O termo "bateria" geralmente se refere à montagem e fabricação de uma bateria de íons de lítio. Envolve a integração de células de bateria, placas de proteção de bateria, conectores de bateria, papéis de etiqueta e outros componentes por meio de processos de bateria para criar o produto desejado para os clientes.
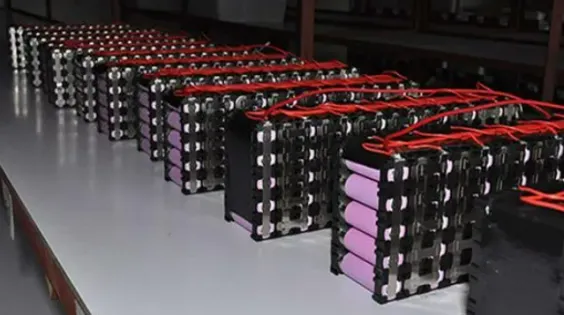
A fabricação de baterias agora se concentra predominantemente nas fábricas de baterias de íons de lítio, que têm seu próprio design estrutural de embalagens, design eletrônico de embalagens e oficinas de produção de embalagens. Eles podem desenvolver e projetar baterias de forma independente de acordo com os requisitos do cliente. Uma vez que os requisitos de personalização da bateria de íons de lítio são confirmados por meio de métodos de bateria, especificações de bateria e amostras de bateria, a linha de produção de embalagens na oficina realiza a produção e o processamento. Depois de passar na inspeção de qualidade, os produtos são enviados.
Para produtos de energia de armazenamento de energia, os pontos-chave do processo de fabricação de baterias de lítio são os seguintes:
- Classificando e combinando grupos
Classificação de bateriasrefere-se à seleção de variáveis apropriadas, como resistência ôhmica da bateria, resistência à polarização, tensão de circuito aberto, capacidade nominal, eficiência de carga-descarga, taxa de autodescarga, etc. Por meio da classificação, as baterias são classificadas em grupos com base em sua consistência nos parâmetros. O principal objetivo é melhorar a consistência interna das baterias após o agrupamento, aumentando assim a eficiência e a vida útil dos módulos de bateria.
Os métodos de classificação de bateria incluem principalmente o método de fator único, o método multifatorial e o método de classificação dinâmica.
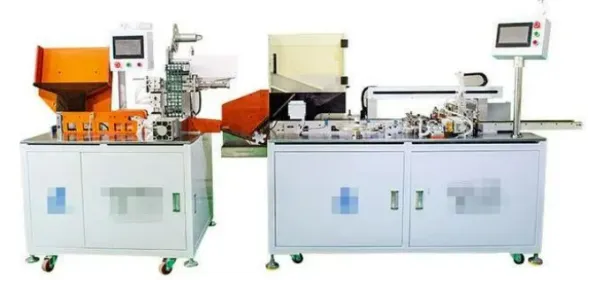
- Um método de montagem de baterias de lítio, incluindo as seguintes etapas:
Teste de capacidade de células de bateria: Instale as células a serem classificadas no equipamento de teste e execute os ciclos de carga e descarga três vezes usando a corrente especificada. No quarto ciclo, carregue a tensão da célula individual em uma faixa de porcentagem definida para a capacidade nominal.
Obtenção de benchmarks de referência de agrupamento: Registre a capacidade de descarga, tempo de carregamento de corrente constante, tempo de carregamento de tensão constante e outros parâmetros das células após o terceiro ciclo.
Classificação da capacidade da célula: Com base na capacidade de descarga da célula no terceiro ciclo como padrão, a capacidade limite inferior é definida e as células com capacidade maior que o limite inferior são selecionadas como células qualificadas;
Agrupamento preliminar de células de bateria: Com base nos parâmetros obtidos de tempo de carregamento de corrente constante e tempo de carregamento de tensão constante, as células da bateria com capacidade qualificada e os mesmos ou semelhantes parâmetros de tempo de carregamento de corrente constante e tensão constante são combinados;
Queda de tensão da célula da bateria: Armazene as baterias montadas em um ambiente definido por um período de tempo para medir sua capacidade de descarga. Depois de determinar os padrões de qualificação de queda de tensão, selecione baterias qualificadas;
Agrupamento final de células de bateria: Selecione as células da bateria com queda de tensão qualificada e use as células com queda de tensão qualificada para o agrupamento final.
- Dispositivo de montagem para células de bateria de lítio, equipado com uma máquina de solda automática.
Ao montar as células da bateria usando o acessório, é importante seguir a sequência de eletrodos positivo e negativo especificada no Procedimento Operacional Padrão (SOP) fornecido pelo engenheiro de PE. Inverter a sequência pode resultar em um curto-circuito. Uma vez que o programa da máquina de solda automática esteja devidamente definido, o acessório é carregado com as células da bateria e a soldagem a ponto automatizada (máquina relacionada) se inicia.
Após a conclusão da soldagem a ponto automatizada, a equipe de inspeção de qualidade precisa realizar verificações pontuais na bateria. Quaisquer pontos de solda perdidos ou inadequados precisam ser soldados novamente para garantir as conexões adequadas.
- Soldagem de bateria de lítio PCM/BMS
PCM ou PCB (Protection Circuit Module ou Circuit Board) é o "coração" de uma bateria de lítio. Protege a bateria de lítio desobrecarga, descarga excessivae curtos-circuitos, evitando explosões, incêndios e danos à bateria.
Para baterias de lítio de baixa tensão (<20 células), um PCM com funcionalidade de balanceamento deve ser selecionado para manter o equilíbrio e a boa vida útil de cada célula. Para baterias de lítio de alta tensão (>20 células), deve-se considerar o uso de um sistema avançado de gerenciamento de bateria (BMS) para monitorar o desempenho de cada célula e garantir uma operação mais segura da bateria.
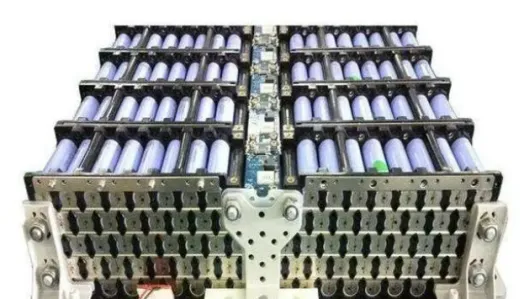
Os funcionários devem usar pulseiras estáticas para evitar danos ao PCM/BMS devido à eletricidade estática.
Existem diferentes etapas, dependendo do design da bateria. Se o projeto envolver soldagem a ponto PCM na bateria, não há necessidade de soldagem. A inspeção de qualidade também é necessária para verificar os pontos de solda por pontos entre o PCM e a bateria.
Se for necessária solda para PCM/BMS ou para conectar parafusos ao pacote, verificações pontuais devem ser realizadas nos pontos de solda e nas conexões dos parafusos para garantir a qualidade. Para fios de coleta de tensão, eles devem ser conectados em sequência de B-, B1... a B+ ou soldado após a remoção do plugue do fio de coleta de tensão. Após a conclusão da soldagem, o plugue de coleta deve ser testado quanto à precisão antes de conectá-lo ao BMS.
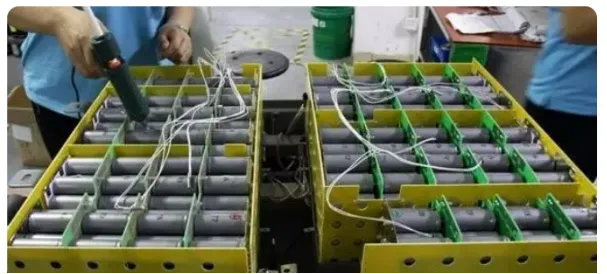
- Semi-acabado produto isolamento
Os fios de coleta de tensão, condutores e fios de saída positivo/negativo precisam ser devidamente fixados e isolados. Os materiais comumente usados para isolamento incluem fita adesiva de alta temperatura, papel de cevada das terras altas, placas epóxi, braçadeiras, etc. É importante ter consciência de segurança e evitar pressão excessiva ou empilhamento nos fios de coleta de tensão ou condutores de saída, pois isso pode causar danos e curtos-circuitos.
- Teste de produto semi-acabado
Depois de adicionar o BMS à bateria, um teste de produto semi-acabado pode ser realizado. Os testes comuns incluem testes simples de carga e descarga, testes de resistência interna do pacote, testes de capacidade do pacote, testes de sobrecarga do pacote, testes de descarga excessiva do pacote, testes de curto-circuito e testes de sobrecorrente. Se houver requisitos especiais, testes adicionais, como testes de alta e baixa temperatura, teste de punção com agulha, teste de queda, teste de névoa salina, etc., podem ser necessários. É importante observar que testes especiais de baterias de lítio podem ser destrutivos, portanto, a amostragem é recomendada.
Deve ser dada atenção à resistência da bateria durante estes ensaios. Por exemplo, durante o teste de sobrecarga da embalagem, o BMS deve ser capaz de suportar alta tensão. Durante o teste de curto-circuito, o BMS deve ser capaz de suportar alta tensão e alta corrente. Durante o teste de sobrecorrente, o BMS deve ser capaz de suportar correntes de pulso e assim por diante.
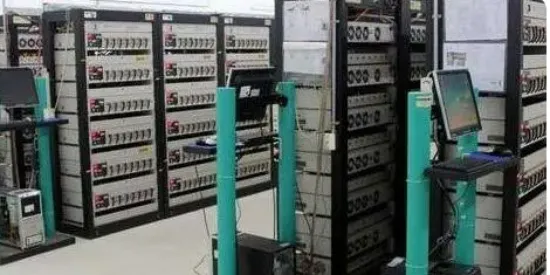
- Packing
Esta etapa também requer consideração do design. No entanto, antes de embalar, é essencial garantir o isolamento dos fios de aquisição de sinal e dos terminais positivo e negativo da bateria.
Para baterias envoltas em PVC, é usada uma máquina termorretrátil. Para baterias seladas com tecnologia ultrassônica, é empregada uma máquina de selagem ultrassônica. As baterias com invólucros externos de metal requerem a montagem do invólucro externo. Ao longo deste processo, é importante manusear a bateria com cuidado, evitando colisões e pressão excessiva. Os fios devem ser bem isolados para evitarcurtos-circuitos.
- Teste de bateria
Os parâmetros de todo o conjunto de testadores são definidos e todo o conjunto de testadores é testado na bateria.
Principais itens de teste: tensão de transporte, resistência interna, carga e descarga simples.
Itens de teste opcionais: sobrecorrente, curto-circuito.
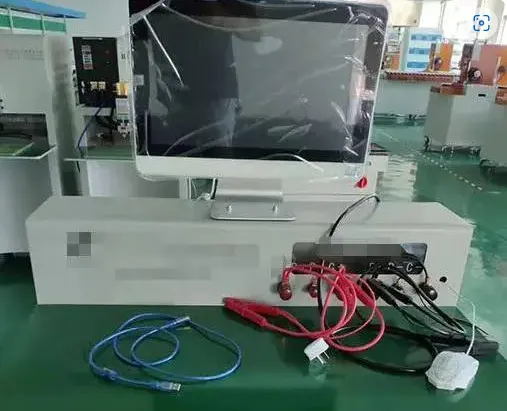
- Embalagem e envio
Embale as caixas de acordo com o tamanho da espuma moldada e não as coloque aleatoriamente. Ao transportar a bateria, você tem mais medo de esvaziar a embalagem interna. Certifique-se de que haja espuma suficiente no interior para amortecimento para evitar danos durante o transporte. Bateria grande, por razões de segurança, você precisa providenciar o envio da moldura de madeira.
Acima, todos os processos e qualidade devem ser rastreados e controlados no local. Cada posição exige funcionários qualificados para realizar um trabalho qualificado, garantindo qualidade e aumentando a velocidade.