Descrição do problema
Orevestimentodos eletrodos de bateria de íons de lítio consiste principalmente em duas partes: revestimento e cozimento. O processo de revestimento determina parâmetros-chave, como largura e quantidade de revestimento, enquanto o processo de cozimento tem um impacto significativo na microestrutura do eletrodo. Além disso, a microestrutura do eletrodo afeta muito a molhabilidade, a adesão e a cinética de difusão dos íons de lítio da bateria. Um defeito comum no cozimento do revestimento é a ocorrência de rachaduras no revestimento, especialmente em eletrodos grossos e eletrodos à base de água.
Análise teórica:
A principal causa de rachaduras no eletrodoRevestimentosdurante o processo de cozimento são forças capilares. Quando um revestimento úmido contendo partículas suspensas seca, inicialmente todas as partículas são suspensas no solvente (Figura 1a). À medida que o solvente evapora, a interface gás-líquido atinge a superfície do revestimento durante o cozimento (Figura 1b). O menisco curvo na interface ar-solvente entre as partículas gera forças capilares, exercendo forças compressivas sobre as partículas perpendiculares à interface gás-líquido. Com o cozimento adicional, a interface gás-líquido penetra no interior do revestimento e as forças capilares aumentam à medida que o solvente evapora (Figura 1c), aplicando forças compressivas adicionais nas partículas. Eventualmente, o revestimento racha em certos pontos críticos para aliviar o estresse de cozimento (Figura 1d).

Figura 1: Processo de rachadura por cozimento do revestimento
O eletrodo tem uma espessura máxima sem rachaduras, conhecida como espessura crítica de rachaduras. Quando a espessura está abaixo da espessura crítica de rachaduras, o revestimento não racha. No entanto, quando a espessura excede esse valor crítico, o revestimento racha. A fórmula de estimativa para a espessura crítica da fissuração, denotada como hmax, é a seguinte:
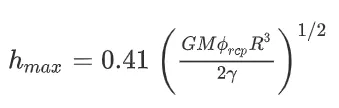
Na equação, G representa o módulo de cisalhamento das partículas, M representa o número de coordenação, φrcp denota a fração de volume de partículas compactadas aleatoriamente, R representa o raio da partícula e γ representa a tensão superficial entre o solvente e o ar.
Experiência de Processo
(1)Na pasta de bateria de lítio, a água é comumente usada como solvente para oeletrodo negativo, enquanto o NMP (N-metil-2-pirrolidona) é usado como solvente para o eletrodo positivo. Devido à maior tensão superficial da água (72,80 mN/m, 20°C) em comparação com o NMP (40,79 mN/m, 20°C), o processo de cozimento da pasta aquosa resulta em maior pressão capilar, tornando-a mais propensa a rachaduras no revestimento (Figura 2-5).
(2)Na preparação de um determinado eletrodo de bateria de lítio submicrométrico, o PVDF (fluoreto de polivinilideno) é usado como aglutinante e o NMP (N-metil-2-pirrolidona) como solvente. Quando a espessura do eletrodo aumenta, mesmo que o eletrodo seja seco ao ar em temperatura ambiente e depois seco a vácuo em um forno a vácuo, ocorrem rachaduras. No entanto, quando o aglutinante é trocado por poliacrilamida, o eletrodo não racha durante o cozimento. Isso indica que o ligante também influencia a rachadura do eletrodo, conforme mostrado nas Figuras 3 e 5. O ligante afeta o ambiente circundante das partículas, o que pode causar alterações nos parâmetros M, φ e γ na equação, afetando assim a tendência de rachadura do eletrodo.
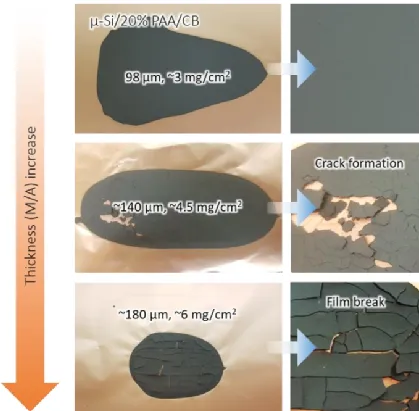
A Figura 2 mostra a espessura crítica de fissuração do eletrodo composto de Si/PAA/agente condutor de tamanho micro. Em todos os eletrodos, a composição de Si (2μm), PAA e agente condutor é de 80%, 10% e 10%, respectivamente, com água como solvente. Nenhuma rachadura é observada quando a espessura do revestimento está abaixo de aproximadamente 100μm (carga de área de revestimento de 3mg/cm2). No entanto, quando a espessura do revestimento excede 140μm (carga de área de revestimento de 4,5mg/cm2), aparecem rachaduras no eletrodo.
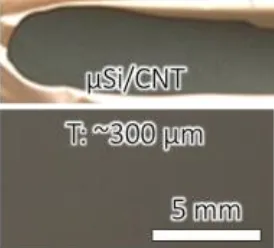
A Figura 3 ilustra que quando nenhum aglutinante é adicionado ao eletrodo e o agente condutor CNT é usado para fornecer alguma coesão, a espessura crítica de fissuração do eletrodo de silício é de 300μm.
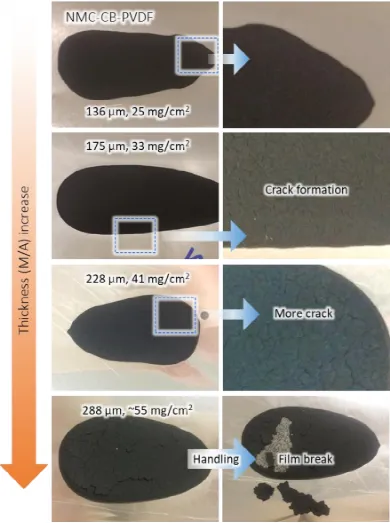
A Figura 4 mostra a espessura crítica de fissuração (175μm) do eletrodo composto de níquel-cobalto-manganês (NMC)/PVDF/agente condutor. A composição de NMC: PVDF: CB no eletrodo é de 90%, 5% e 5%, respectivamente, com NMP como solvente. Quando a espessura do eletrodo é inferior a 175μm, não são observadas rachaduras. No entanto, eletrodos mais grossos são mais propensos a rachaduras e delaminação do coletor de corrente.
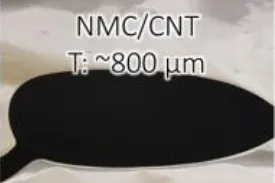
A Figura 5 ilustra que quando nenhum aglutinante é adicionado ao eletrodo e o agente condutor CNT é usado para fornecer alguma coesão, a espessura crítica de fissuração do eletrodo de material ternário é de 800μm.
Solução:
(1)Use uma mistura de água/IPA (álcool isopropílico, tensão superficial 23.00 mN/m, 20°C) como solvente para o eletrodochorumepara reduzir a tensão superficial, evitando rachaduras e melhorando o desempenho do eletrodo. A tensão superficial do solvente misturado pode ser estimada usando a seguinte fórmula:

Onde x1 é a fração molar da água, x2 é a fração molar do IPA. γ1 é a tensão superficial da água e γ2 é a tensão superficial do IPA.
(2) Considere o uso de NMP ou outros solventes com menor tensão superficial para evitar rachaduras. A tensão superficial pode ser caracterizada medindo o ângulo de contato entre o solvente ou uma solução contendo o aglutinante e o substrato.

A Figura 6 ilustra a diminuição gradual do ângulo de contato e da tensão superficial de (a) para (d).
(3) A compactação pode melhorar a qualidade do revestimento, reduzindo o tamanho das rachaduras. No entanto, não pode eliminar completamente as rachaduras (como mostrado na Figura 7).
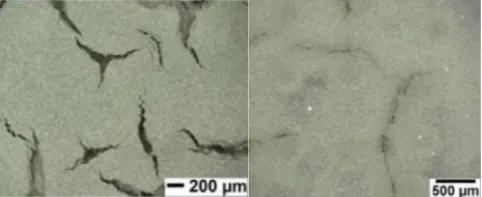
Figura 7 Comparação antes (imagem à esquerda) e depois (imagem à direita) da compactação do eletrodo
(4) Substitua o aglutinante para evitar rachaduras.