O revestimento da folha de eletrodo geralmente se refere ao processo de aplicação uniforme de uma pasta bem misturada em um coletor de corrente e secagem dos solventes orgânicos presentes na pasta. A qualidade do revestimento tem um impacto significativo na capacidade da bateria, resistência interna, ciclo de vida e segurança. Garantir o revestimento uniforme da folha do eletrodo é crucial. Os parâmetros de seleção e controle do método de revestimento desempenham um papel importante no desempenho das baterias de íons de lítio. Isso se reflete principalmente nos seguintes aspectos:
1)RevestimentoControle de temperatura de secagem: Se a temperatura de secagem for muito baixa durante o revestimento (máquina relacionada), não se pode garantir que a folha do eletrodo esteja completamente seca. Se a temperatura for muito alta, o solvente orgânico dentro da folha do eletrodo pode evaporar muito rapidamente, fazendo com que as tartarugas apareçam no revestimento da superfície da folha do eletrodo, rachaduras, quedas, etc.;
2)Densidade da superfície do revestimento: Se a densidade da superfície do revestimento for muito pequena, a capacidade da bateria pode não atingir a capacidade nominal. Se a densidade da superfície do revestimento for muito alta, isso causará facilmente um desperdício de ingredientes. Em casos graves, se houver capacidade excessiva de eletrodo positivo, devido ao lítio A precipitação forma dendritos de lítio que perfuram o separador da bateria e causam um curto-circuito, causando riscos à segurança;
3)Tamanho do revestimento: Se o tamanho do revestimento for muito pequeno ou muito grande, o eletrodo positivo dentro da bateria pode não ser completamente coberto pelo eletrodo negativo. Durante o processo de carregamento, os íons de lítio são incorporados a partir do eletrodo positivo e se movem para o eletrólito que não está completamente coberto pelo eletrodo negativo. Médio, a capacidade real da folha de eletrodo positivo não pode ser usada de forma eficiente. Em casos graves, dendritos de lítio se formarão dentro da bateria, o que pode facilmente perfurar o separador e causar o circuito interno da bateria;
4)Espessura do revestimento: A espessura do revestimento muito fina ou muito espessa terá um impacto no processo subsequente de laminação da folha de eletrodo e não pode garantir a consistência do desempenho da folha de eletrodo da bateria.
Além disso, o revestimento das folhas de eletrodo é de grande importância para a segurança da bateria. Antes do revestimento, o trabalho 5S deve ser feito para garantir que nenhuma partícula, detritos, poeira, etc. sejam misturados nas folhas de eletrodo durante o processo de revestimento. Se os detritos forem misturados, isso causará um microcurto-circuito dentro da bateria e, em casos graves, a bateria pode pegar fogo e explodir.
1. Seleção de equipamentos e processos de revestimento
O processo de revestimento generalizado inclui: desenrolamento → emenda → puxar → controle de tensão → revestimento → secagem → correção de alinhamento → controle de tensão → correção de desvio → enrolamento e outros processos. O processo de revestimento é complexo e há muitos fatores que afetam o efeito do revestimento, como: a precisão de fabricação do equipamento de revestimento, a suavidade da operação do equipamento, o controle da tensão dinâmica durante o processo de revestimento, a quantidade de volume de ar durante o processo de secagem e as curvas de controle de temperatura afetarão o efeito do revestimento, por isso é extremamente importante escolher o processo de revestimento adequado.
Geralmente, os seguintes aspectos precisam ser considerados ao selecionar um método de revestimento, incluindo: o número de camadas de revestimento, a espessura do revestimento úmido, as características reológicas do líquido de revestimento, a precisão necessária do revestimento, o suporte ou substrato do revestimento e a velocidade do tecido, etc.
Além dos fatores acima, as condições e características específicas do revestimento da folha de eletrodo também devem ser combinadas. As características do revestimento das folhas de eletrodo de bateria de íons de lítio são: (1) Revestimento de camada única de dupla face; (2) O revestimento úmido da pasta é espesso (100 ~ 300μm); (3) A pasta é um fluido de alta viscosidade não newtoniano; (4) Os requisitos de precisão do revestimento das folhas de eletrodo são altos, semelhantes à precisão do revestimento do filme; (5) O suporte do revestimento é folha de alumínio e folha de cobre com espessura de 10 a 20 μm; (6) Em comparação com a velocidade de revestimento do filme, a velocidade do revestimento das folhas de eletrodo não é alta. Considerando os fatores acima, o equipamento geral de laboratório geralmente usa o tipo raspador, as baterias de íon de lítio de consumo usam principalmente o tipo de transferência de revestimento de rolo e as baterias de energia usam principalmente o método de extrusão de fenda.
Srevestimento de craper: O princípio de funcionamento é mostrado na Figura 1. O substrato de folha passa pelo rolo de revestimento e está em contato direto com a calha de lama. A pasta excessiva é aplicada ao substrato da folha. Quando o substrato passa entre o rolo de revestimento e o raspador, a folga entre o raspador e o substrato determina a espessura do revestimento e, ao mesmo tempo, o excesso de lama é raspado e refluído, formando assim um revestimento uniforme na superfície do substrato. Tipo raspador raspador de vírgula principal. O raspador de vírgula é um dos principais componentes do cabeçote de revestimento. Geralmente é processado em uma aresta de corte semelhante a uma vírgula na superfície do rolo redondo ao longo da linha de ônibus. Este raspador tem alta resistência e dureza, e é fácil de controlar a quantidade de revestimento e a precisão do revestimento. É adequado para pasta de alto teor de sólidos e alta viscosidade.
Tipo de transferência de revestimento de rolo: A rotação do rolo de revestimento aciona a pasta, a quantidade de transferência de polpa é ajustada através da abertura do raspador de vírgula e a rotação do rolo traseiro e do rolo de revestimento é usada para transferir a pasta para o substrato. O processo é mostrado na Figura 2. O revestimento de transferência de rolo consiste em dois processos básicos: (1) A rotação do rolo de revestimento aciona a pasta através da folga do rolo de medição para formar uma camada de pasta de uma certa espessura; (2) A camada de lama de uma certa espessura passa pela direção oposta do rolo de revestimento e a rotação do rolo de apoio transfere a lama para a folha para formar um revestimento.
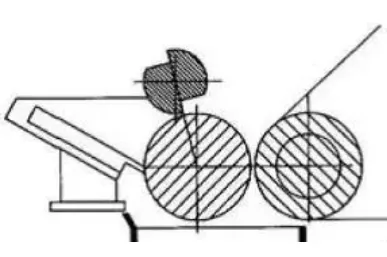
Diagrama esquemático do processo de revestimento de transferência de lâmina de revestimento de rolo
Revestimento de matriz de ranhura: Como uma técnica precisa de revestimento úmido, o revestimento de matriz de ranhura opera conforme mostrado na Figura 3. O princípio de funcionamento envolve a extrusão do líquido de revestimento através da abertura de uma matriz de ranhura a uma pressão e vazão específicas, transferindo-o para o substrato. Comparado a outros métodos de revestimento, o revestimento de matriz de ranhura oferece várias vantagens, como alta velocidade de revestimento, alta precisão e espessura úmida uniforme. O sistema de revestimento é fechado, evitando a entrada de contaminantes durante o processo de revestimento, resultando em alta utilização da pasta e mantendo propriedades estáveis da pasta. Permite o revestimento simultâneo de várias camadas. Além disso, o revestimento de matriz de ranhura pode acomodar uma ampla gama de viscosidades de pasta e conteúdo sólido, tornando-o mais adaptável em comparação com os processos de revestimento de transferência.
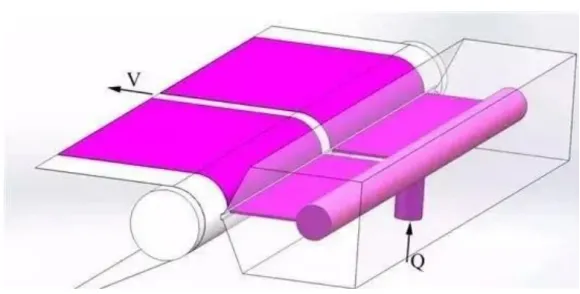
2. Defeitos de revestimento e fatores de influência
Reduzir defeitos de revestimento, melhorar a qualidade e o rendimento do revestimento e reduzir os custos são aspectos importantes a serem considerados no estudo dos processos de revestimento. Problemas comuns que geralmente ocorrem durante o processo de revestimento incluem cabeça grossa, cauda grossa, bordas grossas em ambos os lados, defeitos de manchas, rugosidade da superfície e exposição da folha.
A espessura da cabeça e da cauda pode ser ajustada controlando o tempo de abertura e fechamento da válvula de revestimento ou válvula intermitente. O problema das bordas grossas pode ser melhorado ajustando as propriedades da pasta, a folga do revestimento e a taxa de fluxo da pasta. A rugosidade da superfície, irregularidades e listras podem ser resolvidas estabilizando o material da folha, reduzindo a velocidade e ajustando o ângulo da faca de ar.
Pasta de material de base
A relação entre as propriedades físicas básicas da pasta e do revestimento: No processo real, a viscosidade da pasta tem um certo impacto no efeito do revestimento. As matérias-primas do eletrodo, as proporções da pasta e a viscosidade da pasta preparada também variam quando o tipo de aglutinante é selecionado. diferente. Quando a viscosidade da pasta é muito alta, o revestimento geralmente não pode ser realizado de forma contínua e estável, e o efeito do revestimento também é afetado.
A uniformidade, estabilidade, efeitos de borda e superfície do fluido de revestimento são afetados pelas propriedades reológicas do fluido de revestimento, que determinam diretamente a qualidade do revestimento. Métodos de pesquisa, como análise teórica, tecnologia experimental de revestimento e tecnologia de elementos finitos de mecânica dos fluidos, podem ser usados para estudar a janela de revestimento. A janela de revestimento é a faixa de operação do processo na qual o revestimento estável pode ser alcançado e um revestimento uniforme pode ser obtido.
Substrato - folha de cobre e folha de alumínio
Tensão superficial: A tensão superficial da folha de alumínio e cobre deve ser maior que a tensão superficial da solução revestida, caso contrário, a solução será difícil de espalhar suavemente no substrato, resultando em má qualidade do revestimento. Um princípio que precisa ser seguido é que a tensão superficial da solução a ser revestida deve ser 5 dinas/cm menor que a do substrato. Claro, isso é apenas áspero. A tensão superficial da solução e do substrato pode ser ajustada ajustando a fórmula ou o tratamento de superfície do substrato. A medição da tensão superficial de ambos também deve ser usada como um item de teste de controle de qualidade.
Espessura uniforme: Em um processo semelhante ao revestimento da lâmina, a espessura do substrato é irregular em toda a largura, o que levará a uma espessura de revestimento irregular. Porque no processo de revestimento, a espessura do revestimento é controlada pela folga entre o raspador e o substrato. Se houver um local onde a espessura do substrato seja relativamente baixa na direção transversal do substrato, mais solução passará por esse local e a espessura do revestimento será mais espessa e vice-versa. Se as seguintes flutuações de espessura do material de base forem vistas no medidor de espessura, as flutuações finais da espessura do revestimento também mostrarão o mesmo desvio. Além disso, desvios transversais de espessura também podem levar a defeitos de enrolamento. Portanto, para evitar esse defeito, o controle de espessura das matérias-primas é muito importante.
Eletricidade estática: Na linha de revestimento, muita eletricidade estática será gerada na superfície do substrato quando o revestimento estiver se desenrolando e passando pelo rolo. A eletricidade estática gerada pode absorver facilmente o ar e a camada de cinzas no rolo, causando defeitos no revestimento. Durante o processo de descarga de eletricidade estática, também causará defeitos de aparência estáticos na superfície do revestimento, e casos mais graves podem até causar incêndios. Se a umidade for baixa no inverno, o problema de eletricidade estática na linha de revestimento será mais sério. A maneira mais eficaz de reduzir esses defeitos é manter a umidade ambiente o mais alta possível, aterrar as linhas de revestimento e instalar alguns dispositivos antiestáticos.
Limpeza: Impurezas na superfície do substrato causarão alguns defeitos físicos, como saliências, sujeira, etc. Portanto, é necessário controlar melhor a limpeza das matérias-primas no processo de produção de materiais de base. Os rolos de limpeza de filme online são um método mais eficaz de remover as impurezas do substrato. Embora não possa remover todas as impurezas da membrana, pode efetivamente melhorar a qualidade das matérias-primas e reduzir as perdas.
3. Mapa de defeitos da folha de eletrodo de bateria de lítio
- Defeitos de bolha no revestimento do eletrodo negativo da bateria de íons de lítio
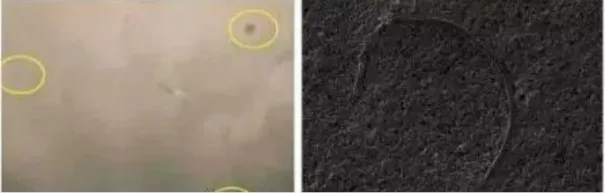
A imagem da esquerda é a placa de eletrodo negativo com bolhas, e a imagem da direita é uma ampliação de 200x do microscópio eletrônico de varredura. Durante os processos de mistura, transferência e revestimento da pasta, materiais estranhos, como poeira ou fiapos longos, são misturados ao líquido do revestimento ou caem na superfície do revestimento úmido, onde a tensão superficial do revestimento é afetada por forças externas, resultando em forças intermoleculares. Ocorrem mudanças, a pasta é ligeiramente transferida e, após a secagem, traços circulares são formados com um meio fino.
- Pinhole
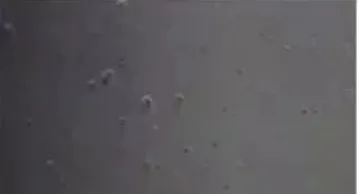
Uma é a geração de bolhas (processo de agitação, processo de transporte, processo de revestimento); Os defeitos de orifício causados por bolhas são relativamente fáceis de entender. As bolhas no filme úmido migram da camada interna para a superfície do filme e estouram na superfície do filme para formar defeitos de orifício. As bolhas vêm principalmente da baixa fluidez e nivelamento da tinta durante a agitação, transporte de líquido de revestimento e processos de revestimento, e baixa liberação de bolhas da tinta.
- Arranhões
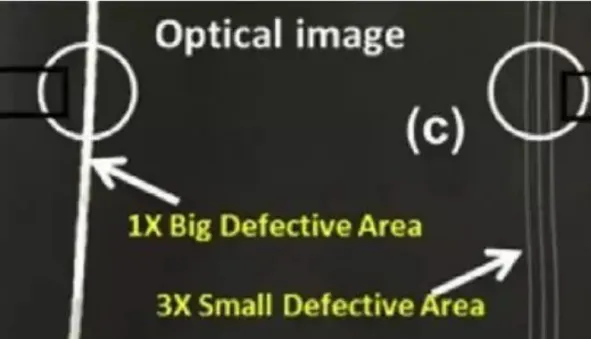
- Bordas grossas
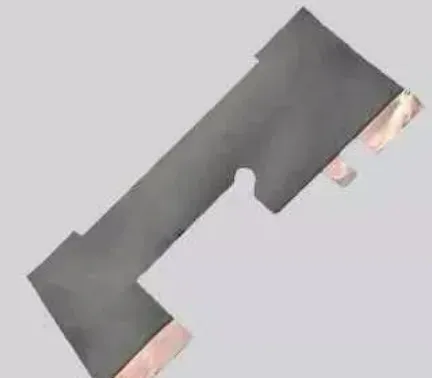
A razão para a borda grossa é que a tensão superficial da pasta faz com que a pasta migre para a área não revestida na borda da folha do eletrodo, formando uma borda espessa após a secagem.
- Partículas agregadas superficiais negativas
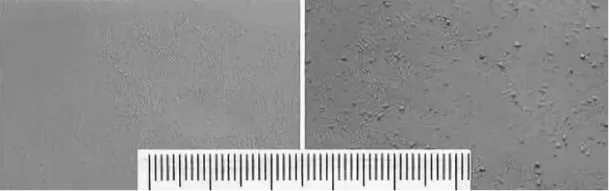
Formulação: Grafite esférica + SUPER C65 + CMC + Água destilada
Aparência macroscópica de dois filmes de eletrodos diferentes usando diferentes processos de mistura: superfície lisa (esquerda) e superfície com numerosas partículas pequenas (direita).
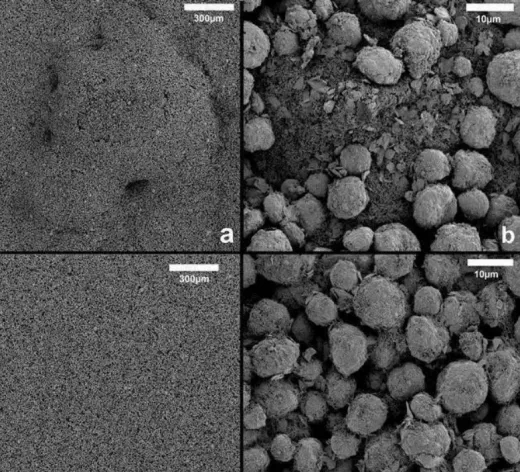
Formulação: Grafite esférica + SUPER C65 + CMC/SBR + Água destilada
Morfologia ampliada da superfície do filme do eletrodo com pequenas partículas (a e b): Agregação de aditivos condutores, dispersão incompleta.
Morfologia ampliada do filme de eletrodo de superfície lisa: Os aditivos condutores são bem dispersos e distribuídos uniformemente.
- Partículas agregadas da superfície do eletrodo positivo
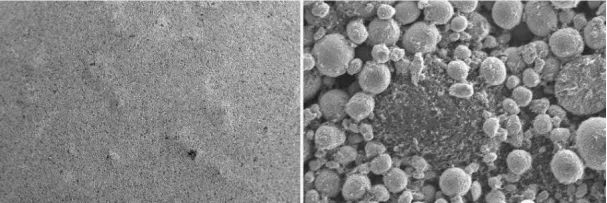
Formulação: NCA + acetileno preto + PVDF + NMP
Durante o processo de agitação, a umidade ambiente era muito alta, fazendo com que a pasta ficasse em estado gelatinoso, o agente condutor não estava completamente disperso e havia um grande número de partículas na superfície da folha do eletrodo após a laminação.
- Rachaduras na folha do eletrodo do sistema de água
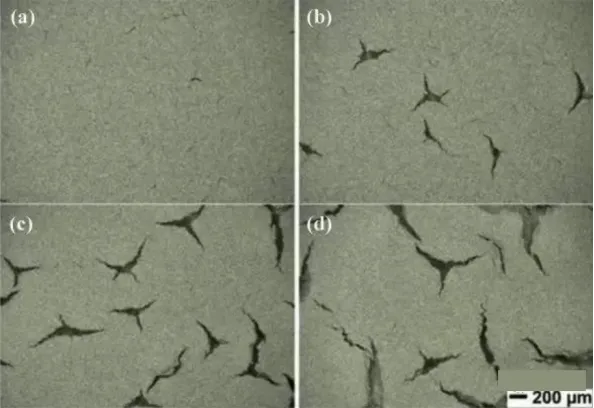
Formulação: NMC532/negro de fumo/aglutinante = 90/5/5% em peso, solvente de água/álcool isopropílico (IPA).
Fotografias ópticas de rachaduras na superfície do filme do eletrodo em diferentes densidades de área de revestimento: (a) 15 mg / cm2, (b) 17,5 mg / cm2, (c) 20 mg / cm2 e (d) 25 mg / cm2. Filmes de eletrodos mais espessos são mais propensos a rachaduras.
- Cavidades de retração na superfície da folha do eletrodo
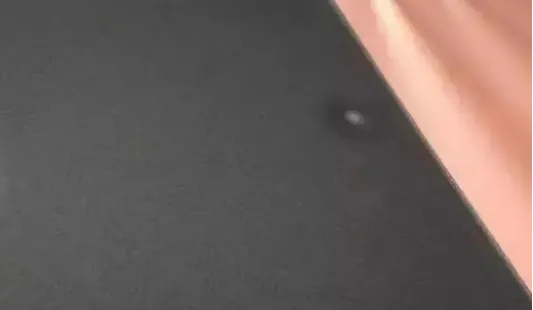
Formulação: grafite em flocos + SP+CMC/SBR+água destilada
Existem partículas poluentes na superfície da folha e há uma área de baixa tensão superficial no filme úmido na superfície das partículas. O filme líquido migra radialmente ao redor das partículas, formando defeitos no ponto de retração.
- Arranhões na superfície da folha do eletrodo

Formulação: NMC532 + SP + PVdF + NMP
Durante o processo de revestimento por extrusão por fenda, a presença de partículas grandes na aresta de corte leva a arranhões na superfície da folha do eletrodo.
- Revestimento de tiras verticais
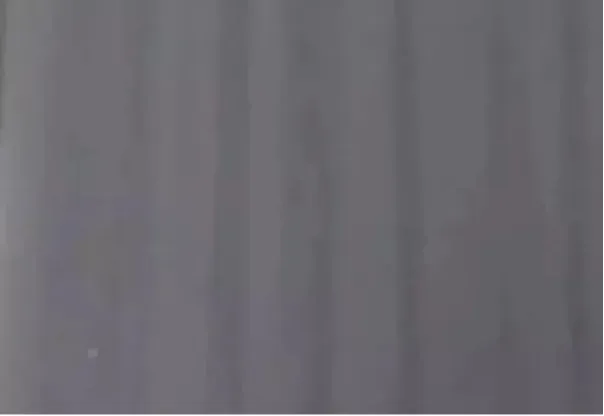
Formulação: NCA + SP + PVdF + NMP
Durante os estágios posteriores do revestimento de transferência, a pasta exibe maior viscosidade devido à absorção de água. O processo de revestimento se aproxima do limite superior da janela de revestimento, resultando em baixo nivelamento da pasta e formação de listras verticais.
- Rachaduras rolantes na área úmida da folha do eletrodo
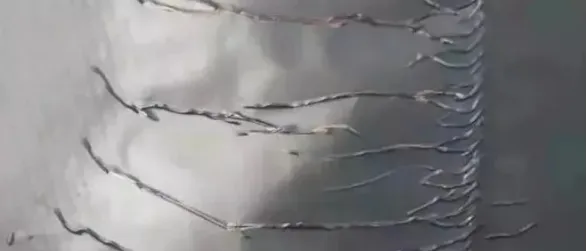
Formulação: grafite em flocos + SP+CMC/SBR+água destilada
Durante o revestimento, a área intermediária da folha de eletrodo não estava completamente seca e o revestimento migrou durante a laminação, formando rachaduras semelhantes a tiras.
- Folha de eletrodo rugas de borda laminada
Bordas grossas são formadas durante o revestimento. O tipo de rolamento causa rugas nas bordas do revestimento.
- O revestimento de corte do eletrodo negativo é separado da folha
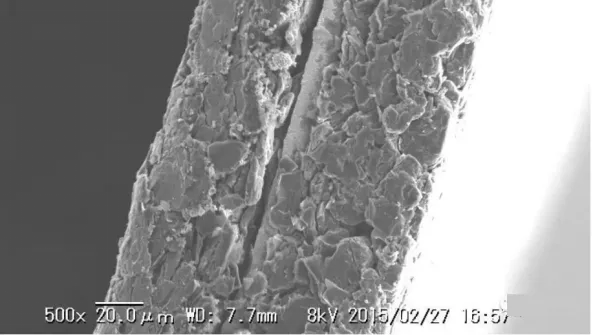
Fórmula: grafite natural + preto de acetileno + CMC/SBR + água destilada, proporção de substância ativa 96%
Quando o disco da folha do eletrodo é cortado, o revestimento se separa da folha.
- Rebarbas de corte de folha de eletrodo
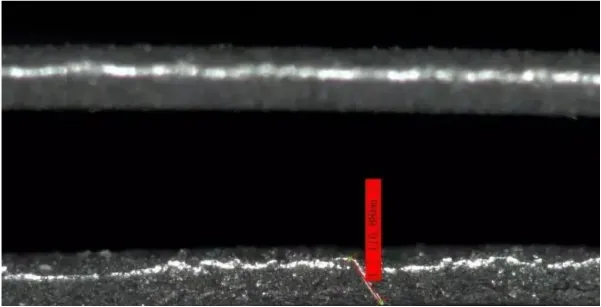
Quando o disco de eletrodo positivo é cortado, o controle de tensão instável faz com que rebarbas de folha sejam formadas por corte secundário.
- Folha de eletrodo fenda borda ondulada
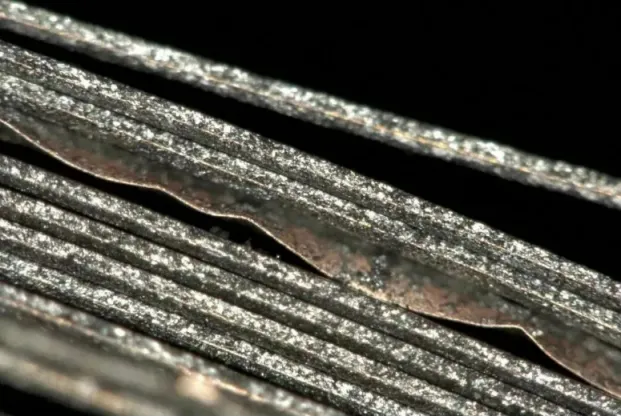
Quando o disco do eletrodo negativo é cortado, devido à sobreposição e pressão inadequadas dos cortadores, bordas onduladas são formadas e o revestimento do corte é descascado.
- Outros defeitos comuns de revestimento incluem: infiltração de ar, ondas transversais, fluxo vertical, riacho, expansão, ondulações de água, etc.
Os defeitos podem ocorrer em vários estágios do processamento: formulação do revestimento, preparação do substrato, área de operação do revestimento, zona de secagem, corte, corte, processos de calandragem e assim por diante. A abordagem lógica geral para resolver defeitos é a seguinte:
Otimize os processos de formulação, revestimento e secagem do produto, desde a escala piloto até a produção. Encontre a janela de processo ideal ou mais ampla ajustando parâmetros e variáveis.
Implementar medidas de controle de qualidade e ferramentas estatísticas (como Controle Estatístico de Processo, CEP) para controlar a qualidade do produto. Utilize sistemas de monitoramento on-line para garantir uma espessura de revestimento estável ou empregue sistemas de inspeção visual (Visual Systems) para detectar defeitos de superfície.
Quando ocorrerem defeitos, faça ajustes oportunos no processo para evitar defeitos recorrentes. Identifique a causa raiz, analise as variáveis do processo e modifique os parâmetros de acordo para corrigir o problema.
4. Uniformidade do revestimento
O termo "uniformidade do revestimento" refere-se à consistência da espessura do revestimento ou distribuição do adesivo dentro de uma área de revestimento. Quanto melhor a consistência da espessura do revestimento ou distribuição do adesivo, maior a uniformidade do revestimento e vice-versa. Não existe uma métrica padronizada para a uniformidade do revestimento, mas ela pode ser medida pelo desvio ou desvio percentual da espessura do revestimento ou da quantidade de adesivo em vários pontos dentro de uma determinada área em relação à espessura média do revestimento ou quantidade de adesivo nessa área. Também pode ser medido pela diferença entre a espessura máxima e mínima do revestimento ou a quantidade de adesivo dentro de uma determinada área. A espessura do revestimento é normalmente expressa em micrômetros (μm).
A uniformidade do revestimento é usada para avaliar a qualidade geral do revestimento em uma área específica. No entanto, na produção prática, geralmente estamos mais preocupados com a uniformidade nas direções transversal (cross-machine) e longitudinal (direção da máquina) do substrato. A uniformidade transversal refere-se à uniformidade na direção da largura do revestimento (ou direção da máquina), enquanto a uniformidade longitudinal refere-se à uniformidade na direção do comprimento do revestimento (ou direção de deslocamento do substrato).
A magnitude, os fatores de influência e os métodos de controle dos erros de revestimento transversal e longitudinal são significativamente diferentes. Geralmente, quanto maior a largura do substrato (ou revestimento), mais desafiador é controlar a uniformidade transversal. Com base em anos de experiência prática em operações de revestimento, geralmente é relativamente fácil garantir a uniformidade transversal quando a largura do substrato é inferior a 800 mm. Quando a largura do substrato varia de 1300 mm a 1800 mm, a uniformidade transversal geralmente pode ser bem controlada, mas requer um nível considerável de especialização. No entanto, quando a largura do substrato excede 2000 mm, alcançar a uniformidade transversal torna-se extremamente desafiador e apenas alguns fabricantes podem lidar com isso de forma eficaz. Por outro lado, à medida que o tamanho do lote de produção (ou seja, comprimento do revestimento) aumenta, a uniformidade longitudinal pode se tornar um desafio ou dificuldade maior em comparação com a uniformidade transversal.