1. Qual é a razão para furos no revestimento do eletrodo negativo? É porque os materiais não estão bem dispersos? É possível que a distribuição do tamanho das partículas do material não seja boa?
A ocorrência de furos no revestimento negativo do eletrodo pode ser atribuída a vários fatores:
1.1 Impurezas na superfície da folha.
1.2 Má dispersão do agente condutor.
1.3 Dispersão inadequada do material ativo do eletrodo negativo.
1.4 Impurezas em certos componentes da formulação.
1.5 Distribuição não uniforme e difícil dispersão das partículas do agente condutor.
1.6 Distribuição não uniforme e difícil dispersão das partículas do eletrodo negativo.
1.7 Problemas de qualidade com os próprios materiais de formulação.
1.8 Pó seco residual no tanque de mistura devido à limpeza incompleta.
Para determinar as causas específicas, é necessário realizar monitoramento e análise do processo. Em relação à questão das manchas pretas no separador, encontrei-a há muitos anos. Em primeiro lugar, darei uma breve resposta. Por favor, corrija-me se eu estiver errado. Na verdade, é causado por alta temperatura localizada no separador devido à descarga de polarização durante a operação da bateria. Essa descarga de polarização é resultado de materiais e fatores relacionados ao processo, onde partículas de material ativo se ligam ao rolo de gelatina e causam descarga de polarização durante o carregamento da bateria. Para evitar esses problemas, é importante adotar processos de lama apropriados para lidar com a adesão entre o material ativo e o coletor de corrente. Além disso, deve-se tomar cuidado durante a fabricação do eletrodo e a montagem da bateria para evitar o desprendimento do pó. A adição de certos aditivos durante o processo de revestimento, que não afetam o desempenho da bateria, pode melhorar as propriedades específicas do eletrodo. Esses aditivos também podem ser incluídos no eletrólito para obter efeitos de consolidação. A alta temperatura localizada no separador é de fato causada pela não uniformidade do eletrodo, o que pode ser considerado uma forma de microcurto-circuito. Microcurtos-circuitos podem levar a alta temperatura localizada e potencial desprendimento do pó do eletrodo negativo.
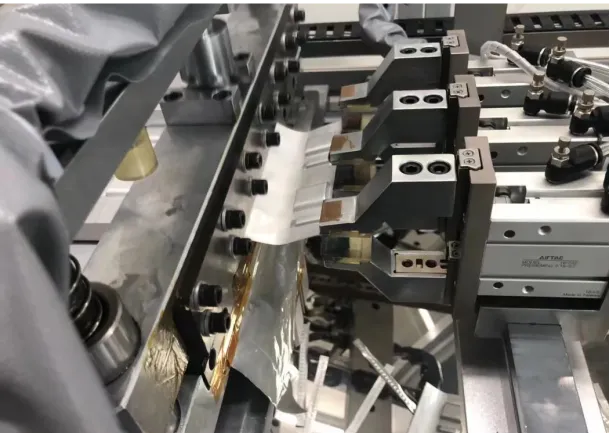
2. Quais são as causas da resistência interna excessiva da bateria?
Em termos de fatores de processo:
2.1 Agente condutor insuficiente na formulação de eletrodo positivo (baixa condutividade entre materiais, pois o próprio lítio-cobalto tem condutividade muito baixa).
2.2 Aglutinante excessivo na formulação de eletrodo positivo (os aglutinantes são geralmente materiais poliméricos com fortes propriedades de isolamento).
2.3 Aglutinante excessivo na formulação de eletrodo negativo (os aglutinantes são geralmente materiais poliméricos com fortes propriedades de isolamento).
2.4 Dispersão não uniforme dos ingredientes.
2.5 Dissolução incompleta de solventes de aglutinantes durante a mistura de ingredientes (não pode se dissolver completamente em NMP ou água).
2.6 Revestimento excessivo e densidade superficial da pasta (aumento da distância de migração de íons).
2.7 Densidade de compactação excessiva, sobrepressão durante a calandragem (pressão excessiva de calandragem pode danificar a estrutura dos materiais ativos).
2.8 Fracosoldagemde abas de eletrodo positivas, resultando em soldagem virtual.
2.9 Soldagem fraca ou rebitagem de abas de eletrodos negativos, resultando em soldagem ou desprendimento virtual.
2.10 Enrolamento solto, célula de enrolamento relaxada (distância aumentada entre as folhas de eletrodo positivo e negativo).
2.11 Soldagem fraca de abas de eletrodo positivo ao invólucro.
2.12 Soldagem fraca de abas de eletrodo negativas na coluna de eletrodos.
2.13 Temperatura excessiva de cozimento das baterias, causando encolhimento do separador (reduzindo o tamanho dos poros).
2.14 Injeção insuficiente de eletrólitos (condutividade reduzida, aumento da resistência interna após o ciclo!).
2.15 Tempo de espera insuficiente após injeção de eletrólitos, infiltração incompleta de eletrólitos.
2.16 Ativação incompleta durante a formação.
2.17 Vazamento excessivo de eletrólitos durante o processo de formação.
2.18 Controle inadequado da umidade durante a produção, causando inchaço da bateria.
2.19 Vol de carga excessivotage configuração, levando aSobrecarga.
2.20 Ambiente de armazenamento inadequado para baterias.
Em relação aos fatores materiais:
2.21 Alta resistência do material do eletrodo positivo (baixa condutividade, como fosfato de ferro e lítio).
2.22 Influência do material separador (espessura, baixa porosidade, tamanho pequeno dos poros).
2.23 Influência do material eletrolítico (baixa condutividade, alta viscosidade).
2.24 Influência do material aglutinante de PVDF no eletrodo positivo (quantidade excessiva ou alto peso molecular).
2.25 Influência do material do agente condutor no eletrodo positivo (baixa condutividade, alta resistência).
2.26 Influência dos materiais positivos e negativos da aba do eletrodo (espessura fina, baixa condutividade, espessura irregular, baixa pureza do material).
2.27 Baixa condutividade da folha de cobre ou material de folha de alumínio, ou presença de óxidos superficiais.
2.28 Alta resistência de contato na rebitagem da placa de cobertura e da coluna de eletrodos.
2.29 Alta resistência do material do eletrodo negativo.
Outros fatores:
2.30 Desvio no equipamento de teste de resistência interna.
2.31. Erro humano nas operações.
3.As folhas de eletrodos são revestidas de forma desigual. A quais questões devemos prestar atenção?
Esse problema é bastante comum e relativamente fácil de resolver. No entanto, muitos operadores de revestimento não são bons em resumir, o que leva a considerar certos problemas existentes como fenômenos normais e inevitáveis. Primeiro, é importante entender os fatores que afetam a densidade da superfície do revestimento e os fatores que influenciam o valor estável da densidade da superfície para resolver o problema de forma eficaz. Os fatores que influenciam a densidade da superfície do revestimento incluem:
3.1 Fatores materiais
3.2 Formulação
3.3 Mistura e mistura
3.4 Ambiente de revestimento
3.5 Lâmina raspadora
3.6 Viscosidade da pasta
3.7 Velocidade da folha de eletrodo
3.8 Planicidade da superfície
3.9 Precisão da máquina de revestimento
3.10 Fluxo de ar do forno
3.11 Tensão do revestimento, etc.
Os fatores que afetam a uniformidade da folha de eletrodo incluem:
3.12 Qualidade da pasta
3.13 Viscosidade da pasta
3.14 Velocidade da folha de eletrodo
3.15 Tensão da folha
3.16 Método de equilíbrio de tensão
3.17 Comprimento de tração do revestimento
3.18 Ruído
3.19 Planicidade da superfície
3.20 Uniformidade da lâmina raspadora
3.21 Uniformidade da folha, etc.
Estes são apenas alguns dos fatores listados, sendo necessário analisar a situação específica e eliminar sistematicamente os fatores que causam densidade superficial anormal.
4.Existe alguma razão especial pela qual os coletores de corrente dos eletrodos positivo e negativo são feitos de folha de alumínio e folha de cobre, respectivamente? Existe algum problema em usá-lo ao contrário?Mquaisquer documentos usando malha de aço inoxidável diretamente. Existe alguma diferença?
4.1 A escolha de usar cobre e alumínio como coletores de corrente deve-se principalmente à sua boa condutividade, textura macia (que pode facilitar a colagem), relativa comunalidade e custo-benefício. Além disso, tanto o cobre quanto o alumínio podem formar uma camada protetora de óxido em suas superfícies.
4.2 A camada de óxido na superfície do cobre é um semicondutor e permite a condução de elétrons. Se a camada de óxido for muito espessa, aumenta a impedância. Por outro lado, a camada de óxido do alumínio, conhecida como óxido de alumínio, é um isolante e não conduz eletricidade. No entanto, devido à sua magreza, a condução de elétrons pode ocorrer por meio de efeitos de tunelamento. Se a camada de óxido no alumínio for muito espessa, pode resultar em condutividade desigual ou até mesmo isolamento. Geralmente, é recomendado limpar as superfícies dos coletores atuais antes de usar para remover camadas espessas de óleo e óxido.
4.3 O eletrodo positivo tem um potencial maior e a fina camada de óxido do alumínio é altamente densa, o que ajuda a evitar a oxidação do coletor de corrente. Em contraste, a camada de óxido no cobre é relativamente porosa. Para evitar a oxidação, é melhor manter o potencial mais baixo. Além disso, o lítio tem dificuldade em formar ligas de lítio-cobre em baixos potenciais. No entanto, se houver uma quantidade significativa de oxidação na superfície do cobre, o lítio pode reagir com o óxido de cobre para formar ligas de lítio-cobre em potenciais ligeiramente mais altos. As folhas de alumínio não devem ser usadas como eletrodos negativos, pois podem sofrer ligas com lítio para formar ligas LiAl em baixos potenciais.
4.4 É importante que os colecionadores atuais tenham composições puras. As impurezas no alumínio podem levar à formação de filmes de superfície não densos e corrosão localizada e, em casos graves, à formação de ligas de LiAl devido ao dano do filme de superfície. As malhas de cobre devem ser limpas com bissulfato e enxaguadas com água deionizada antes de assar, enquanto as malhas de alumínio devem ser limpas com sais de amônio e enxaguadas com água deionizada antes de assar. Esta preparação ajuda a obter uma boa condutividade no revestimento da malha.
5. Ao medir o curto-circuito do rolo de gelatina do enrolamento, o testador de curto-circuito da bateria usado pode testar com precisão a célula de curto-circuito em que tensão. Além disso, qual é o princípio de quebra de alta tensão do testador de curto-circuito?
A tensão usada para testar curtos-circuitos em células de bateria depende de vários fatores, incluindo:
5.1 O processo de fabricação e experiência da empresa: Diferentes empresas podem ter diferentes padrões e práticas para testes de tensão com base em seu nível de especialização.
5.2 O projeto estrutural da própria bateria: Os componentes internos e a construção da bateria podem influenciar a tensão necessária para testar curtos-circuitos.
5.3 O material da membrana (separador) usado na bateria: As propriedades do material da membrana podem afetar a tensão necessária paracurto-circuitoteste.
5.4 O uso pretendido da bateria: Diferentes aplicações podem exigir diferentes voltage níveis para testes de curto-circuito.
Esses fatores podem ser classificados em ordem de importância da seguinte forma: 1 > 4 > 3 > 2. Isso significa que o processo de fabricação e a experiência da empresa têm a maior influência na determinação da tensão para testes de curto-circuito.
Em termos simples, o princípio de quebra é que, se houver pontos fracos potenciais, como poeira, partículas, poros maiores da membrana ou rebarbas entre as folhas de eletrodos e o separador, esses pontos fracos podem criar uma resistência interna mais baixa entre os eletrodos positivo e negativo. Sob uma tensão fixa mais alta, esses pontos fracos podem facilitar a ionização do ar, levando à geração de um arco elétrico. Alternativamente, se os eletrodos positivo e negativo já estiverem em curto-circuito e houver um pequeno ponto de contato, uma alta corrente pode passar por esses pequenos pontos de contato instantaneamente, convertendo energia elétrica em energia térmica, resultando em fusão da membrana ou quebra instantânea.
6. Qual é o impacto do tamanho da partícula do material na corrente de descarga?
Em termos simples, o tamanho de partícula menor geralmente leva a uma melhor condutividade, enquanto o tamanho de partícula maior resulta em menor condutividade. Consequentemente, os materiais de alta taxa geralmente consistem em pequenas partículas com alta condutividade. No entanto, embora essa análise seja verdadeira em teoria, a implementação prática de alcançar alta condutividade em materiais de tamanho de partícula pequeno é uma tarefa desafiadora, especialmente para materiais em nanoescala. Além disso, materiais com tamanhos de partículas pequenos tendem a ter menor densidade de compactação, o que se traduz em capacidades de volume menores.
7. Depois que os eletrodos positivo e negativo foram rolados, eles se recuperaram em 10um após serem cozidos por 12 horas e armazenados por um dia. Por que há uma recuperação tão grande?
Existem dois fatores fundamentais de influência: material e processo.
7.1 Material: As propriedades do material determinam o coeficiente de rebote. Diferentes materiais têm diferentes coeficientes de rebote. Para o mesmo material, diferentes formulações podem resultar em diferentes coeficientes de rebote. Além disso, para o mesmo material e formulação, variar a espessura da chapa prensada também pode levar a diferentes coeficientes de rebote.
7.2 Processo: O controle deficiente do processo também pode contribuir para a recuperação. Fatores como tempo de armazenamento, temperatura, pressão, umidade,empilhamento método, estresse interno, equipamento e muito mais podem influenciar o rebote.
8.Como resolver o problema de vazamento de baterias cilíndricas?
Vedação de baterias cilíndricas após eletrólitoinjecçãoé um aspecto desafiador do processo de vedação. Atualmente, existem vários métodos usados para vedar baterias cilíndricas:
8.1 Vedação de soldagem a laser
8.2 Vedação com junta ou O-ring
8.3 Vedação adesiva
8.4 Vedação por vibração ultrassônica
8.5 Combinações de dois ou mais dos métodos de vedação acima
8.6 Outros métodos de vedação
Existem vários fatores que podem causar vazamento de líquido em baterias cilíndricas seladas:
8.7 Vedação insuficiente: Isso pode ocorrer devido à deformação ou contaminação na área de vedação, resultando em má vedação.
8.8 Estabilidade de vedação: Mesmo que a vedação inicial seja satisfatória, se a área de vedação for facilmente danificada posteriormente, isso pode levar ao vazamento de líquido.
8.9 Geração de gás durante a formação ou teste: Se o gás for produzido durante o processo de formação e atingir a tensão máxima que a vedação pode suportar, pode causar um impacto na vedação, levando ao vazamento de líquido. Isso é diferente do segundo ponto porque não é um defeito na vedação, mas sim uma pressão interna excessiva que causa danos à vedação.
8.10 Outras vias de vazamento: Pode haver fatores ou caminhos adicionais que contribuem para o vazamento de líquido.
Para lidar com o vazamento de líquido, é crucial identificar as causas subjacentes. Uma vez identificadas as causas raiz, fica mais fácil encontrar soluções apropriadas. No entanto, o desafio está em identificar as causas, pois avaliar a eficácia da vedação das baterias cilíndricas é difícil, muitas vezes exigindo testes destrutivos ou amostragem aleatória.
9.Durante o experimento, o eletrólito era excessivo. Sem transbordar, o excesso de eletrólito afetará o desempenho da bateria?
Existem várias situações em que o eletrólito não transborda: 1. O eletrólito está certo 2. O eletrólito é ligeiramente excessivo 3. O eletrólito é excessivamente grande, mas não atinge o limite 4. O eletrólito é excessivamente grande e está próximo do limite 5. O eletrólito está cheio até o limite, OK A primeira situação de vedação é a situação ideal e não há problema. No segundo caso, um pequeno excesso às vezes é um problema de precisão e, às vezes, é um problema de design. Geralmente, o design é excessivo. No terceiro caso, não há problema, é apenas um desperdício de custo. A quarta situação é um pouco perigosa. Porque durante o uso ou teste da bateria, haverá vários motivos: o eletrólito se decompõe e produz algum gás; a bateria aquecerá e produzirá expansão térmica; As duas situações acima podem facilmente fazer com que o invólucro da bateria inche (também chamado de deformação) ou vaze. fluido, o que aumenta o risco de segurança da bateria. A quinta situação é na verdade uma versão aprimorada da quarta situação e é ainda mais perigosa. Para ser mais exagerado, os líquidos também podem se tornar baterias. Ou seja, os eletrodos positivo e negativo são inseridos em um recipiente contendo uma grande quantidade de eletrólito ao mesmo tempo (como um béquer de 500ML). Neste momento, os eletrodos positivo e negativo podem ser carregados e descarregados. Também é uma bateria, então o excesso de eletrólito aqui não é apenas um pouco. O eletrólito é apenas um meio que conduz eletricidade. No entanto, o volume da bateria é limitado. Dentro do volume limitado, é natural considerar as questões de utilização e deformação do espaço.
10.Se a quantidade de líquido injetado for muito pequena, isso causará uma concha de tambor depois que a bateria for dividida?
Só posso dizer que não é certo, depende de quão pequeno é o volume de injeção. 1. Se a célula da bateria estiver completamente infiltrada pelo eletrólito, mas não houver resíduos, a bateria não inchará depois que o volume for dividido; 2. Se a célula da bateria estiver completamente infiltrada pelo eletrólito, há uma pequena quantidade de resíduo, mas é mais líquido do que os requisitos da sua empresa. A quantidade deve ser menor (é claro, esse requisito não é necessariamente o valor ideal, há um pequeno desvio), e a bateria dividida em capacidade não inchará neste momento; 3. Se a célula da bateria estiver completamente encharcada pelo eletrólito, haverá uma grande quantidade de resíduo de eletrólito, mas sua empresa A necessidade da quantidade de injeção de líquido é maior do que a quantidade real. Neste momento, a chamada quantidade insuficiente de injeção de líquido é apenas um conceito da empresa e não reflete verdadeiramente a adequação da quantidade real de injeção de líquido da bateria. A bateria com capacidade diferente não possui um invólucro protuberante;4. O volume de injeção substancial é insuficiente. Isso também depende do grau. Se o eletrólito mal consegue se infiltrar na célula da bateria, o invólucro pode ou não inchar após a divisão do volume, mas a probabilidade de o invólucro da bateria inchar após a divisão do volume é maior; se a quantidade de líquido injetado na célula da bateria for seriamente insuficiente, a bateria será formada A energia elétrica neste momento não pode ser convertida em energia química. Neste momento, a probabilidade do invólucro do tambor da célula da bateria de capacidade dividida é de quase 100%. Então, podemos fazer o seguinte resumo: Suponha que o volume ideal real de injeção de líquido da bateria seja Mg. Se o volume de injeção de líquido for muito pequeno, ele pode ser dividido nas seguintes situações: 1. Volume de injeção de líquido = M: a bateria está normal 2. O volume de injeção de líquido é ligeiramente menor que M: A capacidade da bateria não está saliente. A capacidade pode ser normal ou ligeiramente inferior ao valor do projeto. A probabilidade de abaulamento circulatório aumenta e o desempenho do ciclo piora. 3. O volume de injeção de líquido é muito menor que M: a taxa de abaulamento da capacidade da bateria é bastante alta. , a bateria tem baixa capacidade e estabilidade de ciclo extremamente baixa. Geralmente, a capacidade é inferior a 80% em dezenas de semanas. 4. M = 0, a bateria não tem invólucro protuberante e nenhuma capacidade.