão e da tampa superior em um corpo por meio de soldagem a laser, descarga automática após remoção de poeira e aplicação de cola, conforme mostrado na figura.
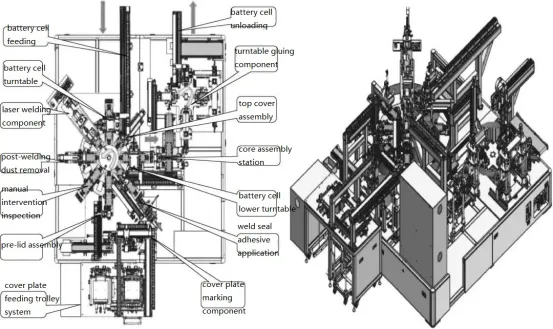
Dimensões do equipamento: Comprimento × Largura × Altura = 2800mm × 3800mm × 2300mm.
Aparência: O chassi de suporte de carga adota uma estrutura de soldagem de tubo quadrado e a estrutura de vedação superior adota uma estrutura de perfil de liga de alumínio, selada com vidro orgânico.
Interface operacional: O equipamento está equipado com uma tela sensível ao toque independente para operação e todas as telas sensíveis ao toque do equipamento são incorporadas.
2) Estruturas-chave
A partir do diagrama acima, pode-se ver que o mecanismo de alimentação da placa de cobertura, o conjunto da tampa superior, o módulo de soldagem a laser, o mecanismo de remoção de poeira pós-soldagem e o componente de aplicação do adesivo de vedação de solda são cruciais e desempenham um papel vital na montagem do produto semiacabado. Forneceremos introduções e explicações detalhadas para alguns desses mecanismos.
(1) mecanismo de alimentação da placa de cobertura
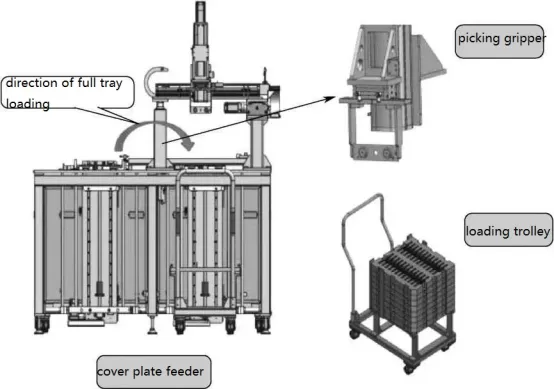
a. Função: O mecanismo de alimentação da placa de cobertura atinge o fornecimento de placas de cobertura e inclui recursos como posicionamento e transferência da bandeja.
b. Componentes chave: Mecanismo de elevação, mecanismo de posicionamento da bandeja, carrinho pequeno, etc.
c. Requisitos: Carregamento único para atender a produção contínua do equipamento por 30 minutos; um carrinho de carregamento em uso e um sobressalente e três carrinhos de descarga; Precisão de posicionamento secundário da bandeja de ≤0,1 mm.
(2) conjunto da tampa superior
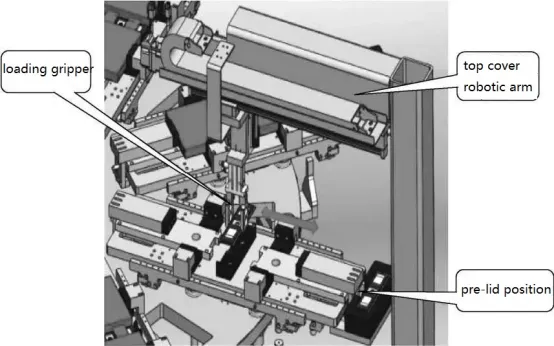
a.Função: Para agarrar a placa de cobertura codificada e colocá-la na plataforma giratória.
b. Componentes chave: Módulo de correia síncrona de tradução, módulo de parafuso de elevação, garra de preensão, etc.
c. Requisitos: Agarramento confiável sem queda ou dano de material, precisão repetitiva da operação do mecanismo ≤±0,05 mm, design flexível do braço robótico, partes sem contato do braço robótico que entram em contato com o produto devem usar materiais não contaminantes.
(3) Módulo de soldagem a laser (conforme mostrado no diagrama).
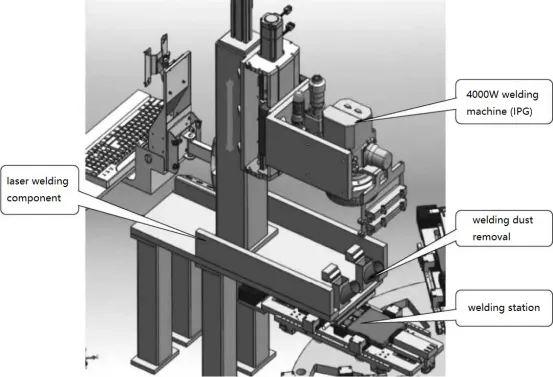
a. Função: Para soldar a placa de cobertura e a aba juntas usando a máquina de solda a laser.
b. Componentes chave: Plataforma de soldagem, transportador de células, etc.
(4) Mecanismo de remoção de poeira pós-soldagem (Figura 21): O cilindro de elevação abaixa, cobrindo a área de soldagem para criar um espaço selado para extração de poeira. A velocidade do fluxo de ar de sucção é de ≥12m/s e a velocidade é infinitamente ajustável dentro da faixa máxima.
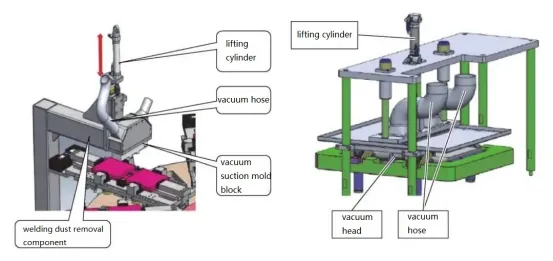
um. Componentes principais: Cilindro de elevação, motor rotativo, porta de sucção, etc.
b. Processo de operação: O dispositivo se move para a estação de remoção de poeira; O cilindro desce e o motor gira para realizar a remoção de poeira.
(5) Componente de aplicação do adesivo de vedação de solda (conforme mostrado no diagrama).
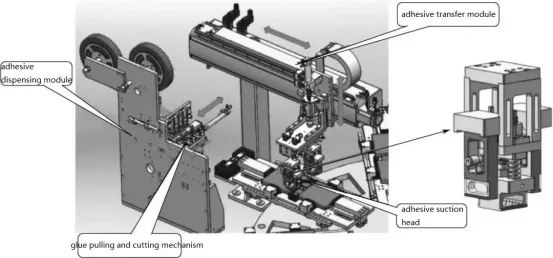
a. Função: Aplique adesivo protetor na parte superior da área de soldagem da aba.
b. Componentes principais: Mecanismo de tração de cola, mecanismo de corte de cola, mecanismo de aplicação de cola, conjunto de rolo de cola, etc.
c. Requisitos: Comprimento da fita ajustável e colocação do adesivo; detecção de vácuo e aviso de fita de backup defeituosa; função de detecção de presença de fita; dispositivo de modelagem para a área de soldagem antes da aplicação do adesivo; rendimento da aplicação de adesivo ≥99,8%.
2.4 Máquina de embalagem de filme
1. Principais funções do equipamento:
A máquina de embalagem de filme é usada principalmente para modelagem automática de células de bateria, alimentação automática do separador e bandeja inferior, envolvendo a célula com o separador, aplicando adesivo nas superfícies laterais e inferiores, teste CCD, etc. O layout do equipamento é mostrado no diagrama.
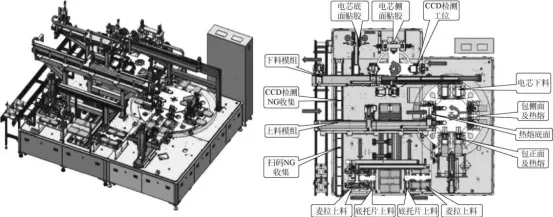
Aqui estão as especificações básicas do equipamento:
· Dimensões externas do equipamento: 3100mm × 4000mm × 2300mm.
· Rendimento do equipamento: ≥99,8% (excluindo a entrada de materiais defeituosos).
· Tempo de atividade do equipamento: ≥98% (referente apenas a falhas causadas por problemas relacionados ao equipamento).
2) Estruturas-chave
A partir do diagrama de layout da máquina de embalagem de filme, pode-se observar que o mecanismo de aplicação de adesivo inferior, o mecanismo de layout de alimentação do separador e da bandeja inferior, o mecanismo de filme de embalagem frontal, o mecanismo de aplicação de adesivo inferior e o mecanismo de mesa giratória de aplicação de adesivo lateral são cruciais e desempenham um papel vital na montagem do produto semi-acabado. Vamos fornecer explicações detalhadas para alguns desses mecanismos.
(1) Layout do separador e da alimentação da bandeja inferior (conforme mostrado no diagrama).
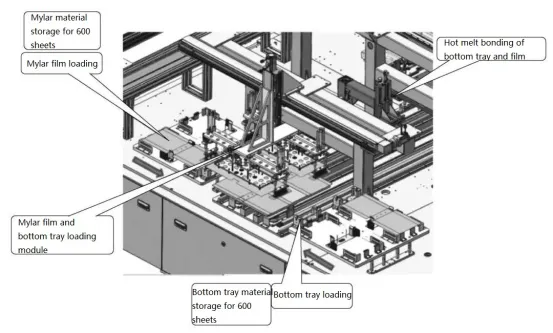
um. Componentes principais: Conjunto de alimentação manual de Mylar (1 conjunto), braço robótico de alimentação de Mylar (1 conjunto), caixa de material da bandeja inferior (1 conjunto), braço robótico de alimentação da bandeja inferior (1 conjunto), plataforma de fusão a quente da bandeja inferior de Mylar (1 conjunto), mecanismo de fusão a quente (1 conjunto).
b. Processo de operação: O braço robótico coloca a bandeja inferior no dispositivo de fusão a quente → O braço robótico de alimentação Mylar coloca o filme no dispositivo de fusão a quente → O dispositivo de fusão a quente é movido para a estação de fusão a quente → Processo de fusão a quente → O braço robótico de alimentação e descarga de filme da plataforma giratória aguarda na posição de recuperação.
(2) Estação de filme de embalagem frontal (conforme mostrado no diagrama). O layout da embalagem do filme e da plataforma giratória hot melt é mostrado no diagrama.
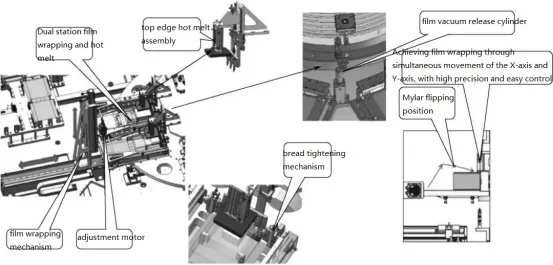
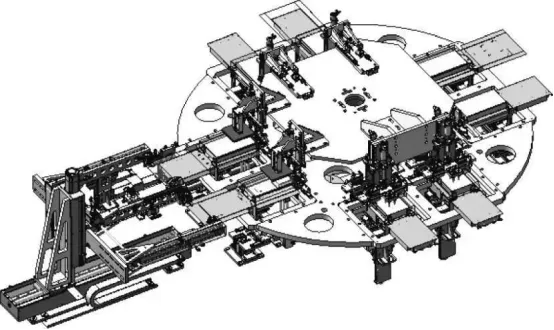
um. Componentes chave: Acessórios de estação de trabalho (8 conjuntos), conjunto de fusão a quente (1 conjunto), conjunto de embalagem de filme (1 conjunto), mecanismo de filme dobrável (1 conjunto), mecanismo de abertura de acessório (3 conjuntos).
b. Processo de operação: → de carregamento de filme → de carregamento de células → de fusão a quente da superfície inferior → → de envolvimento de filme frontal de dobragem de filme lateral → Descarga de → de fusão a quente da superfície lateral.
(3) Mecanismo de aplicação do adesivo inferior (conforme mostrado no diagrama).
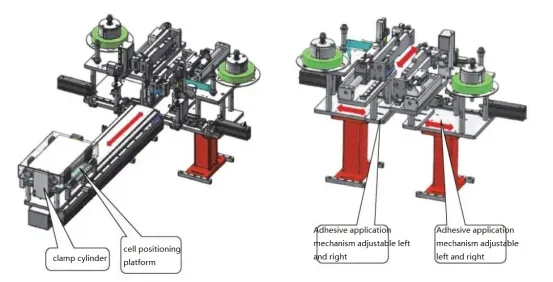
um. Existem fitas adesivas em forma de L em ambos os lados do fundo; O comprimento e a posição das fitas podem ser ajustados, com posições adesivas simétricas e um desvio de ±0,5 mm. O processo adesivo não deve causar pressão ou arranhões na célula da bateria.
b. O backup de adesivo ruim pode ser detectado e tem uma função de aviso. Após a aplicação do adesivo, o adesivo é inspecionado quanto à presença ou ausência usando um sensor de marca de cor.
c. O backup adesivo manual é realizado manualmente.
d. Função: Depois de envolver a célula da bateria, o adesivo é aplicado para fixá-la na bandeja inferior em forma de "L".
e. Componentes chave: Rolo de cola, aplicação de adesivo e montagem de corte, etc.
f. Requisitos: A taxa de defeito adesivo ≥ 99,6%; a aplicação do adesivo deve ser contínua, sem nenhum caso de quebra da fita; as fitas adesivas devem ser aplicadas na célula da bateria sem rugas ou descamação.
(4) Mesa giratória de aplicação de adesivo lateral (conforme mostrado no diagrama).
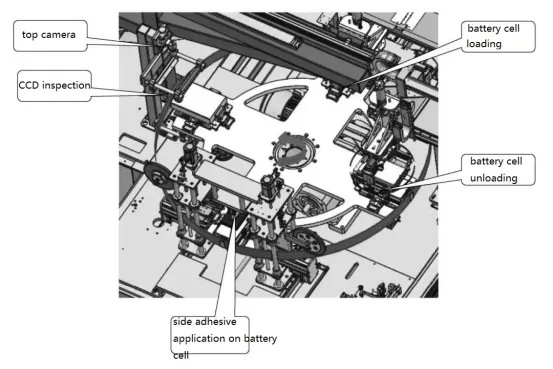
a. Há uma tira de fita adesiva de cada lado.
b. O comprimento e a posição da fita podem ser ajustados, com posições adesivas simétricas e um desvio de ±0,5 mm.
c. O processo adesivo não deve causar pressão ou arranhões na célula da bateria.
d. O backup adesivo ruim pode ser detectado e tem uma função de aviso.
e. Após a aplicação do adesivo, o adesivo é inspecionado quanto à presença ou ausência usando um sensor de marca de cor.
f. O backup adesivo manual é realizado manualmente.
g. Função: Depois de envolver a célula da bateria, o adesivo é aplicado em ambos os lados da célula da bateria para prendê-la em forma de "U".
h. Componentes chave: Rolo de cola, aplicação de adesivo e montagem de corte, montagem de parafuso de avanço do eixo X, etc.
i. Requisitos: A taxa de defeito do adesivo ≥ 99,6%; a aplicação do adesivo deve ser contínua, sem nenhum caso de quebra da fita; as fitas adesivas devem ser aplicadas na célula da bateria sem rugas ou descamação.
2.5 Máquina de pré-solda Shell
1) Função principal do equipamento
O layout da máquina de pré-solda de concha é mostrado no diagrama.
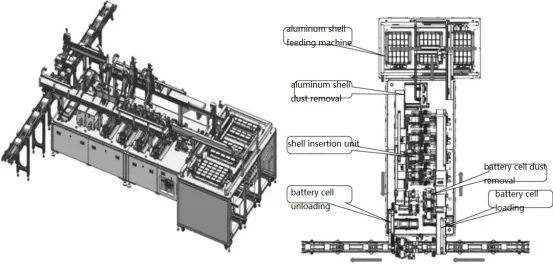
O equipamento da máquina de pré-soldagem de inserção de caixa é usado para inserir automaticamente baterias prismáticas de caixa de alumínio na caixa. A função principal
Os números do equipamento incluem: carregamento de caixa de alumínio, carregamento automático de bateria e varredura de código, remoção de poeira de caixa de alumínio e núcleo de bateria, inserção de núcleo de bateria, descarga de bateria, ligação e upload de informações (MES), etc.
Principais parâmetros técnicos do equipamento.
Dimensões totais do equipamento: 2850mm×1900mm×2500mm.
Taxa de rendimento do equipamento: ≥99,8% (refere-se apenas a defeitos causados pelo equipamento).
Taxa de disponibilidade dos equipamentos: ≥99% (refere-se apenas a falhas causadas por equipamentos).
Intervalo de tempo de carregamento do invólucro de alumínio: ≥25min; Os parâmetros de remoção de poeira são registrados automaticamente e o núcleo da bateria e o invólucro de alumínio não serão danificados durante o processo de remoção de poeira. Nenhuma partícula visível que possa ser apagada.
Para controlar a espessura da célula, a força de fixação precisa ser aumentada: 10 ~ 50kgf (1kgf = 9,81N) é ajustável, a precisão de depuração é de ±5kgf e a pressão de fixação e o valor do vácuo são ajustáveis digitalmente.
Precisão do controle de empuxo durante o processo de revestimento: ±5% do valor de ajuste; O invólucro e as células da bateria são posicionados duas vezes antes de serem inseridos no invólucro e têm a função de expandir a abertura do invólucro. O núcleo da bateria adota um mecanismo de guia totalmente envolvente para guiar o núcleo da bateria para dentro da caixa. A boca da concha de alumínio não pode ser tocada.
Desvio de posicionamento: 0,5 mm.
Repetibilidade de operação do mecanismo: desvio ≤±0,05 mm.
2)Estruturas-chave
A partir do diagrama de layout do equipamento da máquina de pré-solda de invólucro mostrado acima, várias estruturas-chave podem ser identificadas, incluindo o mecanismo de alimentação de invólucro de alumínio, invólucro de alumínio e célula de bateria, mecanismo de limpeza da tampa superior, mecanismo de inserção de célula de bateria e mecanismo de alimentação de célula de bateria. Essas estruturas desempenham um papel crítico na montagem do produto final. Vamos fornecer explicações detalhadas para alguns mecanismos selecionados.
(1) Módulo de alimentação de casca de alumínio (conforme mostrado no diagrama)
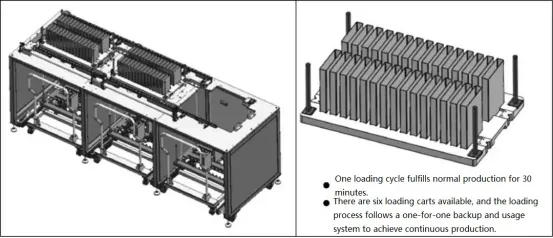
um. Função: realiza a alimentação de conchas de alumínio e possui funções como posicionamento e transferência de paletes.
b. Componentes principais: empilhamento de palete de alumínio, dispositivo de carregamento automático, palete de alumínio, carrinho de transporte de material, etc.
c. Requisitos: O intervalo de alimentação do invólucro de alumínio é ≥ 20 minutos; equipado com mecanismo de guia confiável e mecanismo de posicionamento.
(2)Mecanismo de remoção de poeira do núcleo da bateria e da caixa (conforme mostrado na figura).
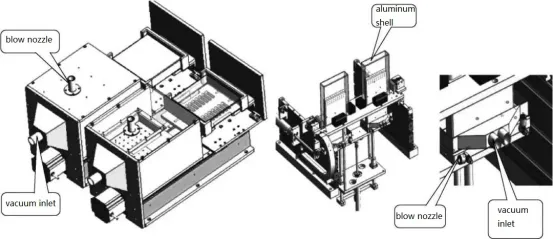
a. Função: O invólucro é limpo verticalmente e o processo de sopro cobre todos os ângulos sem pontos cegos óbvios. A abertura da concha é tratada especificamente.
b. Componentes principais: Mecanismo de remoção de poeira, mecanismo de translação do cilindro, etc.
3. Mecanismo de inserção da célula da bateria (conforme mostrado no diagrama).
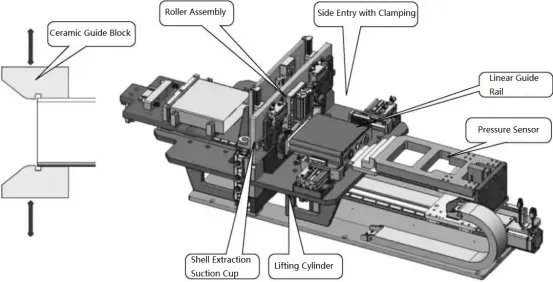
a. Durante a inserção do invólucro, o invólucro de alumínio é fixado e a célula da bateria é presa e empurrada para frente para proteger as abas da célula.
b. O processo de inserção do invólucro utiliza blocos-guia de cerâmica com um grande ângulo de inclinação para evitar a raspagem do invólucro de alumínio, bem como danos ou arranhões no separador.
c. Os materiais cerâmicos são usados na área de contato com o invólucro de alumínio.
d. Após a inserção, uma folga de 4 mm é mantida para a estação de prensagem subsequente, exigindo que o suporte entre na casca e garanta uma profundidade consistente de inserção da casca.
e. Precisão de posicionamento: Com uma estrutura de extração de concha de ventosa, a concha é posicionada firmemente, alcançando uma precisão de posicionamento de ±0,1 mm. Todo o processo de inserção do invólucro é monitorado quanto à pressão e um peso padrão é fornecido para calibração sem desmontar o sensor.
f. O mecanismo de limpeza limpa a superfície de soldagem da célula da bateria e da tampa do invólucro soprando pelos lados superiores e sucção pela parte inferior.
g. O ângulo e a altura de sopro do bico podem ser ajustados livremente, garantindo um fluxo de ar uniforme e formando uma cortina de ar eficaz.
h. Prensagem da tampa: Usado principalmente para testes de alta potência da célula da bateria após a inserção. Antes de pressionar, a poeira ao redor da placa de cobertura é removida e a placa de cobertura é pressionada contra o invólucro.
i. Função: Para inserir a célula da bateria no invólucro.
j. Componentes principais: Mecanismo de inserção de concha, conjunto de fuso, mecanismo de sucção de extração de concha, etc.
4. Mecanismo de alimentação da célula da bateria (conforme mostrado no diagrama).
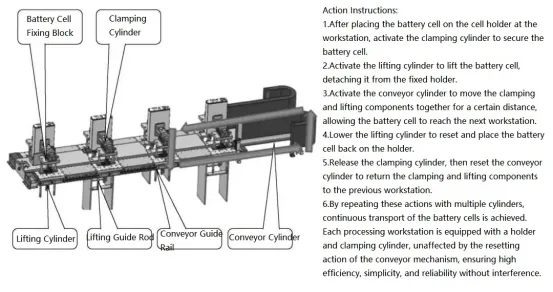
a. Função: Usado para transportar células de bateria após a inserção no invólucro.
b. Componentes principais: Mecanismo de fixação da célula da bateria, cilindro de elevação, mecanismo de transporte, etc.
2.6 Máquina de pré-solda
1. Principais funções do equipamento
O layout da máquina de pré-soldagem é mostrado no diagrama.
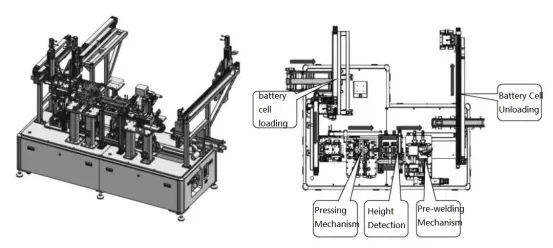
O layout do equipamento da máquina de pré-soldagem é usado para pré-soldar o invólucro de alumínio prismático e a placa de cobertura. As principais funções do equipamento incluem alimentação e digitalização automática da bateria, prensagem, detecção de altura, soldagem a laser, descarga da bateria e vinculação/upload de informações para o MES (Manufacturing Execution System).
(1) Principais parâmetros técnicos do equipamento:
Dimensões totais: 3000 mm × 1800 mm × 2500 mm.
Rendimento do equipamento: ≥99,8% (referente a defeitos causados unicamente por motivos do equipamento).
Taxa de utilização do equipamento: ≥99% (referente a falha do equipamento causada exclusivamente por motivos do equipamento).
Teste de alta potência: Tempo de teste variando de 0,5s a 5s, ajustável na faixa de 1s a 100s. A marca utilizada é a Hioki com uma precisão de ±5%. A tensão de teste (DC) entre os terminais positivo e negativo é de 100V, com uma faixa (DC) de incrementos de 0V a 500V e 50V.
Desvio de posicionamento: 0,5 mm.
Repetibilidade da operação do mecanismo: Desvio ≤±0,05 mm.
2) Estruturas-chave
A partir do diagrama de layout do equipamento da máquina de pré-soldagem, pode-se ver que o mecanismo de modelagem e pré-prensagem da célula da bateria, o módulo de teste de passo e curto-circuito, o mecanismo de prensagem, o mecanismo de pré-soldagem, bem como a vedação da tampa e o mecanismo de prensagem são críticos e desempenham um papel crucial na montagem do produto semi-acabado. Vamos fornecer explicações detalhadas para alguns desses mecanismos.
(1) Mecanismo de modelagem e pré-prensagem da célula da bateria (2 conjuntos, conforme mostrado na figura)
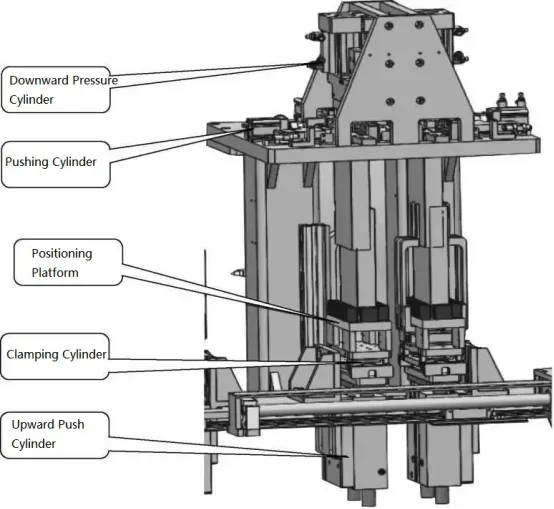
a. Função: Para moldar e pressionar a tampa superior da célula da bateria depois de inserida na caixa.
b. Componentes principais: Componentes de posicionamento, montagem de elevação e pré-prensagem, etc.
c. Requisitos: Deve ser capaz de predefinir o limite superior de pressão, fornecer uma função de alarme e parada quando o limite for excedido para evitar danos à célula da bateria e ao invólucro. A faixa de ajuste de pressão deve ser de 200 a 1000N. Após a prensagem, a tampa superior não deve apresentar danos ou detritos e não deve haver rebarbas, rebarbas ou arranhões ao redor da abertura da caixa. O módulo de prensagem deve ser projetado com modularidade para troca fácil e conveniente.
(2) Mecanismo de vedação e prensagem da tampa (conforme mostrado na figura)
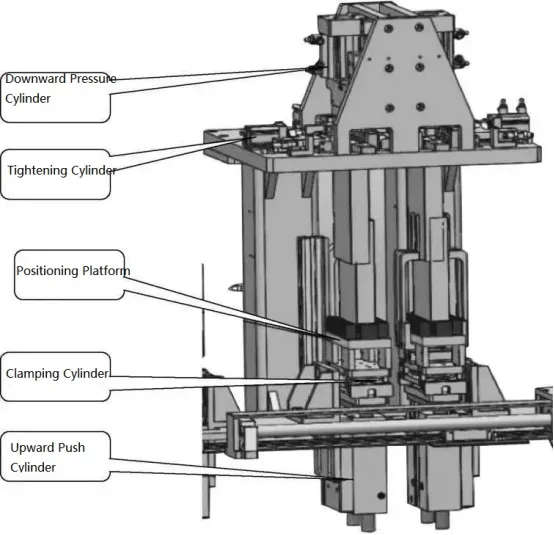
A sequência operacional específica do mecanismo de vedação e prensagem da tampa é a seguinte:
a. ClampAção do cilindro: Clamps a célula da bateria enquanto o cilindro de empurrar para cima levanta a célula para a posição de montagem.
b. Ação do cilindro de centralização: Clamps a célula da bateria, alinha-a na posição correta e libera o clampcilindro.
c. Ação do cilindro de aperto: Fixa o invólucro e a placa de cobertura dentro do molde de prensagem, garantindo que o degrau esteja dentro de 0,20 mm. O molde tem dimensões precisas, alta suavidade, permitindo o movimento suave da concha e da placa de cobertura no interior.
d. Ação do conjunto da ventosa: Segura o invólucro e puxa-o para fora para evitar deformações internas significativas.
e. Ação do cilindro de pressão para baixo: Guiado pelo molde de pressão, pressiona a placa de cobertura no invólucro, enquanto incorpora limitadores mecânicos para evitar pressão excessiva.
f. Cada cilindro tem comprimento de curso ajustável e as peças-chave são equipadas com almofadas hidráulicas e limitadores de ajuste fino.
(3) Mecanismo de pré-soldagem (conforme mostrado na figura)
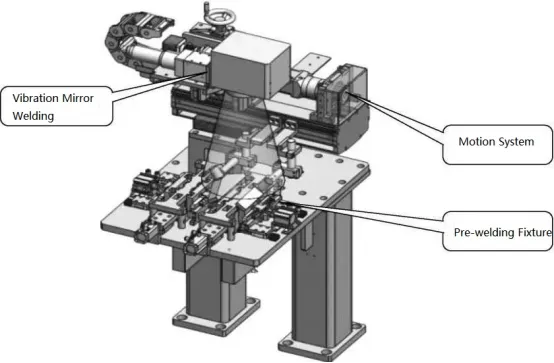
O "mecanismo de pré-soldagem" é composto principalmente por um sistema de movimento e um dispositivo de pré-soldagem.
a. Função: Foco a laser, medição de desfoque, proteção de gás de soldagem e o sistema de movimento arrasta a cabeça do laser para escanear o caminho de soldagem.
b. Componentes principais: Os eixos X e Y do sistema de movimento adotam servomotores, máquinas de solda a laser, etc. O sensor de detecção de passos usa um perfilômetro 2D, com uma precisão de detecção de passos de ±0,02 mm e passos inferiores a 0,2 mm.
2.7 Máquina de solda a laser de tampa superior
1) Principais funções do equipamento
O layout da máquina de solda a laser da tampa superior é mostrado na figura abaixo. Este equipamento é usado principalmente para soldagem a laser da tampa superior da célula da bateria após a pré-soldagem e para testes de alta potência. Suas principais funções incluem leitura automática de código de barras para carga e descarga de células, manuseio automático de placas de proteção
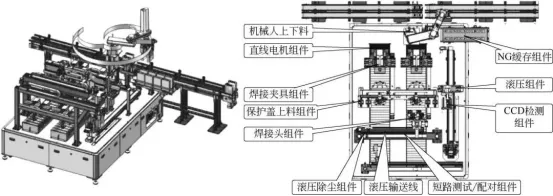
Dimensões totais do equipamento: 3000mm×4500mm×2200mm.
A taxa de rendimento inicial do equipamento é de ≥98,5%, a taxa excelente de segunda vez é de ≥99,5% (excluindo materiais de entrada defeituosos) e a taxa de utilização é de ≥98%.
Velocidade de soldagem ≥150 mm / s, CMK ≥ 1,33.
Força de pressão de soldagem a laser>10kgf, CMK≥1.33.
Potência de saída da máquina de solda a laser e precisão do controle de pressão do acessório: valor definido ±5%, CMK≥1.33.
Qualidade de soldagem (precisão de posicionamento de soldagem ±0,1 mm, desvio de largura de solda ≤±0,1 mm) consistência CMK≥1,33.
A limpeza ambiental da cavidade protetora em contato com o produto durante o processo de soldagem a laser é superior ao requisito de nível 100.000.
As funções do equipamento podem atender às necessidades de organização, comunicação e acoplamento de equipamentos de processo dianteiros e traseiros.
2) Estruturas-chave
A partir do diagrama de layout da máquina de solda a laser de tampa superior, podemos identificar vários componentes críticos, como o mecanismo de alimentação, conjunto de posicionamento, componente de alimentação da tampa protetora, buffer de NG, componente de inspeção móvel, componente de inspeção CCD, componente de manuseio de NG, componente de descarga e componente de cabeça de soldagem. Esses componentes desempenham um papel crucial na montagem do produto semiacabado. Vamos fornecer uma introdução detalhada a alguns mecanismos selecionados.
(1) Mecanismo de alimentação da máquina de solda a laser da tampa superior (conforme mostrado na figura).
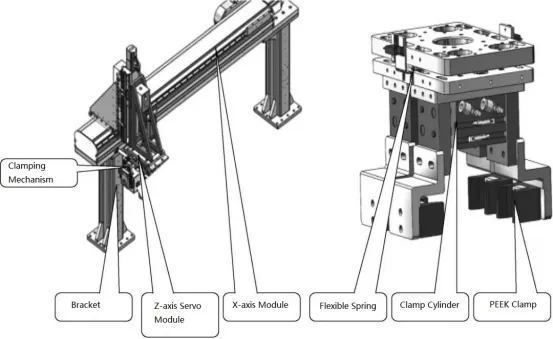
um. O mecanismo de carregamento inclui um suporte de carga, módulo de eixo X, módulo de eixo Z, mecanismo de fixação, etc. Use a braçadeira de carregamento para agarrar os núcleos da bateria na linha de logística de entrada de material. Pegue duas baterias de cada vez e coloque-as no dispositivo de soldagem. Existem 4 conjuntos de acessórios de soldagem. Duas baterias são colocadas de cada vez e as baterias são descarregadas duas vezes.
b. O mecanismo de elevação do manipulador é protegido de forma flexível. Quando encontra resistência antes de atingir a posição definida durante o processo de descida, ele sobe imediatamente e emite um alarme sonoro e visual.
c. O manipulador tem uma função de proteção de energia e gás. Quando a bateria é clamped e a bateria é cortada, a bateria não cairá por pelo menos 30 minutos.
d. Posicione e clamp o núcleo da bateria para que sua posição seja precisa e confiável durante a soldagem. O bloco de fixação é feito de materiais resistentes a altas temperaturas. A precisão de posicionamento da soldagem é de ±0,1 mm e o desvio da largura da solda é de ≤±0,1 mm.
e. A direção da altura do núcleo da bateria é posicionada com base na superfície superior da tampa superior. Depois que o núcleo da bateria é posicionado e fixado, a altura da superfície superior da tampa superior do núcleo da bateria excede a superfície superior do bloco de fixação em 1,5 ~ 2 mm (determinado pelo cliente). O erro de nível de superfície superior é de ≤0,1 mm, o erro de repetibilidade na direção da altura é de ≤0,05 mm.
f. Durante o processo de posicionamento e fixação do núcleo da bateria, o bloco de fixação não produz atrito deslizante com o núcleo da bateria. Um dispositivo seguidor é usado para evitar beliscar ou arranhar o núcleo da bateria. Depois que o núcleo da bateria é posicionado e preso, a folga entre o bloco de fixação e o núcleo da bateria é de ≤0,05 mm (peça padrão).
g. A pressão do cilindro de posicionamento e fixação da célula é ajustável e o valor da pressão do ar flutua <0,05 MPa.
(2) Componente de posicionamento superior (como mostrado na figura).
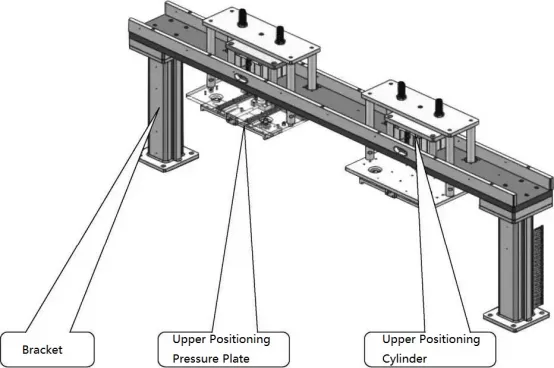
O processo de ação específico é o seguinte:
um. A braçadeira da bateria se move para a posição de posicionamento superior através do motor linear A/B.
b. Controle a válvula solenóide do cilindro de posicionamento lateral longo e curto da braçadeira da bateria para mudar para a posição de descarga média.
c. O cilindro móvel de posicionamento superior aciona a placa de pressão de posicionamento superior para pressionar para baixo para posicionar a bateria.
d. Após a conclusão do posicionamento superior, as válvulas solenóides laterais longas e curtas mudam para a pressão normal e o cilindro móvel de posicionamento superior sobe.
(3) Conjunto de carregamento da tampa protetora (conforme mostrado na imagem).
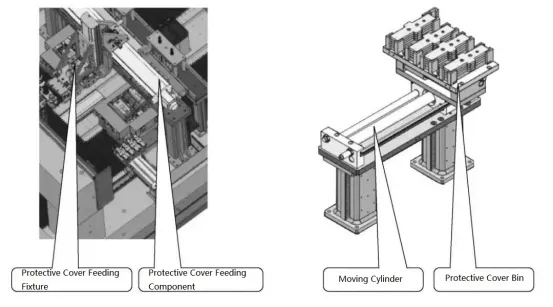
As etapas de ação específicas são as seguintes:
um. Após a conclusão do posicionamento superior, a bateria é movida para a posição superior da tampa protetora para alimentação da tampa protetora.
b. Após a conclusão da soldagem, o sistema se move para a posição de descarga para remover a tampa protetora e descarregar a bateria.
Nota: A tampa protetora pode ser substituída sem parar a máquina. A tampa protetora é usada para proteger a coluna do eletrodo, evitando a contaminação da coluna do eletrodo, código QR, filme à prova de explosão e orifício de injeção de respingos de soldagem.
(4) Componente de inspeção CCD (conforme mostrado na figura).
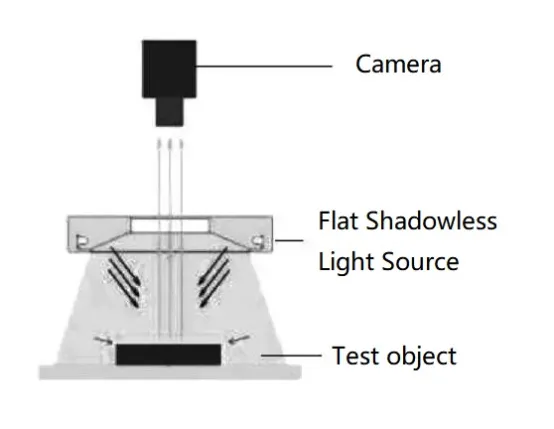
Após a soldagem, as células da bateria são transportadas para o componente de inspeção móvel usando o módulo de braço robótico. O componente de inspeção móvel é equipado com dois conjuntos de grampos e possui três estações: posição de alimentação, posição de inspeção e posição de descarga. O componente de inspeção CCD é equipado com uma câmera para detectar defeitos como poços, espiráculos, descontinuidades de solda, porosidade e solda incompleta no cordão de solda (como mostrado na figura).
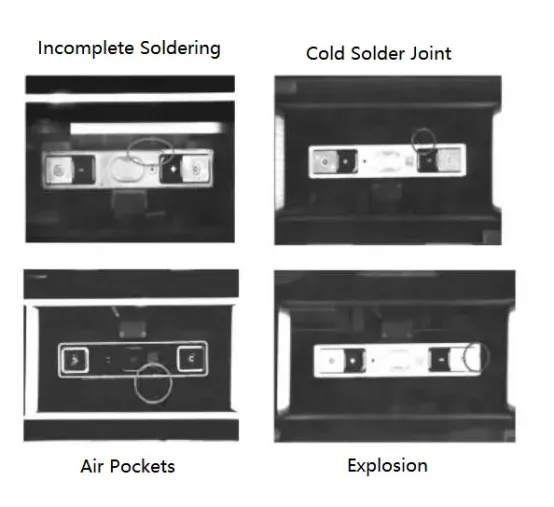
2.8 Testador de vazamento de hélio de pressão positiva
1. Principais funções do equipamento
O diagrama de layout mostrado abaixo mostra o equipamento de teste de vazamento de hélio de pressão positiva. Este equipamento é usado principalmente para testar o desempenho de vedação de células de bateria prismáticas de alumínio após a soldagem a laser da tampa superior. Ele emprega um método de vácuo para detectar o estado de vedação da tampa superior após a soldagem. O processo de trabalho é o seguinte: Depois que a tampa superior é soldada a laser, as células da bateria testadas são alimentadas na máquina por meio de um transportador de alimentação e o código QR da tampa superior é lido. O braço robótico de classificação coloca as células de bateria testadas na câmara de teste. A câmara é evacuada até que o valor de pressão negativa definido seja atingido e, em seguida, a fonte de vácuo externa é fechada. O testador de estanqueidade ao gás é usado para testar a estanqueidade interna ao gás da célula da bateria. Este dispositivo ajuda a determinar se as peças testadas são qualificadas.
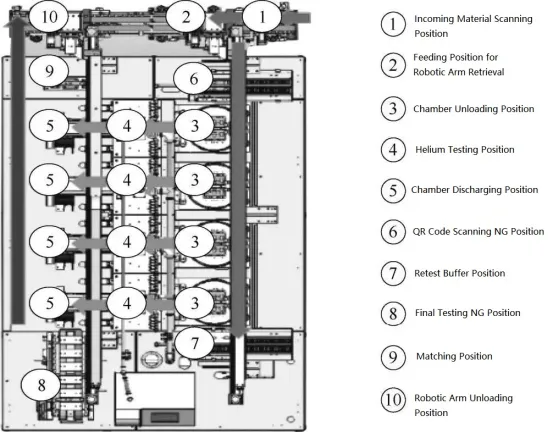
O sistema é projetado e fabricado em estrita conformidade com os requisitos do comprador, usando um design modular, considerando totalmente os requisitos de detecção de vazamentos do comprador e usando módulos e componentes padronizados tanto quanto possível para garantir a confiabilidade e manutenção do sistema e atender aos requisitos do fabricante. Especifique indicadores técnicos.
Os indicadores básicos do equipamento são os seguintes:
Taxa de rendimento do equipamento: ≥99,8% (exceto para materiais de entrada defeituosos).
Taxa de utilização do equipamento: ≥99%; Taxa de detecção falsa: ≤0,3%.
Padrão de inspeção de hélio: ≤9,9×10-7Pa·m3/s.
2) Estrutura chave
Este equipamento consiste nos seguintes dispositivos: dispositivo manipulador de entrada/saída da peça de trabalho, corrediça da caixa, dispositivo de evacuação/enchimento de hélio, dispositivo de detecção de vazamento da caixa de vácuo, dispositivo de enchimento e remoção de hélio e dispositivo de controle elétrico. Pode-se ver no diagrama de layout do equipamento de inspeção de hélio de pressão positiva na Figura 48 que o dispositivo manipulador de entrada/saída da peça, o dispositivo de evacuação/enchimento de hélio, etc. são críticos e desempenham um papel vital em todo o produto semiacabado montado. Vários desses mecanismos são selecionados para detalhes. Introdução.
(1) Verifique o prato giratório. A principal função da plataforma giratória de detecção é carregar e descarregar baterias e detectá-las ao mesmo tempo, maximizando a eficácia e eficiência do detector de estanqueidade. O módulo é composto principalmente por uma plataforma giratória, um divisor de cames e um dispositivo de detecção, conforme mostrado na figura.
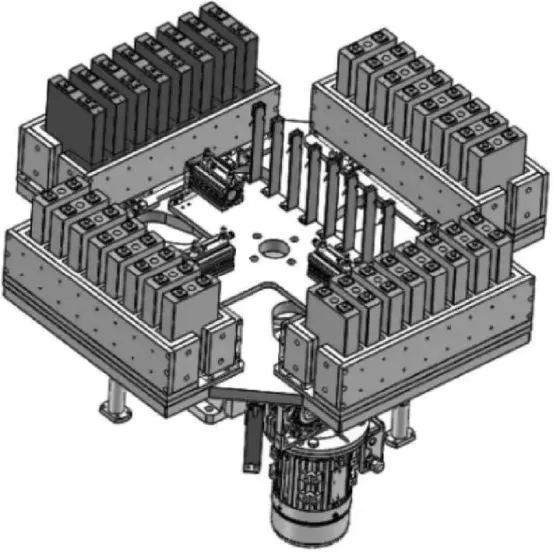
(2)Mecanismo de bombeamento de vácuo (como mostrado abaixo). As peças de evacuação e enchimento de hélio são compostas principalmente por bombas de vácuo, válvulas solenóides, sensores de pressão e tubulações. A peça de trabalho pode ser evacuada e preenchida com hélio dentro de um tempo definido.
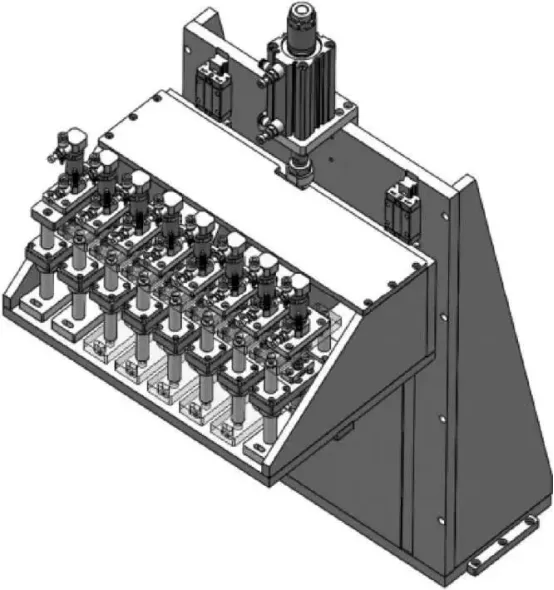
um. A pressão de enchimento de hélio (pressão absoluta) é de 0,05 ~ 0,15 MPa, que é ajustável dentro dessa faixa.
b. O sistema possui funções de monitoramento de pressão e concentração de hélio e reabastecimento automático de hélio. Quando o sistema detecta que a concentração ou pressão de hélio é inferior ao valor definido, ele abre automaticamente a válvula para reabastecer o hélio de alta pureza.
c. Sistema de recuperação: marca de bomba de vácuo, Leybold; quantidade, 1 bomba de vácuo, SV16B; 1 bomba de recuperação (bomba seca), Leybold.
d. Medidor de concentração de hélio: O padrão de concentração pode ser definido.
e. A taxa de recuperação do sistema de recuperação é de >80%.
f. A função de limpeza automática de hélio está intacta e pode eliminar de forma rápida e eficaz o hélio residual na caixa e nos tubos. A precisão e a repetibilidade da detecção de vazamentos são confiáveis. A Parte B fornecerá orifícios de vazamento padrão.
03 Seleção de equipamentos e casos de aplicação
Um cliente tem os seguintes requisitos para o tamanho da célula da bateria.
(1) Os clientes fornecem informações técnicas. A planta baixa do modelo do equipamento é mostrada na figura, e seu codinome e dimensões são mostrados na tabela.
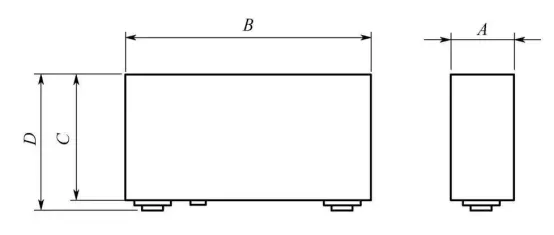

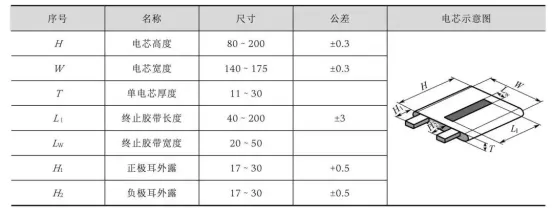
De acordo com as necessidades do cliente, as especificações da célula são fixadas ajustando a mão de fixação compartilhada. Se necessário, as almofadas necessárias podem ser substituídas para alcançar a produção de células de diferentes especificações (como gabaritos, acessórios, bandejas). Especificações do tamanho da célula A faixa de variação não deve exceder a faixa de tamanho máximo do dispositivo.
Esta linha de produção automática é usada para realizar a montagem automática de células de bateria de íon de lítio de invólucro de alumínio prismático após o enrolamento. A linha de produção consiste principalmente nas seguintes peças: máquina de prensagem a quente, máquina de solda ultrassônica, máquina de solda a laser de placa adaptadora e máquina de embalagem. , máquina de descascamento, máquina de solda pré-ponto, máquina de solda a laser de tampa superior e linhas de transmissão logística entre vários equipamentos, etc.