Durante o processo de fabricação de baterias de íons de lítio, existem três fatores cruciais que devem ser rigorosamente controlados: poeira, partículas metálicas e umidade. O mau controle de poeira e partículas metálicas pode levar diretamente acurtos-circuitos internose acidentes de incêndio na bateria. Da mesma forma, o controle inadequado da umidade também pode causar danos significativos ao desempenho da bateria e resultar em sérios acidentes de qualidade. Portanto, é essencial manter um controle rigoroso sobre o teor de água de materiais-chave, como eletrodos, separadores e eletrólitos durante todo o processo de fabricação, sem qualquer relaxamento. A seguir, forneceremos uma explicação detalhada de três aspectos: os perigos da umidade nas baterias de lítio, as fontes de umidade durante oProcesso de fabricaçãoe o controle da umidade durante o processo de fabricação.
01O dano da umidade às baterias de lítio
- Bateria saliente e vazamento
Se o teor de umidade em uma bateria de íons de lítio for muito alto, ela pode reagir com o sal de lítio no eletrólito, gerando HF (fluoreto de hidrogênio):
H2O + LiPF6 → POF3 + LiF + 2HF
O fluoreto de hidrogênio (HF) é um ácido altamente corrosivo que pode causar danos significativos ao desempenho da bateria. O HF pode corroer os componentes metálicos internos da bateria, o invólucro da bateria e as vedações, levando a vazamentos e, por fim, causando a ruptura da bateria.
O HF também pode interromper o filme de interface de eletrólito sólido (SEI) dentro da bateria. HF pode reagir com os principais componentes do filme SEI:ROCO2Li + HF → ROCO2H + LiFLi2CO3 + 2HF → H2CO3 + 2LiF
Finalmente, a formação de precipitados de LiF dentro da bateria leva a reações químicas irreversíveis entre os íons de lítio e o eletrodo negativo, resultando no consumo de íons de lítio ativos e na redução da energia da bateria.
Quando há uma quantidade significativa de umidade, a geração de gás aumenta, levando a um aumento na pressão interna dentro da bateria. Isso pode resultar na deformação da bateria devido à força aplicada, levando a riscos como inchaço e vazamento da bateria.
Casos de inchaço da bateria ou abertura da tampa do dispositivo, comumente encontrados em smartphones ou produtos eletrônicos digitais no mercado, são causados principalmente por alto teor de umidade e geração de gás na bateria de íons de lítio.
- A resistência interna da bateria aumenta
A resistência interna é um dos parâmetros de desempenho mais importantes de uma bateria. Ele serve como um indicador primário da facilidade ou dificuldade de transporte de íons e elétrons dentro da bateria, impactando diretamente o ciclo de vida e o status operacional da bateria. Uma resistência interna mais baixa resulta em uma queda de tensão mais baixa durante a descarga da bateria, permitindo uma maior saída de energia.
Quando o teor de água aumenta, pode levar à formação de precipitados de POF3 e LiF na superfície do filme de interface eletrolítica sólida (SEI) na bateria. Isso interrompe a compactação e uniformidade do filme SEI, aumentando gradualmente a resistência interna da bateria. Consequentemente, a capacidade de descarga da bateria diminui continuamente.
- Ciclo de vida reduzido
Quando o teor de água é muito alto, danifica o filme SEI da bateria, levando a um aumento gradual da resistência interna. Como resultado, a capacidade de descarga da bateria diminui e o tempo de uso por carga completa também se torna mais curto. O número de ciclos de carga e descarga que a bateria pode sofrer antes de sofrer degradação diminui naturalmente, levando a uma vida útil geral mais curta da bateria.
02 Fontes de umidade no processo de produção de baterias de lítio
-
Umidade trazida por matérias-primas
- 1Materiais de eletrodo positivo e negativo:Os materiais ativos nos eletrodos positivo e negativo das baterias consistem em partículas em micro e nanoescala, que são altamente propensas a absorver umidade do ar. Isso é particularmente verdadeiro para materiais de eletrodos positivos ternários ou binários com alto teor de níquel (Ni), pois eles têm uma área de superfície relativamente grande que facilita a absorção de umidade e reações subsequentes. Depois que os eletrodos são revestidos, se forem armazenados em um ambiente de alta umidade, o revestimento da superfície dos eletrodos pode absorver rapidamente a umidade do ar.
- 2Eletrólito:O componente solvente no eletrólito pode sofrer reações químicas com moléculas de água. Além disso, os sais de lítio soluto no eletrólito também são propensos a absorver umidade e sofrer reações químicas. Como resultado, há uma certa quantidade de conteúdo de água presente no eletrólito. Se o eletrólito for armazenado por um longo período ou em um ambiente de alta temperatura, o teor de água no eletrólito pode aumentar.
- 3Separador:O separador é um filme plástico poroso (feito de material PP/PE), e tem uma capacidade significativa de absorção de água.
- Umidade adicionada à polpa da folha do eletrodo:Durante a preparação da pasta do eletrodo negativo, a água é adicionada e misturada com as matérias-primas antes do processo de revestimento. Como resultado, a própria folha de eletrodo negativo contém água. No processo de revestimento subsequente, embora haja aquecimento e secagem envolvidos, uma quantidade significativa de umidade ainda é absorvida no revestimento da folha de eletrodo.
O teor de umidade no ar é geralmente medido usando a umidade relativa. A umidade relativa do ar pode variar significativamente dependendo das diferentes estações e condições climáticas. Na primavera e no verão, o ar tende a ser mais úmido, com umidade relativa superior a 60%. No outono e inverno, o ar é relativamente seco, com umidade mais baixa abaixo de 40%. Em dias chuvosos, a umidade do ar é maior, enquanto em dias ensolarados, a umidade do ar é menor. Portanto, o teor de umidade no ar varia dependendo dos diferentes níveis de umidade relativa.
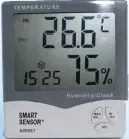
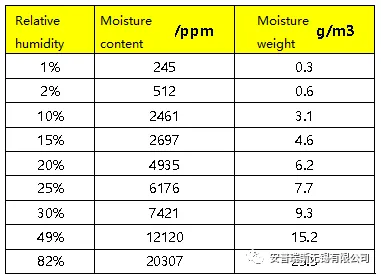
Água produzida pelo corpo humano (suor do corpo humano, respiração exalada, água após lavar as mãos)
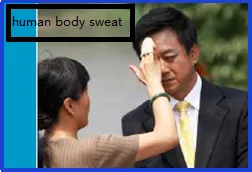
Umidade trazida por vários materiais auxiliares e papéis (caixas, trapos, relatórios)
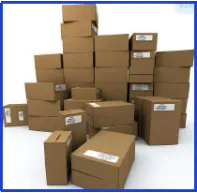
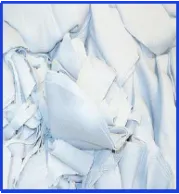
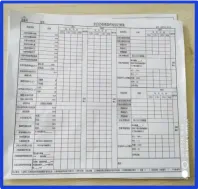
03Controle de umidade durante o processo de produção de baterias de lítio
1.Controle rigorosamente a umidade ambiental na oficina de produção
1.1 Na oficina de produção de eletrodos, durante a mistura da pasta, a umidade relativa deve ser de ≤10%.
1.2 Na oficina de produção de eletrodos, durante o revestimento (cabeça e cauda) e prensagem do rolo, a umidade do ponto de orvalho deve ser de ≤-10 °C DP.
1.3 Na oficina de produção de eletrodos, durante o corte, a umidade relativa deve ser de ≤10%.
1.4 Na oficina de empilhamento, enrolamento e montagem de eletrodos, a umidade do ponto de orvalho deve ser de ≤-35 °C DP.
1.5 Durante a injeção e vedação da célula, a umidade do ponto de orvalho deve ser de ≤-45 °C DP.
2.Controle rigorosamente o corpo humano e a umidade externa trazida para a oficina
2.1 Gestão de Conformidade:
A entrada na oficina de secagem requer troca de roupa, chapéu, troca de sapatos e máscara.
É estritamente proibido tocar nas folhas e células do eletrodo com as mãos desprotegidas.
2.2 Gerenciamento de contaminação por umidade:
É estritamente proibido trazer caixas de papelão para a oficina de secagem.
Cartazes e placas em papel dentro da área de secagem devem ser laminados.
A limpeza com água é proibida na área de secagem.
3. Controle rigoroso do armazenamento da folha de eletrodo e tempo de exposição:
3.1 Gerenciamento de armazenamento de baixa umidade:
As folhas de eletrodo após a prensagem e corte do rolo devem ser armazenadas em um ambiente de baixa umidade dentro de 30 minutos (≤-35°C DP).
As folhas de eletrodo que foram cozidas, mas não processadas prontamente (enrolamento de filme) devem ser armazenadas sob vácuo (≤-95kPa).
3.2 Gestão do tempo de exposição:
Após o cozimento, as folhas de eletrodo devem ser processadas (enrolamento de filme), encapsuladas, injetadas com eletrólito e seladas dentro de 72 horas (umidade do ponto de orvalho da oficina ≤-35°C).
3.3 Gerenciamento FIFO (primeiro a entrar, primeiro a sair):
O uso de folhas de eletrodos deve seguir o princípio FIFO, onde os lotes produzidos anteriormente são usados primeiro.
As folhas de eletrodo assadas devem ser usadas na ordem de cozimento.
4. Controle rigorosamente o processo de cozimento da folha de eletrodo e do separador
4.1 As folhas e separadores de eletrodos devem ser cozidos (secos) antes do uso.
4.2 Se as folhas e separadores de eletrodos não forem cozidos (secos) antes do enrolamento do filme, eles devem ser cozidos (secos) antes da injeção da célula.
4.3 Durante o processo de cozimento (secagem) de folhas ou células de eletrodos, os parâmetros do forno (temperatura, tempo, nível de vácuo) devem ser rigorosamente monitorados.
4.4 A temperatura e o nível de vácuo do forno devem ser calibrados regularmente para garantir a precisão.
5. Teste e controle do teor de água
5.1 O teor de água das folhas de eletrodos, separadores (ou células) e eletrólitos deve ser testado, e somente se atenderem aos requisitos a célula pode ser preenchida.
5.2 Método de teste: Amostragem de acordo com os regulamentos e medição usando um testador de umidade Karl Fischer.
5.3 Critérios de aceitação para o teor de água:
Teor de água da folha de eletrodo ≤200ppm (pré-controle ≤150ppm)
Teor de água do separador ≤600ppm
Teor de água eletrolítica ≤20ppm

Em resumo, no processo de fabricação de baterias de lítio, o controle da umidade ambiental, o armazenamento e o tempo de exposição das folhas de eletrodos, os processos de secagem e desumidificação das folhas e separadores de eletrodos, as datas de validade dos eletrólitos e o teste do teor de água são essenciais. A falha no controle desses fatores pode levar a defeitos graves no desempenho dos lotes de baterias, com sérias consequências. Portanto, seja pessoal de gerenciamento, operadores de produção ou inspetores de qualidade, é crucial aumentar a conscientização sobre o controle de umidade em baterias e cumprir rigorosamente os regulamentos durante todo o processo de fabricação para garantir que o teor de umidade das baterias permaneça controlado e dentro de limites aceitáveis.