Na última década, a indústria de baterias de íons de lítio fez a transição da automação semiautomática para a autônoma e, em seguida, gradualmente para a automação e inteligência completas. Ao longo desse processo, houve mudanças mínimas nos processos de fabricação de baterias. No entanto, com o crescimento contínuo e rápido da demanda de baterias, excedendo 100% ao ano, e as atualizações contínuas nos sistemas de materiais de baterias, os processos de fabricação de baterias inevitavelmente precisam ser atualizados para acomodar mudanças na escala de fabricação e nos sistemas de baterias. Da mesma forma, os equipamentos de bateria, como a "galinha mãe" da indústria de baterias de íons de lítio, também encontraram novas oportunidades para avanços.
Tecnologia de fabricação e tendências de desenvolvimento de equipamentos
No futuro, a tendência de desenvolvimento de baterias de armazenamento de energia mudará para uma maior capacidade de pequenas células individuais. Os equipamentos de íons de lítio precisam garantir precisão na fabricação dessas grandes células, alta eficiência de fabricação e melhorar a compatibilidade e a escalabilidade. Isso requer melhorias correspondentes na precisão de usinagem dos componentes e na precisão de montagem dos módulos.
Para enfrentar os desafios da fabricação de baterias de íons de lítio em larga escala, a eficiência do equipamento precisa ser aprimorada.A eficiência de produção de equipamentos de íons de lítio é melhorada principalmente em dois aspectos. Em primeiro lugar, aumentando a velocidade de produção do equipamento usando estruturas e métodos de controle mais rápidos e estáveis. Em segundo lugar, reduzindo o tempo consumido pelos movimentos dos equipamentos, conhecido como tempo auxiliar.
Por exemplo, a máquina de enrolamento contínuo para separadores desenvolvida pela Geesun Intelligent é um equipamento típico. Anteriormente, cada célula acelerava e era alimentada até a velocidade de enrolamento mais alta, depois desacelerava, parava, cortava o separador, enfiava a agulha e passava para o próximo enrolamento da célula. Após a melhoria, o separador não desacelera e um mecanismo de corte voador é usado para cortar o separador, o que é feito com antecedência durante o processo de desaceleração do eletrodo. Isso reduz o tempo consumido pelo processo de corte do eletrodo e do separador, minimizando efetivamente o tempo auxiliar para quase zero, resultando em uma melhoria geral do tempo do ciclo de produção de 30-60% (dependendo do comprimento do eletrodo). Outro exemplo é a máquina de corte de aba de eletrodo, que aumentou sua velocidade de corte a laser dos anteriores 80-120m/min para 200m/min.
Nessa perspectiva, o avanço e a iteração dos equipamentos de fabricação de íons de lítio estão se movendo em direção a soluções inteligentes em larga escala, de alta precisão, alta confiabilidade e totalmente integradas.
Do ponto de vista da otimização dos processos de fabricação de íons de lítio, equipamentos integrados e totalmente inteligentes oferecem maior estabilidade de produção, maior automação e maior adaptabilidade aos processos de fabricação. Também ajuda as empresas de manufatura a reduzir os custos de mão de obra e espaço, encurtar as ligações do processo e minimizar o desperdício de material, desempenhando um papel fundamental no aumento da eficiência geral.
Integração profunda da tecnologia de materiais e tecnologia de fabricação
Ao longo do processo de fabricação da bateria, envolve a transição das operações de processamento de materiais em nanoescala para a produção e processamento de dispositivos em escala de medidores. No passado, a fabricação de íons de lítio se concentrava principalmente no controle da eficiência, qualidade e custo de fabricação de equipamentos com base na mecânica newtoniana. Os principais parâmetros controlados foram as posições físicas, velocidades, acelerações, inércias, atrito e resistência dos materiais. Esses controles eram relativamente macroscópicos e a visibilidade e a observabilidade do processo eram relativamente fáceis de gerenciar.
Com base no fato de que as baterias envolvem a migração de íons sob a influência de um campo elétrico interno, enquanto externamente, o processo se reflete na transferência de elétrons, é necessário controlar a produção e o uso de baterias de uma perspectiva microscópica usando a mecânica quântica. Isso implica considerar a evolução da estrutura e composição da bateria durante a produção e montagem, bem como os comportamentos de transporte de elétrons e íons, problemas de interface e o efeito da escala de desempenho nas baterias. Mudanças na interface durante o processo de carga-descarga, variações de desempenho e escala e os efeitos de acoplamento entre moléculas e íons internos, efeitos de temperatura e mudanças na forma e volume devem ser levados em consideração para controlar a segurança da bateria, autodescarga, vida útil, densidade de energia e densidade de potência.
Isso requer uma maior consideração da termodinâmica, cinética (cinética de transporte de íons, cinética de transferência de carga, cinética de reação, cinética de transição de fase, etc.) e estabilidade no processo de fabricação de uma perspectiva microscópica.
No entanto, o controle desses processos complexos atualmente carece de um modelo teórico completo no campo da manufatura. Isso se deve aos desafios inerentes ao acoplamento de campo multifísico, dados multielementos e heterogêneos, controle de forma em várias escalas, controle de propriedades intrínsecas e gerenciamento de dados massivos. Os métodos que podem ser empregados incluem aprendizado de máquina e modelagem de otimização com base em análise de tendências qualitativas e modelagem de big data. Ao usar a teoria da mecânica quântica para entender os princípios científicos intrínsecos das baterias, a otimização do processo, a tomada de decisões e o controle podem ser alcançados. Métodos analíticos e técnicas de avaliação podem ser estabelecidos para obter a fabricação de baterias reconfiguráveis, em larga escala e personalizadas. Em última análise, essa abordagem pode abordar questões como migração de íons, geração e transferência de calor, controle de pressão interna, deformação do processo, formação de filme SEI e controle de dendritos de lítio.
Integração de fabricação e mudanças nos princípios de fabricação
A discussão anterior se concentrou nos aspectos microscópicos a serem considerados na fabricação de baterias de uma perspectiva quântica. No contexto das reações eletroquímicas acopladas em baterias de íons de lítio, que envolvem vários campos físicos, uma quantificação dos processos eletroquímicos da bateria pode ser obtida usando variáveis de estado generalizadas, como números adimensionais, densidade de partículas, densidade de defeitos de rede, velocidade de partículas, etc.
Ao empregar técnicas de simulação numérica de dinâmica de partículas suaves multidirecionais, modelos numéricos que consideram a microestrutura de mesoescala dos eletrodos podem ser desenvolvidos. Esses modelos podem simular o campo de concentração de íons, campo potencial sólido-líquido, densidade de corrente de conversão e outros detalhes microscópicos na bateria durante o processo de descarga. Além disso, eles podem analisar e revelar os mecanismos físico-químicos fundamentais dos processos de carga-descarga da bateria e sua correlação com o desempenho macroscópico da bateria, incluindo fatores como tensão de saída e tamanho de partícula de materiais ativos sólidos que constituem os eletrodos.
A fabricação de eletrodos secos, guiada pelos princípios da dinâmica de partículas de mesoescala, envolve a integração de processos como fabricação, mistura, agitação, revestimento, secagem e laminação de eletrodos. A integração de corte e enrolamento a laser, bem como corte e empilhamento a laser em um único equipamento é uma tendência importante. No futuro, prevemos que a produção de células de bateria pode exigir apenas três tipos principais de equipamentos: equipamento de produção de eletrodos, equipamento de montagem e equipamento de teste. No entanto, este é um cenário ideal que requer esforços conjuntos e progresso em materiais, processos e equipamentos. Isso não pode ser alcançado da noite para o dia e exigirá esforços dedicados e diligência dos profissionais de fabricação de baterias.
O principal processo de preparação de eletrodos secos (também conhecido como "revestimento seco") inclui a seleção de ligantes não fibrosos, moagem de bolas de ligantes não fibrosos para granulação e mistura de ligantes não fibrosos, ligantes fibrosos e materiais ativos de eletrodos (cátodo/ânodo) antes da calotagem. Para garantir a plasticidade dos materiais, a mistura é frequentemente aquecida a temperaturas acima de 100°C durante o processo de conformação.
Os aglutinantes não fibrosos usados pela Maxwell incluem fluoreto de polivinilideno e carboximetilcelulose, enquanto o aglutinante fibroso usado principalmente é o politetrafluoretileno. O processamento paralelo é comumente empregado em seus processos de fabricação. Consulte a Figura abaixo para obter uma ilustração do processo de fabricação de eletrodos secos da Tesla.
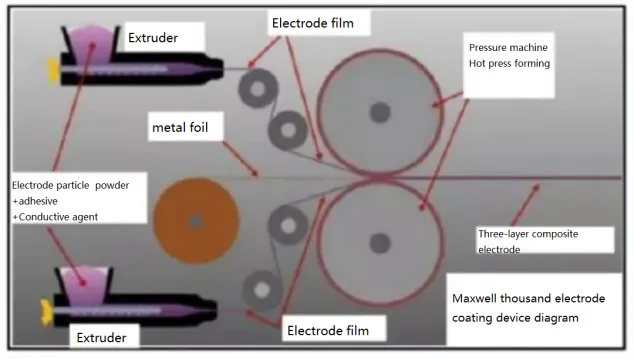
Comparado aos processos tradicionais de eletrodo úmido, o processo de eletrodo seco usado pela Tesla (Maxwell) oferece várias vantagens. Substitui a agitação por moagem de bolas e o revestimento por calandragem, eliminando o processo de secagem após o revestimento úmido. Este método pode economizar solventes, reduzir o tempo de processamento, evitar resíduos de solvente e diminuir a complexidade do equipamento. No entanto, o processo seco tem suas limitações, particularmente na obtenção de dispersão uniforme de materiais ativos, o que é especialmente desafiador para eletrodos de bateria de íons de lítio em comparação com materiais de eletrodos de supercapacitor.
O processo de eletrodo seco da Tesla é ainda mais simples e não requer o uso de solventes. O processo começa com o pó do eletrodo, onde uma pequena quantidade (aproximadamente 5-8%) de aglutinante fino de politetrafluoretileno (PTFE) é misturada com o pó do cátodo. A mistura de pó catódico e aglutinante é então extrudada para formar uma tira fina de material de eletrodo. Esta tira de material de eletrodo extrudado é laminada em um coletor de corrente de folha de metal para produzir o eletrodo final. O processo seco melhora a eficiência da fabricação de eletrodos, encurta as etapas de processamento e abre novas possibilidades para a produção em larga escala de baterias de armazenamento de energia.
Processo de fabricação simplificado e estrutura da bateria
O equipamento usado em cada processo de fabricação de baterias de lítio afeta significativamente o desempenho da bateria. A duração do fluxo do processo da bateria também afeta a consistência e a controlabilidade da preparação da célula. A simplificação dos processos de fabricação de eletrodos e formação de células é um exemplo de sucesso. O desenvolvimento de equipamentos como máquinas integradas de calandragem e corte, máquinas de corte e enrolamento a laser e máquinas de corte e empilhamento a laser simplificou os processos e aprimorou a capacidade de controle de circuito fechado. Essa simplificação não apenas reduz o custo do transporte de materiais devido a rotas complexas, mas também economiza mão de obra.
No desenvolvimento futuro da indústria de baterias, haverá mudanças revolucionárias na otimização do desempenho da bateria e nas estruturas de fabricação. Isso inclui alterações na forma, tamanho e conexões do eletrodo da caixa da bateria com base nos requisitos de desempenho, fabricação e conectividade. Os coletores de corrente internos e as conexões dos eletrodos também podem mudar para atender aos requisitos de reciclagem da bateria.
Tanto a CATL quanto a BYD adotaram abordagens diferentes para agilizar seus processos. Eles utilizam diferentes formas de CTP (Cell to Pack) para encurtar o fluxo do processo. CTP refere-se a pular o estágio do módulo e integrar diretamente as células da bateria ao pacote para aumentar a utilização do volume. Na bateria CTP da CATL, existem vários módulos de bateria, cada um contendo várias células e uma estrutura para acomodar essas células. Eles substituíram módulos menores por maiores. O CTP da BYD, também conhecido como GCTP (Blade Battery), atinge níveis ainda mais altos de eliminação de módulos, onde a bateria blade usa apenas um único módulo grande. Consulte a Tabela abaixo para uma comparação dos processos CATL-CTP e BYD-CTP.
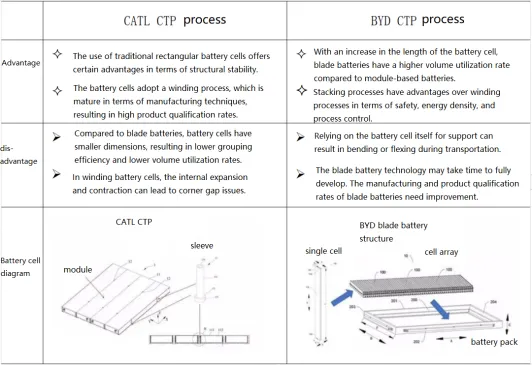
A demanda por baterias de íons de lítio no campo de novas aplicações de energia continua a se expandir. As principais empresas de baterias de íons de lítio visam obter economias de escala e custos mais baixos por meio da expansão contínua da capacidade. Eles têm requisitos mais altos para processos de linha de produção, desempenho e eficiência de produção. O equipamento de íons de lítio desempenha um papel crucial na melhoria da eficiência do processo, taxas de rendimento e eficiência de produção na fabricação de íons de lítio. A capacidade de inovação é a principal competência dos processos de fabricação de baterias. A melhoria contínua e a iteração de equipamentos de íons de lítio, juntamente com novos avanços na tecnologia de fabricação de íons de lítio, exigem estreita colaboração.