A linha de montagem de baterias de bolsa é uma parte crucial dos processos de estágio intermediário a final na fabricação de baterias de lítio. É o principal responsável por manusear as células nuas montadas ou enroladas e realizar operações como soldagem de abas, fitagem, revestimento de células e vedação do lado superior. O princípio de design da linha de montagem é baseado no processo de produção de baterias de lítio, levando em consideração fatores como tamanho da célula, estrutura e eficiência de produção desejada.
1.Visão geral debolsa Linha de montagem de pacotes
1.1 Princípios de design e princípios da linha de montagem
A seleção da forma da linha de montagem para baterias de bolsa é determinada principalmente pelas especificações de tamanho das células. Para células com comprimento abaixo de 390 mm, a máquina de solda de guias, a máquina de embalagem e a seção subsequente da máquina de embalagem geralmente adotam uma estrutura de plataforma giratória acionada por um divisor de cames. Este layout estrutural é compacto e ocupa uma pequena área útil. No entanto, é limitado pela precisão do toca-discos. Quanto maior a plataforma giratória, menor a precisão de montagem das células. Além disso, o aumento da carga também afeta a dificuldade e a eficiência de iniciar e parar a plataforma giratória.
Para especificações de células com comprimento acima de 390 mm, a máquina de solda de guias, a máquina de embalagem e a seção subsequente da máquina de embalagem geralmente adotam uma estrutura linear. Esse layout permite um posicionamento preciso durante a comutação da estação para baterias grandes e oferece alta eficiência na comutação da estação, proporcionando melhor potencial para melhorar a eficiência da produção. No entanto, esse layout tem a desvantagem de ocupar uma área útil relativamente estreita, e o mecanismo de acionamento para comutação de estações é mais complexo, resultando em custos relativamente mais altos. O layout de uma linha de montagem linear é mostrado no diagrama abaixo.
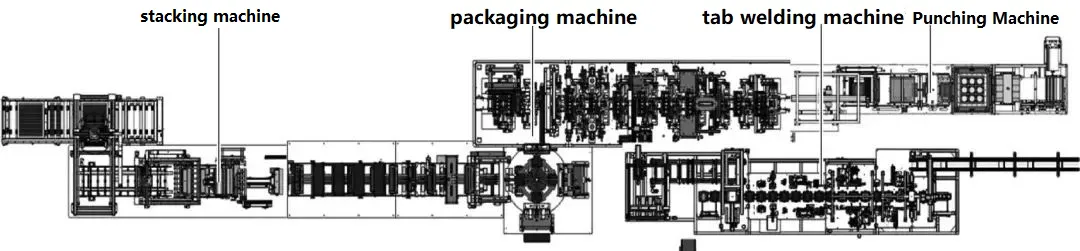
1.2Assembléia linhaeficiência distribuição
No processo de projeto da linha de construção, o controle do ritmo depende principalmente das limitações da estação de gargalo de produção de cada estação. Por exemplo, o requisito real de capacidade de produção é de 8PPM. Em relação à capacidade de produção abrangente do equipamento, o projeto real é geralmente baseado em 10PPM, e o limite de trabalho é As posições serão realizadas de maneira multiestações, como o mecanismo de alimentação de chapas protetoras na pré-soldagem da guia da seção da máquina de solda, o mecanismo de alimentação da guia na soldagem da guia, o tempo de embalagem de vedação superior e inferior, o tempo de embalagem de vedação lateral na máquina de embalagem, etc. . Depois de comparar os requisitos de capacidade de produção, calcule o tempo de processo necessário para cada estação. Se não for atendido, é necessário o projeto de várias estações. Por exemplo, quando o requisito de eficiência do equipamento é de 12 PPM, o tempo de processo e o tempo de produção de cada célula de bateria são de 5 segundos. Os requisitos de tempo de embalagem de alguns clientes chegam a 4 a 5 segundos, mais o tempo de comutação da estação de célula da bateria e o tempo de ação do mecanismo de embalagem. , não pode atender aos requisitos de eficiência de produção, por isso é necessário projetar uma estação de trabalho dupla desta estação para atender aos requisitos de eficiência de produção. A distribuição de batidas de outras estações de trabalho é a mesma.
1.3 Métodos logísticos
Quando as baterias são montadas, a logística deve ser usada para transferir e alternar entre as estações de trabalho. Portanto, métodos logísticos razoáveis precisam ser selecionados para baterias em diferentes estados.
(1) Para as células nuas descarregadas da máquina de empilhamento, a fim de garantir a eficiência de transporte das células e proteger a segurança das células, o método de corrente de dupla velocidade + braçadeira de célula é geralmente usado. A corrente de dupla velocidade tem alta eficiência de transporte e é adequada para produção de longo prazo. Tem as vantagens de transporte de longa distância, grande carga, manutenção simples, etc., e o perfil de corrente de dupla velocidade tem grande flexibilidade para definir paradas e outras instalações e ajustes de estruturas auxiliares. A desvantagem é que a corrente de dupla velocidade é propensa a atrito e gera poeira. Para evitar o impacto da poeira nos núcleos das baterias, alguns fabricantes usam linhas transportadoras de levitação magnética para transportar baterias desencapadas, mas isso é caro.
(2) Os núcleos elétricos são transportados da máquina de empilhamento para a máquina de solda. Cada estação na máquina de solda tem altos requisitos para a precisão de posicionamento dos núcleos elétricos. Os núcleos elétricos são carregados no dispositivo de soldagem e adotam um método de transporte passo a passo. A fim de garantir a precisão De acordo com os requisitos, o acionamento adota a estrutura de circulação do servo motor + garfo de mudança.
(3) Depois que os núcleos da bateria são descarregados da máquina de solda, o método de transporte de servo motor + correia síncrona é geralmente usado. Isso pode garantir o espaçamento igual do transporte do núcleo da bateria e facilitar a precisão das posições de carregamento e descarregamento do robô. Da mesma forma, o mesmo método é adotado após a máquina de embalagem, que é econômica e eficiente.
1.4 Métodos e princípios de posicionamento celular
Na linha de montagem de células de bateria, o fabricante da bateria tem certos requisitos de precisão dimensional para as células de bateria em termos de processo. Portanto, as células da bateria precisam ser posicionadas antes que a bateria entre na linha de montagem. As células da bateria são posicionadas na mesma base. Cada estação de trabalho subsequente O ajuste também é baseado nisso para garantir a consistência da montagem da bateria.
A forma do corpo do núcleo da bateria é retangular, portanto, em termos de posicionamento, dois lados são geralmente usados como referência de posicionamento e os outros dois lados são usados para posicionar o núcleo da bateria empurrando. Você também pode usar o método de posicionamento central do corpo da bateria para empurrar o corpo da bateria para frente, para trás, para a esquerda e para a direita ao mesmo tempo. A escolha do método de posicionamento geralmente depende dos requisitos de tamanho do processo do núcleo da bateria e da conveniência do projeto estrutural, desde que o benchmark seja consistente.
1.5 Controle de poeira
No processo de produção da bateria, o perigo mais fatal é que o pó metálico entra no corpo da bateria, causando uma série de problemas, como curto-circuito da bateria e incêndio. Para evitar que essa situação aconteça, é necessário controlar rigorosamente as fontes de poeira na linha de montagem e removê-las o máximo possível. Para controlar a poeira, devemos primeiro descobrir a fonte da poeira e, em seguida, tomar medidas direcionadas.
(1) Linha de transporte da máquina de laminação (corrente de velocidade dupla). Durante o processo de transporte, a corrente de dupla velocidade esfregará contra o perfil da corrente de dupla velocidade para gerar muita poeira. Para este tipo de poeira, é necessário instalar uma placa à prova de poeira no corpo da linha de corrente de dupla velocidade para evitar que a poeira caia no núcleo da bateria. Ao mesmo tempo, o grampo do núcleo da bateria deve ser o menor possível. O transportador é transportado por fixação superior e inferior, e os acessórios vazios na linha de retorno são polvilhados em pontos fixos. O método de remoção de poeira é realizado por sopro + sucção. Como a linha é relativamente longa, a frequência da limpeza manual precisa ser aumentada para evitar o acúmulo de poeira, etc. .
(2) Linha de montagem. Quando as baterias circulam na linha de montagem, algumas estações de trabalho podem gerar poeira, como as estações de pré-soldagem, corte, soldagem de abas e estampagem de solda das abas. Desde que haja uma estação de corte ou soldagem, eles serão instalados. Um mecanismo especial de remoção de poeira realiza a coleta ininterrupta de poeira. A imagem abaixo mostra o mapa da estação de remoção de poeira.
1.6 Controle de qualidade
Para garantir a estabilidade e consistência da qualidade da produção da bateria, haverá sensores de detecção correspondentes para controle de qualidade em todos os aspectos da produção da bateria. Para a linha de montagem, as manifestações específicas são as seguintes:
(1) O sensor de cor é usado para detectar a polaridade do núcleo da bateria de entrada, principalmente para evitar que a bateria seja descarregada inversamente após intervenção manual.
(2) Digitalize o código da bateria para garantir que as informações da bateria sejam carregadas no sistema MES em tempo hábil, o que facilita o rastreamento das informações de produção da bateria.
(3)A inspeção por raios-X do núcleo da bateria é usada para detectar o alinhamento do núcleo da bateria para evitar a produção subsequente de baterias gravemente desalinhadas.
(4) Detecção de polaridade da guia e detecção positiva e negativa para evitar erros de soldagem.
(5) Detecção de cola após a soldagem da guia para evitar o contato direto da impressão de solda com o filme de alumínio-plástico durante a embalagem subsequente.
(6) Inspeção de tamanho CCD após a soldagem da guia para garantir a consistência do tamanho da produção do núcleo da bateria.
(7) Após a soldagem, o teste Hi-pot é realizado na célula da bateria para garantir que não haja condutividade entre os terminais positivo e negativo da célula soldada.
(8) Controle de desvio de filme plástico de alumínio para garantir a taxa de rendimento de perfuração do filme plástico de alumínio.
(9) Detecção do tamanho do CCD da bateria após a embalagem para garantir a consistência da aparência e tamanho da bateria.
(10) Após o encapsulamento, o teste Hi-pot é realizado na bateria para garantir que não haja condutividade entre os terminais positivo e negativo da célula encapsulada.
(11)O teste de isolamento da bateria após o encapsulamento é realizado para garantir que não haja condutividade entre os terminais positivo e negativo da célula encapsulada e o filme de alumínio-plástico.
(12) Teste a espessura da vedação da bateria após a embalagem para garantir a consistência da vedação da bateria após a embalagem.
Através da série de métodos e pontos de controle acima mencionados, a qualidade da bateria em toda a linha de montagem pode ser controlada de forma eficaz.
2. Principais funções e descrição do equipamento
As baterias de lítio são um tipo de bateria que usa metal de lítio ou liga de lítio como material de eletrodo negativo e usa uma solução eletrolítica não aquosa. Os principais componentes das baterias de lítio são eletrodos positivos e negativos, eletrólitos, separadores e invólucros. As baterias de lítio são baterias com um invólucro de polímero colocado em uma bateria líquida de íons de lítio e embaladas com filme composto de alumínio-plástico. Em comparação com baterias cilíndricas e baterias de alumínio, a composição da bateria é a mesma, mas a forma de embalagem e a estrutura física da bateria são diferentes, o que faz com que a forma de montagem e o processo de produção da bateria de bolsa sejam diferentes. baterias de bolsa A estrutura é mostrada na figura.
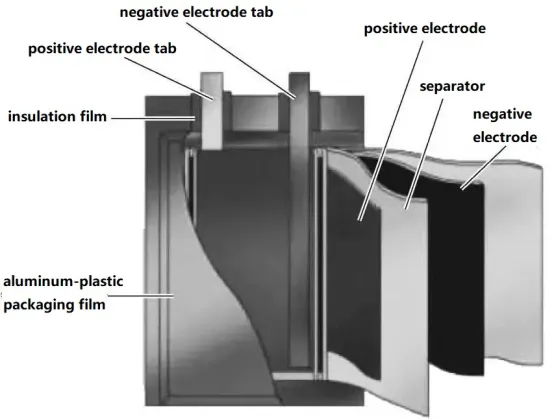
estrutura celular da bolsa
O processo de produção da linha de montagem da bateria do pacote de bolsas pode ser dividido em três partes: a primeira parte é a parte de soldagem da aba, a segunda parte é a parte da máquina de embalagem e a terceira parte é a parte da máquina de perfuração de poço
Os principais indicadores técnicos de uma linha de montagem de células de bolsa são os seguintes:
(1) Taxa de qualificação do produto: ≥99%.
(2) Eficiência geral da produção da linha: Dependendo dos requisitos da linha de produção.
(3) Número de operadores necessários para a linha de produção: 2 pessoas.
(4) Taxa de utilização geral do equipamento: ≥98% [Fórmula de cálculo: (24h – tempo de inatividade – hora do alarme)/24 × 100%].
(5) Taxa de qualificação do equipamento de embalagem: ≥98,8%.
3.Composição do equipamento e estruturas-chave
A linha de montagem da célula de bolsa consiste principalmente em uma máquina de solda de eletrodo, uma máquina de embalagem e a máquina de pós-embalagem.
3.1 Máquina de solda de aba
A máquina de solda de aba é responsável por dobrar e pré-soldar as abas de cobre ou alumínio das células nuas recebidas da máquina de empilhamento. Ele executa processos como soldagem ultrassônica final das abas, achatamento das impressões de solda, remoção de poeira e aplicação de adesivo para se preparar para o encapsulamento subsequente nos bolsos de filme plástico de alumínio. As principais estruturas da máquina de solda de aba de eletrodo incluem pré-soldagem das abas de célula, corte de aba, soldagem final das abas de célula, achatamento de impressão de solda e remoção de poeira e aplicação de adesivo.
A máquina de solda de abas realiza a pré-soldagem e a soldagem final das abas das células nuas recebidas da máquina de empilhamento. Suas principais estruturas incluem corte de abas, pré-soldagem de abas, soldagem de aba a aba e remoção de poeira de impressão de solda.
A pré-soldagem de abas envolve dobrar e soldar as abas de cobre ou alumínio da célula, preparando-as para o processo final de soldagem. Os componentes desta estrutura incluem uma máquina de pré-solda, uma base de máquina de solda, um mecanismo de dobragem e um mecanismo de remoção de poeira. A estrutura da pré-soldagem de abas é mostrada no diagrama.
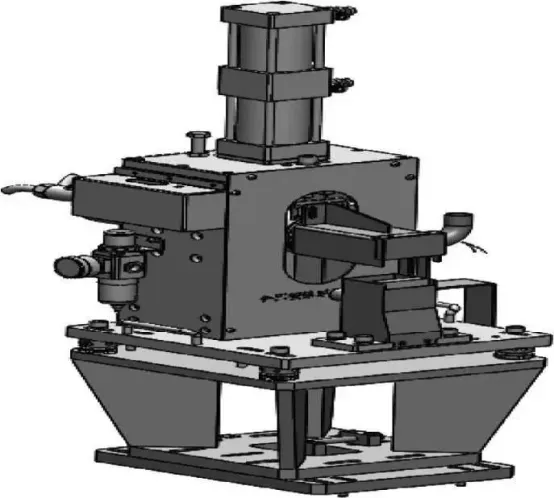
1) Pre-soldadura das abas
A função e a ação desta estrutura são usadas para realizar a pré-soldagem ultrassônica das abas. A cabeça de soldagem sob a máquina de solda é fixa (o design da cabeça de soldagem, base de soldagem e base precisa ser comunicado ao cliente). Depois que as abas das células estão no lugar, o cilindro é pressionado para baixo A braçadeira do palete atinge a altura de trabalho de pré-soldagem e a poeira é coletada durante a soldagem; e as abas são reunidas durante a soldagem. Há um dispositivo de proteção no núcleo da bateria soldada para evitar que a escória de soldagem caia no núcleo da bateria. A cabeça de soldagem inferior possui uma tampa contra poeira e há um dispositivo de adsorção de poeira dentro da tampa contra poeira, incluindo um dispositivo soprador e um dispositivo de adsorção de poeira para garantir que a poeira de soldagem possa ser absorvida de forma limpa; A velocidade do vento de sucção de poeira deve ser de ≥15 m/s.
Para a precisão da posição de soldagem da pré-soldagem da guia, o desvio na direção para cima e para baixo deve ser de ≤±0,2 mm e o desvio na direção esquerda e direita é de ≤± 0,2 mm.
Observações: A linha de embalagem de soldagem precisa ser conectada aos dados de acordo com a máquina de solda e pode coletar os principais parâmetros de soldagem (os parâmetros de soldagem incluem energia, potência, tempo, pressão, etc.) e pode receber informações anormais de soldagem relevantes, realizar alarmes anormais e descarregar a célula NG.
2) Corte de abas
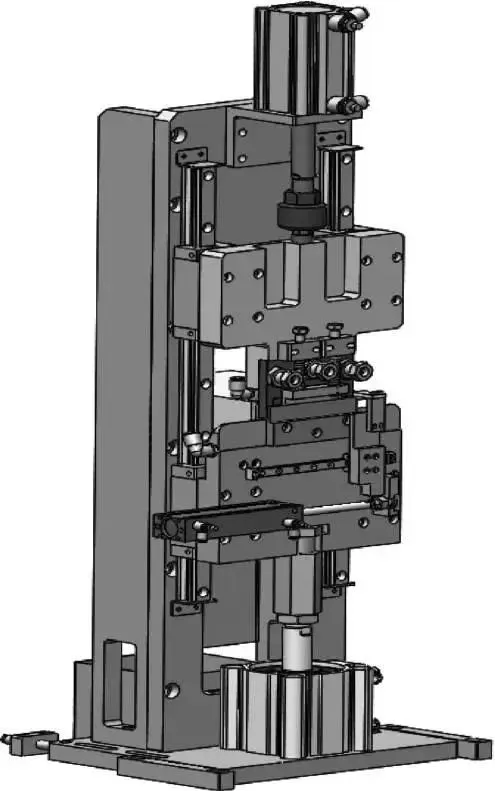
A estrutura de corte de abas é usada principalmente para cortar as abas de cobre e alumínio pré-soldadas ordenadamente. Consiste em lâminas de corte superior e inferior, mecanismos de orientação da lâmina de corte superior e inferior, mecanismo de remoção de poeira, calha guia de resíduos, cilindro superior, cilindro inferior e outros componentes. A estrutura do corte da aba do eletrodo é mostrada na Figura.
Esta estrutura é usada para obter o corte automático das abas de eletrodo positivo após a pré-soldagem. As ferramentas de corte usam SKD11 com revestimento de carbono tipo diamante para evitar a adesão. As ferramentas de backup são usadas em uma abordagem individual, e o tratamento de carboneto de tungstênio pode ser aplicado ao SKD11 de acordo com os requisitos do cliente. Há um micrômetro digital para ajustar a posição de corte, tornando-o conveniente para o ajuste manual, e a lâmina de corte corta na impressão da solda de pré-soldagem. A faixa ajustável do comprimento da aba de corte é de 0 a 10 mm, com uma precisão de corte de ±0,1 mm. O requisito de vida útil da lâmina de corte é que ela possa ser usada por um mínimo de 300.000 vezes (com um lembrete para afiar a cada 200.000 vezes) e pode ser afiada novamente mais de 10 vezes. Há uma capa à prova de poeira na lâmina de corte, isolando o mecanismo de corte do ambiente externo. O exaustor à prova de poeira possui um dispositivo de adsorção de poeira para garantir a limpeza através da adsorção de resíduos de corte e poeira. O requisito de velocidade do fluxo de ar de extração de poeira é de ≥15 m/s. Há uma caixa receptora dentro do mecanismo de corte para coletar o material da folha cortada. A placa de corte tem um design convexo e a força da mola é ajustável. Antes do corte, a película protetora de ambos os lados é pressionada para evitar que a película protetora se deforme e afete os processos subsequentes.
3.Soldagem final da guia
O processo de soldagem final da guia consiste no mecanismo de alimentação da guia positiva / negativa e no processo de soldagem principal das guias de eletrodo positivo / negativo.
(1) Mecanismo de alimentação de guia positivo / negativo: O mecanismo de alimentação de guia positivo / negativo consiste em um mecanismo de alimentação estilo carregador de guia, dispositivo de elevação servo, mecanismo de sucção de guia, mecanismo de posicionamento secundário, sensor de detecção de mecanismo de carregador, etc. É usado para obter alimentação automática de guias positivas e negativas.
A principal função do mecanismo de alimentação de abas positivas/negativas é o processo crítico de soldagem da alça condutora da aba e das abas positivas/negativas pré-cortadas. Na produção real, as guias precisam ser alimentadas continuamente. Para garantir a troca ininterrupta de material sem parar a máquina, um mecanismo de buffer de aba precisa ser projetado no mecanismo. O robô de recuperação de guias precisa ter uma função de rotação para evitar erros na orientação das guias. A detecção de polaridade das abas é para detectar a polaridade das abas positivas e negativas para evitar o posicionamento incorreto por humanos. O mecanismo de posicionamento das abas é necessário devido à precisão posicional entre as abas da célula e as abas durante a soldagem. Os pontos de referência de posicionamento podem ser as laterais das abas e o adesivo PP ou os arredores das abas, dependendo dos requisitos do cliente. O mecanismo de alimentação das abas segura com segurança as abas posicionadas corretamente e as entrega na posição predeterminada para a soldagem final. Devido aos requisitos de precisão posicional, o mecanismo de acionamento é uma combinação de um servo motor e um fuso de esferas para garantir a precisão. O mecanismo de alimentação de abas positiva/negativa é mostrado na figura a seguir.
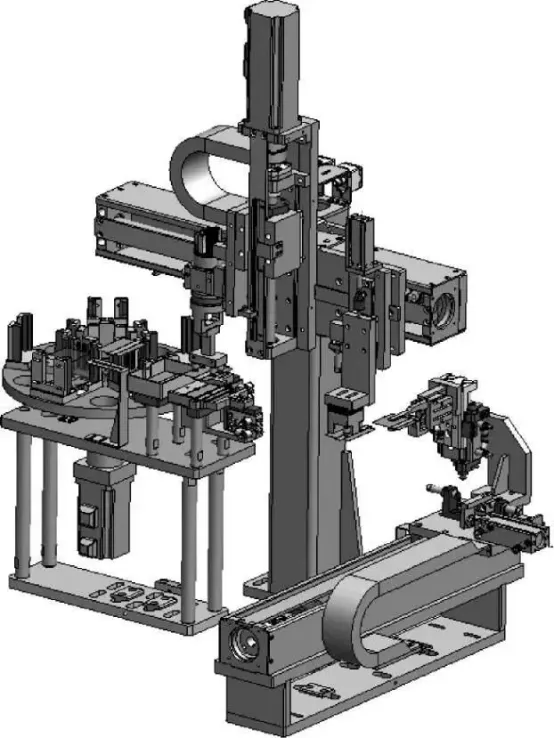
As funções e ações do mecanismo de carregamento de guias positivas/negativas são as seguintes:
um. Há um total de 5 revistas no mecanismo da revista. As revistas positivas e negativas são diferenciadas por cores e marcações. Um carregador pode conter 200 guias por vez e pode funcionar continuamente por mais de 2 horas com uma alimentação.
b. Precisão dimensional da guia para materiais recebidos: As guias são colocadas manualmente no clipe durante a recepção do material. A bateria utiliza procedimentos de escovação, sopro de ar e agitação elétrica para evitar várias peças, garantindo uma taxa de qualificação de 100%. A detecção da posição da alça condutora é usada para identificar os lados positivo e negativo. Os grampos terminais positivo e negativo são diferenciados pela cor. A transferência de 6 carregadores é completada por servos, e existem sensores na posição de carregamento do material para detectar a presença de materiais. A rotação servo é adotada para evitar deslocamento excessivo de posicionamento, o que pode causar distorção das orelhas da guia.
c. O posicionamento da aba usa o posicionamento mecânico para posicionar o lado curto do clipe condutor e a cola da aba.
d. Para fixação e carregamento, um cilindro de dedo é usado para prender a alça condutora na maior área para evitar o deslizamento da alça condutora. O método de transferência servo atinge uma alimentação precisa e a precisão de posicionamento da guia é de ±0,2 mm.
(2) Soldagem principal de abas de eletrodo positivo / negativo. Os principais componentes da soldagem principal de abas positivas / negativas são máquina de solda ultrassônica, mecanismo de posicionamento, sistema de detecção, sistema de coleta de poeira, etc. A soldagem principal de abas positivas/negativas é mostrada na figura.
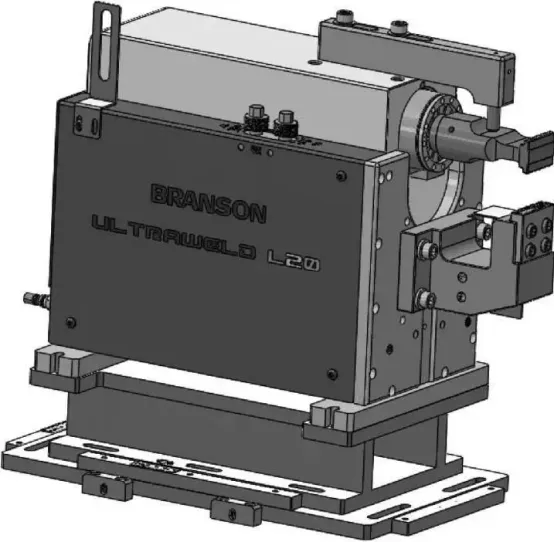
A soldagem principal de abas positivas/negativas é usada para obter soldagem ultrassônica de abas positivas e negativas. A cabeça de soldagem inferior deste mecanismo é fixa e as abas são soldadas acima das abas da bateria. Toda a máquina de solda pode ser ajustada horizontalmente para se adaptar aos requisitos do processo.
As características técnicas da soldagem principal de aba positiva / negativa são as seguintes:
a. A vida útil de uso único da ponta de soldagem/matriz inferior é de ≥ 50.000 vezes e pode ser remoída por mais de 5 vezes em uma única superfície. A compatibilidade da ponta de soldagem/matriz inferior com o número de camadas de soldagem de aba é de ≤50 camadas. O projeto da ponta de soldagem/matriz inferior e da base precisa ser comunicado com a Parte A.
b. Após a soldagem, existe um dispositivo para detectar se a aba está soldada à alça condutora. O sistema irá gerar um alarme e acionar o dispositivo NG (não bom) se houver algum problema com a bateria.
c. Os principais parâmetros de soldagem (os parâmetros de soldagem incluem energia, potência, tempo, pressão, etc.) podem ser definidos com limites superior e inferior. Tem as funções de detecção on-line, alarme anormal, exclusão de NG celular e alça condutora reservada para soldagem para cima e para baixo.
d. Tratamento de coleta de poeira: Há um dispositivo de proteção na lateral do núcleo da bateria soldada para evitar que a escória de soldagem caia no núcleo da bateria. Faça uma tampa protetora contra poeira para seguir o movimento da cabeça de soldagem e ligue a poeira durante a soldagem ultrassônica. A velocidade do vento de sucção de poeira é de 20m/s, o que pode efetivamente sugar a poeira de metal.
e. Precisão: A precisão de posicionamento da guia é de ±0,2 mm; A precisão da posição de soldagem é de ±0,2 mm para cima e para baixo e ±0,2 mm para a esquerda e para a direita.
f. Os parâmetros de soldagem possuem armazenamento local e possuem a função de interface para conexão com MES. Uma porta manual de remoção de poeira é adicionada, e a estação de soldagem tem a função de verificar se a aba de soldagem está presente e detectar a aba após a soldagem.
4) Remoção de poeira da solda da guia
A remoção de poeira das marcas de soldagem da aba é crucial para a taxa de escoamento e o desempenho de segurança do núcleo da bateria. A principal razão é que o processo de soldagem ultrassônica é a soldagem por fricção mecânica, que produzirá muita poeira de metal e muitas rebarbas afiadas cairão nas marcas de soldagem. Às vezes, também pode se tornar uma fonte de pó de metal. Depois que esse pó de metal entrar no corpo da bateria, ele perfurará o separador entre os eletrodos positivo e negativo, causando curto-circuito na bateria e causando acidentes perigosos, como incêndio.
A remoção de poeira da guia é dividida em duas partes: o mecanismo de achatamento de estampagem de soldagem e o mecanismo de remoção de poeira secundário de estampagem de soldagem.
(1) Mecanismo de soldagem e achatamento. O achatamento do carimbo de soldagem é carimbar e achatar o carimbo de solda após a soldagem final da peça Tab. Seu principal objetivo é achatar ou remover as rebarbas do carimbo de solda na superfície da guia após a soldagem ultrassônica, de modo a facilitar a remoção de poeira secundária do carimbo de solda. É fácil se preparar para o trabalho. Há também uma porta de sucção de poeira neste mecanismo para remover a poeira da escória de soldagem que é pressionada diretamente para baixo e fácil de sugar.
O mecanismo de estampagem e achatamento de soldagem consiste em um mecanismo de movimentação do cilindro superior, um mecanismo de elevação inferior, um bloco de pressão, uma tampa de vácuo, etc. É usado principalmente para realizar a modelagem após a soldagem das abas, a pressão de modelagem é de ≥500N e o material da placa de pressão é PEEK. Não há empenamento após a modelagem, a posição de modelagem é ajustável e o mecanismo de soldagem e achatamento é mostrado na figura.
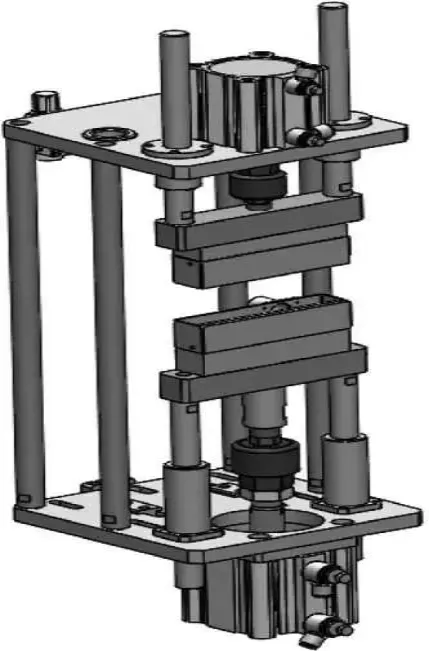
(2) Mecanismo de remoção de poeira secundária de impressão de soldagem. O objetivo da remoção de poeira secundária da impressão de soldagem é remover independentemente a poeira da impressão de soldagem, limpando completamente a poeira de metal que não foi removida pelo mecanismo de achatamento.
O mecanismo secundário de remoção de poeira consiste principalmente em um mecanismo de movimento do cilindro, câmara selada, mecanismo de escova, etc. Sua função e ações são as seguintes: usar um dispositivo de limpeza para limpar a área de soldagem, garantindo que não haja partículas estranhas maiores que 50μm após a limpeza. Ele também possui um dispositivo de adsorção de poeira para garantir a limpeza completa da poeira, com uma velocidade de fluxo de ar de extração de poeira de ≥20 m/s. O processo de limpeza não deve causar contaminação secundária na célula da bateria e não deve danificar as abas dos eletrodos. O mecanismo de remoção de poeira secundária da impressão de soldagem é mostrado na figura a seguir.
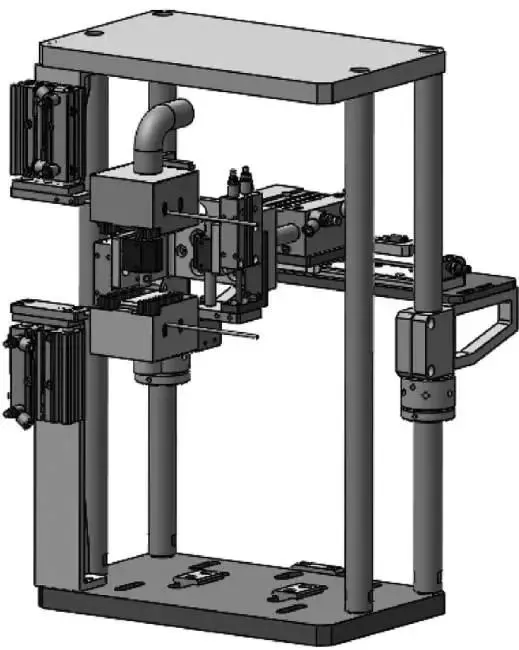
O mecanismo de achatamento para soldar impressões e o mecanismo secundário de remoção de poeira garantem a suavidade dos processos subsequentes, como aplicação e embalagem de adesivo, bem como a fusão de ar quente.
5.Colagem e inspeção de guias
A colagem das impressões de abas é realizada aplicando fita adesiva para garantir que, durante a embalagem subsequente, a superfície irregular das impressões não entre em contato direto com o filme de alumínio-plástico, evitando assim o risco de perfurar o adesivo PP e entrar em contato direto com a camada de alumínio.
O processo de colagem e inspeção de abas consiste em duas partes: o mecanismo de colagem de abas e o mecanismo de inspeção de colagem de abas.
(1)Mecanismo de colagem de abas: O mecanismo de colagem de abas consiste em mecanismo de alimentação de fita adesiva, mecanismo de tensionamento, mecanismo de guia, mecanismo de corte automático, mecanismo de sucção de adesivo, etc. O processo de colagem envolve mecanismos de colagem superior e inferior separados. O mecanismo de colagem é dividido em mecanismo de colagem superior e mecanismo de colagem inferior, ambos funcionando da mesma maneira. O comprimento da fita adesiva é compatível com ≤100 mm e a largura é de ≤25 mm. Ele garante que a fita adesiva azul cubra completamente a impressão e as bordas inferiores da aba, com colagem perfeita e sem pressionar o adesivo PP na alça condutora. No mecanismo de colagem, a tensão da fita adesiva azul durante o processo de tração é controlada pela tensão da mola para garantir que a fita adesiva azul não volte, enrugue ou se solte após a colagem, resultando em uma adesão completa e adequada. O material da cabeça de sucção adesiva é anodizado A6061, o que não danifica a aba. Ele pode atingir uma precisão de posição de colagem de ±0,2 mm, precisão de alinhamento vertical de ±0,2 mm e precisão de corte de ±0,2 mm. O diagrama do mecanismo de colagem da aba é mostrado na figura a seguir.
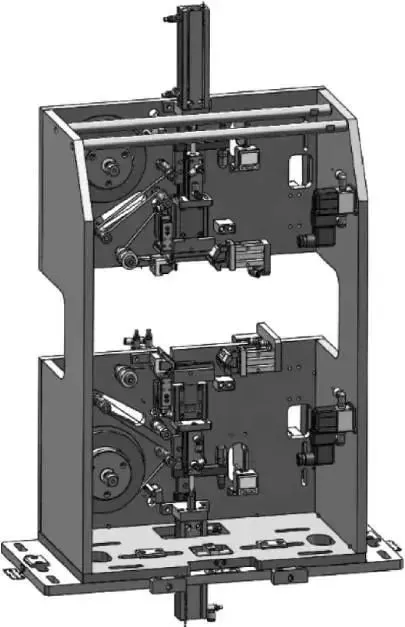
(2) Mecanismo de inspeção de colagem de abas. O principal objetivo do mecanismo de inspeção de colagem de abas é detectar a presença de fita adesiva nas impressões da aba da célula da bateria e achatar a fita adesiva.
O mecanismo de inspeção de colagem consiste principalmente em cilindros, blocos de pressão, sondas e outros componentes. O mecanismo para inspecionar a colagem de impressões de abas é mostrado na figura a seguir.
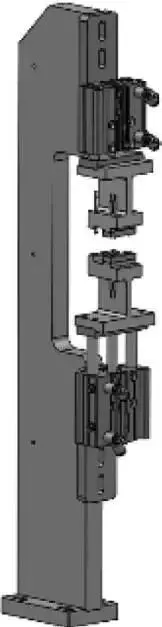
Após o tratamento do mecanismo de colagem de abas e do mecanismo de inspeção de colagem, o impacto das impressões de soldagem na embalagem de filme plástico de alumínio é efetivamente evitado.
(2) Máquina de perfuração de filme plástico de alumínio
A máquina de perfuração de filme de alumínio-plástico desenrola ativamente a bobina de filme de alumínio-plástico e perfura os bolsos de filme de alumínio-plástico de maneira sequencial para atender aos requisitos de tamanho da bateria. As principais estruturas da máquina de perfuração de filme de alumínio-plástico incluem principalmente o mecanismo de desenrolamento e correção, mecanismo de corte, mecanismo de perfuração, mecanismo de corte, mecanismo de corte, etc.
(1) Mecanismo de desenrolamento e correção: O mecanismo de desenrolamento e correção é a seção frontal da máquina de perfuração de filme plástico-alumínio. É responsável por carregar, trocar e desenrolar o filme de alumínio-plástico, bem como a correção em tempo real do filme de alumínio-plástico durante a operação normal.
O mecanismo de desenrolamento e correção consiste em um eixo de expansão de ar, mecanismo de posicionamento de filme de alumínio-plástico, mecanismo de desenrolamento ativo (incluindo motor, redutor, etc.), sistema de controle de tensão, plataforma de recebimento de material, sistema de correção, etc. Suas funções e ações são as seguintes: carregamento manual, posicionamento do cilindro do rolo de material, detecção do sensor fotoelétrico da presença do material, plataforma de alimentação manual da correia com faca de corte de filme de alumínio-plástico e placa de prensagem da correia e um dispositivo de sucção de poeira de pressão negativa abaixo da plataforma de alimentação da correia. A tensão do filme de alumínio-plástico é ajustada por um controlador de tensão e freio de pó magnético para manter uma tensão constante e uma direção de alimentação consistente. Possui uma estrutura de desenrolamento dupla para garantir a operação oportuna e a eficiência de toda a linha de produção. O mecanismo de desenrolamento e correção é mostrado na figura a seguir.
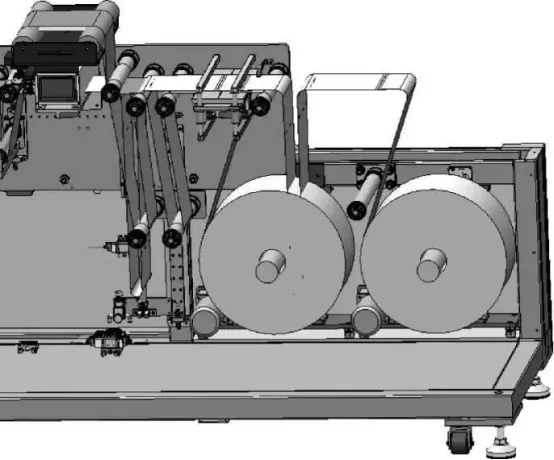
Os parâmetros de precisão relevantes do mecanismo de desenrolamento e correção são os seguintes:
Faixa de tensão: 0-100N
Precisão do controle de tensão: ±3N
Detecção do diâmetro do rolo: Faixa de detecção ≥ 400 mm, requisito de precisão de detecção ±0,1 mm
Para garantir que o filme de alumínio-plástico não seja danificado durante o transporte, tratamento e processamento especiais foram aplicados aos rolos-guia. O rolo guia é feito de liga de alumínio anodizado duro preto A6061, com uma espessura de revestimento superior a 4μm e uma rugosidade superficial de Ra0,8. A vida útil pode exceder 3 anos (garantindo a eficiência do equipamento, taxa de utilização e taxa de qualificação do produto). Rolamentos de baixo atrito são usados para o eixo do rolo para minimizar a resistência rotacional.
(2) Mecanismo de corte: O mecanismo de corte consiste principalmente em rolamentos lineares, colunas, cilindros, lâminas de corte e placas de fixação de lâminas. Suas principais funções e ações são as seguintes: antes de perfurar os bolsos, é usado para liberar o estresse cortando entre as duas camadas de filme plástico-alumínio. A lâmina de corte usa uma lâmina de faca artística para facilitar a aquisição e preparação. Quando o material está no lugar, a sucção a vácuo da plataforma é ativada e o cilindro superior aciona o mecanismo de corte para cortar o filme. O mecanismo de corte possui uma tampa de sucção de poeira, que pode sugar negativamente a poeira gerada durante o processo de corte, garantindo que os resíduos de corte e a poeira sejam removidos com eficácia. O requisito de velocidade do fluxo de ar de sucção é de ≥15m/s. A precisão da posição de pré-corte é de 0,3 mm e a faixa de ajuste do comprimento de corte pode ser selecionada conforme necessário. O mecanismo de corte é mostrado na figura a seguir.
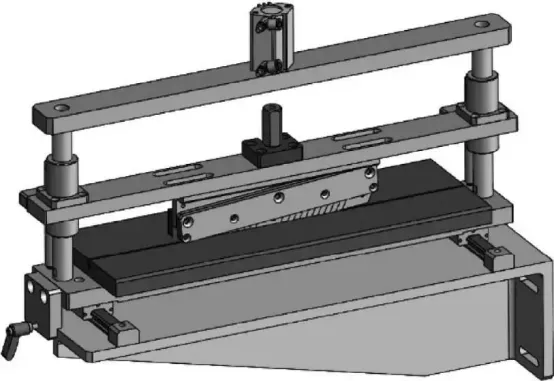
O mecanismo de corte prepara para a perfuração do filme de alumínio-plástico cortando fendas no filme de alumínio-plástico.
(3) Mecanismo de perfuração de poço. O mecanismo de perfuração é composto principalmente de molde de perfuração de concha, servo motor, redutor, fuso de esferas, cilindro, eixo guia, etc.
O mecanismo de perfuração do poço usa vários cilindros para comprimir o filme de alumínio-plástico, e um servo motor aciona o fuso de esferas para perfurar o poço. A profundidade pode ser ajustada livremente através de bolsas, com uma faixa de ajuste de 2 a 12 mm. A força de prensagem do filme de alumínio-plástico é ajustada pelo servo. O molde tem a função de perfurar os furos de posicionamento. Ele usa um método de perfuração de poço duplo. A precisão dimensional do invólucro de perfuração pode ser controlada dentro de ±0,1 mm. Os orifícios dos pinos de posicionamento são perfurados por um cilindro e a precisão de perfuração é alta. ±0,1 mm, os resíduos do orifício do pino são descarregados de ambos os lados da placa do molde inferior. Ambos os lados do molde de perfuração do equipamento são equipados com grades (perpendiculares à direção de transporte da correia). Quando materiais estranhos são detectados, o alarme soa e a máquina para. A manutenção é equipada com funções de proteção de segurança para evitar que o pessoal de manutenção fique preso pelo molde. dano.
O mecanismo de perfuração tem requisitos de troca de molde, portanto, cada máquina de perfuração é equipada com um carrinho de molde para facilitar a troca de molde.
O mecanismo de perfuração é usado muitas vezes, portanto, a seleção do material é muito importante. Existem principalmente os seguintes tipos de materiais: placa inferior 45 # temperada + niquelagem, placa superior 45 # temperada + niquelada, coluna principal 45 # temperada + cromada, modelo superior SKD11 + têmpera + nitretação, molde côncavo SKD11 + têmpera + nitretação, punção KD11 + têmpera + nitretação, placa fixa perfurada 45 # + niquelagem. O mecanismo de perfuração do poço é mostrado na Figura.
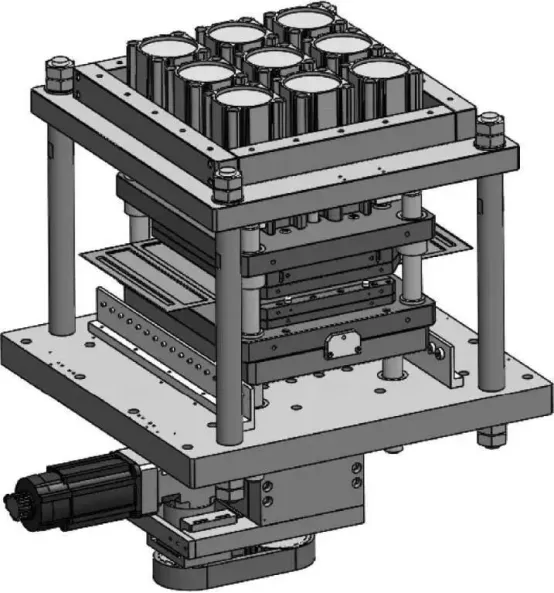
(4) Mecanismo de corte. O mecanismo de corte consiste principalmente em hastes guia, lâminas de corte, assentos de fixação de lâminas, cilindros superiores, cilindros inferiores, mecanismo de remoção de poeira, etc. Sua função e ação são cortar o filme de alumínio-plástico em comprimentos fixos, com um dispositivo de remoção de poeira durante o corte. A lâmina de corte normalmente tem uma vida útil de 300.000 a 500.000 cortes (com um alarme de lembrete de vida útil) e pode ser afiada mais de 10 vezes. A aresta de corte está equipada com um sistema de sucção de poeira durante o corte. O requisito de velocidade do fluxo de ar de sucção é de ≥20 m/s e a precisão de corte para o invólucro de alumínio-plástico é de ±0,2 mm. O mecanismo de corte é mostrado na figura a seguir.
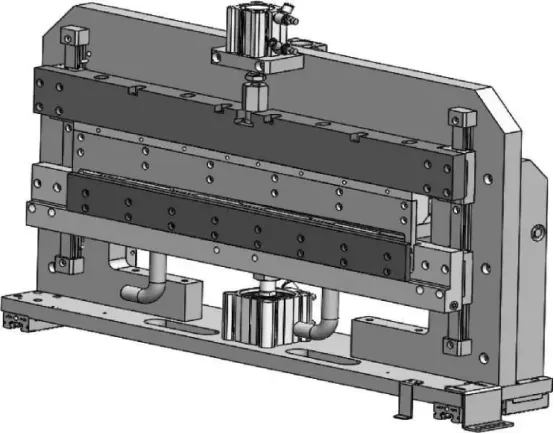
(3)Máquina de embalagem
A máquina de embalagem monta o núcleo da bateria soldado pela máquina de solda de aba e o filme de alumínio-plástico estampado pela máquina de perfuração em uma forma preliminar de bateria. As principais estruturas da máquina de embalagem incluem principalmente a braçadeira da máquina de embalagem, mecanismo de dobra, mecanismo de corte, mecanismo de vedação superior/lateral, etc.
(1) Dispositivo elétrico da máquina de empacotamento. O acessório da máquina de embalagem é um importante suporte para a montagem de filme de alumínio-plástico e células de bateria para completar vários processos. Consiste em cremalheiras, rolamentos angulares, cavidade superior, cavidade inferior, ventosas, blocos de posicionamento, etc. Seu princípio de funcionamento é que a cavidade inferior é fixada no suporte e as ventosas a vácuo são razoavelmente distribuídas; a cavidade superior é invertida pelo mecanismo de inversão do dispositivo elétrico através da cremalheira e do pinhão, que pode atingir os três requisitos de posição de abertura, fechamento e manutenção, e as ventosas a vácuo são razoavelmente distribuídas; filme de alumínio Depois de ser colocada na cavidade do molde, a ventosa a vácuo funciona para determinar a posição do filme de alumínio, e a posição do filme de alumínio permanece inalterada durante o fluxo de cada estação. Como o filme de alumínio-plástico é um corpo de bolsa, a fim de garantir a posição de tamanho relativo entre o poço de filme de alumínio-plástico e o núcleo da bateria, as cavidades superior e inferior são processadas copiando as dimensões externas do núcleo da bateria, e a precisão do processamento pode chegar a ±0,2 mm, a fim de tornar a braçadeira o mais leve possível e garantir os requisitos de resistência, o material é geralmente A6061 e oxidado na superfície, o que é durável. Após a dobra, o alinhamento da borda do filme de alumínio é de ±0,2 mm. Acessório da máquina de embalagem conforme mostrado na figura.
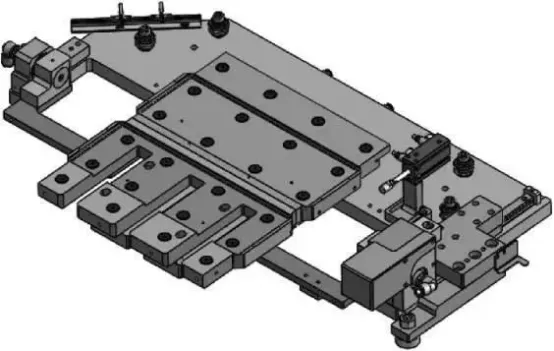
O mecanismo de dobragem consiste principalmente em cilindros de elevação, cilindros de avanço/retração, guias lineares, placas dobráveis, etc. Sua principal função e ação são as seguintes: o cilindro de elevação permanece na posição superior e o servo de avanço/retração empurra a placa dobrável para a posição diretamente acima da linha de dobra do filme de alumínio. O cilindro de elevação então se move para baixo para pressionar o filme de alumínio, alinhando a borda da placa dobrável com a linha de dobra do filme. O dispositivo rotativo fecha e o cilindro que avança / retrátil puxa a placa dobrável, dobrando totalmente o filme de alumínio e se move para a próxima estação de trabalho. Nesta fase, não há células de bateria dentro do filme de alumínio-plástico. A precisão geral do mecanismo de dobragem pode chegar a ±0,2 mm. O mecanismo de dobragem é mostrado na figura a seguir.
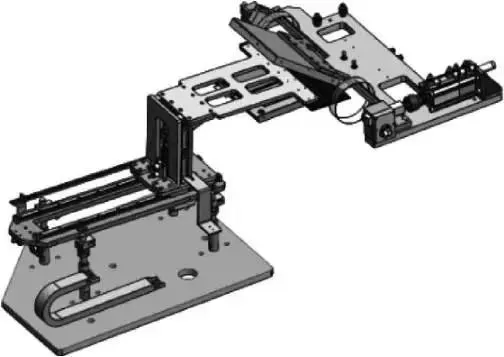
(3) Mecanismo de corte. O mecanismo de corte é usado principalmente para cortar o filme de alumínio-plástico na máquina de embalagem. É composto principalmente por um cilindro de acionamento do cortador superior, um cilindro de acionamento do cortador inferior, um cortador superior, um cortador inferior, um mecanismo de prensagem, um trilho de guia linear, um mecanismo de remoção de poeira e um regulador de pressão. É composto por válvulas, etc., e há um micrômetro na posição de corte para facilitar o ajuste manual. A função e a ação são as seguintes: a plataforma giratória gira uma estação, o cilindro inferior se move, a faca inferior se levanta, o cilindro superior se move, a placa de pressão da mola entra em contato com o filme de alumínio-plástico e, em seguida, corta o filme de alumínio-plástico, e o cilindro reinicia ao mesmo tempo. O mecanismo de corte é mostrado na figura.
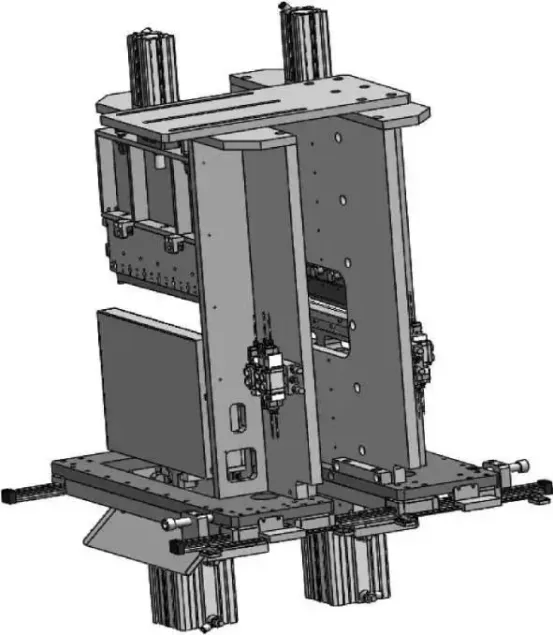
O mecanismo de corte inferior do mecanismo de corte inclui uma caixa receptora de material para coletar o filme de alumínio-plástico cortado. O mecanismo de corte é equipado com uma tampa à prova de poeira que isola a área de corte do ambiente externo durante o processo de corte. A tampa à prova de poeira contém um dispositivo de coleta de poeira, incluindo um dispositivo de sopro e um dispositivo de remoção de poeira por pressão negativa, garantindo que os resíduos de corte e poeira possam ser coletados com eficácia. O requisito de velocidade do fluxo de ar de sucção de poeira é de ≥20 m/s. A precisão de corte da borda superior é de ≤0,2 mm e a precisão do alinhamento da borda superior após o corte também é de ≤0,2 mm. A lâmina de corte tem uma vida útil de 300.000 a 500.000 cortes (com um lembrete para afiação da lâmina) e pode ser afiada mais de 10 vezes. Um micrômetro digital é usado para garantir uma precisão de ajuste de 0,01 mm.
(4) Mecanismo de vedação superior / lateral. O mecanismo de vedação superior/lateral é usado principalmente para a vedação superior ou lateral de baterias. Consiste principalmente em um servo motor, fuso de esferas, guia linear, mecanismo de amortecimento, mecanismo de posicionamento de aba, mecanismo de ajuste fino, cabeça de vedação NAK80, controlador de temperatura, tubo de aquecimento, termopar e outros componentes. A função e a ação são as seguintes: a cabeça de vedação é aquecida usando aquecimento elétrico e a temperatura da cabeça de vedação pode ser ajustada da temperatura ambiente para 250 °C. Durante a operação do equipamento, o desvio geral de temperatura da cabeça de vedação é inferior a ±3°C. A potência do tubo de aquecimento é de 1500W e sua vida útil é de um ano. A precisão do controle de temperatura é de ≤5 °C. Leva menos de 10 minutos para aquecer da temperatura ambiente a 200 °C. O assento de aquecimento do cabeçote de vedação é projetado com uma placa isolante de calor para compensação de temperatura, garantindo que a temperatura permaneça dentro da faixa necessária durante a vedação de alta velocidade. Depois que a bateria gira para esta estação de trabalho, os servomotores superior e inferior acionam simultaneamente o fuso de esferas para fechar as cabeças de vedação superior e inferior para vedação térmica. A faixa de ajuste da pressão de vedação é de 0 a 20kgf/cm2. A cabeça de vedação é projetada com ranhuras de aba. A folga entre o corpo da bateria e a cabeça de vedação é ajustável e há um micrômetro digital para ajuste. O tempo de selagem é ajustável de 0 a 8 segundos com uma precisão de ajuste de 0,1 segundo. A precisão de vedação na área da aba é de ±20μm, enquanto na área sem aba é de ±15μm. O mecanismo de vedação superior/lateral é mostrado na figura a seguir.
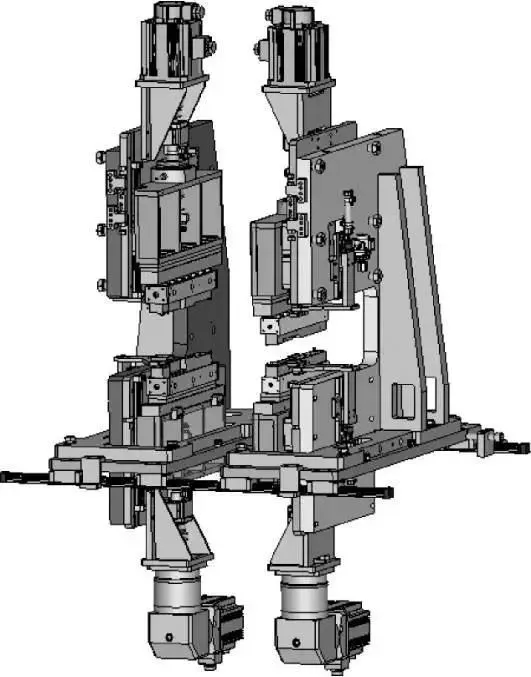